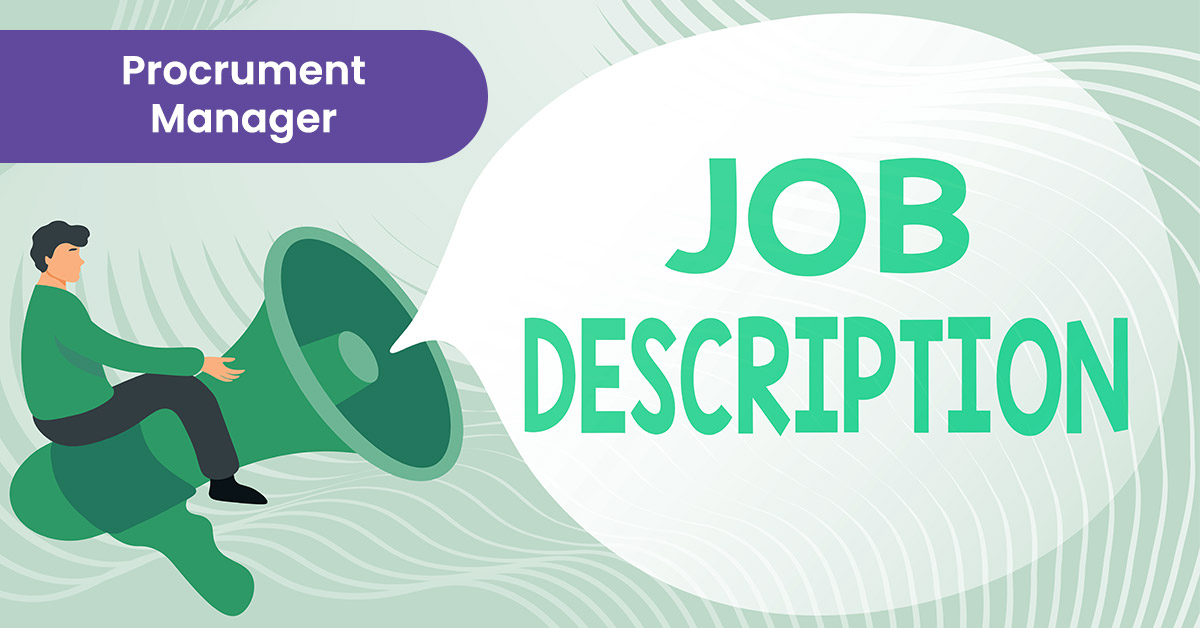
A single-piece flow production line can help increase your output and reduce inventory. It also helps to reduce lead times and lead times. Before you start using this technology, here are some things to keep in mind. You will want to measure the takt time, which is the time it takes to produce an item. This allows to calculate how fast an item must be produced to meet customers' demand.
One piece flow is best suited to manufacturing operations that are geared towards low-variability products. But it isn't the right fit for every company. It is important to ensure that you measure the right metrics in order to determine if this type process is right to your company.
The use of a single-piece flow will require a more robust, scalable control mechanism. This will help to reduce waste and maximize efficiency. It is also important to ensure that the time required to make a single-piece item can be scaled to meet your customers' needs. This will ensure the one-piece flow is not slower than traditional production.
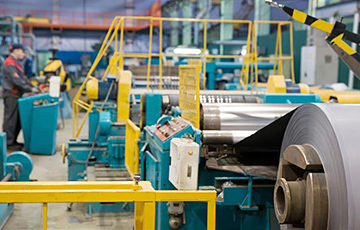
One piece flow is achieved by using a production process that looks like an U or S. This is because it will reduce the amount of movement required to move from step to step. It also increases assembly efficiency.
The poka-yoke refers to a clever way of preventing defects from getting to the next step. This is a great way to save time and money while increasing the quality of your products. The poka yoke is also a great way to reduce waste, inefficiency, and cost.
One-piece flow is also a good option when there's a lot of demand for specific products. You want to save time and money in this situation by not having to order multiple items at once. A single work item flow will reduce the cost of delay and the depreciation of your inventory. It will also reduce the time products spend in the warehouse (WIP).
A single-piece flow process can be used to lower the cost of inventory management. This is especially useful for small businesses. This process will allow you to save money on inventory storage, transportation, and repackaging of your products. This is a great way of reducing the time it takes your customers to receive products.
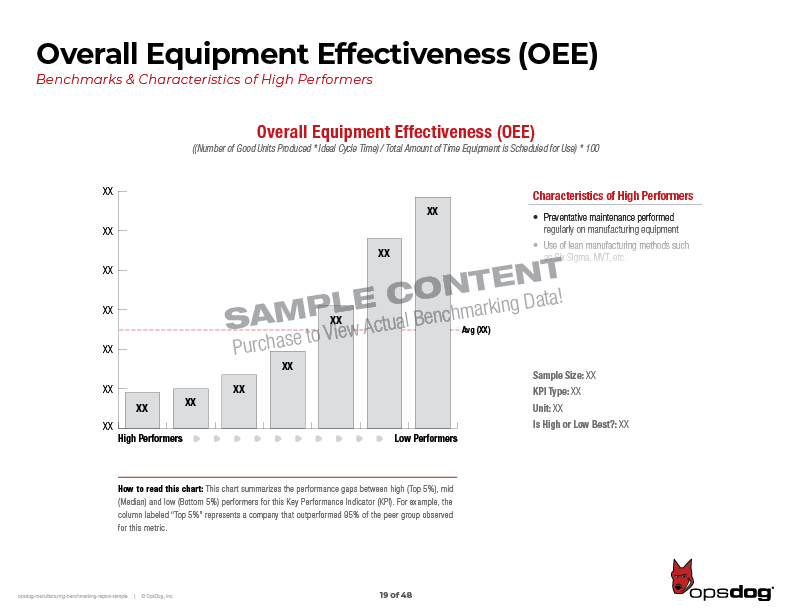
By allowing employees and managers to work together, the one-piece process helps boost employee morale. This makes it easier for you to spot problems with your product. This is important as it could mean that your customers may receive defective or incomplete goods. This is a great opportunity to improve your customer service.
A one-piece flow production line can be used both inside and outside of an assembly line. This type of process is ideal for optimizing your value stream. It also allows for faster production and higher quality products. It can also be a great way of reducing costs and boosting morale among employees.
FAQ
What are the 4 types manufacturing?
Manufacturing refers the process of turning raw materials into useful products with machines and processes. Manufacturing involves many activities, including designing, building, testing and packaging, shipping, selling, service, and so on.
How can manufacturing excess production be decreased?
In order to reduce excess production, you need to develop better inventory management methods. This would reduce the time needed to manage inventory. This could help us free up our time for other productive tasks.
Kanban systems are one way to achieve this. A Kanban Board is a visual display that tracks work progress. Kanban systems are where work items travel through a series of states until reaching their final destination. Each state has a different priority level.
When work is completed, it can be transferred to the next stage. If a task is still in its beginning stages, it will continue to be so until it reaches the end.
This helps to keep work moving forward while ensuring that no work is left behind. Managers can view the Kanban board to see how much work they have done. This information allows them to adjust their workflow based on real-time data.
Lean manufacturing, another method to control inventory levels, is also an option. Lean manufacturing works to eliminate waste throughout every stage of the production chain. Anything that does not contribute to the product's value is considered waste. Here are some examples of common types.
-
Overproduction
-
Inventory
-
Unnecessary packaging
-
Exceed materials
These ideas can help manufacturers improve efficiency and reduce costs.
Why should you automate your warehouse?
Modern warehouses are increasingly dependent on automation. The rise of e-commerce has led to increased demand for faster delivery times and more efficient processes.
Warehouses must be able to quickly adapt to changing demands. Technology investment is necessary to enable warehouses to respond quickly to changing demands. Automating warehouses has many benefits. Here are some of the reasons automation is worth your investment:
-
Increases throughput/productivity
-
Reduces errors
-
Increases accuracy
-
Safety Boosts
-
Eliminates bottlenecks
-
Companies can scale up more easily
-
Increases efficiency of workers
-
Provides visibility into everything that happens in the warehouse
-
Enhances customer experience
-
Improves employee satisfaction
-
This reduces downtime while increasing uptime
-
This ensures that quality products are delivered promptly
-
Eliminates human error
-
Helps ensure compliance with regulations
What does warehouse mean?
A warehouse is a place where goods are stored until they are sold. You can have it indoors or outdoors. It may also be an indoor space or an outdoor area.
What is the role of a production manager?
A production planner makes sure all project elements are delivered on schedule, within budget, as well as within the agreed scope. They also ensure the quality of the product and service meets the client's requirements.
What skills is required for a production planner?
Being a production planner is not easy. You need to be organized and flexible. Effective communication with clients and colleagues is essential.
How can manufacturing efficiency be improved?
First, identify the factors that affect production time. Next, we must find ways to improve those factors. If you don't know where to start, then think about which factor(s) have the biggest impact on production time. Once you have identified the factors, then try to find solutions.
Statistics
- According to the United Nations Industrial Development Organization (UNIDO), China is the top manufacturer worldwide by 2019 output, producing 28.7% of the total global manufacturing output, followed by the United States, Japan, Germany, and India.[52][53] (en.wikipedia.org)
- According to a Statista study, U.S. businesses spent $1.63 trillion on logistics in 2019, moving goods from origin to end user through various supply chain network segments. (netsuite.com)
- It's estimated that 10.8% of the U.S. GDP in 2020 was contributed to manufacturing. (investopedia.com)
- You can multiply the result by 100 to get the total percent of monthly overhead. (investopedia.com)
- [54][55] These are the top 50 countries by the total value of manufacturing output in US dollars for its noted year according to World Bank.[56] (en.wikipedia.org)
External Links
How To
How to Use the Just-In-Time Method in Production
Just-intime (JIT), a method used to lower costs and improve efficiency in business processes, is called just-in-time. This is where you have the right resources at the right time. This means that only what you use is charged to your account. Frederick Taylor developed the concept while working as foreman in early 1900s. He saw how overtime was paid to workers for work that was delayed. He concluded that if workers were given enough time before they start work, productivity would increase.
JIT is about planning ahead. You should have all the necessary resources ready to go so that you don’t waste money. Also, you should look at the whole project from start-to-finish and make sure you have the resources necessary to address any issues. If you expect problems to arise, you will be able to provide the necessary equipment and personnel to address them. This will ensure that you don't spend more money on things that aren't necessary.
There are many JIT methods.
-
Demand-driven: This JIT is where you place regular orders for the parts/materials that are needed for your project. This will allow for you to track the material that you have left after using it. This will allow you to calculate how long it will take to make more.
-
Inventory-based: This is a type where you stock the materials required for your projects in advance. This allows you to forecast how much you will sell.
-
Project-driven: This method allows you to set aside enough funds for your project. Knowing how much money you have available will help you purchase the correct amount of materials.
-
Resource-based JIT : This is probably the most popular type of JIT. You assign certain resources based off demand. For example, if there is a lot of work coming in, you will have more people assigned to them. If you don’t have many orders you will assign less people to the work.
-
Cost-based: This approach is very similar to resource-based. However, you don't just care about the number of people you have; you also need to consider how much each person will cost.
-
Price-based: This is very similar to cost-based, except that instead of looking at how much each individual worker costs, you look at the overall price of the company.
-
Material-based: This is quite similar to cost-based, but instead of looking at the total cost of the company, you're concerned with how much raw materials you spend on average.
-
Time-based: Another variation of resource-based JIT. Instead of worrying about how much each worker costs, you can focus on how long the project takes.
-
Quality-based JIT is another variant of resource-based JIT. Instead of looking at the labor costs and time it takes to make a product, think about its quality.
-
Value-based: This is one of the newest forms of JIT. In this instance, you are not concerned about the product's performance or meeting customer expectations. Instead, you focus on the added value that you provide to your market.
-
Stock-based: This is an inventory-based method that focuses on the actual number of items being produced at any given time. It's useful when you want maximum production and minimal inventory.
-
Just-intime (JIT), planning is a combination JIT management and supply chain management. It is the process of scheduling components' delivery as soon as they have been ordered. It is essential because it reduces lead-times and increases throughput.