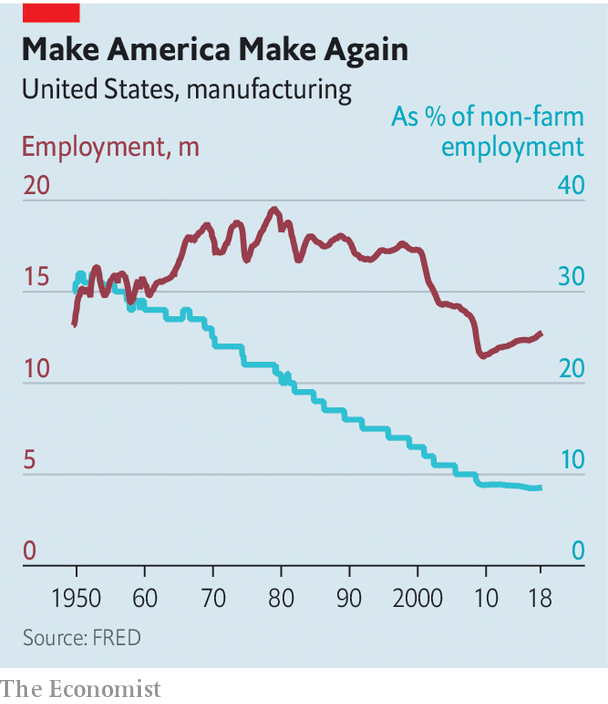
Robotics Technicians are employed by robot manufacturers and robotics suppliers. They are responsible of the repair and maintenance of equipment used for building and operating robotic systems. This job requires both a degree and practical experience. A robotics technician salary can vary considerably depending on the level of education and experience.
Most robotics technicians obtain an associate's in a relevant field. This may include electronics, mathematics, or mechanical engineering. A typical degree will give the student a solid foundation in science, mathematics, computer programming, and science. After completing this program, a robotics technician works with a team consisting of robotics professionals. They create, test and maintain robotic systems.
These systems are utilized in almost all aspects of our lives. Robots can be found in many industries. They are used for material handling, transportation, the defense department, and the medical field. A robot can gather information for soldiers, such as landmines, in the military. Mechatronics is an engineering discipline which combines electrical and mechanical engineering.
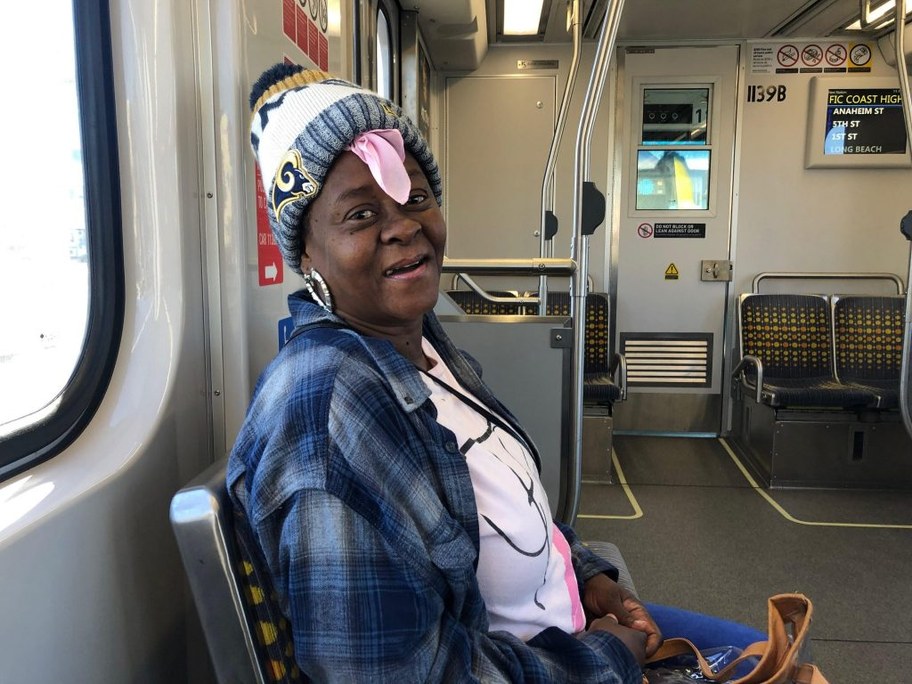
Robotics technician programs are offered by many universities and colleges in the United States. Students can also seek jobs directly with companies that hire robotics technicians. A keen interest in problem solving and a strong aptitude for science and math are essential to becoming a successful robotics operator. Employers will generally require applicants to hold a high school diploma.
While the salary for robotics technicians isn't very high, they do require a significant amount of education. Robotics technicians typically have a two year associate's degree. While it is not unusual to get additional training while working as a robotics technician, the majority of employers provide training on the job.
Robotics technicians will work shifts, depending on what industry they are working in. Robotics technicians are responsible to program robots to do specific tasks. Operators must diagnose the root cause of malfunctioning robots and then repair them. Operators will also need to work weekends and nights.
Robotics Technicians usually earn between $44,175 - $84,520. Atlanta, GA has the highest quality of life for Robotics Technicians. Because it offers the best quality life, this is why. Robotics Technicians in Atlanta earn $1,841 a paycheck.
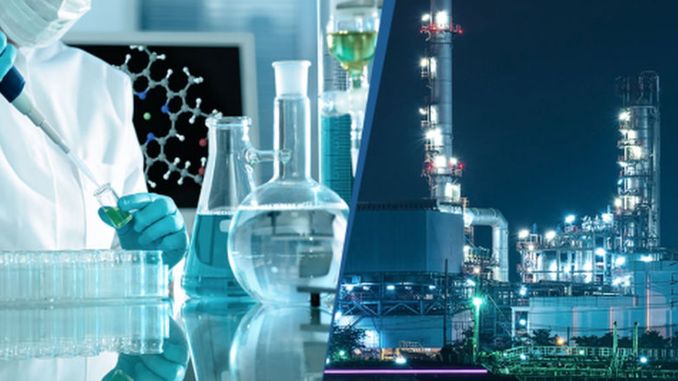
Atlanta's state tax rate is lower for robotics technicians. Georgia robotics technicians are required to pay 6% tax on their salaries. This is significantly more than the national standard. Atlanta has a lower cost of living than many other cities. This makes it a great spot to settle.
Robotics Technicians can make a significant impact on the world. A robotics technician can get a high salary as an expert in the field. They can be employed as either a maintenance technician, or a robot operator.
FAQ
What are the 7 Rs of logistics management?
The acronym "7R's" of Logistics stands for seven principles that underpin logistics management. It was published in 2004 by the International Association of Business Logisticians as part of their "Seven Principles of Logistics Management" series.
The following letters make up the acronym:
-
Responsible - ensure that actions are in compliance with legal requirements and do not cause harm to others.
-
Reliable - You can have confidence that you will fulfill your promises.
-
Reasonable - use resources efficiently and don't waste them.
-
Realistic - consider all aspects of operations, including cost-effectiveness and environmental impact.
-
Respectful – Treat others fairly and equitably.
-
Responsive - Look for ways to save time and increase productivity.
-
Recognizable provides value-added products and services to customers
What are manufacturing and logistic?
Manufacturing refers to the process of making goods using raw materials and machines. Logistics covers all aspects involved in managing supply chains, including procurement and production planning. Sometimes manufacturing and logistics are combined to refer to a wider term that includes both the process of creating products as well as their delivery to customers.
What is the role of a production manager?
Production planners ensure that all project aspects are completed on time, within budget and within the scope. They also ensure the quality of the product and service meets the client's requirements.
How can I learn about manufacturing?
Hands-on experience is the best way to learn more about manufacturing. You can read books, or watch instructional videos if you don't have the opportunity to do so.
How can we reduce manufacturing overproduction?
In order to reduce excess production, you need to develop better inventory management methods. This would decrease the time that is spent on inefficient activities like purchasing, storing, or maintaining excess stock. By doing this, we could free up resources for other productive tasks.
Kanban systems are one way to achieve this. A Kanban board can be used to monitor work progress. Kanban systems are where work items travel through a series of states until reaching their final destination. Each state represents an individual priority level.
As an example, if work is progressing from one stage of the process to another, then the current task is complete and can be transferred to the next. A task that is still in the initial stages of a process will be considered complete until it moves on to the next stage.
This helps to keep work moving forward while ensuring that no work is left behind. With a Kanban board, managers can see exactly how much work is being done at any given moment. This information allows managers to adjust their workflow based off real-time data.
Lean manufacturing is another option to control inventory levels. Lean manufacturing works to eliminate waste throughout every stage of the production chain. Waste includes anything that does not add value to the product. Here are some examples of common types.
-
Overproduction
-
Inventory
-
Unnecessary packaging
-
Excess materials
By implementing these ideas, manufacturers can improve efficiency and cut costs.
What skills are required to be a production manager?
Production planners must be flexible, organized, and able handle multiple tasks. Communication skills are essential to ensure that you can communicate effectively with clients, colleagues, and customers.
What are the differences between these four types?
Manufacturing refers the process of turning raw materials into useful products with machines and processes. Manufacturing involves many activities, including designing, building, testing and packaging, shipping, selling, service, and so on.
Statistics
- According to the United Nations Industrial Development Organization (UNIDO), China is the top manufacturer worldwide by 2019 output, producing 28.7% of the total global manufacturing output, followed by the United States, Japan, Germany, and India.[52][53] (en.wikipedia.org)
- (2:04) MTO is a production technique wherein products are customized according to customer specifications, and production only starts after an order is received. (oracle.com)
- According to a Statista study, U.S. businesses spent $1.63 trillion on logistics in 2019, moving goods from origin to end user through various supply chain network segments. (netsuite.com)
- Many factories witnessed a 30% increase in output due to the shift to electric motors. (en.wikipedia.org)
- In the United States, for example, manufacturing makes up 15% of the economic output. (twi-global.com)
External Links
How To
How to use 5S in Manufacturing to Increase Productivity
5S stands as "Sort", Set In Order", Standardize", Separate" and "Store". Toyota Motor Corporation created the 5S methodology in 1954. It improves the work environment and helps companies to achieve greater efficiency.
The idea behind standardizing production processes is to make them repeatable and measurable. This means that daily tasks such as cleaning and sorting, storage, packing, labeling, and packaging are possible. These actions allow workers to perform their job more efficiently, knowing what to expect.
Implementing 5S requires five steps. These are Sort, Set In Order, Standardize. Separate. And Store. Each step is a different action that leads to greater efficiency. Sorting things makes it easier to find them later. When you set items in an order, you put items together. You then organize your inventory in groups. You can also label your containers to ensure everything is properly labeled.
Employees will need to be more critical about their work. Employees need to understand the reasons they do certain jobs and determine if there is a better way. In order to use the 5S system effectively, they must be able to learn new skills.
In addition to increasing efficiency, the 5S method also improves morale and teamwork among employees. Once they start to notice improvements, they are motivated to keep working towards their goal of increasing efficiency.