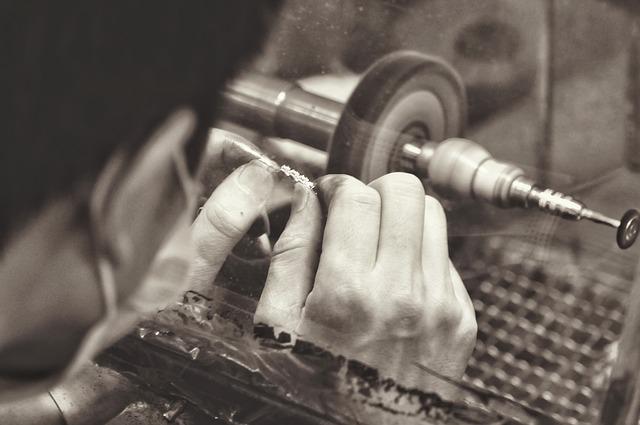
Logistics is an integral part any supply chain. Products must be transported from one place to another, starting at the beginning. In today's fast-paced environment, logistics is an integral part of every company's business operations. It is crucial to have a skilled workforce for efficient logistics. A logistic supply chain is also about the timely and efficient movement of goods, information, or resources. But what exactly does logistics mean? This article will address some key aspects of logistic supply chain.
Logistics is about the movement or products from point A into point B.
Logistics is the process that moves goods from point A or B. Logistics managers oversee these processes. When shipping products from one area to another, logistics managers must be aware of many details. They must determine the best shipping option for a product and weigh it. Also, they need to consider the cost of full shipment. They must consider customer satisfaction as well as warehousing costs, all of which contribute to fully loaded prices.
It is an essential part a supply chains
Logistics involves the identification and resolution of problem areas in the supply chain. These problem areas are associated with high levels of waste and high prices. It is possible for a product to be ordered in large quantities and then remain on a stock shelf for several hours. Transport providers can also be subject to high transportation costs. Overproduction can lead to problems as companies produce more than they use. This causes wasted resources and can impact the market's pricing.
It requires a skilled workforce
Logistics supply chains require a well-trained workforce. A well-trained workforce will help a company gain a competitive edge and ensure that the logistics facility runs smoothly. Employees should be rewarded when they exceed expectations. Total Logistics Solutions consultants are trained to work in warehouses and understand the process from the users' perspective. It is also beneficial to be familiar with your competitors. You should hire a Total Logistics Solutions consultant to make this possible.
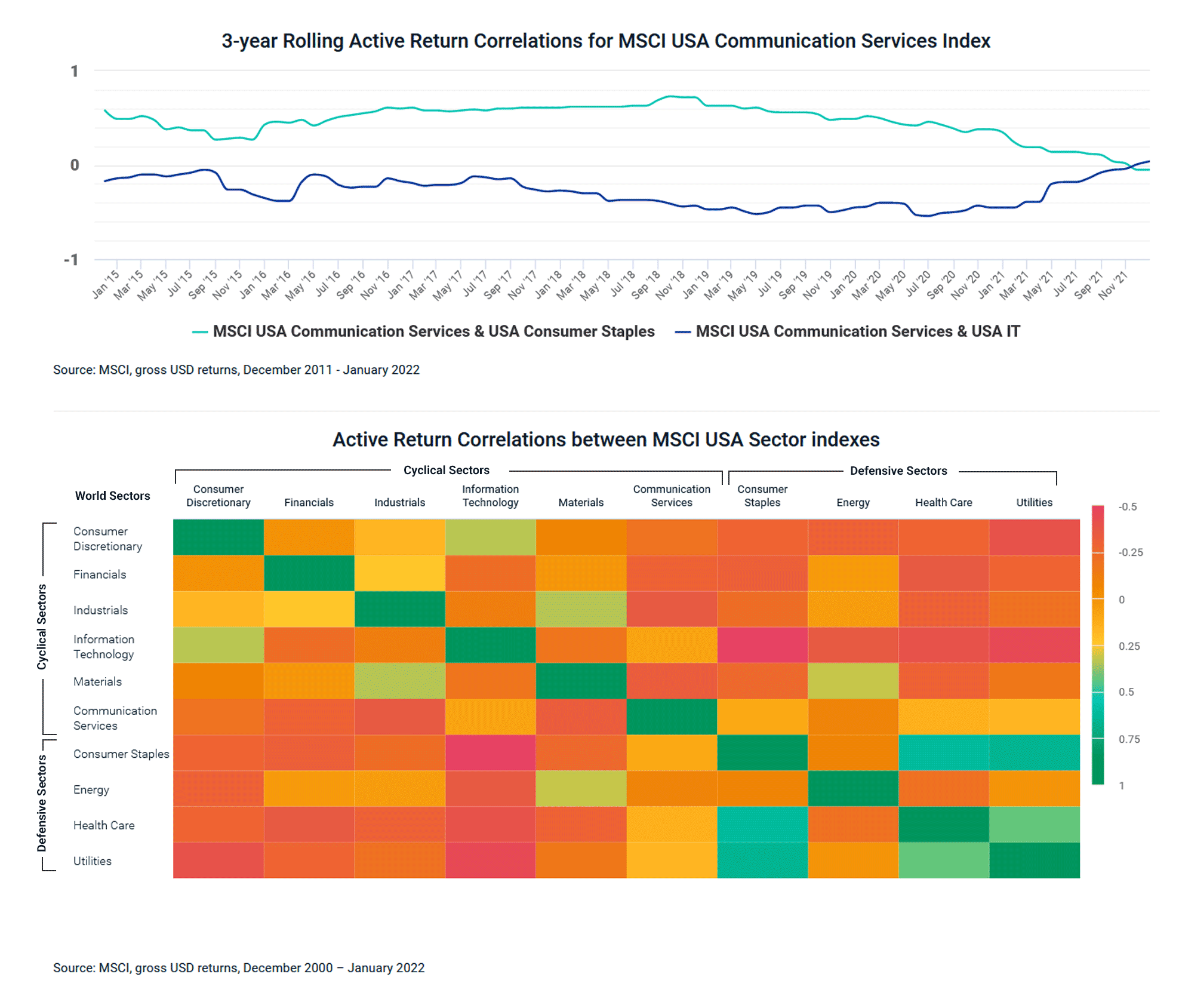
It requires technology
The logistics industry must be competitive. Technological advances are changing not only the industry's landscape but also how it operates. The logistics industry is changing with the advent of advanced analytics, additive manufacturing, automation, and other technological advances. There will be more autonomous vehicles in warehouses and major changes in warehousing strategies and inventory management. These advancements will ultimately make logistics more cost-effective and efficient for businesses.
FAQ
What are the responsibilities of a manufacturing manager
Manufacturing managers must ensure that manufacturing processes are efficient, effective, and cost-effective. They must also be alert to any potential problems and take appropriate action.
They should also know how to communicate with other departments such as sales and marketing.
They should be informed about industry trends and be able make use of this information to improve their productivity and efficiency.
What is production management?
Production planning is the process of creating a plan that covers all aspects of production. This includes scheduling, budgeting and crew, location, equipment, props, and more. This document is designed to make sure everything is ready for when you're ready to shoot. It should also provide information about how best to produce the best results while on set. It should include information about shooting locations, casting lists, crew details, equipment requirements, and shooting schedules.
The first step in filming is to define what you want. You may already know where you want the film to be shot, or perhaps you have specific locations and sets you wish to use. Once you have determined your scenes and locations, it is time to start figuring out the elements that you will need for each scene. For example, you might decide that you need a car but don't know exactly what model you want. In this case, you could start looking up cars online to find out what models are available and then narrow your choices by choosing between different makes and models.
After you have chosen the right car, you will be able to begin thinking about accessories. Do you have people who need to be seated in the front seat? Or perhaps you need someone walking around the back of the car? You might want to change your interior color from black and white. These questions will help determine the look and feel you want for your car. Also, think about what kind of shots you would like to capture. Do you want to film close-ups, or wider angles? Perhaps you want to show the engine or the steering wheel? These things will help you to identify the car that you are looking for.
Once you've determined the above, it is time to start creating a calendar. You can use a schedule to determine when and where you need it to be shot. Each day will include the time when you need to arrive at the location, when you need to leave and when you need to return home. So everyone is clear about what they need to do. Book extra staff ahead of time if you need them. It is not worth hiring someone who won’t show up because you didn’t tell him.
You will need to factor in the days that you have to film when creating your schedule. Some projects only take one or two days, while others may last weeks. When creating your schedule, be aware of whether you need more shots per day. Shooting multiple takes over the same location will increase costs and take longer to complete. You can't be certain if you will need multiple takes so it is better not to shoot too many.
Budget setting is an important part of production planning. It is important to set a realistic budget so you can work within your budget. Remember that you can always reduce the budget later on if you run into unforeseen problems. But, don't underestimate how much money you'll spend. You'll end up with less money after paying for other things if the cost is underestimated.
Production planning is a very detailed process, but once you understand how everything works together, it becomes easier to plan future projects.
How can manufacturing avoid production bottlenecks
The key to avoiding bottlenecks in production is to keep all processes running smoothly throughout the entire production cycle, from the time you receive an order until the time when the product ships.
This includes planning for capacity requirements as well as quality control measures.
This can be done by using continuous improvement techniques, such as Six Sigma.
Six Sigma is a management method that helps to improve quality and reduce waste.
It is focused on creating consistency and eliminating variation in your work.
Is it necessary to be familiar with Manufacturing Processes before we learn about Logistics.
No. It doesn't matter if you don't know anything about manufacturing before you learn about logistics. Knowing about manufacturing processes will help you understand how logistics works.
What are the 4 types of manufacturing?
Manufacturing is the process that transforms raw materials into useful products. It can involve many activities like designing, manufacturing, testing packaging, shipping, selling and servicing.
What types of jobs can you find in logistics
There are many types of jobs in logistics. Some examples are:
-
Warehouse workers - They load and unload trucks and pallets.
-
Transportation drivers – These drivers drive trucks and wagons to transport goods and pick up the goods.
-
Freight handlers: They sort and package freight in warehouses.
-
Inventory managers - They oversee the inventory of goods in warehouses.
-
Sales reps are people who sell products to customers.
-
Logistics coordinators: They plan and manage logistics operations.
-
Purchasing agents: They are responsible for purchasing goods and services to support company operations.
-
Customer service representatives – They answer emails and phone calls from customers.
-
Shipping clerks - They process shipping orders and issue bills.
-
Order fillers: They fill orders based off what has been ordered and shipped.
-
Quality control inspectors: They inspect outgoing and incoming products for any defects.
-
Others - There is a variety of other jobs in logistics. These include transportation supervisors and cargo specialists.
What is the difference between manufacturing and logistics
Manufacturing is the process of creating goods from raw materials by using machines and processes. Logistics manages all aspects of the supply chain, including procurement, production planning and distribution, inventory control, transportation, customer service, and transport. Manufacturing and logistics can often be grouped together to describe a larger term that covers both the creation of products, and the delivery of them to customers.
Statistics
- According to a Statista study, U.S. businesses spent $1.63 trillion on logistics in 2019, moving goods from origin to end user through various supply chain network segments. (netsuite.com)
- (2:04) MTO is a production technique wherein products are customized according to customer specifications, and production only starts after an order is received. (oracle.com)
- In the United States, for example, manufacturing makes up 15% of the economic output. (twi-global.com)
- According to the United Nations Industrial Development Organization (UNIDO), China is the top manufacturer worldwide by 2019 output, producing 28.7% of the total global manufacturing output, followed by the United States, Japan, Germany, and India.[52][53] (en.wikipedia.org)
- It's estimated that 10.8% of the U.S. GDP in 2020 was contributed to manufacturing. (investopedia.com)
External Links
How To
How to use the Just-In Time Method in Production
Just-intime (JIT), which is a method to minimize costs and maximize efficiency in business process, is one way. This is where you have the right resources at the right time. This means that you only pay for what you actually use. Frederick Taylor first coined this term while working in the early 1900s as a foreman. He observed how workers were paid overtime if there were delays in their work. He realized that workers should have enough time to complete their jobs before they begin work. This would help increase productivity.
JIT is about planning ahead. You should have all the necessary resources ready to go so that you don’t waste money. You should also look at the entire project from start to finish and make sure that you have sufficient resources available to deal with any problems that arise during the course of your project. You'll be prepared to handle any potential problems if you know in advance. This way, you won't end up paying extra money for things that weren't really necessary.
There are several types of JIT techniques:
-
Demand-driven: This type of JIT allows you to order the parts/materials required for your project on a regular basis. This will enable you to keep track of how much material is left after you use it. It will also allow you to predict how long it takes to produce more.
-
Inventory-based: This allows you to store the materials necessary for your projects in advance. This allows you predict the amount you can expect to sell.
-
Project-driven: This means that you have enough money to pay for your project. Once you have an idea of how much material you will need, you can purchase the necessary materials.
-
Resource-based JIT is the most widespread form. You assign certain resources based off demand. For instance, if you have a lot of orders coming in, you'll assign more people to handle them. If there aren't many orders, you will assign fewer people.
-
Cost-based: This approach is very similar to resource-based. However, you don't just care about the number of people you have; you also need to consider how much each person will cost.
-
Price-based: This approach is very similar to the cost-based method except that you don't look at individual workers costs but the total cost of the company.
-
Material-based is an alternative to cost-based. Instead of looking at the total cost in the company, this method focuses on the average amount of raw materials that you consume.
-
Time-based: This is another variation of resource-based JIT. Instead of worrying about how much each worker costs, you can focus on how long the project takes.
-
Quality-based JIT: This is another variation of resource based JIT. Instead of looking at the labor costs and time it takes to make a product, think about its quality.
-
Value-based JIT : This is the newest type of JIT. This is where you don't care about how the products perform or whether they meet customers' expectations. Instead, your focus is on the value you bring to the market.
-
Stock-based: This is an inventory-based method that focuses on the actual number of items being produced at any given time. This is used to increase production and minimize inventory.
-
Just-intime (JIT), planning is a combination JIT management and supply chain management. It is the process of scheduling components' delivery as soon as they have been ordered. It's important because it reduces lead times and increases throughput.