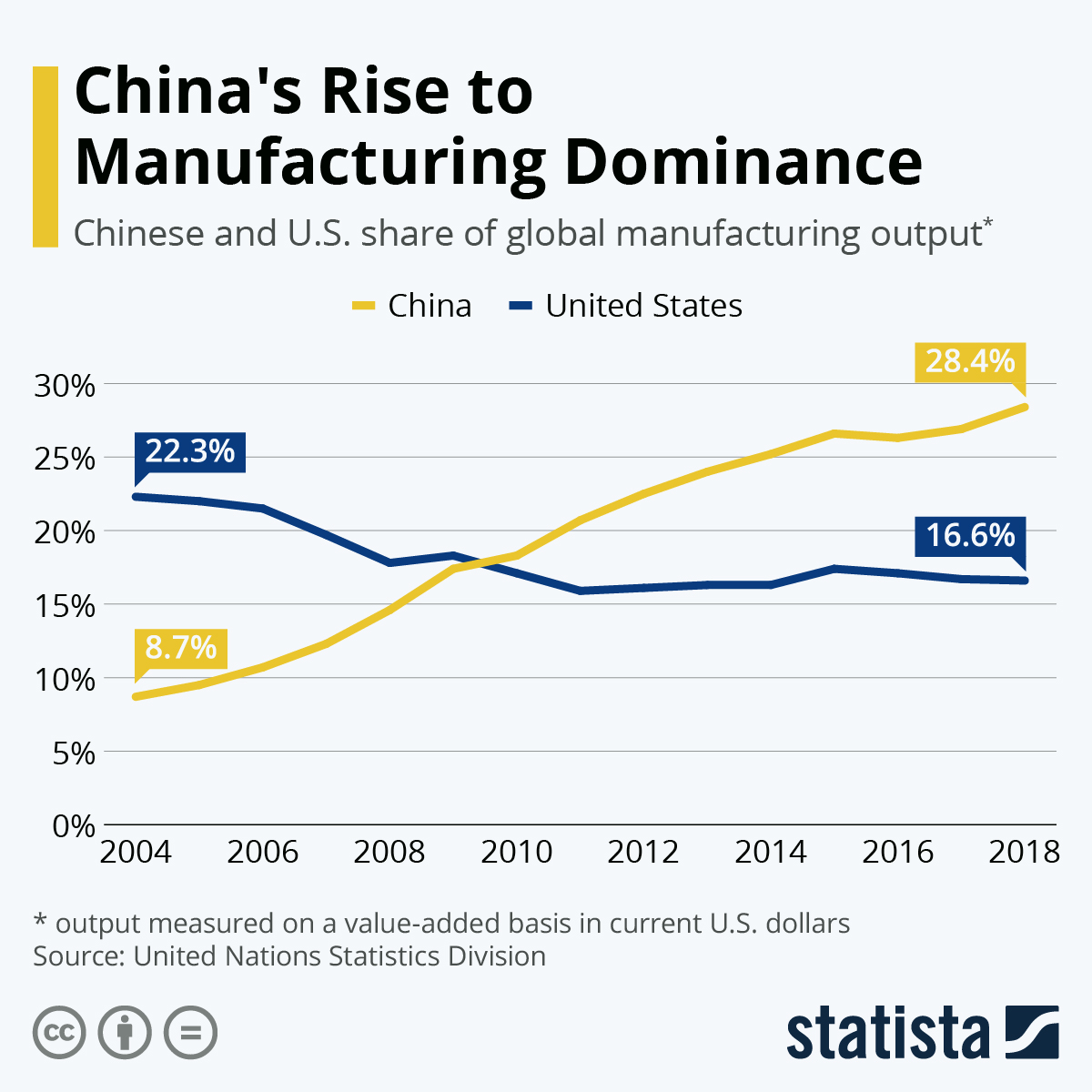
Drawing is a skill that requires a great deal of technical knowledge. They should also be able to work in teams to produce the best results. They may need to learn how engineering plans are read and how to use certain software programs. They might also need the ability to use engineering formulas in order to calculate measurements.
Drawing professionals are often employed by engineering or architectural firms. They use computer-aided design software (CAD), to create plans for structures and buildings. They often work on their own projects but also collaborate with others to create innovative designs. These professionals often work full-time but can also do a variety jobs. They may have to work overtime depending on their company.
A common degree for drafters is an associate's in drafting at a community college. Then, they can continue their education by enrolling in a 4-year university program. The course they choose may allow them to transfer their degree to a bachelor’s degree.
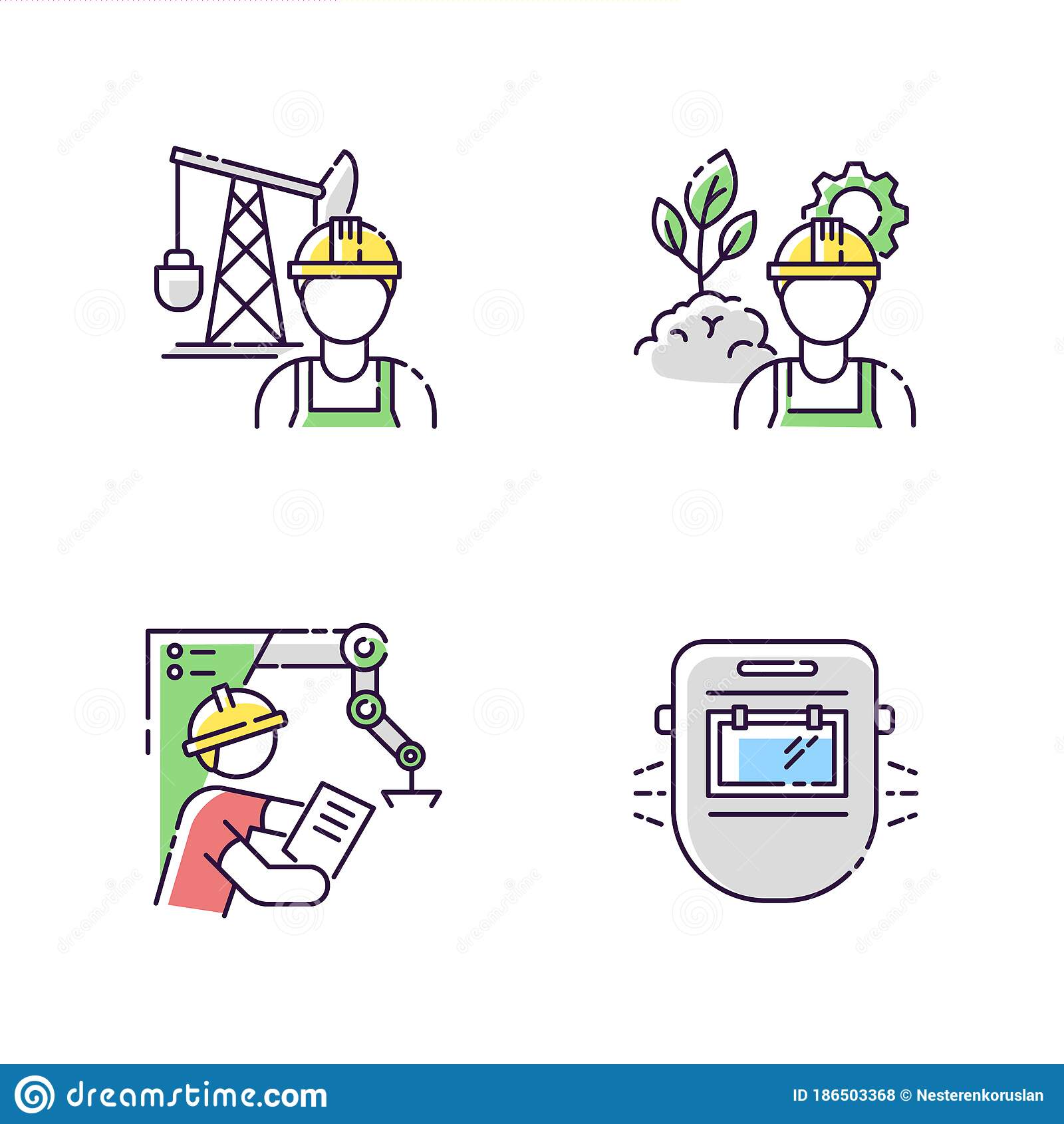
Drafters will need to have professional experience in addition to a degree in drafting. In order to gain real-world experience, they may be required to do an internship at a company. This experience can help drafters land a job. They may also be asked to submit a portfolio in order to demonstrate their drafting skills.
You can also become a certified drafter. The American Design Drafting Association (ADDA) offers certification exams that test drafting knowledge. These exams are intended to assess your ability to create and accept geometric designs. Many certifications can be renewed every three years. The ADDA certifies a variety of drafting specialties.
Drafters typically work for construction, engineering, and manufacturing companies. They might also be employed in factories or with electricity. Although they might work on a schedule, some drafters may work for more than 40 hours per week. They must also be able manage their time and learn how to use computer-aided drawing (CAD) software.
Drafters can profit from the growing use of technology in order to increase their efficiency. To stay competitive, they may need to learn CAD and other programming languages. A master's degree is an option for those who want to become a drafter. When it comes to being hired, those with a master's will be more successful than other candidates. They will be better qualified to give technical information to clients.
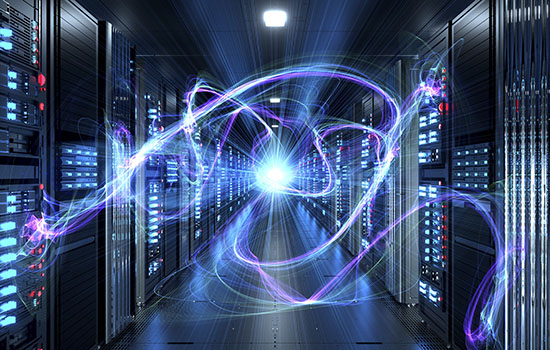
Assisting professional drafters is another option for drafters. To gain experience, drafters may volunteer to help with community projects. If you are interested in becoming a drafter, you should determine what type of project you are interested in before enrolling in classes. Some clients prefer pencil sketches while others prefer computer-generated designs.
Draft technicians can gain practical experience after graduating high school. They can enroll in drafting classes at technical institutes to get professional experience. They should pay particular attention to math and computer classes.
FAQ
What does the term manufacturing industries mean?
Manufacturing Industries refers to businesses that manufacture products. These products are sold to consumers. To accomplish this goal, these companies employ a range of processes including distribution, sales, management, and production. These companies produce goods using raw materials and other equipment. This includes all types if manufactured goods.
How can we improve manufacturing efficiency?
The first step is to identify the most important factors affecting production time. Then we need to find ways to improve these factors. If you don’t know how to start, look at which factors have the greatest impact upon production time. Once you've identified them, try to find solutions for each of those factors.
What is the difference in Production Planning and Scheduling, you ask?
Production Planning (PP), also known as forecasting and identifying production capacities, is the process that determines what product needs to be produced at any particular time. This is done through forecasting demand and identifying production capacities.
Scheduling involves the assignment of dates and times to tasks in order to complete them within the timeframe.
How can overproduction in manufacturing be reduced?
Better inventory management is key to reducing excess production. This would reduce the time needed to manage inventory. We could use these resources to do other productive tasks.
A Kanban system is one way to achieve this. A Kanban board, a visual display to show the progress of work, is called a Kanban board. A Kanban system allows work items to move through several states before reaching their final destination. Each state represents a different priority.
To illustrate, work can move from one stage or another when it is complete enough for it to be moved to a new stage. If a task is still in its beginning stages, it will continue to be so until it reaches the end.
This allows for work to continue moving forward, while also ensuring that there is no work left behind. A Kanban board allows managers to monitor how much work is being completed at any given moment. This data allows them adjust their workflow based upon real-time data.
Lean manufacturing is another option to control inventory levels. Lean manufacturing focuses on eliminating waste throughout the entire production chain. Waste includes anything that does not add value to the product. These are some of the most common types.
-
Overproduction
-
Inventory
-
Unnecessary packaging
-
Excess materials
These ideas will help manufacturers increase efficiency and lower costs.
Why automate your warehouse?
Modern warehousing is becoming more automated. E-commerce has increased the demand for quicker delivery times and more efficient processes.
Warehouses must be able to quickly adapt to changing demands. Technology is essential for warehouses to be able to adapt quickly to changing needs. The benefits of automating warehouses are numerous. Here are some of the reasons automation is worth your investment:
-
Increases throughput/productivity
-
Reduces errors
-
Accuracy is improved
-
Safety is boosted
-
Eliminates bottlenecks
-
Companies can scale up more easily
-
Workers are more productive
-
It gives visibility to everything that happens inside the warehouse
-
Enhances customer experience
-
Improves employee satisfaction
-
Minimizes downtime and increases uptime
-
Quality products delivered on time
-
Removing human error
-
Assure compliance with regulations
Statistics
- (2:04) MTO is a production technique wherein products are customized according to customer specifications, and production only starts after an order is received. (oracle.com)
- According to a Statista study, U.S. businesses spent $1.63 trillion on logistics in 2019, moving goods from origin to end user through various supply chain network segments. (netsuite.com)
- [54][55] These are the top 50 countries by the total value of manufacturing output in US dollars for its noted year according to World Bank.[56] (en.wikipedia.org)
- In the United States, for example, manufacturing makes up 15% of the economic output. (twi-global.com)
- Job #1 is delivering the ordered product according to specifications: color, size, brand, and quantity. (netsuite.com)
External Links
How To
How to use the Just-In Time Method in Production
Just-intime (JIT), which is a method to minimize costs and maximize efficiency in business process, is one way. This is where you have the right resources at the right time. This means you only pay what you use. Frederick Taylor, a 1900s foreman, first coined the term. Taylor observed that overtime was paid to workers if they were late in working. He decided that workers would be more productive if they had enough time to complete their work before they started to work.
The idea behind JIT is that you should plan ahead and have everything ready so you don't waste money. Look at your entire project, from start to end. Make sure you have enough resources in place to deal with any unexpected problems. If you expect problems to arise, you will be able to provide the necessary equipment and personnel to address them. This will prevent you from spending extra money on unnecessary things.
There are several types of JIT techniques:
-
Demand-driven: This is a type of JIT where you order the parts/materials needed for your project regularly. This will allow for you to track the material that you have left after using it. This will let you know how long it will be to produce more.
-
Inventory-based: This type allows you to stock the materials needed for your projects ahead of time. This allows for you to anticipate how much you can sell.
-
Project-driven: This means that you have enough money to pay for your project. When you know how much you need, you'll purchase the appropriate amount of materials.
-
Resource-based JIT: This type of JIT is most commonly used. Here you can allocate certain resources based purely on demand. For example, if there is a lot of work coming in, you will have more people assigned to them. If you don’t have many orders you will assign less people to the work.
-
Cost-based: This is similar to resource-based, except that here you're not just concerned about how many people you have but how much each person costs.
-
Price-based: This is very similar to cost-based, except that instead of looking at how much each individual worker costs, you look at the overall price of the company.
-
Material-based: This approach is similar to cost-based. However, instead of looking at the total cost for the company, you look at how much you spend on average on raw materials.
-
Time-based JIT is another form of resource-based JIT. Instead of focusing on how much each employee costs, you focus on how long it takes to complete the project.
-
Quality-based JIT - This is another form of resource-based JIT. Instead of worrying about the costs of each employee or how long it takes for something to be made, you should think about how quality your product is.
-
Value-based JIT: This is the latest form of JIT. In this scenario, you're not concerned about how products perform or whether customers expect them to meet their expectations. Instead, your goal is to add value to the market.
-
Stock-based: This stock-based method focuses on the actual quantity of products being made at any given time. It's useful when you want maximum production and minimal inventory.
-
Just-intime (JIT), planning is a combination JIT management and supply chain management. It refers to the process of scheduling the delivery of components as soon as they are ordered. It is essential because it reduces lead-times and increases throughput.