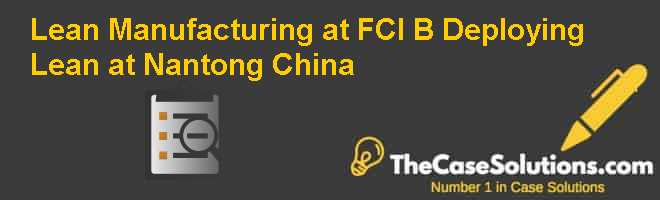
Hoshinkanri, Visual board and Value Stream mapping are just a few tools that make up the lean toolbox. These methods combine statistical data with quality control measures to improve process performance and reduce defects. The safety and well-being of employees, the cycle time, delivery times, and quality of raw materials are all improved by Lean tools. You can find more information in our articles about these tools. We provide examples and explain some of the basics.
Hoshin Kanri
It's important to communicate each department's goals when implementing Hoshinkanri principles. It is crucial to clearly communicate the objectives of your company and the results they produce. Google Images has a sample Hoshin Kanri template. The idea behind the Hoshinkanri matrix is to ensure everyone is on the same page and can work together towards common goals.
Hoshin Kanri is a comprehensive method that can help identify areas in your business that require improvement. This method can help you to identify the activities that need to be improved and to establish a clear pathway from general goals towards concrete actions. It can help you visualize the relationship between each step and how it relates to others. Compared to boring business plans, Hoshin Kanri encourages a collaborative approach to improving the overall company.
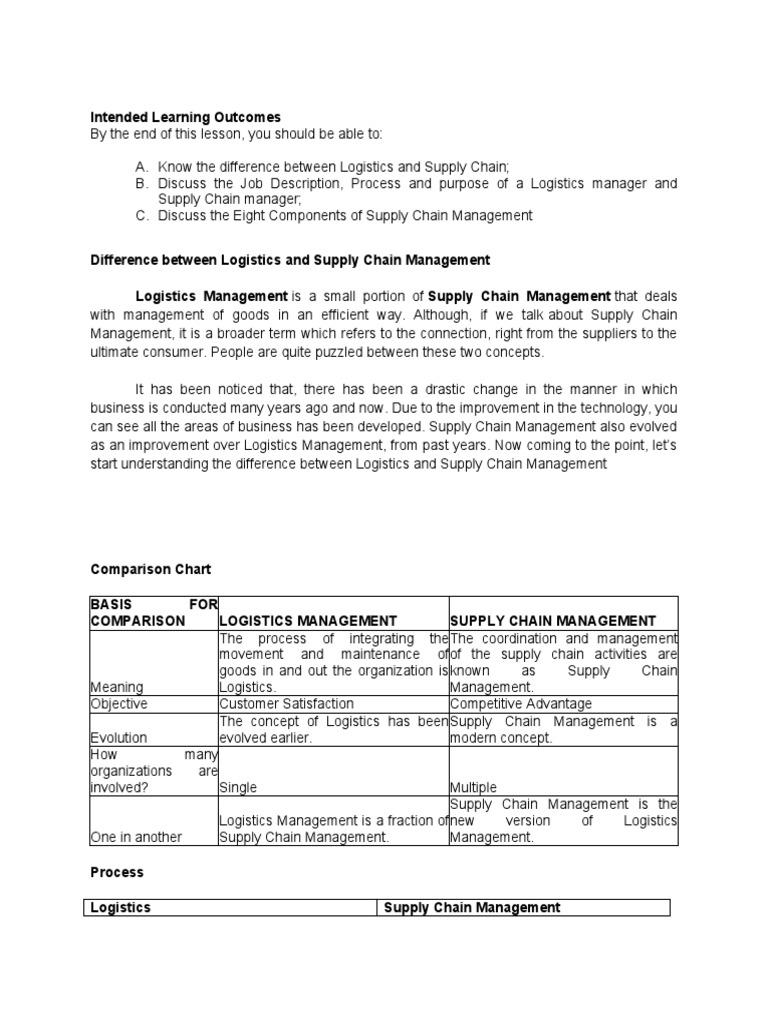
Visual board
The visual board can be used to measure the process's results, but it is not universal. It can only be used as a tool when the implementation process involves people. A visual management board should be customized for the users in order to create a sense of emotion behind the numbers. It can also serve as a tool to track performance indicators like the amount of work hours or pieces that were produced in standard time. It is possible to use this tool in lean production environments, but there are key elements.
One of the most important aspects of a visual board for management is the ability of all team members to quickly communicate what needs to be done, and who will do each task. This information is easily viewed on the board in under 20 seconds. The results of these activities must also be visible to management to ensure that everyone is on the same page. Regular updates can be made to the visual management boards in order to ensure that everyone is on a similar page.
Value Stream Mapping
Facilitators must identify any bottlenecks or constraints when using tools lean to value stream map. The bottleneck is the step in the process with the most WIP. A three-step process with a throughput rate 60 units/hour and a potential work in progress (WIP) of 42 units/hour would be a bottleneck. Step 2 would then be the bottleneck. The value stream map can be used as a guide to pinpoint bottlenecks, and identify opportunities for process improvement.
Understanding the customer perspective and the system or process is key to a successful value stream mapping. This is a cross-functional process that can be complex. This process may require extensive training and involvement of many people. Larger companies might have a value-stream manager who will lead the mapping. Although value stream mapping may be a big project, smaller projects can identify areas where there are potential savings and improvements. Value stream mapping is a powerful tool in tools lean.
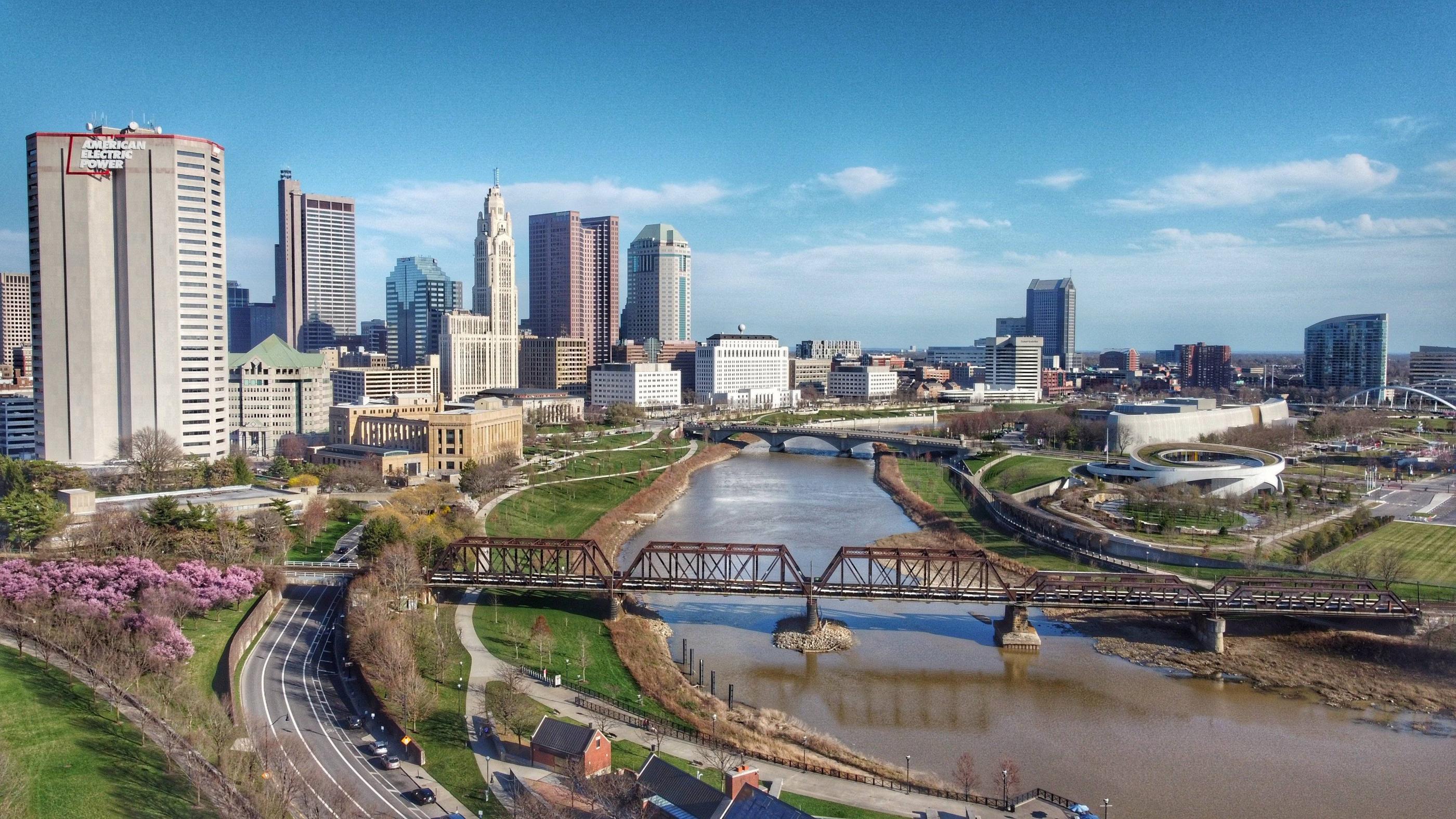
Process observation and analysis
Lean management is built on the concepts of continuous improvement, process observation and quality control. Process observation is a way to make sure standards are being maintained and that processes deliver the desired outcome. Abandoned processes will eventually degrade. Managers need to explain why process observation is important and what the benefits are. Process observation and analysis are a key part of lean management. Managers must clearly communicate to their team why they believe it is important.
When implementing Lean, the first step is to verify the process flow map by conducting a walk-through of the process. The next step after this step is completed is to analyze all data. The Measure phase allows the team to collect data about the current process or product. The project leader applies statistical hypothesis testing techniques to determine the root cause of a problem. This analysis helps to determine if the problem is solved or improved.
FAQ
What are manufacturing and logistic?
Manufacturing is the process of creating goods from raw materials by using machines and processes. Logistics encompasses the management of all aspects associated with supply chain activities such as procurement, production planning, distribution and inventory control. It also includes customer service. Manufacturing and logistics can often be grouped together to describe a larger term that covers both the creation of products, and the delivery of them to customers.
What is the role and responsibility of a Production Planner?
A production planner makes sure all project elements are delivered on schedule, within budget, as well as within the agreed scope. They also ensure the quality of the product and service meets the client's requirements.
What are the 7 Rs of logistics?
The acronym "7R's" of Logistics stands for seven principles that underpin logistics management. It was developed by International Association of Business Logisticians (IABL), and published as part of their "Seven Principles of Logistics Management Series" in 2004.
The following letters form the acronym:
-
Responsible - ensure that actions are in compliance with legal requirements and do not cause harm to others.
-
Reliable - You can have confidence that you will fulfill your promises.
-
Use resources effectively and sparingly.
-
Realistic – consider all aspects of operations, from cost-effectiveness to environmental impact.
-
Respectful - Treat people fairly and equitably
-
Be resourceful: Look for opportunities to save money or increase productivity.
-
Recognizable - Provide value-added services to customers
Are there any Manufacturing Processes that we should know before we can learn about Logistics?
No. You don't have to know about manufacturing processes before learning about logistics. However, knowing about manufacturing processes will definitely give you a better understanding of how logistics works.
How can manufacturing overproduction be reduced?
Better inventory management is key to reducing excess production. This would reduce the time spent on unproductive activities like purchasing, storing and maintaining excess stock. By doing this, we could free up resources for other productive tasks.
Kanban systems are one way to achieve this. A Kanban board can be used to monitor work progress. In a Kanban system, work items move through a sequence of states until they reach their final destination. Each state represents a different priority level.
When work is completed, it can be transferred to the next stage. However, if a task is still at the beginning stages, it will remain so until it reaches the end of the process.
This keeps work moving and ensures no work is lost. With a Kanban board, managers can see exactly how much work is being done at any given moment. This information allows them to adjust their workflow based on real-time data.
Lean manufacturing can also be used to reduce inventory levels. Lean manufacturing focuses on eliminating waste throughout the entire production chain. Anything that does nothing to add value to a product is waste. The following are examples of common waste types:
-
Overproduction
-
Inventory
-
Packaging that is not necessary
-
Materials in excess
Manufacturers can reduce their costs and improve their efficiency by using these ideas.
How can manufacturing avoid production bottlenecks
Avoiding production bottlenecks is as simple as keeping all processes running smoothly, from the time an order is received until the product ships.
This includes both quality control and capacity planning.
Continuous improvement techniques like Six Sigma are the best way to achieve this.
Six Sigma is a management method that helps to improve quality and reduce waste.
It emphasizes consistency and eliminating variance in your work.
Statistics
- Job #1 is delivering the ordered product according to specifications: color, size, brand, and quantity. (netsuite.com)
- According to the United Nations Industrial Development Organization (UNIDO), China is the top manufacturer worldwide by 2019 output, producing 28.7% of the total global manufacturing output, followed by the United States, Japan, Germany, and India.[52][53] (en.wikipedia.org)
- It's estimated that 10.8% of the U.S. GDP in 2020 was contributed to manufacturing. (investopedia.com)
- In the United States, for example, manufacturing makes up 15% of the economic output. (twi-global.com)
- [54][55] These are the top 50 countries by the total value of manufacturing output in US dollars for its noted year according to World Bank.[56] (en.wikipedia.org)
External Links
How To
How to use 5S in Manufacturing to Increase Productivity
5S stands for "Sort", 'Set In Order", 'Standardize', & Separate>. Toyota Motor Corporation invented the 5S strategy in 1954. It improves the work environment and helps companies to achieve greater efficiency.
The basic idea behind this method is to standardize production processes, so they become repeatable, measurable, and predictable. It means tasks like cleaning, sorting or packing, labeling, and storing are done every day. This knowledge allows workers to be more efficient in their work because they are aware of what to expect.
Implementing 5S requires five steps. These are Sort, Set In Order, Standardize. Separate. And Store. Each step requires a different action to increase efficiency. If you sort items, it makes them easier to find later. When items are ordered, they are put together. Next, organize your inventory into categories and store them in containers that are easily accessible. Labeling your containers will ensure that everything is correctly labeled.
Employees must be able to critically examine their work practices. Employees must be able to see why they do what they do and find a way to achieve them without having to rely on their old methods. They must learn new skills and techniques in order to implement the 5S system.
In addition to improving efficiency, the 5S system also increases morale and teamwork among employees. Once they start to notice improvements, they are motivated to keep working towards their goal of increasing efficiency.