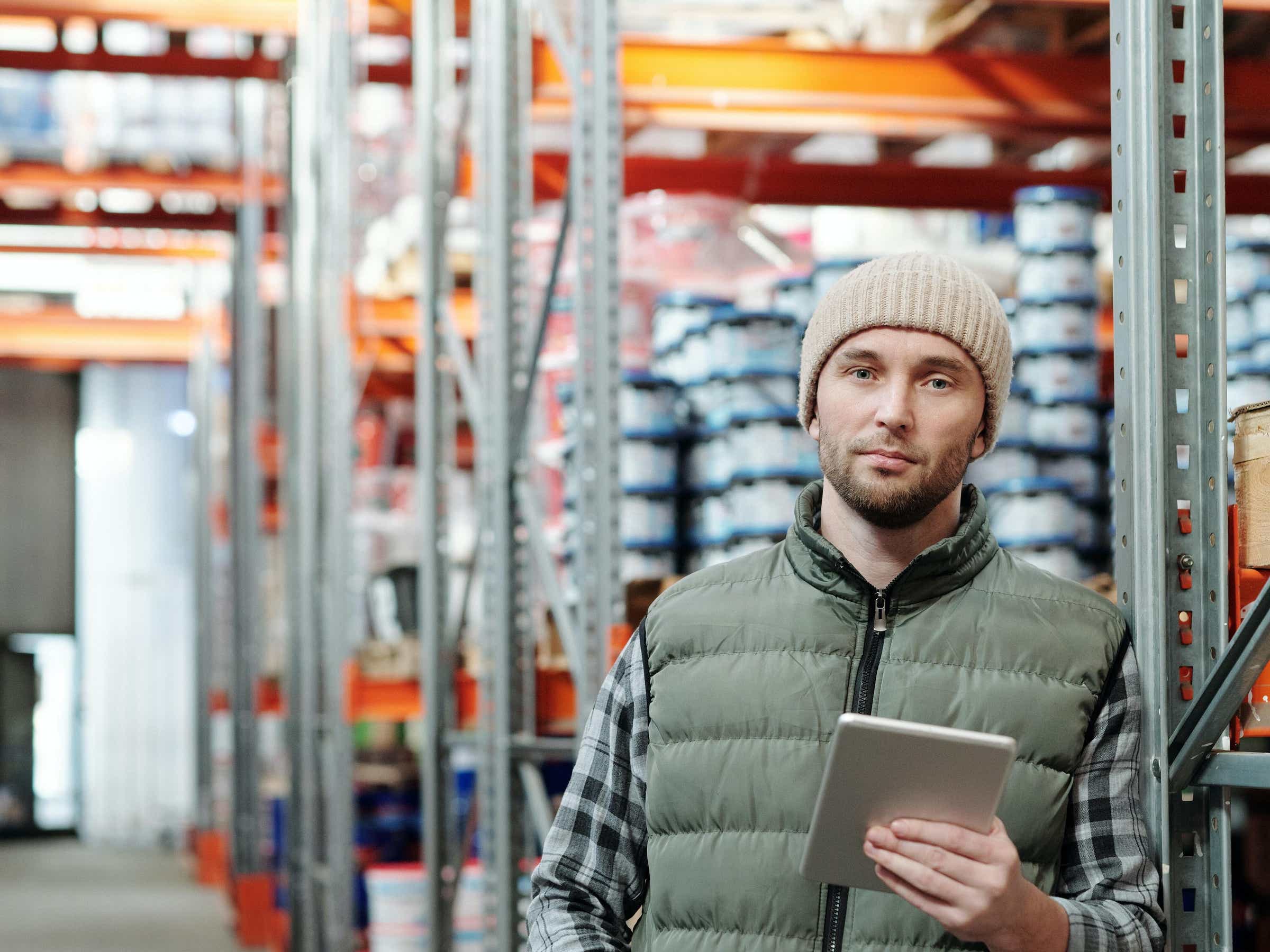
An accurate cost estimate is necessary for nearly every task a company undertakes. Cost estimators are responsible. They assist companies in determining the cost of developing and manufacturing new products and services. They also need to assess the cost of building new structures. This includes analysing the labor and materials costs.
Construction companies employ many cost estimators. They must have a good understanding of construction methods and processes. They should be familiar with computer aided design software (CAD). This software can improve design and manufacturing efficiency. Additionally, cost estimators need to be capable of reading data from database. They can also use Microsoft Excel or other software.
For accurate cost estimates, cost estimaters work together with other professionals. They analyze the project blueprints, site conditions, as well as other materials, to determine each component's costs. They may also work closely with engineers to determine gauges or machining requirements.
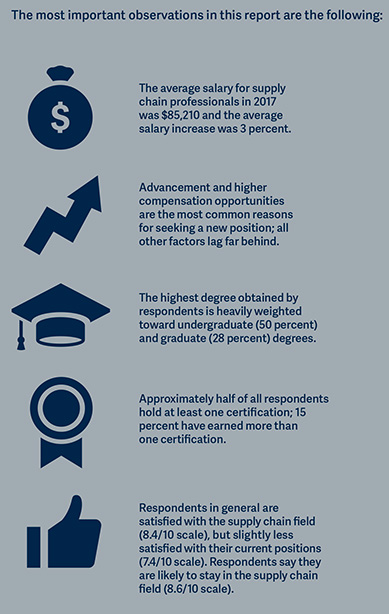
Cost estimators must be meticulous, assertive, and reliable. They must be capable of interpreting difficult information. They should also be able present their findings clearly and persuasively. They should also be able to communicate with clients and professionals.
In most cases, cost estimators work for the engineering or cost department of a company. They must have a strong background in mathematics and science. They should also be comfortable with commercial and CAD software. A certification course may be required. Certified Cost Estimator/Analysts (CCEA), Professional Estimator/Analysts, and Certified Professional Estimators are just a few of the certifications available.
Cost estimators may be skilled in certain services or industries. One person may specialize in building costs or construction, while another might be more interested in software development costs. Cost estimators could also be employed in other areas like automotive repair and management, building construction, or specialty trade contractors.
Individuals in this occupation communicate with engineers, clients, and suppliers. They are also well-versed in industry terminology. They are also able to build a solid knowledge base in order to prepare cost estimates. Apart from preparing cost estimates and finding ways to cut costs, many people in this occupation also do studies.
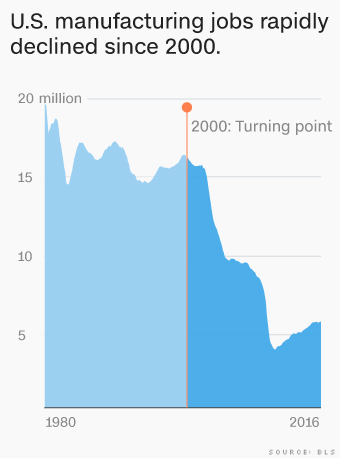
You may need to have a bachelor’s degree depending on your industry. They may also need an internship. They can also participate in cooperative education. Also, construction companies are more interested in individuals who have a degree that focuses on building construction and/or construction management.
In construction companies and other manufacturing firms, cost estimators are employed. They assist companies in making accurate estimates that will allow them to submit profitable bids. They also analyze data related the supply chain as well as other factors that may affect costs. For government programs, cost estimators are also available. They may also be asked to redesign products or services.
Cost estimators must have a strong understanding of computer-aided design (CAD) software. They can also be trained to use automatic cost estimation software.
FAQ
What are the 4 types of manufacturing?
Manufacturing refers to the transformation of raw materials into useful products by using machines and processes. Manufacturing can include many activities such as designing and building, testing, packaging shipping, selling, servicing, and other related activities.
What is production planning?
Production planning is the process of creating a plan that covers all aspects of production. This includes scheduling, budgeting and crew, location, equipment, props, and more. This document will ensure everything is in order and ready to go when you need it. It should also provide information about how best to produce the best results while on set. This includes location information, crew details, equipment specifications, and casting lists.
It is important to first outline the type of film you would like to make. You may have already chosen the location you want, or there are locations or sets you prefer. Once you have determined your scenes and locations, it is time to start figuring out the elements that you will need for each scene. You might decide you need a car, but not sure what make or model. This is where you can look up car models online and narrow down your options by choosing from different makes and models.
Once you have found the right vehicle, you can think about adding accessories. Do you need people sitting in the front seats? Or maybe you just need someone to push the car around. You might want to change your interior color from black and white. These questions will help guide you in determining the ideal look and feel for your car. It is also worth considering the types of shots that you wish to take. You will be filming close-ups and wide angles. Maybe you want to show your engine or the steering wheel. These factors will help you determine which car style you want to film.
Once you have made all the necessary decisions, you can start to create a schedule. You will know when you should start and when you should finish shooting. Each day will include the time when you need to arrive at the location, when you need to leave and when you need to return home. So everyone is clear about what they need to do. Hire extra staff by booking them ahead of time. You don't want to hire someone who won't show up because he didn't know.
When creating your schedule, you will also need to consider the number of days you need to film. Some projects take only a few days while others can last several weeks. When creating your schedule, be aware of whether you need more shots per day. Multiple shots at the same location can increase costs and make it more difficult to complete. If you aren't sure whether you need multiple shots, it is best to take fewer photos than you would like.
Budgeting is another important aspect of production planning. A realistic budget will help you work within your means. Keep in mind that you can always reduce your budget if you face unexpected difficulties. It is important to not overestimate how much you will spend. Underestimating the cost will result in less money after you have paid for other items.
Production planning is a very detailed process, but once you understand how everything works together, it becomes easier to plan future projects.
What is the role of a logistics manager
A logistics manager ensures that all goods are delivered on time and without damage. This is done through his/her expertise and knowledge about the company's product range. He/she should also ensure enough stock is available to meet demand.
What is it like to manage a logistics company?
You need to have a lot of knowledge and skills to manage a successful logistic business. For clients and suppliers to be successful, you need to have excellent communication skills. It is important to be able to analyse data and draw conclusions. You will need to be able handle pressure well and work in stressful situations. You need to be innovative and creative to come up with new ways to increase efficiency. You must be a strong leader to motivate others and direct them to achieve organizational goals.
To meet tight deadlines, you must also be efficient and organized.
What jobs are available in logistics?
Logistics can offer many different jobs. Some of them are:
-
Warehouse workers: They load and unload trucks, pallets, and other cargo.
-
Transport drivers - These are people who drive trucks and trailers to transport goods or perform pick-ups.
-
Freight handlers, - They sort out and pack freight in warehouses.
-
Inventory managers - They oversee the inventory of goods in warehouses.
-
Sales representatives - They sell products to customers.
-
Logistics coordinators - They organize and plan logistics operations.
-
Purchasing agents: They are responsible for purchasing goods and services to support company operations.
-
Customer service representatives - Answer calls and email from customers.
-
Shippers clerks - They process shipping order and issue bills.
-
Order fillers – They fill orders based upon what was ordered and shipped.
-
Quality control inspectors - They check incoming and outgoing products for defects.
-
Others - There are many other types of jobs available in logistics, such as transportation supervisors, cargo specialists, etc.
Statistics
- It's estimated that 10.8% of the U.S. GDP in 2020 was contributed to manufacturing. (investopedia.com)
- According to the United Nations Industrial Development Organization (UNIDO), China is the top manufacturer worldwide by 2019 output, producing 28.7% of the total global manufacturing output, followed by the United States, Japan, Germany, and India.[52][53] (en.wikipedia.org)
- In 2021, an estimated 12.1 million Americans work in the manufacturing sector.6 (investopedia.com)
- Many factories witnessed a 30% increase in output due to the shift to electric motors. (en.wikipedia.org)
- Job #1 is delivering the ordered product according to specifications: color, size, brand, and quantity. (netsuite.com)
External Links
How To
How to Use the 5S to Increase Productivity In Manufacturing
5S stands for "Sort", "Set In Order", "Standardize", "Separate" and "Store". The 5S methodology was developed at Toyota Motor Corporation in 1954. This methodology helps companies improve their work environment to increase efficiency.
The basic idea behind this method is to standardize production processes, so they become repeatable, measurable, and predictable. This means that daily tasks such as cleaning and sorting, storage, packing, labeling, and packaging are possible. Workers can be more productive by knowing what to expect.
Implementing 5S requires five steps. These are Sort, Set In Order, Standardize. Separate. And Store. Each step is a different action that leads to greater efficiency. By sorting, for example, you make it easy to find the items later. Once you have placed items in an ordered fashion, you will put them together. After you have divided your inventory into groups you can store them in easy-to-reach containers. You can also label your containers to ensure everything is properly labeled.
This requires employees to critically evaluate how they work. Employees need to understand the reasons they do certain jobs and determine if there is a better way. They must learn new skills and techniques in order to implement the 5S system.
In addition to improving efficiency, the 5S system also increases morale and teamwork among employees. Once they start to notice improvements, they are motivated to keep working towards their goal of increasing efficiency.