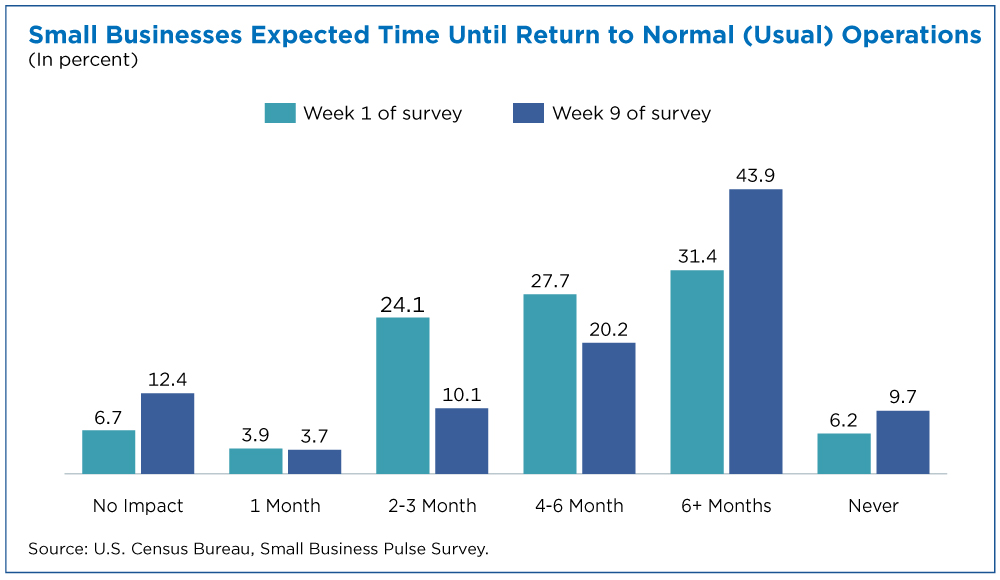
A process technician is responsible in maintaining and servicing the equipment at a manufacturing site. To troubleshoot or maintain equipment, they use science, math, chemistry and computer operation. They are required to adhere to company quality standards.
Some Process Technicians work at a laboratory. These technicians perform experiments and draw conclusions from the test data. They also make suggestions for improvement. Additionally, they might train employees. It may be advantageous to have a background or education in engineering or biochemistry depending on the job.
Most Process Technicians work as factory workers. They may also work in other industries. For example, in a water treatment plant, they help to provide clean drinking water. Because of this, they need to have excellent problem-solving and observation skills.
Process technicians are responsible for ensuring safety at work. They must maintain the plant equipment in a safe condition and adhere to safety policies. Process Technicians must repair and replace damaged machinery or automation if it malfunctions.
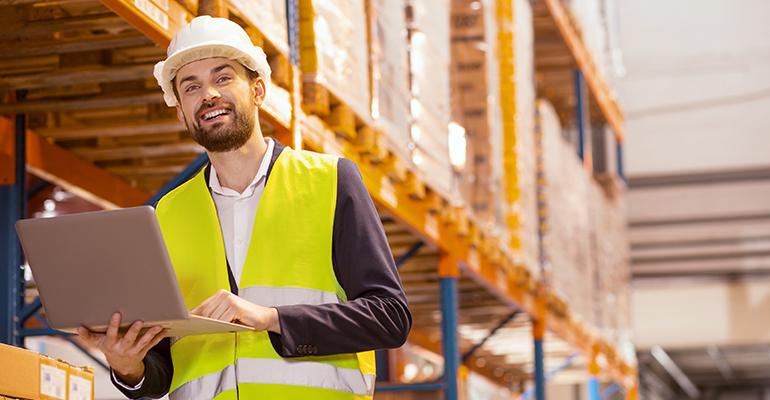
Process Technicians often have to work in shifts. Some industries are open 24 hours. This may mean that some process technicians have to work weekends or on holidays. Process technicians must be flexible and adaptable to work in different environments.
A skilled Process Technie can meet all of the challenges and problems in their work efficiently. By developing a strong skill set, they can produce the highest quality products possible.
This is a great place to start if you are looking for a career. These could be in chemistry, maths, or physics. Additional certifications may be an option.
A formal degree is required by some employers. An associate's level in process technology might be especially helpful. This will provide a foundational knowledge in engineering, mathematics and physics. Other employers may require you to have a bachelor's degree. You can pursue a leadership position within the field by having a bachelor’s degree.
Make sure you include all relevant experience and qualifications when applying for a job in Process Technician. Your manager may also be interested in additional certifications. You can also get a better salary if you have the right education.
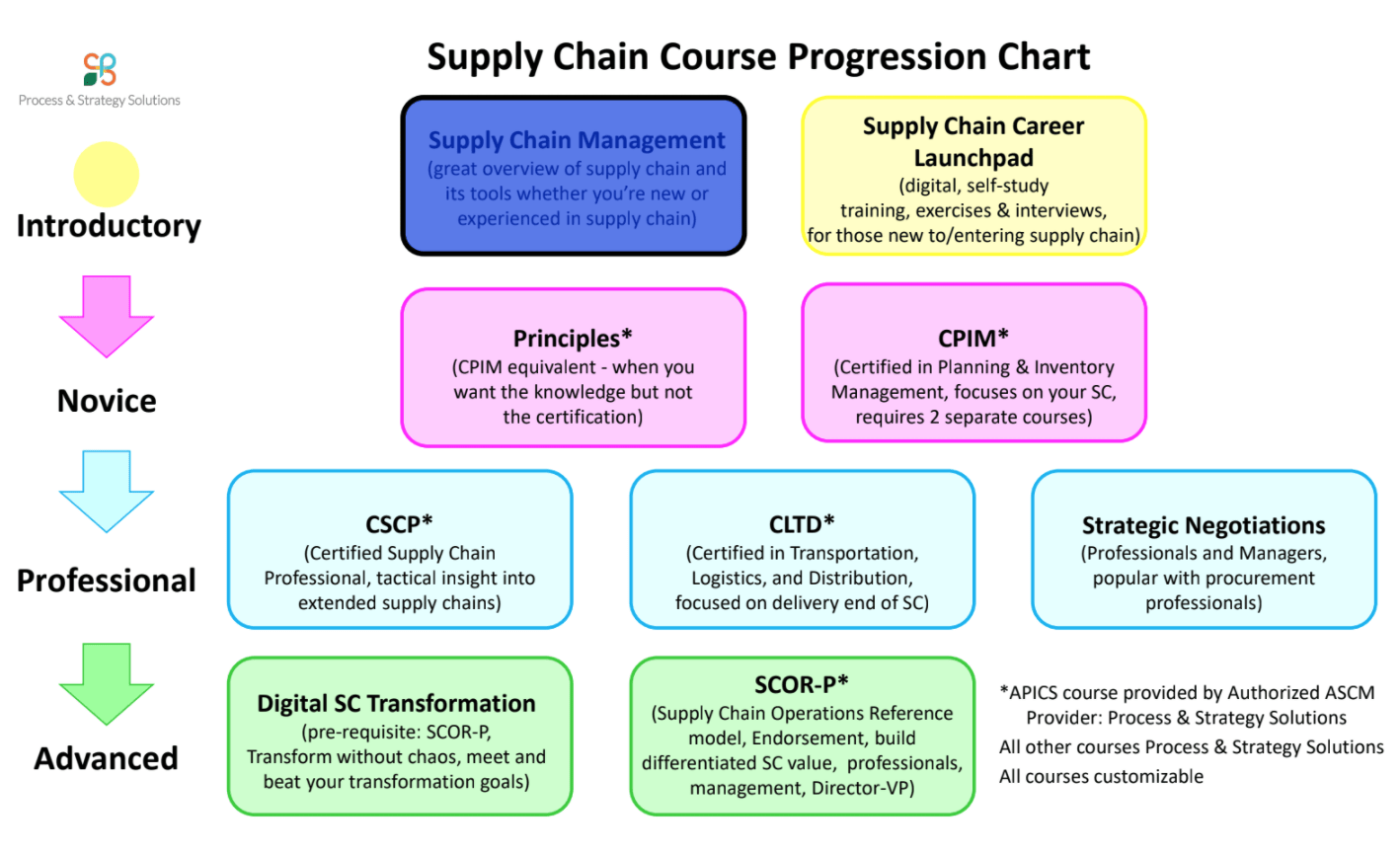
Process Technicians are required to use good communications skills. This will include writing reports and communicating with clients and technical personnel. Additionally, you may be required to participate in safety meetings.
The Process Technicians are trained to detect and minimize defects. Their work helps pharmaceutical companies produce medicine safely. They could also assist in the testing of machines and materials, or perform a variety of other tasks.
A process technician can help improve their job outlook, and even increase their salary. They may be able move into many different careers, including Quality Control Technician or Production Manager.
To start a career as a Process Technician, you should have a solid foundation in math, chemistry, and science. Education and volunteering are great ways to expand your knowledge. It is also a good idea to continue your education in order to keep abreast of the latest technology.
FAQ
What is the responsibility of a manufacturing manager?
A manufacturing manager must ensure that all manufacturing processes are efficient and effective. They should also be aware of any problems within the company and act accordingly.
They must also be able to communicate with sales and marketing departments.
They should be up to date on the latest trends and be able apply this knowledge to increase productivity and efficiency.
What are the jobs in logistics?
There are many kinds of jobs available within logistics. Here are some:
-
Warehouse workers - They load trucks and pallets.
-
Transportation drivers - They drive trucks and trailers to deliver goods and carry out pick-ups.
-
Freight handlers, - They sort out and pack freight in warehouses.
-
Inventory managers – These people oversee inventory at warehouses.
-
Sales representatives - They sell products to customers.
-
Logistics coordinators are responsible for organizing and planning logistics operations.
-
Purchasing agents are those who purchase goods and services for the company.
-
Customer service representatives are available to answer customer calls and emails.
-
Ship clerks - They issue bills and process shipping orders.
-
Order fillers – They fill orders based upon what was ordered and shipped.
-
Quality control inspectors: They inspect outgoing and incoming products for any defects.
-
Others - There are many other types of jobs available in logistics, such as transportation supervisors, cargo specialists, etc.
Why automate your warehouse
Modern warehousing has seen automation take center stage. The rise of e-commerce has led to increased demand for faster delivery times and more efficient processes.
Warehouses must adapt quickly to meet changing customer needs. They must invest heavily in technology to do this. Automating warehouses has many benefits. Here are some benefits of investing in automation
-
Increases throughput/productivity
-
Reduces errors
-
Improves accuracy
-
Safety increases
-
Eliminates bottlenecks
-
Allows companies scale more easily
-
Makes workers more efficient
-
Provides visibility into everything that happens in the warehouse
-
Enhances customer experience
-
Improves employee satisfaction
-
Reduces downtime and improves uptime
-
This ensures that quality products are delivered promptly
-
Removes human error
-
It ensures compliance with regulations
What is the difference between Production Planning, Scheduling and Production Planning?
Production Planning (PP) is the process of determining what needs to be produced at any given point in time. Forecasting and identifying production capacity are two key elements to this process.
Scheduling is the process of assigning specific dates to tasks so they can be completed within the specified timeframe.
What is the difference between a production planner and a project manager?
A production planner is more involved in the planning phase of the project than a project manger.
What is the best way to learn about manufacturing?
Practical experience is the best way of learning about manufacturing. You can read books, or watch instructional videos if you don't have the opportunity to do so.
Statistics
- According to the United Nations Industrial Development Organization (UNIDO), China is the top manufacturer worldwide by 2019 output, producing 28.7% of the total global manufacturing output, followed by the United States, Japan, Germany, and India.[52][53] (en.wikipedia.org)
- You can multiply the result by 100 to get the total percent of monthly overhead. (investopedia.com)
- According to a Statista study, U.S. businesses spent $1.63 trillion on logistics in 2019, moving goods from origin to end user through various supply chain network segments. (netsuite.com)
- (2:04) MTO is a production technique wherein products are customized according to customer specifications, and production only starts after an order is received. (oracle.com)
- It's estimated that 10.8% of the U.S. GDP in 2020 was contributed to manufacturing. (investopedia.com)
External Links
How To
How to Use Lean Manufacturing for the Production of Goods
Lean manufacturing refers to a method of managing that seeks to improve efficiency and decrease waste. It was developed in Japan during the 1970s and 1980s by Taiichi Ohno, who received the Toyota Production System (TPS) award from TPS founder Kanji Toyoda. The first book published on lean manufacturing was titled "The Machine That Changed the World" written by Michael L. Watkins and published in 1990.
Lean manufacturing can be described as a set or principles that are used to improve quality, speed and cost of products or services. It emphasizes the elimination and minimization of waste in the value stream. Lean manufacturing is also known as just in time (JIT), zero defect total productive maintenance(TPM), and five-star (S). Lean manufacturing focuses on eliminating non-value-added activities such as rework, inspection, and waiting.
In addition to improving product quality and reducing costs, lean manufacturing helps companies achieve their goals faster and reduces employee turnover. Lean manufacturing is considered one of the most effective ways to manage the entire value chain, including suppliers, customers, distributors, retailers, and employees. Lean manufacturing can be found in many industries. For example, Toyota's philosophy underpins its success in automobiles, electronics, appliances, healthcare, chemical engineering, aerospace, paper, food, etc.
Lean manufacturing includes five basic principles:
-
Define value - Find out what your business contributes to society, and what makes it different from other competitors.
-
Reduce Waste - Eliminate any activity that doesn't add value along the supply chain.
-
Create Flow - Make sure work runs smoothly without interruptions.
-
Standardize and Simplify – Make processes as consistent, repeatable, and as simple as possible.
-
Build relationships - Develop and maintain personal relationships with both your internal and external stakeholders.
Lean manufacturing isn’t new, but it has seen a renewed interest since 2008 due to the global financial crisis. To increase their competitiveness, many businesses have turned to lean manufacturing. According to some economists, lean manufacturing could be a significant factor in the economic recovery.
Lean manufacturing has many benefits in the automotive sector. These benefits include increased customer satisfaction, reduced inventory levels and lower operating costs.
Lean manufacturing can be applied to almost every aspect of an organization. This is because it ensures efficiency and effectiveness in all stages of the value chain.
There are three main types of lean manufacturing:
-
Just-in-Time Manufacturing (JIT): This type of lean manufacturing is commonly referred to as "pull systems." JIT is a method in which components are assembled right at the moment of use, rather than being manufactured ahead of time. This approach aims to reduce lead times, increase the availability of parts, and reduce inventory.
-
Zero Defects Manufacturing (ZDM),: ZDM is a system that ensures no defective units are left the manufacturing facility. It is better to repair a part than have it removed from the production line if it needs to be fixed. This applies to finished goods that may require minor repairs before shipment.
-
Continuous Improvement (CI), also known as Continuous Improvement, aims at improving the efficiency of operations through continuous identification and improvement to minimize or eliminate waste. It involves continuous improvement of processes, people, and tools.