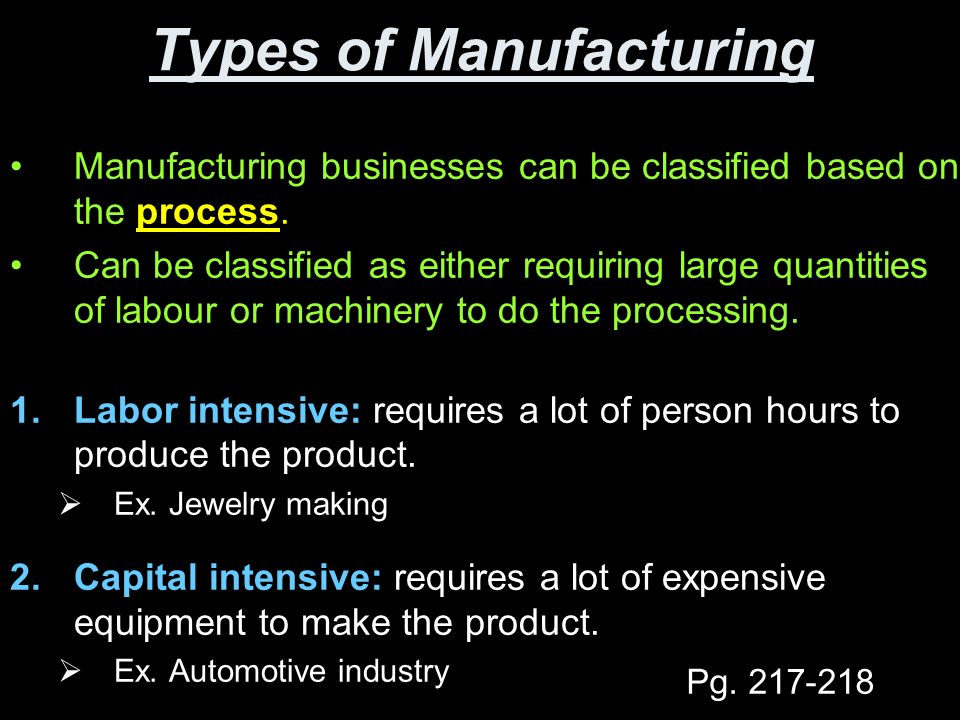
The United States is third in manufacturing in the world and saw its manufacturing output reach a record at $2.00 trillion in Q1 2018. This was nearly twice the amount it had before the Great Recession. Despite the strong domestic economy, the United States' manufacturing industry continues to take a sloppy approach to solving its current problems. We need to be more aggressive in addressing the industry's challenges, regardless of whether this is due to a lack or skilled labor.
The number of jobs has declined by 5,000,000 since 2000
Since 2000, the US has lost five millions manufacturing jobs. Although some believe that trade with China has contributed to the decrease in manufacturing jobs, this accounts for only a quarter of the total decline. Not only was there trade with China, but manufacturing jobs were also lost on local markets that weren't competitive with Chinese imports. There are many reasons why manufacturing jobs have declined. Here are some of these reasons:
The US manufacturing sector has lost almost a third of its jobs over the past 20 years. It was 17,000,000 in 1965. By 2010, it had fallen to 12,000,000. It is not because of trade that manufacturing jobs are declining. Instead, they have been impacted by structural issues - a declines in output, capital investment, productivity and trade deficits. This is not sustainable. While productivity gains were a key factor in the decline, they were not sufficient to offset the loss manufacturing jobs. Not productivity gains, but automation is the problem.
The demand for manufactured products is strong
In the United States, the demand for manufactured goods remains strong despite the fact that the share of consumer spending on these items has decreased over the past few decades. In 1945, personal spending on durable goods made up 58% of total expenditures, compared with 28% today. The reason is that the price of making and selling these goods has fallen while their content has increased. Therefore, computers, televisions, as well as sound equipment, have experienced a dramatic drop in cost.
The US has seen an increase in manufactured goods production due to the recovery in manufacturing activity. According to the Fifth District Manufacturing Activity Survey, demand is high for manufactured goods and production is increasing. However, supply chain bottlenecks are limiting output. Increased production has put pressure on supply chains. Many respondents reported experiencing supply chain disruptions that have affected their ability to keep necessary inventories. The backlog of orders has increased, as well as the lead time for vendors.
The trade deficit in manufactured products has more than doubled over the past decade
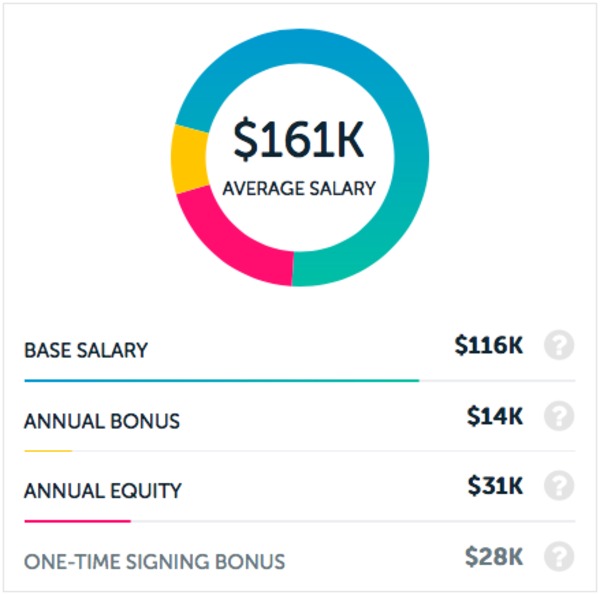
Some economists worry that the U.S.'s trade surplus will lower global growth and create more instability among its trading partners. High imports of US-made goods are not necessarily a negative thing for the U.S., as they are crucial to global economic stability. Trade deficits may be an inevitable evil since the U.S. is heavily dependent on foreign markets to generate its economy. This may make it more difficult to achieve full employment.
Since 2000, the U.S. has almost doubled its trade deficit for manufactured goods. The US deficit has been growing partly because of the increase in Chinese imports. This imbalance is mainly concentrated in the manufacturing sector. Wages and employment have fallen since the 1990s, which is the bigger problem. The result is that US manufacturing employment has dropped dramatically from 26 percent of 1970 to 8.5% in 2016. Some economists attribute this decline to China's increased competitiveness, but many others attribute it to automation, productivity improvements, and the shift in consumer demand away from goods to more services.
Industry uses a shotgun approach
The US manufacturing industry is well-respected for its advanced manufacturing efforts and has many other initiatives. However, some countries have chosen to bring the internet of everything into manufacturing. The US, in contrast, is more focused on various technologies and integrates traditional mass media with Internet marketing. The result is a shotgun approach, where companies focus on many different technologies and aim for a broad customer base.
FAQ
What does warehouse refer to?
A warehouse is an area where goods are stored before being sold. You can have it indoors or outdoors. In some cases, it may be a combination of both.
What are the 7 R's of logistics?
The acronym 7R's of Logistic is an acronym that stands for seven fundamental principles of logistics management. It was published in 2004 by the International Association of Business Logisticians as part of their "Seven Principles of Logistics Management" series.
The acronym is made up of the following letters:
-
Responsive - ensure all actions are legal and not harmful to others.
-
Reliable: Have faith in your ability or the ability to honor any promises made.
-
Reasonable - make sure you use your resources well and don't waste them.
-
Realistic – Consider all aspects, including cost-effectiveness as well as environmental impact.
-
Respectful: Treat others with fairness and equity
-
Reliable - Find ways to save money and increase your productivity.
-
Recognizable - provide customers with value-added services.
What are the logistics products?
Logistics involves the transportation of goods from point A and point B.
They include all aspects of transport, including packaging, loading, transporting, unloading, storing, warehousing, inventory management, customer service, distribution, returns, and recycling.
Logisticians ensure that the right product reaches the right place at the right time and under safe conditions. They help companies manage their supply chain efficiency by providing information on demand forecasts, stock levels, production schedules, and availability of raw materials.
They keep track and monitor the transit of shipments, maintain quality standards, order replenishment and inventories, coordinate with suppliers, vendors, and provide support for sales and marketing.
Is there anything we should know about Manufacturing Processes prior to learning about Logistics.
No. No. But, being familiar with manufacturing processes will give you a better understanding about how logistics works.
What is the role of a manager in manufacturing?
A manufacturing manager must make sure that all manufacturing processes run smoothly and effectively. They should also be aware of any problems within the company and act accordingly.
They should also learn how to communicate effectively with other departments, including sales and marketing.
They should also be aware of the latest trends in their industry and be able to use this information to help improve productivity and efficiency.
Statistics
- Many factories witnessed a 30% increase in output due to the shift to electric motors. (en.wikipedia.org)
- In the United States, for example, manufacturing makes up 15% of the economic output. (twi-global.com)
- You can multiply the result by 100 to get the total percent of monthly overhead. (investopedia.com)
- It's estimated that 10.8% of the U.S. GDP in 2020 was contributed to manufacturing. (investopedia.com)
- [54][55] These are the top 50 countries by the total value of manufacturing output in US dollars for its noted year according to World Bank.[56] (en.wikipedia.org)
External Links
How To
How to use 5S in Manufacturing to Increase Productivity
5S stands to stand for "Sort", “Set In Order", “Standardize", and "Store". Toyota Motor Corporation invented the 5S strategy in 1954. It improves the work environment and helps companies to achieve greater efficiency.
The basic idea behind this method is to standardize production processes, so they become repeatable, measurable, and predictable. Cleaning, sorting and packing are all done daily. Because workers know what they can expect, this helps them perform their jobs more efficiently.
Implementing 5S involves five steps: Sort, Set in Order, Standardize Separate, Store, and Each step requires a different action to increase efficiency. For example, when you sort things, you make them easy to find later. When items are ordered, they are put together. After you have divided your inventory into groups you can store them in easy-to-reach containers. Finally, when you label your containers, you ensure everything is labeled correctly.
This requires employees to critically evaluate how they work. Employees should understand why they do the tasks they do, and then decide if there are better ways to accomplish them. They will need to develop new skills and techniques in order for the 5S system to be implemented.
In addition to increasing efficiency, the 5S method also improves morale and teamwork among employees. They feel more motivated to work towards achieving greater efficiency as they see the results.