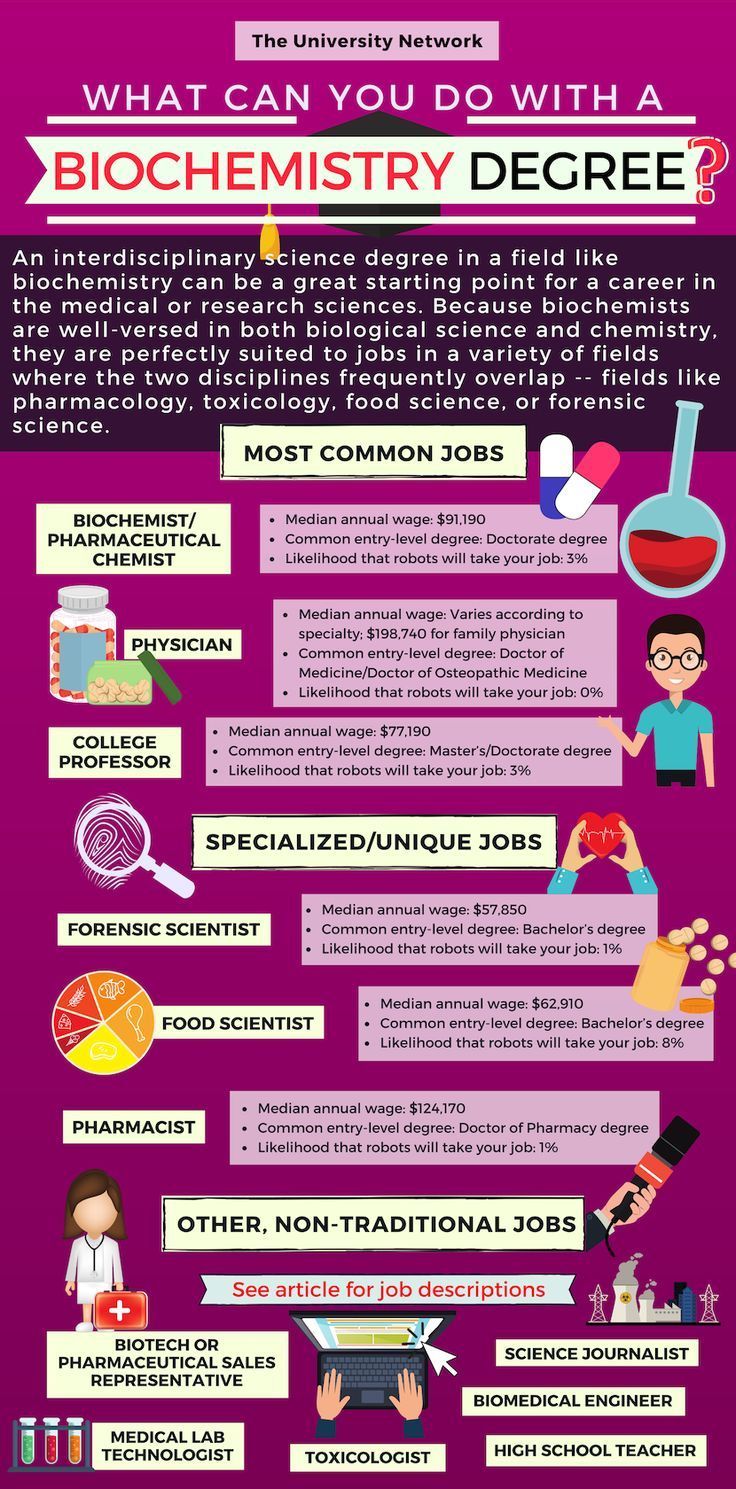
Industrial management refers to a branch of engineering that integrates various engineering processes into a single management system. An industrial manager helps to integrate these engineering processes into a single, integrated management system. Here are some facts about this job. Below are some benefits and requirements that you must meet to be an industrial manager. If you have the required qualifications and are looking for a challenging and rewarding job, this is the career for you. Continue reading for more information.
Job description
An industrial manager oversees the processes involved in the manufacturing and production of goods and services. While this job may cover all aspects of the production process, it will also focus on how to source raw materials and implement equipment. Industrial production managers should be computer-literate as computers are becoming increasingly important in the coordination of departments, suppliers, vendors, and clients. In addition, industrial production managers must be well-versed in the latest production technologies and management practices. Many managers attend conferences and trade shows in the industry and also take courses to attain certification.
In addition to overseeing manufacturing processes, industrial managers coordinate the activities of various departments within a company. They ensure production lines run efficiently and meet customer needs in terms quality and time. They may also supervise staffing levels or change production levels as required to minimize inventory. They may coordinate communication with suppliers or other departments, and supervise quality control programs. A majority of this role involves managing people, which includes identifying, training, and motivating employees.
Education is required
To be qualified as an industrial manger, you will need a bachelor's degree either in management or business administration. Some employers prefer candidates with a background or education in these areas. Computer literacy is also a requirement for industrial managers. Computers are becoming increasingly essential in the manufacturing process. They help coordinate production between departments, suppliers, clients, and other parties. For this job, you will need the necessary education and experience.
Many industrial production managers start their career as production workers and advance to first-line supervisory positions. To advance to an industrial manager position, most professionals must earn a college degree in business management. However, entry-level workers may still be able obtain this education through their jobs or by taking classes sponsored in part by their companies. But, managers should have at least two- to five years of relevant experience to be considered for managerial positions.
Earning potential
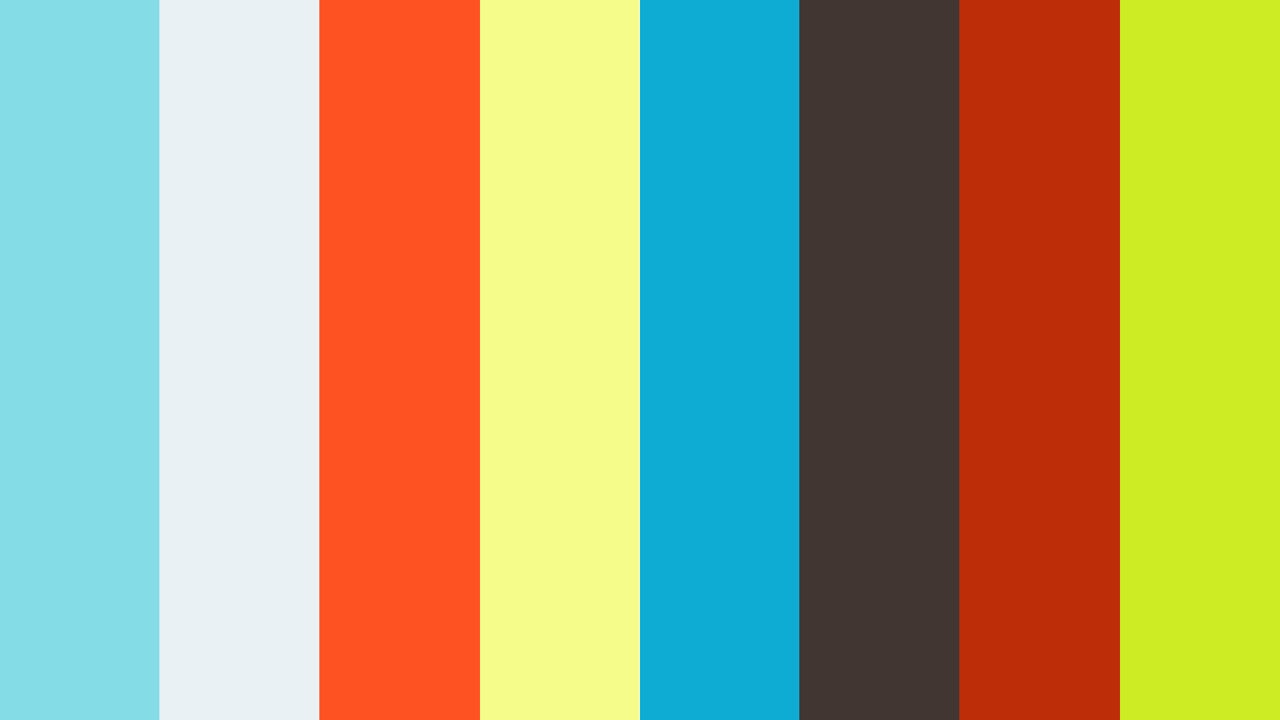
The industrial managers are responsible for overseeing the smooth running of manufacturing plants. They decide how to best utilize employees and equipment, meet production standards, and make strategic decisions. These workers are responsible for the hiring and evaluation of workers, as well as setting production schedules and following safety procedures. They oversee the day to day activities of a group of workers and analyze the production process continuously to ensure that it runs efficiently and at its peak efficiency.
An industrial production manager's earnings potential is dependent on both the employer and their experience. Although it's impossible to predict the future earnings of industrial producers, the average salary was $103,380 in May 2016, with the highest-paid earning industrial production managers earning $172,000. Also, higher earnings are possible for industrial production managers who have had advanced training and certification. According to the U.S. Bureau of Labor Statistics industrial production managers who have earned a bachelor’s degree or higher could earn more.
Work environment
A manager of industrial production divides their time between the production floor or an office. Sometimes, they live in the same building. When working in production areas, industrial production managers should adhere to established health and safety procedures and wear the appropriate protective equipment. They spend significant time in meetings with their subordinates, as well as analyzing production data. These managers might also create reports. The work environment of an industrial production manager is dynamic.
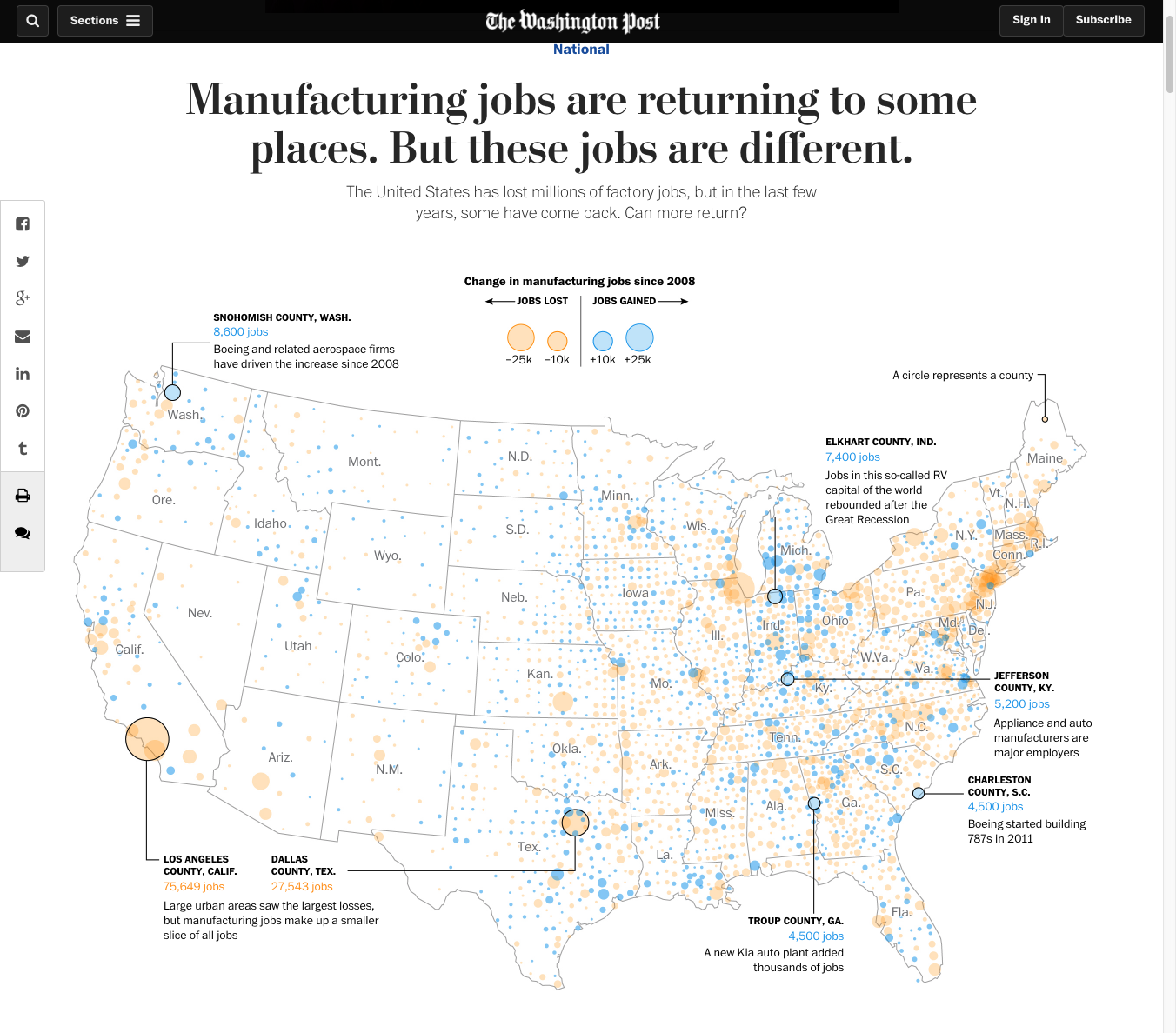
Industrial production managers play a key role in a company's overall management structure. They are responsible for coordinating the activities of workers and increasing productivity. A primary responsibility of an industrial production manager is increasing productivity and ensuring safety. Due to corporate restructuring, many levels have been eliminated and support staff reduced. Production managers are now able to handle more of the work load. This can be a significant challenge for any manager, and can make it difficult to do the job as a production manager.
FAQ
How can manufacturing efficiency improved?
First, we need to identify which factors are most critical in affecting production times. Next, we must find ways to improve those factors. If you don't know where to start, then think about which factor(s) have the biggest impact on production time. Once you identify them, look for solutions.
What are the 7 Rs of logistics?
The acronym 7R's for Logistics stands to represent the seven basic principles in logistics management. It was created by the International Association of Business Logisticians and published in 2004 under its "Seven Principles of Logistics Management".
The following letters form the acronym:
-
Responsive - ensure all actions are legal and not harmful to others.
-
Reliable - You can have confidence that you will fulfill your promises.
-
Be responsible - Use resources efficiently and avoid wasting them.
-
Realistic - consider all aspects of operations, including cost-effectiveness and environmental impact.
-
Respectful: Treat others with fairness and equity
-
You are resourceful and look for ways to save money while increasing productivity.
-
Recognizable - provide customers with value-added services.
What does it mean to be a manufacturer?
Manufacturing Industries refers to businesses that manufacture products. Consumers are people who purchase these goods. To accomplish this goal, these companies employ a range of processes including distribution, sales, management, and production. They make goods from raw materials with machines and other equipment. This includes all types manufactured goods such as clothing, building materials, furniture, electronics, tools and machinery.
Is automation important in manufacturing?
Automation is essential for both manufacturers and service providers. They can provide services more quickly and efficiently thanks to automation. It also helps to reduce costs and improve productivity.
Can some manufacturing processes be automated?
Yes! Yes! Automation has existed since ancient times. The Egyptians created the wheel thousands years ago. Robots are now used to assist us in assembly lines.
In fact, there are several applications of robotics in manufacturing today. These include:
-
Robots for assembly line
-
Robot welding
-
Robot painting
-
Robotics inspection
-
Robots create products
Manufacturing can also be automated in many other ways. 3D printing, for example, allows us to create custom products without waiting for them to be made.
Why automate your warehouse
Modern warehousing has seen automation take center stage. With the rise of ecommerce, there is a greater demand for faster delivery times as well as more efficient processes.
Warehouses have to be flexible to meet changing requirements. In order to do this, they need to invest in technology. The benefits of automating warehouses are numerous. These are some of the benefits that automation can bring to warehouses:
-
Increases throughput/productivity
-
Reduces errors
-
Increases accuracy
-
Safety increases
-
Eliminates bottlenecks
-
Companies can scale up more easily
-
It makes workers more efficient
-
Gives you visibility into all that is happening in your warehouse
-
Enhances customer experience
-
Improves employee satisfaction
-
It reduces downtime, and increases uptime
-
This ensures that quality products are delivered promptly
-
Eliminates human error
-
Helps ensure compliance with regulations
How can I find out more about manufacturing?
Experience is the best way for you to learn about manufacturing. If that is not possible, you could always read books or view educational videos.
Statistics
- In 2021, an estimated 12.1 million Americans work in the manufacturing sector.6 (investopedia.com)
- Job #1 is delivering the ordered product according to specifications: color, size, brand, and quantity. (netsuite.com)
- It's estimated that 10.8% of the U.S. GDP in 2020 was contributed to manufacturing. (investopedia.com)
- (2:04) MTO is a production technique wherein products are customized according to customer specifications, and production only starts after an order is received. (oracle.com)
- According to the United Nations Industrial Development Organization (UNIDO), China is the top manufacturer worldwide by 2019 output, producing 28.7% of the total global manufacturing output, followed by the United States, Japan, Germany, and India.[52][53] (en.wikipedia.org)
External Links
How To
Six Sigma in Manufacturing
Six Sigma is "the application statistical process control (SPC), techniques for continuous improvement." It was developed by Motorola's Quality Improvement Department at their plant in Tokyo, Japan, in 1986. Six Sigma's main goal is to improve process quality by standardizing processes and eliminating defects. Many companies have adopted Six Sigma in recent years because they believe that there are no perfect products and services. The main goal of Six Sigma is to reduce variation from the mean value of production. This means that if you take a sample of your product, then measure its performance against the average, you can find out what percentage of the time the process deviates from the norm. If you notice a large deviation, then it is time to fix it.
Understanding how your business' variability is a key step towards Six Sigma implementation is the first. Once you've understood that, you'll want to identify sources of variation. These variations can also be classified as random or systematic. Random variations happen when people make errors; systematic variations are caused externally. These are, for instance, random variations that occur when widgets are made and some fall off the production line. However, if you notice that every time you assemble a widget, it always falls apart at exactly the same place, then that would be a systematic problem.
Once you identify the problem areas, it is time to create solutions. It might mean changing the way you do business or redesigning it entirely. After implementing the new changes, you should test them again to see if they worked. If they don't work, you will need to go back to the drawing boards and create a new plan.