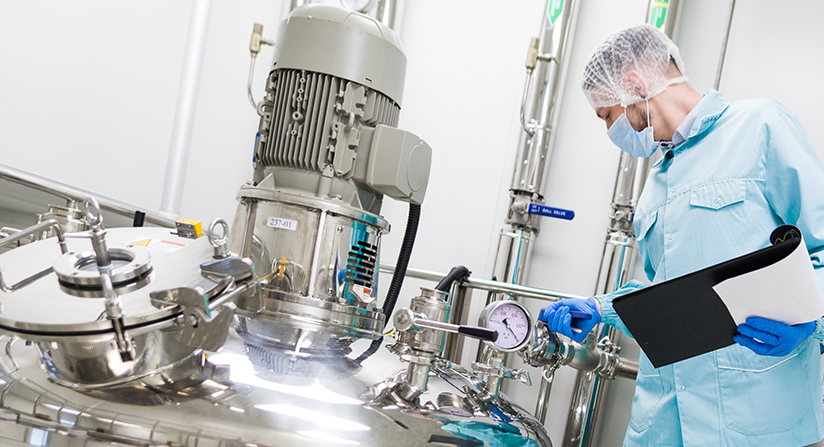
Over the years, global supplies chains have been subject to many changes. They have gone from being an industrial problem into a serious economic problem. It is a good idea to keep an eye on the latest developments. Global supply chains interact in many different ways.
Global value chains include a mixture of capital, intangibles, and flows. They reflect economies that are large, sustainable and specialized. Some value chains require high capital investment, while others are more regionalized.
Global supply chains are increasingly complex, multidimensional and dynamic. They are vital for the functioning of economies and global trade. They are susceptible to disruptions. These disruptions could be either temporary or permanent. Building a resilient, flexible, and diversified supply chain is the best way to combat these disruptions. This requires a comprehensive approach including strategic initiatives and risk management. The first step towards creating a supply-chain that can withstand future storms is to identify and evaluate the greatest problems.
A company should not only assess the risk of supply chain disruptions but also consider the potential risks associated with manufacturing, energy and materials. They should also simulate extreme supply-and-demand disruptions in order to determine their impact. They should also evaluate their inventories of crucial materials and make sure that they have enough to meet the foreseeable demand. The strategic approach to developing a resilient supply supply chain is critical. It may require reprioritizing manufacturing, shifting manufacturing locations to more flexible locations, improving supply chains technology, and implementing reliable sources of supply.
The COVID-19 epidemic caused severe disruptions in global supply chain operations. Several countries imposed tariffs on each other, while others imposed sanctions against each other. These tariffs and sanctions have increased trade frictions and made it more difficult for the United States to sell certain products to China and other countries. These disruptions have exacerbated inflation. However, these disruptions have made companies more aware and re-examined the design and implementation aspects of their supply channels.
While the COVID-19 pandemic caused widespread disruption in global supply chains, the effects are still being felt. For instance, supply chain disruptions resulting from the Suez Canal blocking have been ongoing for six months. The result has been a dramatic rise in freight costs. The UK's annual inflation is now at 9%.
It is difficult not to notice that China and America are at the center of a trade war. Supply chain leaders must question the logic of heavily relying on outsourced networks. They should also consider the risks associated with labor shortages associated with economic shocks. Leaders in supply chains should also be aware of the potential benefits of cross-border finance as well as regulation that can help expand global integration.
Even with all the turmoil, the world is still a highly interconnected place. The benefits of global integration will be realized if firms are willing to take a more holistic approach to their supply chains.
FAQ
What are the products and services of logistics?
Logistics refers to the movement of goods from one place to another.
These include all aspects related to transport such as packaging, loading and transporting, storing, transporting, unloading and warehousing inventory management, customer service. Distribution, returns, recycling are some of the options.
Logisticians ensure the product reaches its destination in the most efficient manner. Logisticians help companies improve their supply chain efficiency by providing information about demand forecasts and stock levels, production schedules, as well as availability of raw materials.
They also keep track of shipments in transit, monitor quality standards, perform inventories and order replenishment, coordinate with suppliers and vendors, and provide support services for sales and marketing.
How can I learn about manufacturing?
The best way to learn about manufacturing is through hands-on experience. If that is not possible, you could always read books or view educational videos.
What types of jobs can you find in logistics
There are many kinds of jobs available within logistics. Here are some:
-
Warehouse workers – They load and unload pallets and trucks.
-
Transport drivers - These are people who drive trucks and trailers to transport goods or perform pick-ups.
-
Freight handlers – They sort and package freight at warehouses.
-
Inventory managers: They are responsible for the inventory and management of warehouses.
-
Sales representatives - They sell products to customers.
-
Logistics coordinators – They plan and coordinate logistics operations.
-
Purchasing agents – They buy goods or services necessary to run a company.
-
Customer service representatives are available to answer customer calls and emails.
-
Shipping clerks: They process shipping requests and issue bills.
-
Order fillers: They fill orders based off what has been ordered and shipped.
-
Quality control inspectors (QCI) - They inspect all incoming and departing products for potential defects.
-
Others – There are many other types available in logistics. They include transport supervisors, cargo specialists and others.
Statistics
- Job #1 is delivering the ordered product according to specifications: color, size, brand, and quantity. (netsuite.com)
- It's estimated that 10.8% of the U.S. GDP in 2020 was contributed to manufacturing. (investopedia.com)
- In the United States, for example, manufacturing makes up 15% of the economic output. (twi-global.com)
- [54][55] These are the top 50 countries by the total value of manufacturing output in US dollars for its noted year according to World Bank.[56] (en.wikipedia.org)
- (2:04) MTO is a production technique wherein products are customized according to customer specifications, and production only starts after an order is received. (oracle.com)
External Links
How To
Six Sigma in Manufacturing
Six Sigma refers to "the application and control of statistical processes (SPC) techniques in order to achieve continuous improvement." Motorola's Quality Improvement Department created Six Sigma at their Tokyo plant, Japan in 1986. Six Sigma's basic concept is to improve quality and eliminate defects through standardization. Many companies have adopted Six Sigma in recent years because they believe that there are no perfect products and services. Six Sigma's primary goal is to reduce variation from the average value of production. It is possible to measure the performance of your product against an average and find the percentage of time that it differs from the norm. If this deviation is too big, you know something needs fixing.
Understanding how your business' variability is a key step towards Six Sigma implementation is the first. Once you have a good understanding of the basics, you can identify potential sources of variation. You'll also want to determine whether these variations are random or systematic. Random variations are caused when people make mistakes. While systematic variations are caused outside of the process, they can occur. Random variations would include, for example, the failure of some widgets to fall from the assembly line. However, if you notice that every time you assemble a widget, it always falls apart at exactly the same place, then that would be a systematic problem.
Once you've identified the problem areas you need to find solutions. You might need to change the way you work or completely redesign the process. Once you have implemented the changes, it is important to test them again to ensure they work. If they don't work you need to rework them and come up a better plan.