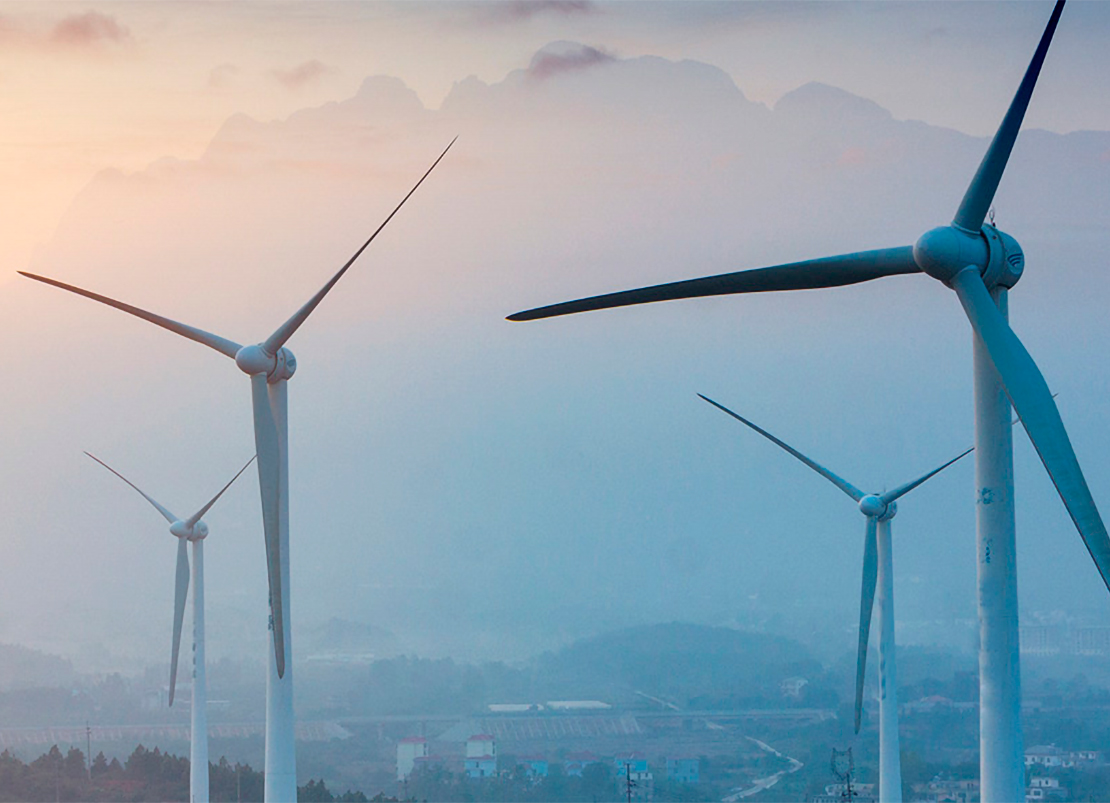
If you want to ensure your product is profitable, it is important to factor in manufacturing costs. You may need to buy wood, adhesives and other materials if your plan is to sell wooden tabletop furnishings. So that your finished product is durable, it is important to source the best raw material from reliable suppliers. If you do not use high quality materials, you could be left with a broken item and lost revenue.
It is best to break down manufacturing costs into three categories. Each of these costs will have an effect on the final cost of the product you are selling. One of the most important components of a manufacturing cost is the unit cost, which is the amount of money it costs to produce an item. This number is a good place to start, but it is a tricky concept to pin down.
The units-per-hour or unit-per-unit ratio is a good rule of thumb to use when determining the most cost-effective manufacturing process for your company. By calculating how many hours each project takes, you can determine the average cost to make 5,000 wooden furniture tables.
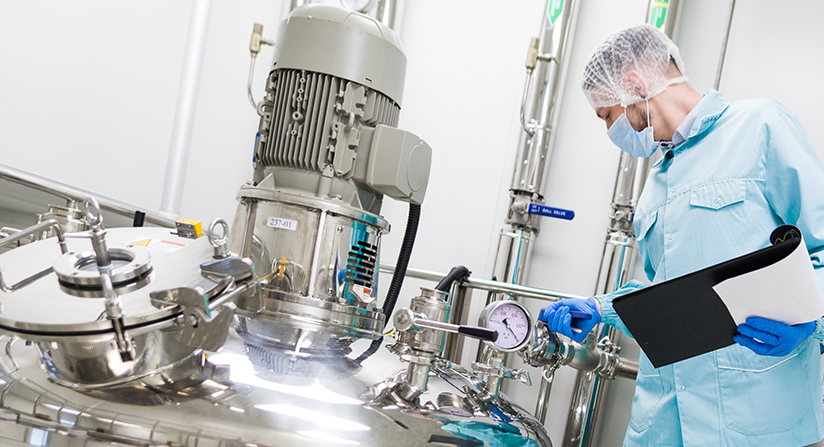
You will need to budget for general and administrative expenses, in addition to direct labor. Advertising costs, office supplies and rent are all possible. For regulatory compliance, you will have to spend a lot. Online inventory control software can be used to track and forecast production.
Direct labor costs are the wages paid to workers in a factory, and includes employees engaged in the actual preparation of the goods for manufacturing. These costs may include staff such as maintenance, sanitation, and bookkeepers. The hourly rate for direct labor is generally around $150 an hour.
Indirect costs are part of manufacturing. They include utility bills, equipment maintenance, and other costs. To calculate the unit-per-hour you need to include the costs of preparation, assembly and delivery. The manufacturing overhead account can be used to estimate your overhead for the next fiscal year and calculate the total cost of your operations.
You should also take into account the cost of manufacturing a product. Wood, thread, or cotton are just a few examples. The use of low quality materials can lead you to poor products. Food producers in certain countries will need testing to ensure your products are safe to eat.
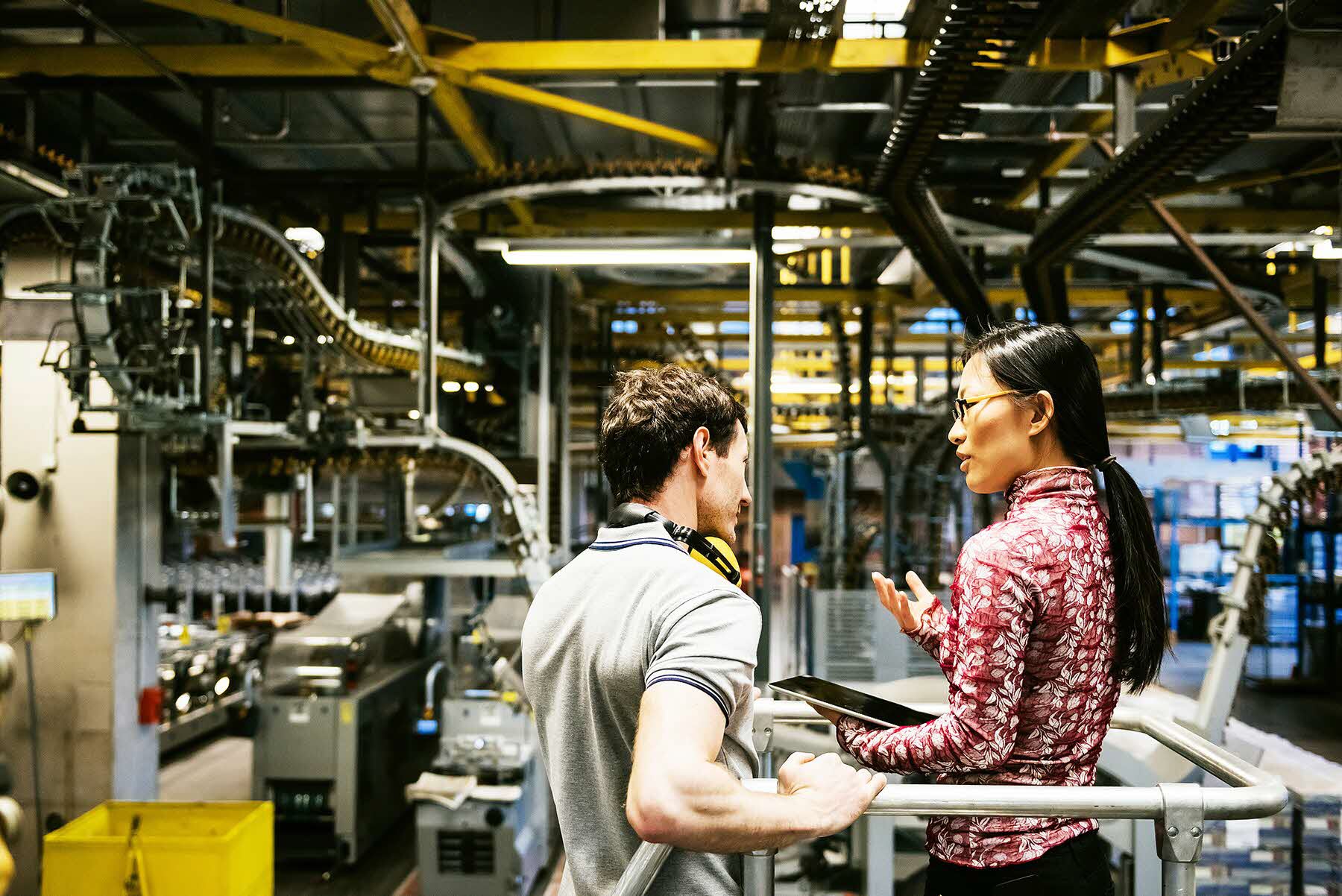
To determine whether you should produce a new product, you will need to know the unit-per–unit ratio and the manufacturing costs. You should also know the price you should charge for your products to increase your business' profitability.
FAQ
What does warehouse refer to?
Warehouses and storage facilities are where goods are kept before being sold. You can have it indoors or outdoors. In some cases it could be both indoors and outdoors.
What is the difference between manufacturing and logistics
Manufacturing is the process of creating goods from raw materials by using machines and processes. Logistics is the management of all aspects of supply chain activities, including procurement, production planning, distribution, warehousing, inventory control, transportation, and customer service. Manufacturing and logistics can often be grouped together to describe a larger term that covers both the creation of products, and the delivery of them to customers.
What does it take for a logistics enterprise to succeed?
To be a successful businessman in logistics, you will need many skills and knowledge. To communicate effectively with clients and suppliers, you must be able to communicate well. You must be able analyze data and draw out conclusions. You must be able to work well under pressure and handle stressful situations. To improve efficiency, you must be innovative and creative. You need to have strong leadership qualities to motivate team members and direct them towards achieving organizational goals.
You must be organized to meet tight deadlines.
What is the difference in Production Planning and Scheduling, you ask?
Production Planning (PP), is the process of deciding what production needs to take place at any given time. This is done through forecasting demand and identifying production capacities.
Scheduling refers to the process of allocating specific dates to tasks in order that they can be completed within a specified timeframe.
How can manufacturing efficiency be improved?
First, identify the factors that affect production time. The next step is to identify the most important factors that affect production time. If you don’t know where to begin, consider which factors have the largest impact on production times. Once you've identified them all, find solutions to each one.
Why is logistics important in manufacturing
Logistics are an essential part of any business. They are essential to any business's success.
Logistics plays a significant role in reducing cost and increasing efficiency.
How can manufacturing overproduction be reduced?
It is essential to find better ways to manage inventory to reduce overproduction. This would reduce the time spent on unproductive activities like purchasing, storing and maintaining excess stock. This could help us free up our time for other productive tasks.
This can be done by using a Kanban system. A Kanban board is a visual display used to track work in progress. Work items are moved through various states to reach their destination in a Kanban system. Each state has a different priority level.
If work is moving from one stage to the other, then the current task can be completed and moved on to the next. But if a task remains in the beginning stages it will stay that way until it reaches its end.
This allows you to keep work moving along while making sure that no work gets neglected. A Kanban board allows managers to monitor how much work is being completed at any given moment. This allows them the ability to adjust their workflow using real-time data.
Lean manufacturing can also be used to reduce inventory levels. Lean manufacturing works to eliminate waste throughout every stage of the production chain. Anything that does nothing to add value to a product is waste. Some common types of waste include:
-
Overproduction
-
Inventory
-
Unnecessary packaging
-
Excess materials
Manufacturers can reduce their costs and improve their efficiency by using these ideas.
Statistics
- In the United States, for example, manufacturing makes up 15% of the economic output. (twi-global.com)
- It's estimated that 10.8% of the U.S. GDP in 2020 was contributed to manufacturing. (investopedia.com)
- In 2021, an estimated 12.1 million Americans work in the manufacturing sector.6 (investopedia.com)
- According to the United Nations Industrial Development Organization (UNIDO), China is the top manufacturer worldwide by 2019 output, producing 28.7% of the total global manufacturing output, followed by the United States, Japan, Germany, and India.[52][53] (en.wikipedia.org)
- According to a Statista study, U.S. businesses spent $1.63 trillion on logistics in 2019, moving goods from origin to end user through various supply chain network segments. (netsuite.com)
External Links
How To
How to use 5S in Manufacturing to Increase Productivity
5S stands to stand for "Sort", “Set In Order", “Standardize", and "Store". Toyota Motor Corporation created the 5S methodology in 1954. It assists companies in improving their work environments and achieving higher efficiency.
This method has the basic goal of standardizing production processes to make them repeatable. Cleaning, sorting and packing are all done daily. Workers can be more productive by knowing what to expect.
Five steps are required to implement 5S: Sort, Set In Order, Standardize. Separate. Each step involves a different action which leads to increased efficiency. Sorting things makes it easier to find them later. When you arrange items, you place them together. After you have divided your inventory into groups you can store them in easy-to-reach containers. Labeling your containers will ensure that everything is correctly labeled.
Employees need to reflect on how they do their jobs. Employees must be able to see why they do what they do and find a way to achieve them without having to rely on their old methods. They must learn new skills and techniques in order to implement the 5S system.
The 5S Method not only improves efficiency, but it also helps employees to be more productive and happier. They feel more motivated to work towards achieving greater efficiency as they see the results.