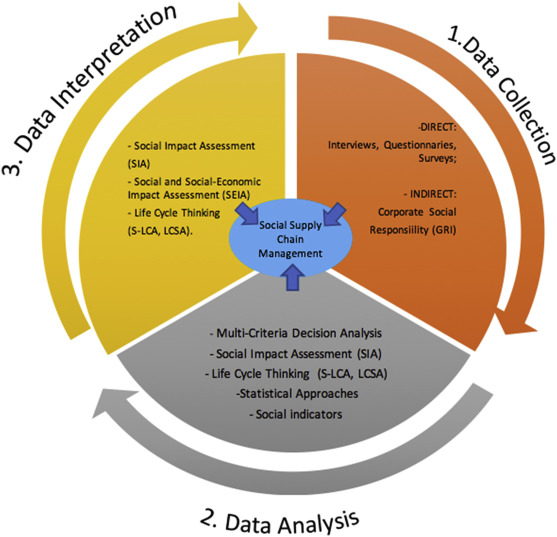
During his tenure as CEO of Wiremold, Art Byrne introduced a series of innovations that helped the company achieve its goal of reducing costs while increasing productivity. Byrne demonstrated a keen understanding of how the team can be engaged in this lean manufacturing case. Byrne encouraged the team to learn from each other while implementing the changes and included everyone in the kaizen process.
He established a lean program to track the flow of parts throughout the manufacturing process. He also introduced tools to increase productivity and reduce waste. He invented a laser cutting machine which allowed for small quantities to be produced. This saved him money on tooling. He used a simple strategy to achieve his success, which only required a few steps.
He also implemented a just in time (JIT) manufacturing process. This manufacturing method allowed the company's vehicles to be delivered quickly. Harmony was also possible during the manufacturing process. This was key to reducing the amount of waste.
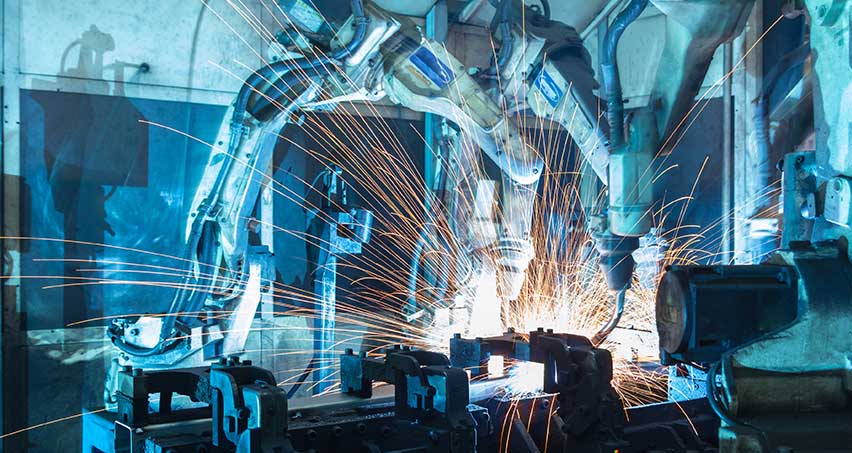
He was open to problem solving and developed a tool maintenance plan that saved the company $2 million during the recession. He also implemented an early retirement plan for unionized workers. These moves helped him transform Wiremold from a haphazard, inefficient company into a Lean-oriented one.
He also introduced a system to monitor the flow of raw materials during the manufacturing process. He also implemented a new ERP system. He made sure all his team members understood the importance respecting their employees. His lean strategy was simple and effective. This allowed him make sure all employees understood the concept. His management style fostered respect for employees and encouraged a hands-on approach.
His greatest asset was his understanding of the kaizen process. Danaher Corporation had been his employer for a while, and he was familiar with the three Ps of a good kaizen: process, product, and people. He also reduced the number of salaried workers. His kaizen strategy was a way for him to ensure that his team did the right thing.
He also introduced value stream mapping. This diagram illustrates the impact of manufacturing resources on overall company efficiency. He also introduced Kaizen events worksheets, which can help track key improvement efforts. A chart that shows overall achievements displays the results.
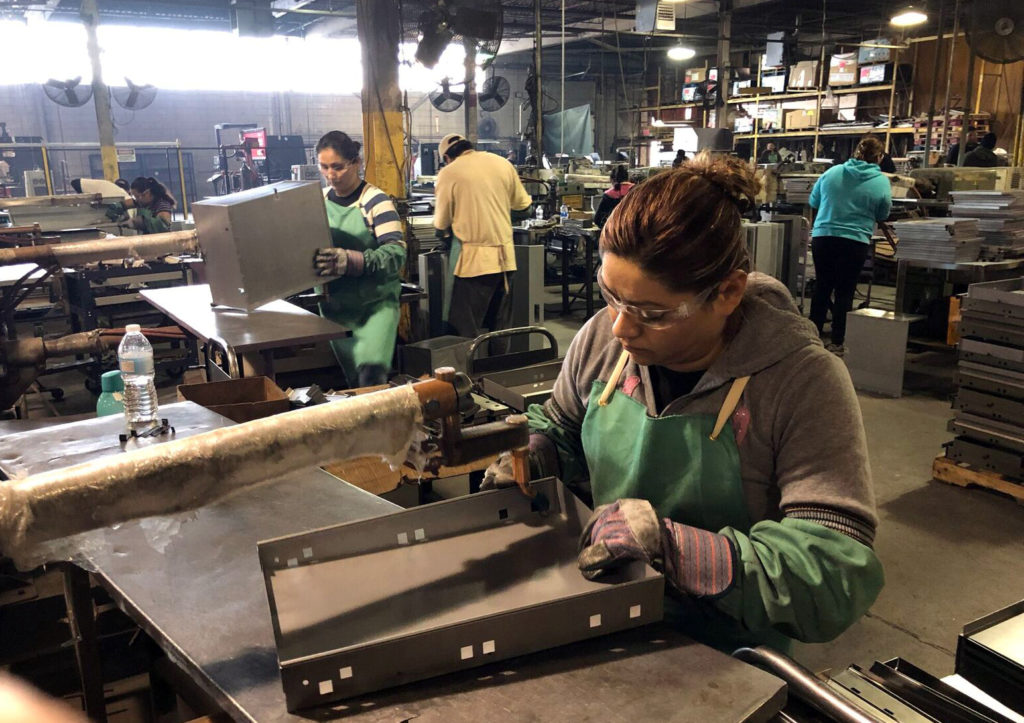
He also created a system for reducing lead times, which is crucial for the manufacturing industry. The fine blank machine was capable of producing 600 to 800 blades per hour. It also eliminated the need for a lot of manual work. The kanban card is another tool that was used for reducing lead time.
Wiremold was a major leader in the manufacturing of conduit casing. In just ten year, sales rose from 100 million dollars up to 450 millions. French competitor Legrand purchased the company in 2001. Wiremold was not always a success. Its biggest problem was the queue processing which left designated stations with either too much work or too little.
FAQ
What is it like to manage a logistics company?
A successful logistics business requires a lot more than just knowledge. Effective communication skills are necessary to work with suppliers and clients. You should be able analyse data and draw inferences. You must be able and able to handle stress situations and work under pressure. You must be creative and innovative to develop new ideas to improve efficiency. Strong leadership qualities are essential to motivate your team and help them achieve their organizational goals.
You should also be organized and efficient to meet tight deadlines.
What is the responsibility of a logistics manager?
A logistics manager makes sure that all goods are delivered on-time and in good condition. This is accomplished by using the experience and knowledge gained from working with company products. He/she should make sure that enough stock is on hand to meet the demands.
How can we reduce manufacturing overproduction?
In order to reduce excess production, you need to develop better inventory management methods. This would reduce time spent on activities such as purchasing, stocking, and maintaining excess stock. We could use these resources to do other productive tasks.
This can be done by using a Kanban system. A Kanban board is a visual display used to track work in progress. A Kanban system allows work items to move through several states before reaching their final destination. Each state represents a different priority level.
When work is completed, it can be transferred to the next stage. However, if a task is still at the beginning stages, it will remain so until it reaches the end of the process.
This allows work to move forward and ensures that no work is missed. With a Kanban board, managers can see exactly how much work is being done at any given moment. This information allows managers to adjust their workflow based off real-time data.
Lean manufacturing can also be used to reduce inventory levels. Lean manufacturing focuses on eliminating waste throughout the entire production chain. Anything that does not contribute to the product's value is considered waste. These are some of the most common types.
-
Overproduction
-
Inventory
-
Packaging that is not necessary
-
Exceed materials
These ideas will help manufacturers increase efficiency and lower costs.
What does warehouse refer to?
Warehouses and storage facilities are where goods are kept before being sold. It can be an outdoor or indoor area. In some cases, it may be a combination of both.
What are the responsibilities for a manufacturing manager
A manufacturing manager must ensure that all manufacturing processes are efficient and effective. They must also be alert to any potential problems and take appropriate action.
They should also be able communicate with other departments, such as sales or marketing.
They should be informed about industry trends and be able make use of this information to improve their productivity and efficiency.
Statistics
- Many factories witnessed a 30% increase in output due to the shift to electric motors. (en.wikipedia.org)
- Job #1 is delivering the ordered product according to specifications: color, size, brand, and quantity. (netsuite.com)
- [54][55] These are the top 50 countries by the total value of manufacturing output in US dollars for its noted year according to World Bank.[56] (en.wikipedia.org)
- You can multiply the result by 100 to get the total percent of monthly overhead. (investopedia.com)
- In 2021, an estimated 12.1 million Americans work in the manufacturing sector.6 (investopedia.com)
External Links
How To
Six Sigma: How to Use it in Manufacturing
Six Sigma is defined as "the application of statistical process control (SPC) techniques to achieve continuous improvement." Motorola's Quality Improvement Department in Tokyo, Japan developed Six Sigma in 1986. Six Sigma's core idea is to improve the quality of processes by standardizing and eliminating defects. Many companies have adopted this method in recent years. They believe there is no such thing a perfect product or service. Six Sigma aims to reduce variation in the production's mean value. This means that you can take a sample from your product and then compare its performance to the average to find out how often the process differs from the norm. If this deviation is too big, you know something needs fixing.
The first step toward implementing Six Sigma is understanding how variability works in your business. Once you have a good understanding of the basics, you can identify potential sources of variation. Also, you will need to identify the sources of variation. Random variations occur when people make mistakes; systematic ones are caused by factors outside the process itself. If you make widgets and some of them end up on the assembly line, then those are considered random variations. You might notice that your widgets always fall apart at the same place every time you put them together.
Once you've identified the problem areas you need to find solutions. You might need to change the way you work or completely redesign the process. To verify that the changes have worked, you need to test them again. If they don't work, you will need to go back to the drawing boards and create a new plan.