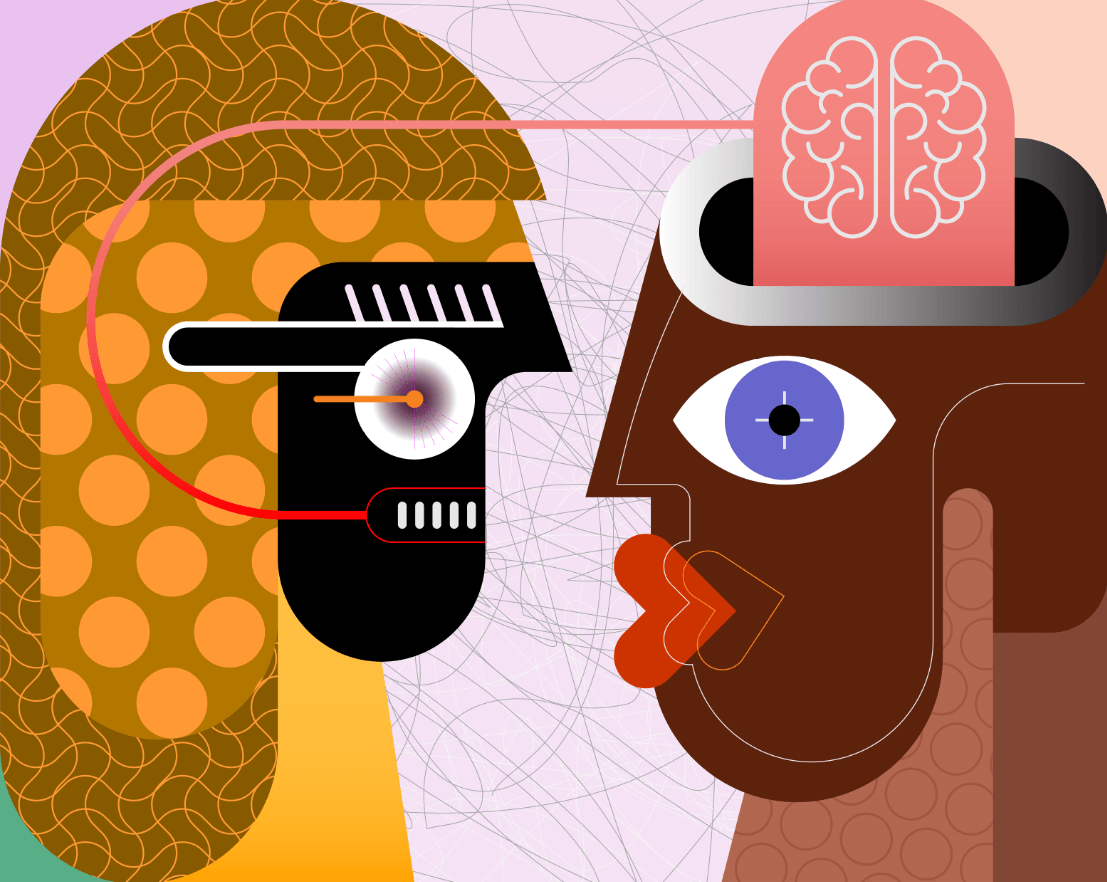
In a globalized world, where factories are moving to other countries due to globalization, it is easy to lose sight of how many products are still manufactured in America. There are many products that Americans love, from candy to vehicles and beers.
Find American-Made Products
Made in America is one of the most powerful labels in business. It evokes patriotism, and a promise of quality that's not spoken. This is a way to show that the company cares about the safety and future of the workers.
It is important to also understand how the actual labeling of a product takes place. The Federal Trade Commission has guidelines that manufacturers must follow when using this phrase.
Generally, a product can only claim to be made in the United States if every significant part, processing, and labor that went into making it is derived from raw materials in the United States. However, a manufacturer can make an unqualified claim that tells consumers their product was made in the United States using only certain foreign components.
Some companies that advertise "Made in the USA" may not have met all of these requirements, according to FTC attorney Julia Solomon Ensor. This is particularly true for products like gas grills that are assembled and shipped in the United States, but then sent to a distributor in another country.
The Federal Trade Commission is cracking down on companies that boast "Made in the USA" claims but that do not meet these requirements. The Federal Trade commission explains the need for the terms to be clearly defined. They must also cover the entire product.
Searching for items that were made in the United States can be done by both category and country. If you are shopping for furniture or bedding, you can use our link to narrow down your search.
You can type the name of a manufacturer in the search bar when you are looking for an item to see if it is made in America. This is a way to show the companies you support that they should do more to promote American manufacturing.
Check out the Made in the USA Website from a business like Wayfair. It does a fantastic job at labeling the products by their country of origin. They have an entire section dedicated to US-made items.
It's not hard to find items that are made in the United States on their websites, but if you have any questions or concerns about a specific item, you can always contact them through our link and ask! They'll get back to you as soon as possible.
You can find American-made toys, clothing and more at these retailers. On their website, they list over 500 different items as "Made by USA", making this a great place for you to start your hunt for authentically made products in the United States.
FAQ
How can we reduce manufacturing overproduction?
Better inventory management is key to reducing excess production. This would reduce time spent on activities such as purchasing, stocking, and maintaining excess stock. This could help us free up our time for other productive tasks.
You can do this by adopting a Kanban method. A Kanban board, a visual display to show the progress of work, is called a Kanban board. Work items are moved through various states to reach their destination in a Kanban system. Each state is assigned a different priority.
To illustrate, work can move from one stage or another when it is complete enough for it to be moved to a new stage. But if a task remains in the beginning stages it will stay that way until it reaches its end.
This allows you to keep work moving along while making sure that no work gets neglected. With a Kanban board, managers can see exactly how much work is being done at any given moment. This allows them to adjust their workflows based on real-time information.
Lean manufacturing is another way to manage inventory levels. Lean manufacturing is about eliminating waste from all stages of the production process. Anything that does not contribute to the product's value is considered waste. These are some of the most common types.
-
Overproduction
-
Inventory
-
Packaging not required
-
Overstock materials
Manufacturers can reduce their costs and improve their efficiency by using these ideas.
What skills do production planners need?
You must be flexible and organized to become a productive production planner. You must also be able to communicate effectively with clients and colleagues.
What is the difference between manufacturing and logistics
Manufacturing refers to the process of making goods using raw materials and machines. Logistics manages all aspects of the supply chain, including procurement, production planning and distribution, inventory control, transportation, customer service, and transport. Sometimes manufacturing and logistics are combined to refer to a wider term that includes both the process of creating products as well as their delivery to customers.
What is the role of a logistics manager
Logistics managers ensure that goods arrive on time and are unharmed. This is achieved by using their knowledge and experience with the products of the company. He/she must also ensure sufficient stock to meet the demand.
How can we increase manufacturing efficiency?
The first step is to determine the key factors that impact production time. We must then find ways that we can improve these factors. If you aren't sure where to begin, think about the factors that have the greatest impact on production time. Once you've identified them all, find solutions to each one.
What does the term manufacturing industries mean?
Manufacturing Industries refers to businesses that manufacture products. These products are sold to consumers. To accomplish this goal, these companies employ a range of processes including distribution, sales, management, and production. They produce goods from raw materials by using machines and other machinery. This includes all types if manufactured goods.
What jobs are available in logistics?
There are many kinds of jobs available within logistics. Some of them are:
-
Warehouse workers: They load and unload trucks, pallets, and other cargo.
-
Transportation drivers - They drive trucks and trailers to deliver goods and carry out pick-ups.
-
Freight handlers – They sort and package freight at warehouses.
-
Inventory managers - These are responsible for overseeing the stock of goods in warehouses.
-
Sales representatives - They sell products to customers.
-
Logistics coordinators are responsible for organizing and planning logistics operations.
-
Purchasing agents - They purchase goods and services needed for company operations.
-
Customer service representatives - Answer calls and email from customers.
-
Shipping clerks - They process shipping orders and issue bills.
-
Order fillers - They fill orders based on what is ordered and shipped.
-
Quality control inspectors - They check incoming and outgoing products for defects.
-
Others - There is a variety of other jobs in logistics. These include transportation supervisors and cargo specialists.
Statistics
- In 2021, an estimated 12.1 million Americans work in the manufacturing sector.6 (investopedia.com)
- Many factories witnessed a 30% increase in output due to the shift to electric motors. (en.wikipedia.org)
- According to a Statista study, U.S. businesses spent $1.63 trillion on logistics in 2019, moving goods from origin to end user through various supply chain network segments. (netsuite.com)
- [54][55] These are the top 50 countries by the total value of manufacturing output in US dollars for its noted year according to World Bank.[56] (en.wikipedia.org)
- According to the United Nations Industrial Development Organization (UNIDO), China is the top manufacturer worldwide by 2019 output, producing 28.7% of the total global manufacturing output, followed by the United States, Japan, Germany, and India.[52][53] (en.wikipedia.org)
External Links
How To
How to Use the Just In Time Method in Production
Just-intime (JIT), which is a method to minimize costs and maximize efficiency in business process, is one way. It allows you to get the right amount resources at the right time. This means you only pay what you use. Frederick Taylor developed the concept while working as foreman in early 1900s. Taylor observed that overtime was paid to workers if they were late in working. He decided that workers would be more productive if they had enough time to complete their work before they started to work.
JIT is an acronym that means you need to plan ahead so you don’t waste your money. Look at your entire project, from start to end. Make sure you have enough resources in place to deal with any unexpected problems. If you anticipate that there might be problems, you'll have enough people and equipment to fix them. This will prevent you from spending extra money on unnecessary things.
There are several types of JIT techniques:
-
Demand-driven: This JIT is where you place regular orders for the parts/materials that are needed for your project. This will enable you to keep track of how much material is left after you use it. This will allow you to calculate how long it will take to make more.
-
Inventory-based: This type allows you to stock the materials needed for your projects ahead of time. This allows for you to anticipate how much you can sell.
-
Project-driven: This is an approach where you set aside enough funds to cover the cost of your project. Once you have an idea of how much material you will need, you can purchase the necessary materials.
-
Resource-based JIT: This is the most popular form of JIT. Here, you allocate certain resources based on demand. You will, for example, assign more staff to deal with large orders. You'll have fewer orders if you have fewer.
-
Cost-based: This is a similar approach to resource-based but you are not only concerned with how many people you have, but also how much each one costs.
-
Price-based pricing: This is similar in concept to cost-based but instead you look at how much each worker costs, it looks at the overall company's price.
-
Material-based: This is very similar to cost-based but instead of looking at total costs of the company you are concerned with how many raw materials you use on an average.
-
Time-based: Another variation of resource-based JIT. Instead of focusing only on how much each employee is costing, you should focus on how long it takes to complete your project.
-
Quality-based JIT is another variant of resource-based JIT. Instead of focusing on the cost of each worker or how long it takes, think about how high quality your product is.
-
Value-based: This is one of the newest forms of JIT. This is where you don't care about how the products perform or whether they meet customers' expectations. Instead, your focus is on the value you bring to the market.
-
Stock-based: This stock-based method focuses on the actual quantity of products being made at any given time. It's useful when you want maximum production and minimal inventory.
-
Just-in time (JIT), planning: This is a combination JIT/supply chain management. This refers to the scheduling of the delivery of components as soon after they are ordered. It's important because it reduces lead times and increases throughput.