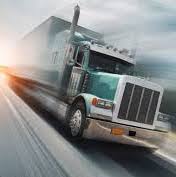
The Defense Industrial Base or DIB is a network of approximately 200,000 companies that supply goods to the Department of Defense. It includes small businesses, big corporations, and startups. A new report from the Government Accountability Office highlights the risks that the DIB faces, as well as its challenges in addressing these threats.
The defense industrial sector has suffered a nearly 40 percent decline over the past decade. As a result, the Department of Defense has struggled to attract new entrants into the sector. The Defense Department has made a number of attempts to encourage businesses to join the sector. Despite all of these efforts, smaller companies are still being left behind. This has resulted in a growing threat to national security.
Diverse DOD offices are working on mitigation of risks in the DIB. However, there is no comprehensive strategy in place to assess and manage these risk. GAO reviewed several reports and interviewed DOD personnel to determine areas that could be improved. GAO identified five components that could help the department meet its goals.
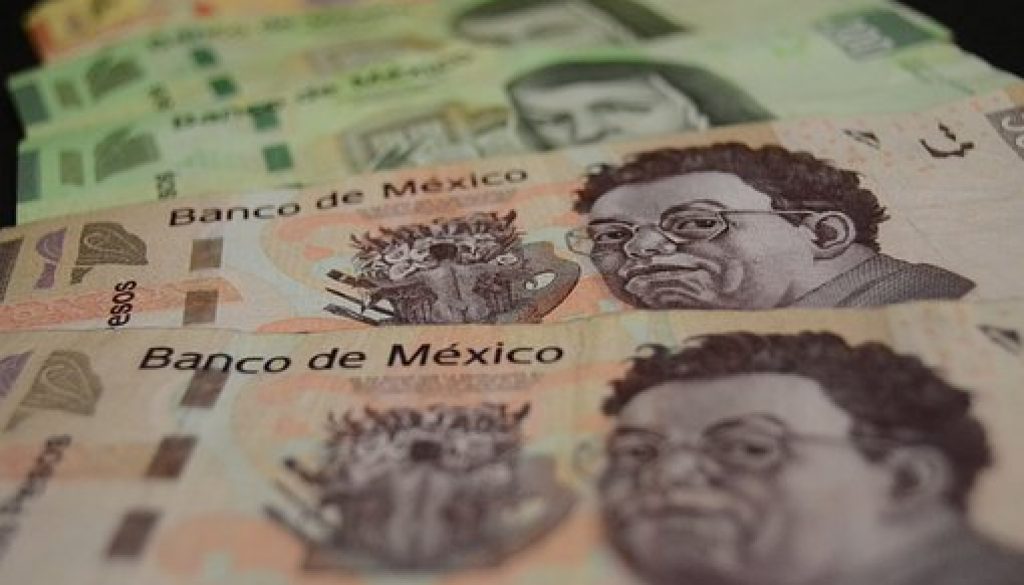
The loss of commercial suppliers is a major concern. Many of these suppliers provide parts for military weapon systems. Over the last decade, the number of small businesses in this industry has declined. There is no clear indicator of how many new companies are entering this market.
Other problems include material shortages as well as reliance on foreign vendors. The acquisition process of the military is often slowed down by intellectual property restrictions. There is also no standard definition of "new entrant" in the defense industrial bases.
GAO recommended the Department of Defense revise its policy on mitigating the risks in the DIB. The GAO recommended that the Department of Defense continue to engage traditional defense contractors as well as implement tools to make it easier for private technology providers to access the DoD market. These recommendations should form part of an overall strategy to address industrial base concerns.
As part this strategy, the Defense Department needs to think about how it can use its OTAs as well as CSOs to accelerate acquisition strategy creation. By using the right people, processes, and technologies, the supply chain can be restructured to deliver dynamic outcomes.
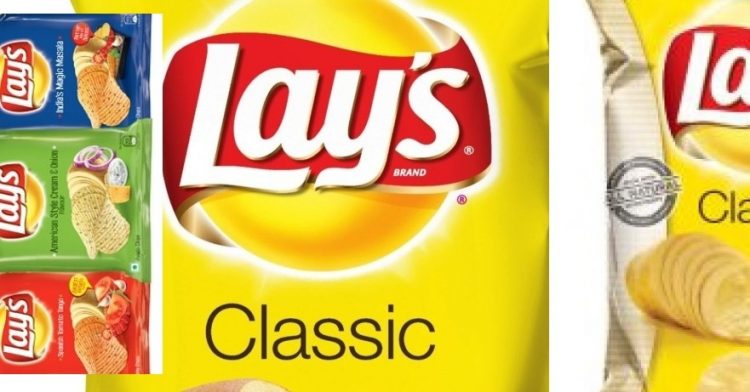
Despite the fact that the number has dropped over the past decade in defense industry, it is still developing. Many companies do not feel comfortable with the Federal Acquisition Regulation (FAR). Furthermore, the current landscape may lead to fewer opportunities for small businesses to compete.
Startups and small businesses are key to innovation in defense industrial bases. Companies that make up the resilient DIB are able to support National Security requirements and enable the Department of Defense (DoD) to develop better military equipment.
The defense industrial base is complex and requires a comprehensive strategy in order to ensure that the resources are available for the military's needs. The Department of Defense must continue to research best practices for integrating tech into its business processes. This will lead to more efficient and innovative products.
FAQ
What skills is required for a production planner?
To become a successful production planner, you need to be organized, flexible, and able to multitask. Also, you must be able and willing to communicate with clients and coworkers.
What is the job of a manufacturer manager?
A manufacturing manager must make sure that all manufacturing processes run smoothly and effectively. They should be aware of any issues within the company and respond accordingly.
They should also be able communicate with other departments, such as sales or marketing.
They should also be knowledgeable about the latest trends in the industry so they can use this information for productivity and efficiency improvements.
What is the role and responsibility of a Production Planner?
Production planners make sure that every aspect of the project is delivered on-time, within budget, and within schedule. They also ensure that the product/service meets the client’s needs.
Statistics
- It's estimated that 10.8% of the U.S. GDP in 2020 was contributed to manufacturing. (investopedia.com)
- You can multiply the result by 100 to get the total percent of monthly overhead. (investopedia.com)
- In the United States, for example, manufacturing makes up 15% of the economic output. (twi-global.com)
- According to the United Nations Industrial Development Organization (UNIDO), China is the top manufacturer worldwide by 2019 output, producing 28.7% of the total global manufacturing output, followed by the United States, Japan, Germany, and India.[52][53] (en.wikipedia.org)
- [54][55] These are the top 50 countries by the total value of manufacturing output in US dollars for its noted year according to World Bank.[56] (en.wikipedia.org)
External Links
How To
How to Use 5S to Increase Productivity in Manufacturing
5S stands for "Sort", 'Set In Order", 'Standardize', & Separate>. Toyota Motor Corporation invented the 5S strategy in 1954. It assists companies in improving their work environments and achieving higher efficiency.
This approach aims to standardize production procedures, making them predictable, repeatable, and easily measurable. This means that every day tasks such cleaning, sorting/storing, packing, and labeling can be performed. Workers can be more productive by knowing what to expect.
Five steps are required to implement 5S: Sort, Set In Order, Standardize. Separate. Each step requires a different action to increase efficiency. For example, when you sort things, you make them easy to find later. When you set items in an order, you put items together. Next, organize your inventory into categories and store them in containers that are easily accessible. Labeling your containers will ensure that everything is correctly labeled.
Employees must be able to critically examine their work practices. Employees need to understand the reasons they do certain jobs and determine if there is a better way. To implement the 5S system, employees must acquire new skills and techniques.
In addition to increasing efficiency, the 5S method also improves morale and teamwork among employees. They feel more motivated to work towards achieving greater efficiency as they see the results.