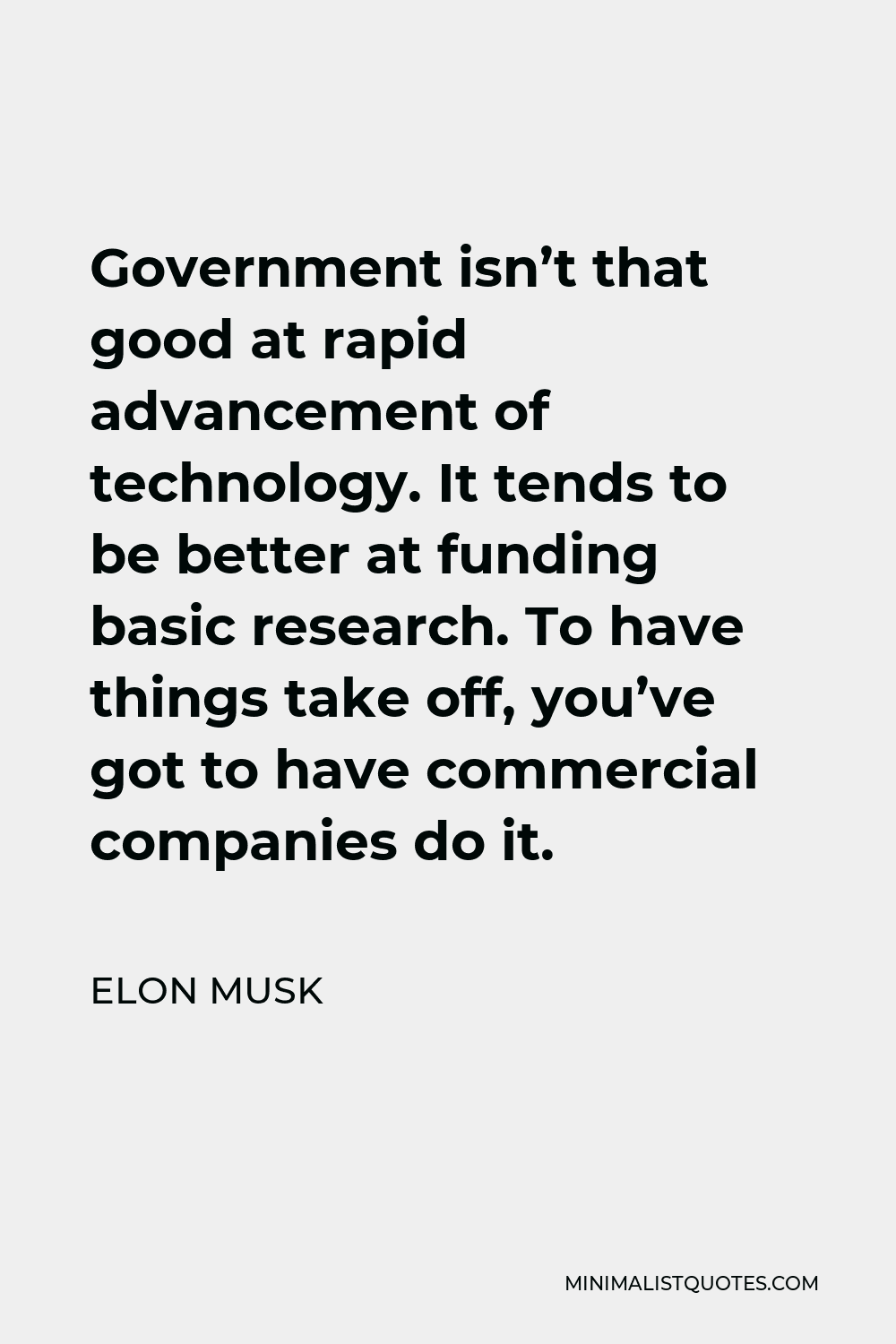
Kanban models in manufacturing can improve efficiency and lower costs. These principles aim to minimize downtime and inefficiencies. This results in faster manufacturing and delivery times, and better customer service. It also allows continuous improvement.
Kanban is a method to manage and organize work flow. Kanban helps teams and manufacturers to track and monitor their processes and improve productivity. Kanban is a visual system that displays all the steps in a process and helps to identify and minimize inefficiencies.
You can either use a software program or manually to implement the kanban method. This software can help the team determine what they should do and who should do it, so that the process is optimized. Employees can also adapt to feedback and make improvements in their work processes using the kanban method. It can also be used as a brainstorming tool.
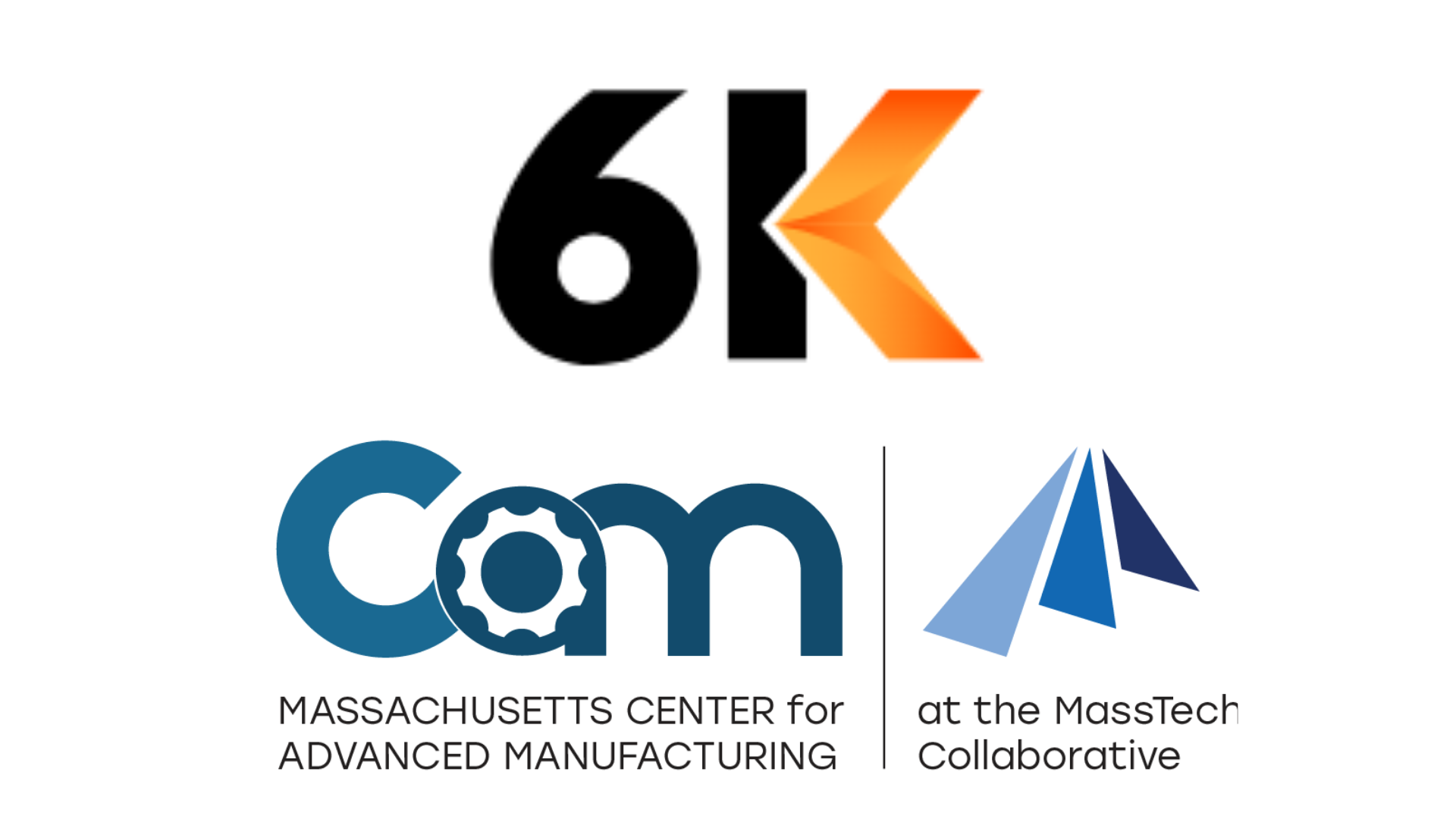
Kanban boards are a common example of Kanban in manufacturing. They depict a process. The board displays the steps involved in the process in order of priority. For example, the first task is to contact a supplier. The second task is ordering the necessary supplies to complete the job. The third task of manufacturing is the final. The fourth task will be to test and deliver the final product.
The kanban board allows teams to visualise their process and make small changes as necessary. The kanbanboard can also be used for communication and to address any bottlenecks.
The kanban method is also designed to eliminate waste, and to promote information sharing. This is especially helpful when the company wants to adopt lean principles. It is possible to accumulate waste over the course of a manufacturing operation in many ways. Manufacturers who eliminate waste are able to add real value to the entire manufacturing process. The kanban system is also useful in managing inventory. It can be used as a way to reduce inventory overstocking.
Kanban can be used to simplify the process and cut down on costs. Kanban can help improve efficiency and reduce the number of items required to complete a job. It also helps to improve communication, and to minimize downtime. The kanban system is a good example of how technology can help with a difficult task.
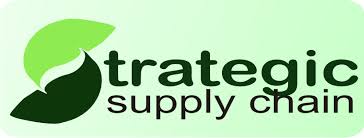
Kanban can be used for brainstorming, as well as to improve productivity. Kanban can be used to link companies to suppliers and to improve communication. It can also be used to improve quality and streamline production.
A board, which groups tasks according to their priority and how long it will take to complete them, is one of the most commonly used Kanban examples in manufacturing. The board also shows the steps involved, such as designing, manufacturing, and testing.
FAQ
What are the 7 Rs of logistics.
The acronym 7Rs of Logistics refers to the seven core principles of logistics management. It was created by the International Association of Business Logisticians and published in 2004 under its "Seven Principles of Logistics Management".
The following letters make up the acronym:
-
Responsible - ensure that actions are in compliance with legal requirements and do not cause harm to others.
-
Reliable - You can have confidence that you will fulfill your promises.
-
Use resources effectively and sparingly.
-
Realistic - consider all aspects of operations, including cost-effectiveness and environmental impact.
-
Respectful - treat people fairly and equitably.
-
Resourceful - look for opportunities to save money and increase productivity.
-
Recognizable is a company that provides customers with value-added solutions.
What is the role of a logistics manager
A logistics manager makes sure that all goods are delivered on-time and in good condition. This is done through his/her expertise and knowledge about the company's product range. He/she should ensure that sufficient stock is available in order to meet customer demand.
Is it possible to automate certain parts of manufacturing
Yes! Yes! Automation has existed since ancient times. The wheel was invented by the Egyptians thousands of years ago. Today, robots assist in the assembly of lines.
There are many uses of robotics today in manufacturing. They include:
-
Automated assembly line robots
-
Robot welding
-
Robot painting
-
Robotics inspection
-
Robots that make products
Automation can be applied to manufacturing in many other ways. For example, 3D printing allows us to make custom products without having to wait for weeks or months to get them manufactured.
What is the job of a production plan?
A production planner makes sure all project elements are delivered on schedule, within budget, as well as within the agreed scope. A production planner ensures that the service and product meet the client's expectations.
What are manufacturing and logistic?
Manufacturing is the act of producing goods from raw materials using machines and processes. Logistics covers all aspects involved in managing supply chains, including procurement and production planning. Logistics and manufacturing are often referred to as one thing. It encompasses both the creation of products and their delivery to customers.
How is a production manager different from a producer planner?
The main difference between a production planner and a project manager is that a project manager is usually the person who plans and organizes the entire project, whereas a production planner is mainly involved in the planning stage of the project.
What are the four types in manufacturing?
Manufacturing is the process that transforms raw materials into useful products. Manufacturing can include many activities such as designing and building, testing, packaging shipping, selling, servicing, and other related activities.
Statistics
- According to the United Nations Industrial Development Organization (UNIDO), China is the top manufacturer worldwide by 2019 output, producing 28.7% of the total global manufacturing output, followed by the United States, Japan, Germany, and India.[52][53] (en.wikipedia.org)
- Many factories witnessed a 30% increase in output due to the shift to electric motors. (en.wikipedia.org)
- (2:04) MTO is a production technique wherein products are customized according to customer specifications, and production only starts after an order is received. (oracle.com)
- Job #1 is delivering the ordered product according to specifications: color, size, brand, and quantity. (netsuite.com)
- In the United States, for example, manufacturing makes up 15% of the economic output. (twi-global.com)
External Links
How To
Six Sigma: How to Use it in Manufacturing
Six Sigma is defined as "the application of statistical process control (SPC) techniques to achieve continuous improvement." Motorola's Quality Improvement Department, Tokyo, Japan, developed it in 1986. Six Sigma's basic concept is to improve quality and eliminate defects through standardization. Many companies have adopted this method in recent years. They believe there is no such thing a perfect product or service. Six Sigma's primary goal is to reduce variation from the average value of production. It is possible to measure the performance of your product against an average and find the percentage of time that it differs from the norm. If the deviation is excessive, it's likely that something needs to be fixed.
Understanding how variability works in your company is the first step to Six Sigma. Once you understand this, you can then identify the causes of variation. This will allow you to decide if these variations are random and systematic. Random variations occur when people make mistakes; systematic ones are caused by factors outside the process itself. If you make widgets and some of them end up on the assembly line, then those are considered random variations. You might notice that your widgets always fall apart at the same place every time you put them together.
Once you have identified the problem, you can design solutions. The solution could involve changing how you do things, or redesigning your entire process. You should then test the changes again after they have been implemented. If they don't work you need to rework them and come up a better plan.