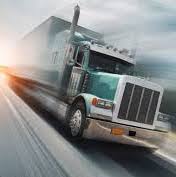
The National Network for Manufacturing Innovation's primary goal is to develop cutting-edge manufacturing technologies. President Obama announced the interagency initiative in his FY 2013 budget proposal. It is intended to bring together university engineering schools, community colleges, and federal agencies in order to commercialize innovative manufacturing technologies.
Manufacturing plays an important role in the American economy. American workers are able to find employment in this industry. To stay competitive, manufacturing firms invest in technological innovations that increase productivity and reduce labor costs. These innovations include automation as well as green energy sources. Companies invest in machine-downtime solutions. This includes the development of innovative products, such as autonomous mobile bots. These robots reduce labor costs, and increase productivity. Additionally, companies invest in technologies that reduce the waste of resources, such as smart sensor technology.
The "Maker's Economy," which is expected to transform the manufacturing process, will be revolutionizing how products are made. This economy involves manufacturing users taking an active role when designing and building new products. It uses readily available technologies. These innovations are expected by the manufacturing sector, which is expected to benefit from them to increase productivity and operational efficiency as well as enhance decision-making. It is also expected it to be a major contributor in the nation's overall production. The United States has a history of being a world leader in manufacturing.
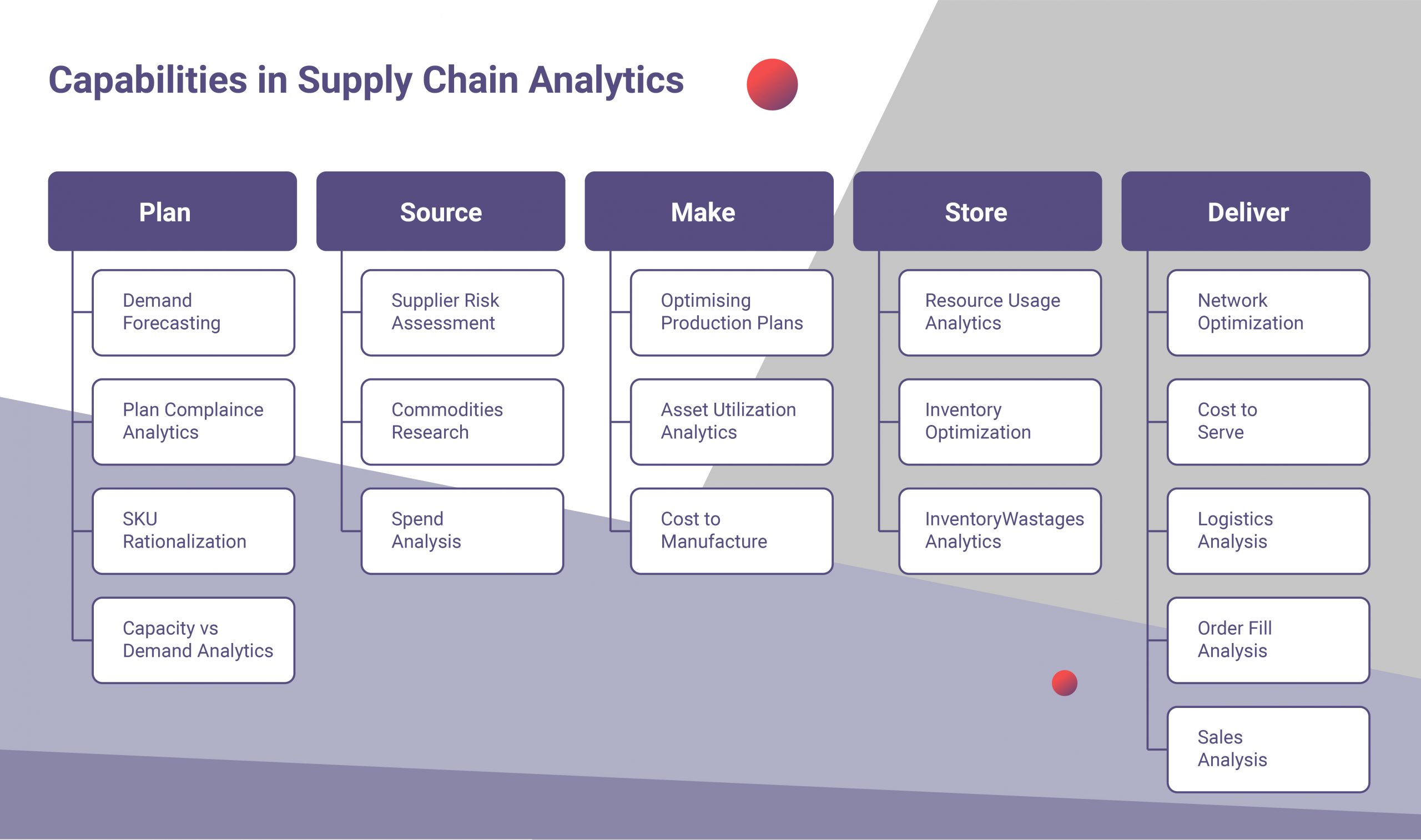
The "Maker's Economy", which is based on various technologies such as artificial intelligence and smart factories, relies heavily on these technologies. These innovations improve manufacturing productivity by increasing worker efficiency and decreasing the amount of time it takes to produce a product. The Industrial Internet of Things uses sensors to aid in tasks. It allows for continuous monitoring of industrial assets. Secure connectivity is essential to the IIoT. Data transmission must also be fast. It is expected that it will improve warehousing efficiency as well as supply chain visibility.
The National Network for Manufacturing Innovation will include at least fifteen manufacturing institutions. It is expected that it will help speed up the development of manufacturing technology. This network will also include public/private partnerships between government agencies and private companies.
There are currently 14 US manufacturing innovation institutes. The Commerce Department is expected to fund another three. In addition, the National Institute of Standards and Technology is expected to fund two Institutes. This will result in an average of $70 million per institution over five to 7 years.
Each Institute for Manufacturing Innovation will have its own research focus. They will serve as manufacturing innovation hubs for state and local economies. These Institutes will be able to assist manufacturers with their integration efforts. These institutes provide access to cutting-edge technology and equipment, as well training opportunities. These institutes can also be used to help manufacturers tackle cross-cutting problems in advanced manufacturing.
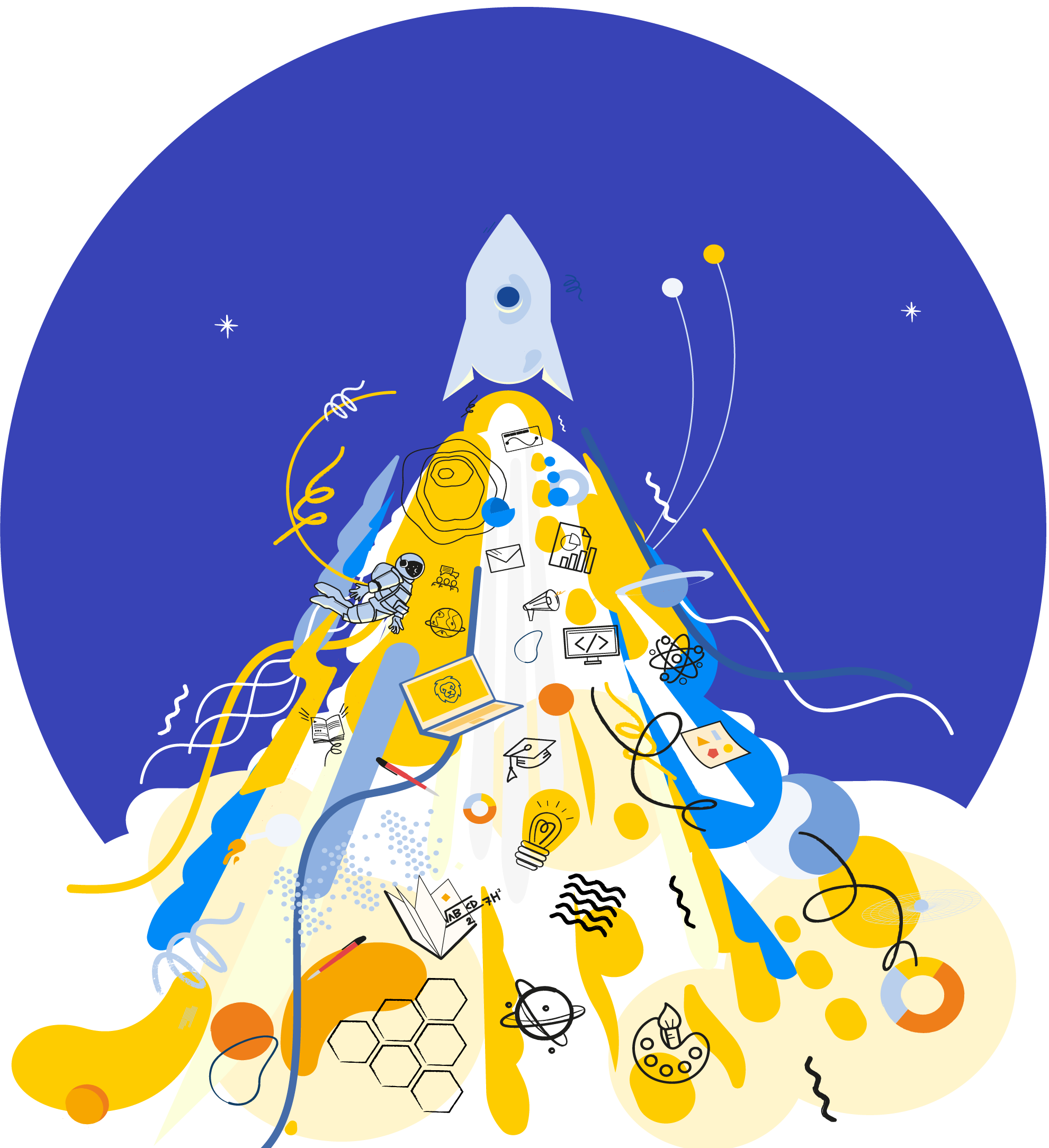
The Network for Manufacturing Innovation has a broad range of goals, including accelerating the commercialization of innovative manufacturing technologies, bridging the gap between laboratory research and market applications, and strengthening state and local economies. The U.S. Department of Energy will manage the institutes and funding will come from the U.S. Commerce Department's National Institute of Standards and Technology.
FAQ
What are the differences between these four types?
Manufacturing refers to the transformation of raw materials into useful products by using machines and processes. Manufacturing involves many activities, including designing, building, testing and packaging, shipping, selling, service, and so on.
What are the requirements to start a logistics business?
It takes a lot of skills and knowledge to run a successful logistics business. Effective communication skills are necessary to work with suppliers and clients. You will need to know how to interpret data and draw conclusions. You will need to be able handle pressure well and work in stressful situations. You must be creative and innovative to develop new ideas to improve efficiency. You need to have strong leadership qualities to motivate team members and direct them towards achieving organizational goals.
It is important to be organized and efficient in order to meet tight deadlines.
What are the 7 Rs of logistics.
The acronym "7R's" of Logistics stands for seven principles that underpin logistics management. It was developed by the International Association of Business Logisticians (IABL) and published in 2004 as part of its "Seven Principles of Logistics Management" series.
The following letters form the acronym:
-
Responsible - ensure that all actions taken are within legal requirements and are not harmful to others.
-
Reliable - Have confidence in your ability to fulfill all of your commitments.
-
Use resources effectively and sparingly.
-
Realistic - Take into consideration all aspects of operations including cost-effectiveness, environmental impact, and other factors.
-
Respectful – Treat others fairly and equitably.
-
Responsive - Look for ways to save time and increase productivity.
-
Recognizable - provide customers with value-added services.
Statistics
- In 2021, an estimated 12.1 million Americans work in the manufacturing sector.6 (investopedia.com)
- Job #1 is delivering the ordered product according to specifications: color, size, brand, and quantity. (netsuite.com)
- Many factories witnessed a 30% increase in output due to the shift to electric motors. (en.wikipedia.org)
- [54][55] These are the top 50 countries by the total value of manufacturing output in US dollars for its noted year according to World Bank.[56] (en.wikipedia.org)
- In the United States, for example, manufacturing makes up 15% of the economic output. (twi-global.com)
External Links
How To
How to Use Lean Manufacturing for the Production of Goods
Lean manufacturing is a management system that aims at increasing efficiency and reducing waste. It was created in Japan by Taiichi Ohno during the 1970s and 80s. He received the Toyota Production System award (TPS), from Kanji Toyoda, founder of TPS. Michael L. Watkins published the first book on lean manufacturing in 1990.
Lean manufacturing is often defined as a set of principles used to improve the quality, speed, and cost of products and services. It is about eliminating defects and waste from all stages of the value stream. Just-in-time (JIT), zero defect (TPM), and 5S are all examples of lean manufacturing. Lean manufacturing focuses on eliminating non-value-added activities such as rework, inspection, and waiting.
Lean manufacturing can help companies improve their product quality and reduce costs. Additionally, it helps them achieve their goals more quickly and reduces employee turnover. Lean manufacturing has been deemed one of the best ways to manage the entire value-chain, including customers, distributors as well retailers and employees. Lean manufacturing is widely used in many industries. Toyota's philosophy is the foundation of its success in automotives, electronics and appliances, healthcare, chemical engineers, aerospace, paper and food, among other industries.
Lean manufacturing is based on five principles:
-
Define Value: Identify the social value of your business and what sets you apart.
-
Reduce Waste - Eliminate any activity that doesn't add value along the supply chain.
-
Create Flow – Ensure that work flows smoothly throughout the process.
-
Standardize and simplify – Make processes as repeatable and consistent as possible.
-
Build Relationships- Develop personal relationships with both internal as well as external stakeholders.
Although lean manufacturing isn't a new concept in business, it has gained popularity due to renewed interest in the economy after the 2008 global financial crisis. Many companies have adopted lean manufacturing methods to increase their marketability. Some economists even believe that lean manufacturing can be a key factor in economic recovery.
Lean manufacturing is now becoming a common practice in the automotive industry, with many benefits. These include higher customer satisfaction levels, reduced inventory levels as well as lower operating costs.
Lean manufacturing can be applied to almost every aspect of an organization. However, it is particularly useful when applied to the production side of an organization because it ensures that all steps in the value chain are efficient and effective.
There are three main types of lean manufacturing:
-
Just-in-Time Manufacturing: Also known as "pull systems", this type of lean manufacturing uses just-in-time manufacturing (JIT). JIT means that components are assembled at the time of use and not manufactured in advance. This method reduces lead times, increases availability, and decreases inventory.
-
Zero Defects Manufacturing (ZDM): ZDM focuses on ensuring that no defective units leave the manufacturing facility. Repairing a part that is damaged during assembly should be done, not scrapping. This applies to finished goods that may require minor repairs before shipment.
-
Continuous Improvement (CI: Continuous improvement aims to increase the efficiency of operations by constantly identifying and making improvements to reduce or eliminate waste. Continuous Improvement involves continuous improvement of processes.