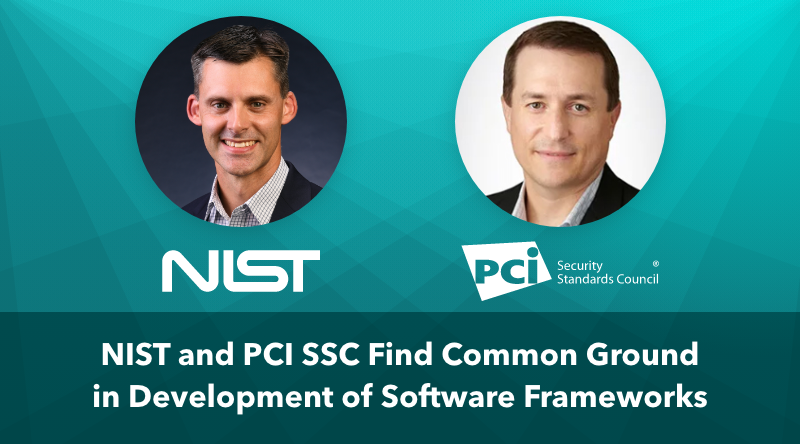
Regardless of what type of engineering career you are interested in, there are plenty of industrial engineering jobs in Dallas. You have many options, including computer and electronic manufacturers as well as transportation equipment manufacturers. Many plants require qualified industrial engineers in order to maintain smooth production.
Industrial engineers aid in process improvement by identifying opportunities for improvement and analyzing how these improvements have affected performance. Industrial engineers typically work in teams with other engineering professionals. To implement changes effectively, these professionals must have strong project management skills as well as math skills. Industrial engineers are also responsible for training and reporting. These engineers are often employed in corporations as well small- and mid-sized businesses.
Many industrial engineering professionals also work in client-facing and consulting roles. Some of these roles are in business analysis, data analysis, and software development. Industrial engineers can also be involved in projects that reduce production costs and increase efficiency. Industrial engineers are usually employed in manufacturing or transportation equipment-oriented industries. They are also employed in the aviation industry, as well as consumer goods industries. The Bureau of Labor Statistics (BLS) projects that the number of industrial engineering jobs will increase by 10% over the next decade.
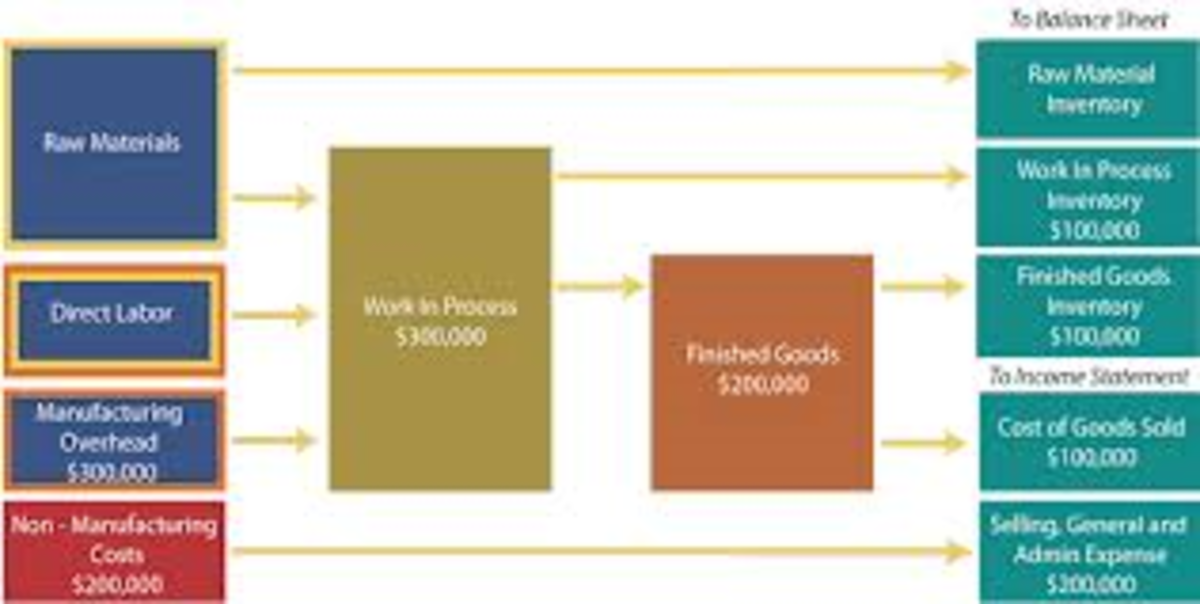
Industrial engineers are responsible for identifying wasteful practices within their production process. The engineer needs to collaborate with the right groups to identify potential improvement areas. They are also responsible to save time and energy. These engineers must possess strong math skills and a desire reduce waste to achieve their goal. A career as an industrial engineer can be a rewarding experience.
In Dallas and in neighboring cities, you can find jobs as an industrial engineer. Plano, McKinney and Frisco are some of these cities. Most of the industrial engineers who work in Dallas are employed in transportation equipment manufacturers. Other industries that are seeking qualified engineers include electronics and computer manufacturers as well as professional scientific and technical service.
Industrial engineers are often employed in a variety of roles, from a team leader to a manager. You can apply for a Monster profile if you're interested in a career in industrial engineering. You can create job alerts and customize your resume on this site. Expert advice is also available. You can start your search today for industrial engineering jobs in Dallas.
An internship is a great option if you are interested in pursuing a career as an industrial engineer. Most internships in industrial engineering require a commute of no more than 30 minutes. These internships can give you valuable experience in your industry and help you develop career skills. In addition to their engineering courses, industrial engineers may also choose to take business classes. There are many universities that offer business classes and parallel IE coursework.
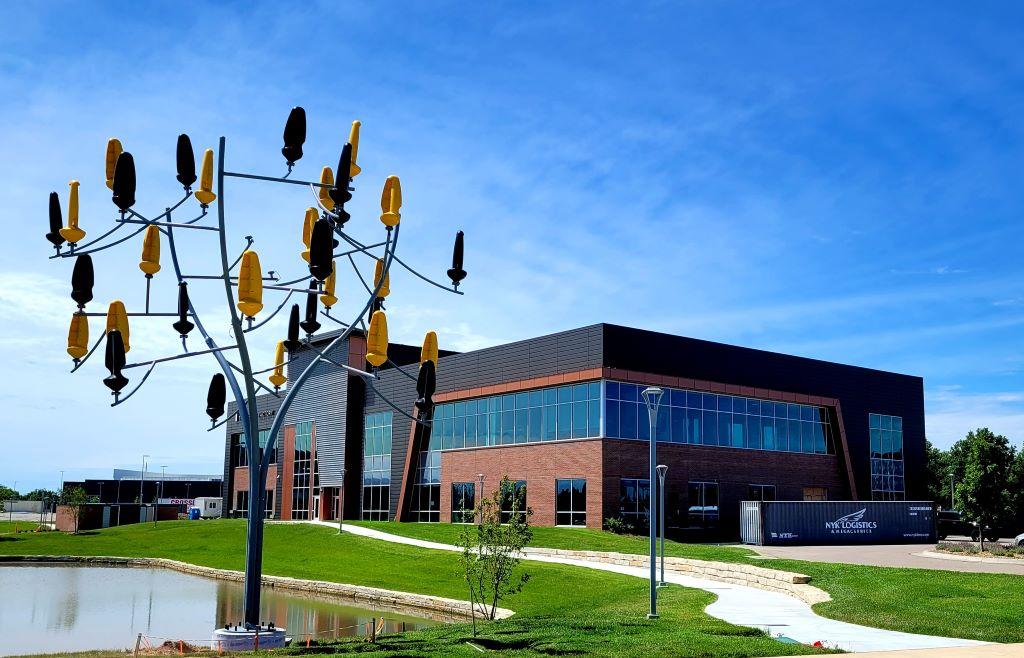
Industrial engineers will work closely with other engineers and analysts to improve company processes. You may also be asked to analyze labor management standards, track labor standards and maintain labor management system.
FAQ
Why is logistics important in manufacturing?
Logistics are an essential component of any business. Logistics can help you achieve amazing results by helping to manage product flow from raw materials to finished products.
Logistics play an important role in reducing costs as well as increasing efficiency.
Can certain manufacturing steps be automated?
Yes! Since ancient times, automation has been in existence. The Egyptians invent the wheel thousands of year ago. Robots are now used to assist us in assembly lines.
Actually, robotics can be used in manufacturing for many purposes. These include:
-
Robots for assembly line
-
Robot welding
-
Robot painting
-
Robotics inspection
-
Robots that create products
There are many other examples of how manufacturing could benefit from automation. For example, 3D printing allows us to make custom products without having to wait for weeks or months to get them manufactured.
What is the responsibility of a production planner?
Production planners ensure that all project aspects are completed on time, within budget and within the scope. A production planner ensures that the service and product meet the client's expectations.
What is the difference between Production Planning and Scheduling?
Production Planning (PP) is the process of determining what needs to be produced at any given point in time. This is done through forecasting demand and identifying production capacities.
Scheduling is the process of assigning specific dates to tasks so they can be completed within the specified timeframe.
What are the 7 R's of logistics?
The acronym 7Rs of Logistics refers to the seven core principles of logistics management. It was developed and published by the International Association of Business Logisticians in 2004 as part of the "Seven Principles of Logistics Management".
The following letters form the acronym:
-
Responsible - ensure that actions are in compliance with legal requirements and do not cause harm to others.
-
Reliable - You can have confidence that you will fulfill your promises.
-
Reasonable - use resources efficiently and don't waste them.
-
Realistic – consider all aspects of operations, from cost-effectiveness to environmental impact.
-
Respectful: Treat others with fairness and equity
-
Responsive - Look for ways to save time and increase productivity.
-
Recognizable - Provide value-added services to customers
Statistics
- You can multiply the result by 100 to get the total percent of monthly overhead. (investopedia.com)
- According to a Statista study, U.S. businesses spent $1.63 trillion on logistics in 2019, moving goods from origin to end user through various supply chain network segments. (netsuite.com)
- In the United States, for example, manufacturing makes up 15% of the economic output. (twi-global.com)
- Job #1 is delivering the ordered product according to specifications: color, size, brand, and quantity. (netsuite.com)
- It's estimated that 10.8% of the U.S. GDP in 2020 was contributed to manufacturing. (investopedia.com)
External Links
How To
How to Use Six Sigma in Manufacturing
Six Sigma is defined as "the application of statistical process control (SPC) techniques to achieve continuous improvement." Motorola's Quality Improvement Department, Tokyo, Japan, developed it in 1986. Six Sigma is a method to improve quality through standardization and elimination of defects. Since there are no perfect products, or services, this approach has been adopted by many companies over the years. Six Sigma's primary goal is to reduce variation from the average value of production. It is possible to measure the performance of your product against an average and find the percentage of time that it differs from the norm. If it is too large, it means that there are problems.
Understanding how variability works in your company is the first step to Six Sigma. Once you have this understanding, you will need to identify sources and causes of variation. You'll also want to determine whether these variations are random or systematic. Random variations are caused when people make mistakes. While systematic variations are caused outside of the process, they can occur. These are, for instance, random variations that occur when widgets are made and some fall off the production line. If however, you notice that each time you assemble a widget it falls apart in exactly the same spot, that is a problem.
After identifying the problem areas, you will need to devise solutions. You might need to change the way you work or completely redesign the process. You should then test the changes again after they have been implemented. If they didn't work, then you'll need to go back to the drawing board and come up with another plan.