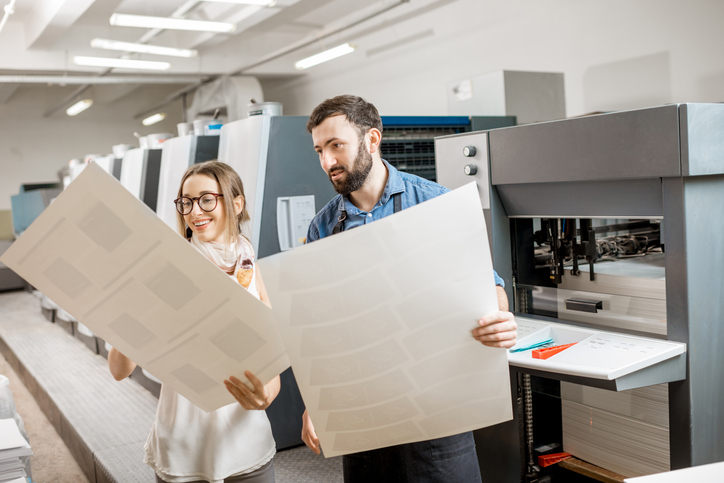
The director of manufacturing oversees the company's production process. This is a crucial role as they oversee the entire manufacturing process, from design to production. For this position to be successful, candidates must have experience in manufacturing and familiarity with new technologies. These technologies include 3D printing and robotics. It is a benefit to a director who stays current with the latest technologies. As the manufacturing industry evolves, the director's job will be more complex. He or she will have to coordinate with both the engineering and operations departments.
Salary for a director of manufacturing
The salary of a Director of Manufacturing can vary depending on where they are located. Many directors get a salary in the low six figures, but some earn more than others. The salary of a Director of Manufacturing may also vary significantly based on years of experience and education. Here are some factors that could impact your salary.
Although the salary for a Director of Manufacturing can vary depending on your experience, the average salary is higher. As with many positions, the cost of living and location may also affect salary. You will earn a higher salary if you live in a large city. However, your salary may not be sufficient to cover the cost of living. Always be willing to negotiate for a higher salary, if offered.
A Director of Manufacturing Operations can earn between $181 500 and $66,000 annually. The salary for a Director of Manufacturing Operations is highly variable and can vary by up to 8% between different cities. Fremont, CA's director for manufacturing operations can earn between $128.493 and $164.500. This is significantly more than the average national salary. The salary of a Director in Manufacturing Operations can vary depending on where you live, how experienced you are, and what company you work for.
Education necessary
The director manufacturing is responsible for overseeing and managing a factory. This job includes managing new employees, quality assurance, working with designers and meeting production standards. A director of manufacturing usually reports to the top management team. He or she executes sales and policy initiatives. Candidates must have some manufacturing experience and be able communicate well. There are different educational requirements to become a director in manufacturing.
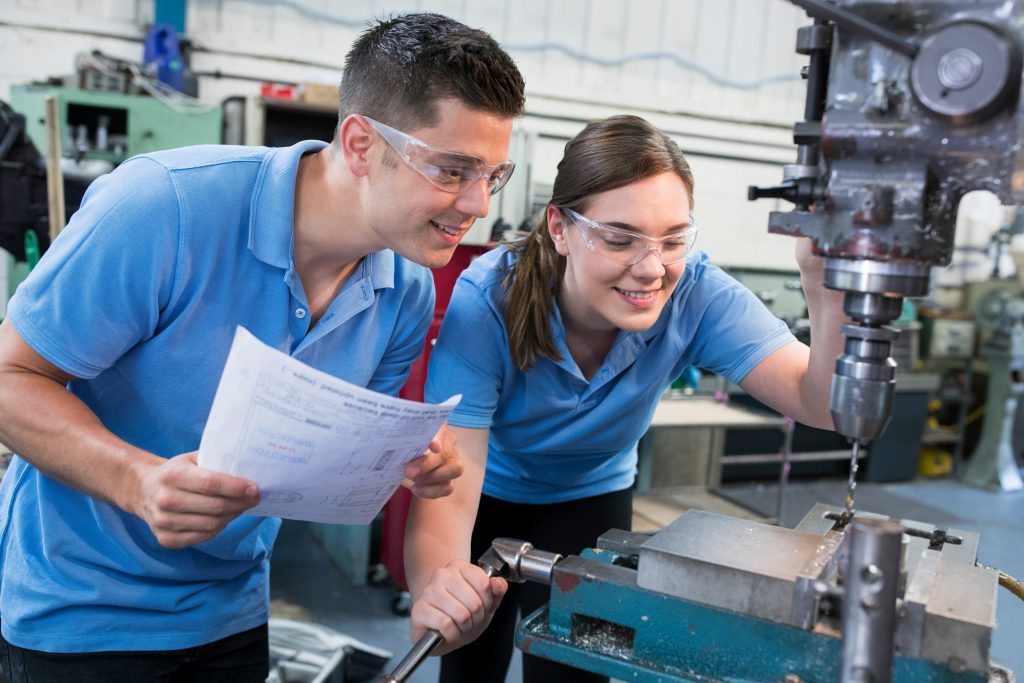
Although a master's degree in engineering does not necessarily make you a director in manufacturing, having a post-secondary education is a great way to increase your knowledge and skill set. A MBA program in business administration or industrial management is a great choice as it helps candidates learn about management, economics and organization. You will ultimately be responsible for managing diverse groups of people.
You will collaborate closely with engineers and designers as a director for manufacturing during the product development phase. This stage will see you actively evaluate the feasibility of new processes, and ensure quality standards before committing resources for larger productions. Successful directors are also responsible for overseeing the production process and acting as coaches for their employees. They will coach them in best practices and risk mitigation. They will also mentor them on best practices and risk mitigation.
Experience required
For this position, a bachelor's Degree in a relevant subject and 5-10 years of progressive experience are usually required. For this job, most manufacturing companies prefer to use their own employees. A candidate who is a good fit for this role will have an in-depth understanding of manufacturing processes and business goals. Employers may want to see a graduate level. These requirements may not be sufficient. Candidates may need to have additional training in their chosen industry or field.
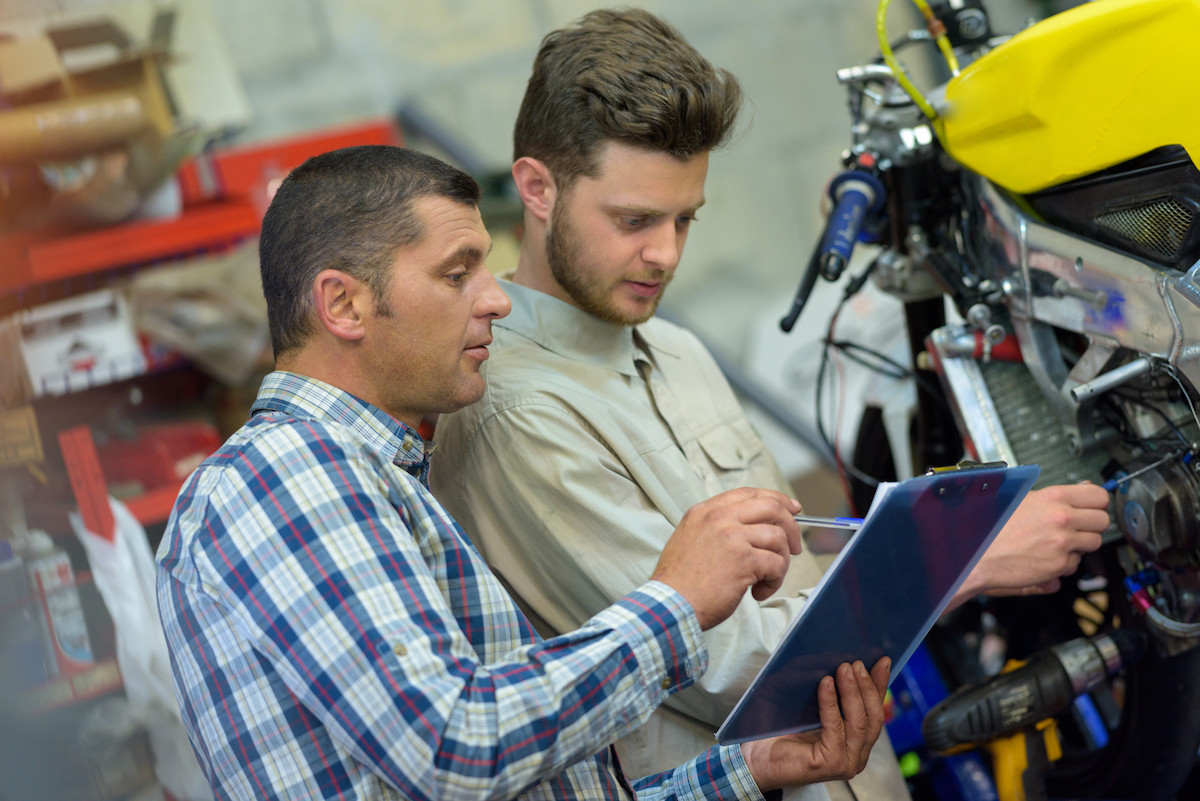
The manufacturing process is managed by the director of production, who oversees engineers, supervisors and workers. They could be responsible to solve problems and develop solutions. In addition to overseeing production, they may also be responsible for developing and implementing quality-control programs. Directly reports to the top management of the manufacturing organization, the director of manufacturing. Experience in manufacturing is essential. This position can be made more successful if you have experience in manufacturing management.
Experience as a manufacturing director will be an asset. Directors should have at least 10 years' experience in a manufacturing setting. These people might have been employed as technicians or supervisors in manufacturing. They should also possess strong communication skills. The director of production should also have an in-depth understanding of the business strategy. A director of Manufacturing must also be able to communicate effectively with other departments. In this capacity, the director oversees the production process and ensures that it meets the highest quality standards.
FAQ
What's the difference between Production Planning & Scheduling?
Production Planning (PP), also known as forecasting and identifying production capacities, is the process that determines what product needs to be produced at any particular time. This is done through forecasting demand and identifying production capacities.
Scheduling is the process of assigning specific dates to tasks so they can be completed within the specified timeframe.
How can overproduction in manufacturing be reduced?
The key to reducing overproduction lies in developing better ways to manage inventory. This would reduce the time spent on unproductive activities like purchasing, storing and maintaining excess stock. This will allow us to free up resources for more productive tasks.
This can be done by using a Kanban system. A Kanban board, a visual display to show the progress of work, is called a Kanban board. Kanban systems are where work items travel through a series of states until reaching their final destination. Each state represents a different priority.
For instance, when work moves from one stage to another, the current task is complete enough to be moved to the next stage. However, if a task is still at the beginning stages, it will remain so until it reaches the end of the process.
This keeps work moving and ensures no work is lost. Managers can monitor the work being done by Kanban boards to see what is happening at any given time. This data allows them adjust their workflow based upon real-time data.
Lean manufacturing is another option to control inventory levels. Lean manufacturing focuses on eliminating waste throughout the entire production chain. Anything that doesn't add value to the product is considered waste. The following are examples of common waste types:
-
Overproduction
-
Inventory
-
Unnecessary packaging
-
Materials in excess
Manufacturers can reduce their costs and improve their efficiency by using these ideas.
How can manufacturing avoid production bottlenecks
To avoid production bottlenecks, ensure that all processes run smoothly from the moment you receive your order to the time the product ships.
This includes planning for both capacity requirements and quality control measures.
Continuous improvement techniques such Six Sigma are the best method to accomplish this.
Six Sigma Management System is a method to increase quality and reduce waste throughout your organization.
It focuses on eliminating variation and creating consistency in your work.
What skills is required for a production planner?
Being a production planner is not easy. You need to be organized and flexible. Communication skills are essential to ensure that you can communicate effectively with clients, colleagues, and customers.
What are the four types of manufacturing?
Manufacturing refers the process of turning raw materials into useful products with machines and processes. Manufacturing involves many activities, including designing, building, testing and packaging, shipping, selling, service, and so on.
Statistics
- In the United States, for example, manufacturing makes up 15% of the economic output. (twi-global.com)
- [54][55] These are the top 50 countries by the total value of manufacturing output in US dollars for its noted year according to World Bank.[56] (en.wikipedia.org)
- In 2021, an estimated 12.1 million Americans work in the manufacturing sector.6 (investopedia.com)
- You can multiply the result by 100 to get the total percent of monthly overhead. (investopedia.com)
- Many factories witnessed a 30% increase in output due to the shift to electric motors. (en.wikipedia.org)
External Links
How To
How to Use Just-In-Time Production
Just-intime (JIT), a method used to lower costs and improve efficiency in business processes, is called just-in-time. It's the process of obtaining the right amount and timing of resources when you need them. This means you only pay what you use. Frederick Taylor first coined this term while working in the early 1900s as a foreman. Taylor observed that overtime was paid to workers if they were late in working. He decided that workers would be more productive if they had enough time to complete their work before they started to work.
JIT is about planning ahead. You should have all the necessary resources ready to go so that you don’t waste money. It is important to look at your entire project from beginning to end and ensure that you have enough resources to handle any issues that may arise. You will have the resources and people to solve any problems you anticipate. This will prevent you from spending extra money on unnecessary things.
There are several types of JIT techniques:
-
Demand-driven: This type of JIT allows you to order the parts/materials required for your project on a regular basis. This will allow to track how much material has been used up. It will also allow you to predict how long it takes to produce more.
-
Inventory-based: This is a type where you stock the materials required for your projects in advance. This allows one to predict how much they will sell.
-
Project-driven: This means that you have enough money to pay for your project. When you know how much you need, you'll purchase the appropriate amount of materials.
-
Resource-based JIT: This type of JIT is most commonly used. Here you can allocate certain resources based purely on demand. If you have many orders, you will assign more people to manage them. If there aren't many orders, you will assign fewer people.
-
Cost-based: This is the same as resource-based except that you don't care how many people there are but how much each one of them costs.
-
Price-based: This is similar to cost-based but instead of looking at individual workers' salaries, you look at the total company price.
-
Material-based: This approach is similar to cost-based. However, instead of looking at the total cost for the company, you look at how much you spend on average on raw materials.
-
Time-based: This is another variation of resource-based JIT. Instead of focusing solely on the amount each employee costs, focus on how long it takes for the project to be completed.
-
Quality-based JIT - This is another form of resource-based JIT. Instead of thinking about the cost of each employee or the time it takes to produce something, you focus on how good your product quality.
-
Value-based JIT : This is the newest type of JIT. This is where you don't care about how the products perform or whether they meet customers' expectations. Instead, you're focused on how much value you add to the market.
-
Stock-based: This stock-based method focuses on the actual quantity of products being made at any given time. It is used when production goals are met while inventory is kept to a minimum.
-
Just-in-time (JIT) planning: This is a combination of JIT and supply chain management. It is the process of scheduling components' delivery as soon as they have been ordered. It reduces lead times and improves throughput.