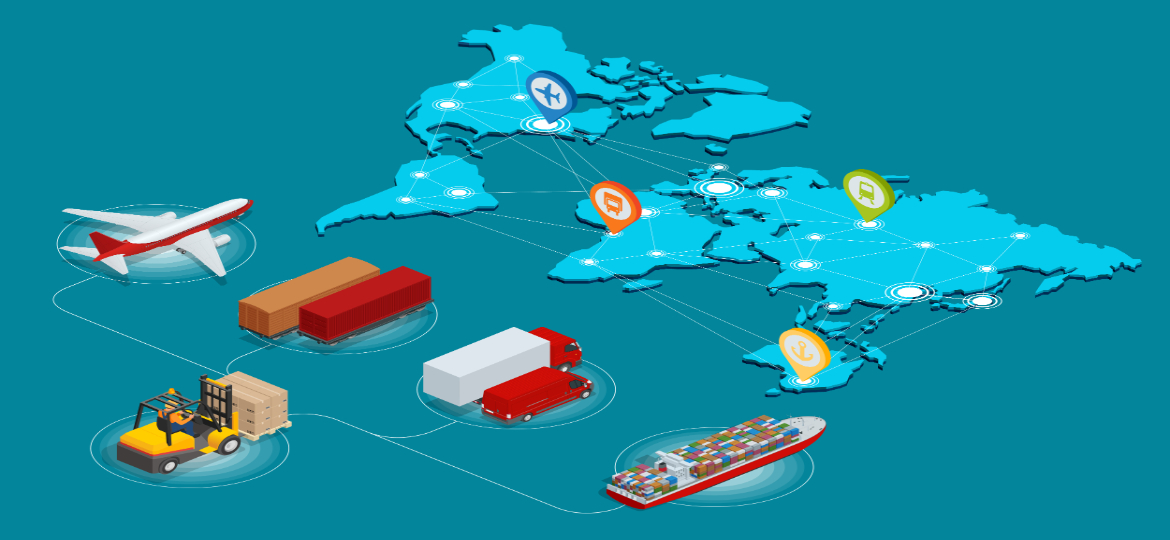
Using lean product development methodologies, companies can ensure that products are developed in a way that is best suited to their needs. Lean products can reduce waste and speed up product design. Lean principles allow companies to stay competitive.
Lean product creation is an approach that blends engineering and manufacturing. Its purpose is build a functioning product with less stock, effort and time. It uses visual planning techniques like visual boards and rapid learning cycles. It integrates set-based concur engineering.
Lean product development starts with understanding the customer. This is done through a process of identifying the key risks in the business case and determining the consumer's interaction with the product. It is important to understand the scope of the product, which includes functions and features. If the customer doesn’t require them, these features can be unnecessary and extraneous. It also involves the creation of a verification-validation plan.
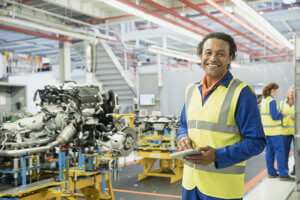
The next step is to create an activity network. This allows teams the freedom to decide what they do and how they plan it. The network provides a framework for the development of value. It reduces waste and helps teams find opportunities to improve their processes.
The ideal PD process focuses on a continuous flow of value from conception to production. It should not include bureaucratic stops and loop backs to correct any errors. It should also be representative of the value stream system. The system should not become unstable and lead to vision loss. The process should work in a single-piece fashion, similar to manufacturing.
First, you need to establish the value. This is done through an analysis of the business case and a systematic literature review. It is crucial to establish the value expectations for all stakeholders. It is important to define the product scope. This includes customer value as well as the features and functions. These are the elements that determine the technology and process used.
The next step in the process is to design the value flow. This is accomplished by eliminating the steps that don’t add value. Unused designs and unverified codes should be eliminated. Also, it is important to limit the number of tasks being done at once. This is usually accomplished by frequently changing priorities.
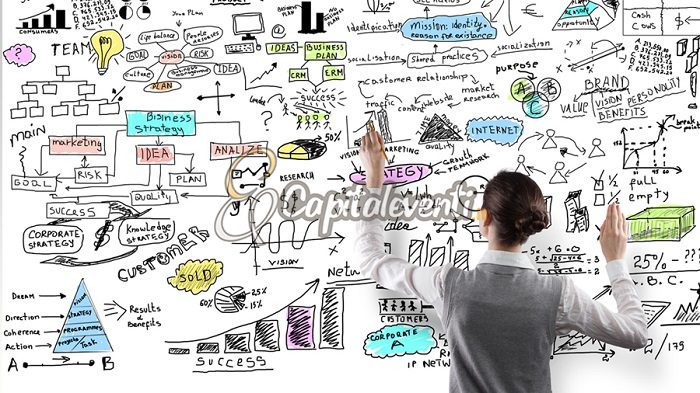
Lean product development can be a valuable tool for businesses that helps them reduce costs, identify inefficiencies and stay competitive. It also allows companies to build sustainable value streams, which will help them to become profitable in the future. It has helped businesses from all industries including healthcare, high tech, and manufacturing.
Lean product engineering uses a set based concurrent engineering approach which allows teams and individuals to develop products with fewer resources. In the past, big companies took longer to develop new products than start-ups, primarily due to the complex codebases they used. This can be difficult to maintain and build upon.
FAQ
Why automate your warehouse?
Modern warehousing is becoming more automated. E-commerce has increased the demand for quicker delivery times and more efficient processes.
Warehouses have to be flexible to meet changing requirements. To do so, they must invest heavily in technology. Automating warehouses has many benefits. Here are some reasons why it's worth investing in automation:
-
Increases throughput/productivity
-
Reduces errors
-
Improves accuracy
-
Safety is boosted
-
Eliminates bottlenecks
-
This allows companies to scale easily
-
Workers are more productive
-
It gives visibility to everything that happens inside the warehouse
-
Enhances customer experience
-
Improves employee satisfaction
-
Reduces downtime and improves uptime
-
High quality products delivered on-time
-
Removes human error
-
It helps ensure compliance with regulations
How can excess manufacturing production be reduced?
The key to reducing overproduction lies in developing better ways to manage inventory. This would reduce the amount of time spent on unnecessary activities such as purchasing, storing, and maintaining excess stock. This will allow us to free up resources for more productive tasks.
This can be done by using a Kanban system. A Kanban Board is a visual display that tracks work progress. Kanban systems allow work items to move through different states until they reach their final destination. Each state is assigned a different priority.
To illustrate, work can move from one stage or another when it is complete enough for it to be moved to a new stage. However, if a task is still at the beginning stages, it will remain so until it reaches the end of the process.
This helps to keep work moving forward while ensuring that no work is left behind. Managers can monitor the work being done by Kanban boards to see what is happening at any given time. This data allows them adjust their workflow based upon real-time data.
Lean manufacturing is another way to manage inventory levels. Lean manufacturing seeks to eliminate waste from every step of the production cycle. Anything that doesn't add value to the product is considered waste. Some common types of waste include:
-
Overproduction
-
Inventory
-
Unnecessary packaging
-
Material surplus
By implementing these ideas, manufacturers can improve efficiency and cut costs.
What skills should a production planner have?
To become a successful production planner, you need to be organized, flexible, and able to multitask. Communication skills are essential to ensure that you can communicate effectively with clients, colleagues, and customers.
What are the logistics products?
Logistics involves the transportation of goods from point A and point B.
They encompass all aspects transport, including packaging and loading, transporting, storage, unloading.
Logisticians ensure that the product is delivered to the correct place, at the right time, and under safe conditions. Logisticians assist companies in managing their supply chains by providing information such as demand forecasts, stock levels and production schedules.
They can also track shipments in transit and monitor quality standards.
How can efficiency in manufacturing be improved?
First, identify the factors that affect production time. We must then find ways that we can improve these factors. If you don't know where to start, then think about which factor(s) have the biggest impact on production time. Once you have identified the factors, then try to find solutions.
What type of jobs is there in logistics
There are many jobs available in logistics. Here are some examples:
-
Warehouse workers – They load, unload and transport pallets and trucks.
-
Transportation drivers - They drive trucks and trailers to deliver goods and carry out pick-ups.
-
Freight handlers: They sort and package freight in warehouses.
-
Inventory managers - They oversee the inventory of goods in warehouses.
-
Sales reps - They sell products and services to customers.
-
Logistics coordinators - They plan and organize logistics operations.
-
Purchasing agents – They buy goods or services necessary to run a company.
-
Customer service representatives – They answer emails and phone calls from customers.
-
Shipping clerks – They process shipping orders, and issue bills.
-
Order fillers – They fill orders based upon what was ordered and shipped.
-
Quality control inspectors (QCI) - They inspect all incoming and departing products for potential defects.
-
Others - There is a variety of other jobs in logistics. These include transportation supervisors and cargo specialists.
Statistics
- Many factories witnessed a 30% increase in output due to the shift to electric motors. (en.wikipedia.org)
- According to the United Nations Industrial Development Organization (UNIDO), China is the top manufacturer worldwide by 2019 output, producing 28.7% of the total global manufacturing output, followed by the United States, Japan, Germany, and India.[52][53] (en.wikipedia.org)
- Job #1 is delivering the ordered product according to specifications: color, size, brand, and quantity. (netsuite.com)
- It's estimated that 10.8% of the U.S. GDP in 2020 was contributed to manufacturing. (investopedia.com)
- [54][55] These are the top 50 countries by the total value of manufacturing output in US dollars for its noted year according to World Bank.[56] (en.wikipedia.org)
External Links
How To
How to use the Just In-Time Production Method
Just-in time (JIT), is a process that reduces costs and increases efficiency in business operations. It is a process where you get the right amount of resources at the right moment when they are needed. This means you only pay what you use. The term was first coined by Frederick Taylor, who developed his theory while working as a foreman in the early 1900s. He noticed that workers were often paid overtime when they had to work late. He realized that workers should have enough time to complete their jobs before they begin work. This would help increase productivity.
The idea behind JIT is that you should plan ahead and have everything ready so you don't waste money. Look at your entire project, from start to end. Make sure you have enough resources in place to deal with any unexpected problems. You will have the resources and people to solve any problems you anticipate. This will ensure that you don't spend more money on things that aren't necessary.
There are many JIT methods.
-
Demand-driven JIT: This is a JIT that allows you to regularly order the parts/materials necessary for your project. This will enable you to keep track of how much material is left after you use it. You'll also be able to estimate how long it will take to produce more.
-
Inventory-based: This allows you to store the materials necessary for your projects in advance. This allows for you to anticipate how much you can sell.
-
Project-driven: This method allows you to set aside enough funds for your project. Once you have an idea of how much material you will need, you can purchase the necessary materials.
-
Resource-based: This is the most common form of JIT. Here, you allocate certain resources based on demand. For instance, if you have a lot of orders coming in, you'll assign more people to handle them. If there aren't many orders, you will assign fewer people.
-
Cost-based : This is similar in concept to resource-based. But here, you aren't concerned about how many people your company has but how much each individual costs.
-
Price-based: This approach is very similar to the cost-based method except that you don't look at individual workers costs but the total cost of the company.
-
Material-based: This approach is similar to cost-based. However, instead of looking at the total cost for the company, you look at how much you spend on average on raw materials.
-
Time-based JIT: This is another variant of resource-based JIT. Instead of focusing only on how much each employee is costing, you should focus on how long it takes to complete your project.
-
Quality-based JIT - This is another form of resource-based JIT. Instead of thinking about how much each employee costs or how long it takes to manufacture something, you think about how good the quality of your product is.
-
Value-based JIT: This is the latest form of JIT. You don't worry about whether the products work or if they meet customer expectations. Instead, you focus on the added value that you provide to your market.
-
Stock-based: This is an inventory-based method that focuses on the actual number of items being produced at any given time. This method is useful when you want to increase production while decreasing inventory.
-
Just-intime (JIT), planning is a combination JIT management and supply chain management. It is the process that schedules the delivery of components within a short time of their order. This is important as it reduces lead time and increases throughput.