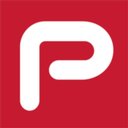
To become a drafter, one must have technical knowledge and the ability to translate design ideas into technical drawings. They should also be able to work in teams to produce the best results. They may need to learn how engineering plans are read and how to use certain software programs. They might also need to know engineering formulas for calculating measurements.
Drafters are typically employed by engineering and architectural firms. These professionals create plans for buildings and structures using computer-aided designing (CAD) software. Although they may work independently, many of these professionals work in teams to create unique designs. Although they are often full-time workers, they can also take on other jobs. They may need to work overtime depending upon the company they work for.
Most drafters obtain an associate's degree from a technical or community college in drafting. They can then continue their education with a 4-year program at a university. It is possible to transfer their degree, depending on the course taken.
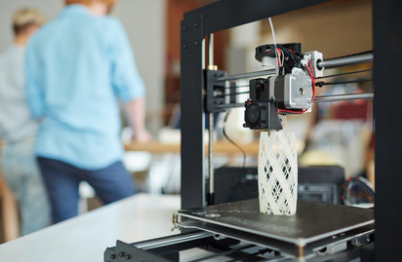
Drafters will need to have professional experience in addition to a degree in drafting. To gain practical experience, drafters may be required to intern with a company. This can be a great way to land a job as a drafter. You may also be asked for a portfolio to showcase your drafting skills.
Also, drafters can earn certifications. American Design Drafting Association, (ADDA), offers certification tests that test drafting knowledge. These exams test the ability to understand and use geometric designs. Many certifications are valid up to three years. To renew, candidates must take updated exams. The ADDA offers certification in many drafting specialties.
Most drafters work in engineering, construction, or manufacturing. They may also work in factories, or with electrics. They might also have a set work schedule. However, some drafters work 40+ hours per week. They must be able to manage time and know how to use computer assisted drafting (CAD).
Drafters can profit from the growing use of technology in order to increase their efficiency. They may need to understand CAD and other software programs, and stay current on building codes to remain competitive. Those who are interested in becoming a drafter may want to consider earning a master's degree. When it comes down to getting hired, people with master's degrees will be able to stand out from the rest. They are also better equipped to communicate technical information to clients.
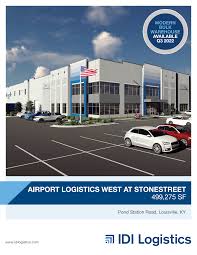
Assisting professional drafters is another option for drafters. For experience, they may also volunteer to assist with community projects. Before enrolling in classes, determine what type project you are interested to do as a drafter. Some clients prefer pencil sketches while others prefer computer-generated designs.
Draft technicians can gain work experience after they graduate from highschool. They should pay particular attention to math and computer classes.
FAQ
Why is logistics important in manufacturing
Logistics are essential to any business. Logistics can help you achieve amazing results by helping to manage product flow from raw materials to finished products.
Logistics play a key role in reducing expenses and increasing efficiency.
Are there ways to automate parts of manufacturing?
Yes! Yes. The Egyptians invent the wheel thousands of year ago. Today, robots assist in the assembly of lines.
There are many applications for robotics in manufacturing today. These include:
-
Robots for assembly line
-
Robot welding
-
Robot painting
-
Robotics inspection
-
Robots that make products
Manufacturing could also benefit from automation in other ways. For instance, 3D printing allows us make custom products and not have to wait for months or even weeks to get them made.
What does "warehouse" mean?
A warehouse is an area where goods are stored before being sold. You can have it indoors or outdoors. It could be one or both.
Statistics
- In the United States, for example, manufacturing makes up 15% of the economic output. (twi-global.com)
- (2:04) MTO is a production technique wherein products are customized according to customer specifications, and production only starts after an order is received. (oracle.com)
- You can multiply the result by 100 to get the total percent of monthly overhead. (investopedia.com)
- Job #1 is delivering the ordered product according to specifications: color, size, brand, and quantity. (netsuite.com)
- Many factories witnessed a 30% increase in output due to the shift to electric motors. (en.wikipedia.org)
External Links
How To
How to Use Just-In-Time Production
Just-in-time is a way to cut costs and increase efficiency in business processes. This is where you have the right resources at the right time. This means that only what you use is charged to your account. Frederick Taylor was the first to coin this term. He developed it while working as a foreman during the early 1900s. He noticed that workers were often paid overtime when they had to work late. He decided that workers would be more productive if they had enough time to complete their work before they started to work.
JIT is an acronym that means you need to plan ahead so you don’t waste your money. Also, you should look at the whole project from start-to-finish and make sure you have the resources necessary to address any issues. If you anticipate that there might be problems, you'll have enough people and equipment to fix them. You won't have to pay more for unnecessary items.
There are several types of JIT techniques:
-
Demand-driven JIT: This is a JIT that allows you to regularly order the parts/materials necessary for your project. This will let you track the amount of material left over after you've used it. This will allow you to calculate how long it will take to make more.
-
Inventory-based: This type allows you to stock the materials needed for your projects ahead of time. This allows you to predict how much you can expect to sell.
-
Project-driven: This means that you have enough money to pay for your project. Knowing how much money you have available will help you purchase the correct amount of materials.
-
Resource-based JIT: This is the most popular form of JIT. Here you can allocate certain resources based purely on demand. You will, for example, assign more staff to deal with large orders. If you don’t have many orders you will assign less people to the work.
-
Cost-based: This is the same as resource-based except that you don't care how many people there are but how much each one of them costs.
-
Price-based: This is similar to cost-based but instead of looking at individual workers' salaries, you look at the total company price.
-
Material-based: This is very similar to cost-based but instead of looking at total costs of the company you are concerned with how many raw materials you use on an average.
-
Time-based: This is another variation of resource-based JIT. Instead of worrying about how much each worker costs, you can focus on how long the project takes.
-
Quality-based JIT: Another variation on resource-based JIT. Instead of thinking about how much each employee costs or how long it takes to manufacture something, you think about how good the quality of your product is.
-
Value-based JIT is the newest form of JIT. You don't worry about whether the products work or if they meet customer expectations. Instead, your focus is on the value you bring to the market.
-
Stock-based: This stock-based method focuses on the actual quantity of products being made at any given time. This is used to increase production and minimize inventory.
-
Just-in time (JIT), planning: This is a combination JIT/supply chain management. It is the process that schedules the delivery of components within a short time of their order. It's important because it reduces lead times and increases throughput.