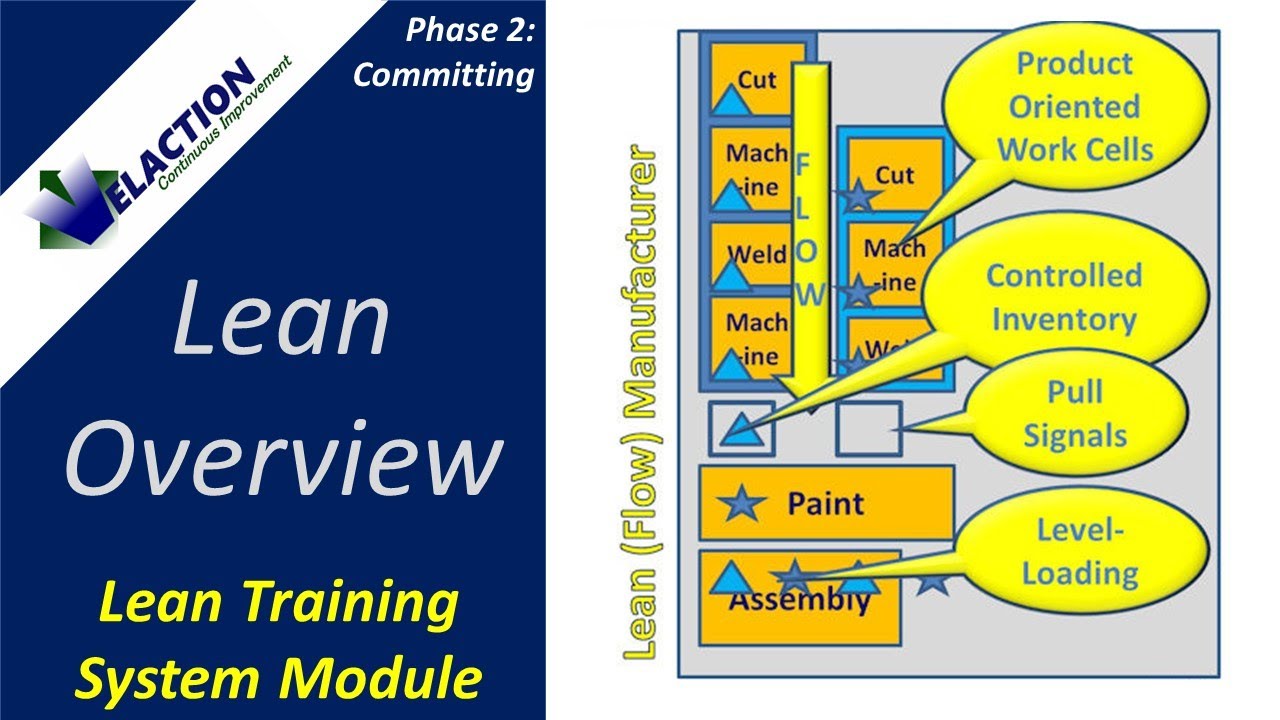
SIPOC diagram is a useful visual tool that helps to define the inputs and outputs of a business process. The SIPOC diagram allows team members identify any gaps or improvements to business operations.
The sipoc chart is frequently used in conjunction with the DMAIC (Dynamic Management and Improvement Cycle), which is a process improvement framework designed to help create business processes that can be continuously improved through analysis. It can also help teams and sponsors reach agreement on project boundaries, scope, and Key Process Input Variables.
What Is SIPOC?
The SIPOC diagram is a simple and easy-to-follow visual representation of the inputs and outputs of a specific business process. Its main purpose is to provide a visual representation of the inputs and outputs for a business process.
What is the background of the sipoc diagrams?
The sipoc diagram dates back to the 1980s as part of a total quality management approach (TQM), and the Six Sigma model for business process improvement. Since then, its use in lean manufacturing programs and business process improvements has expanded. It is a valuable tool for streamlining and identifying processes and potential improvements.
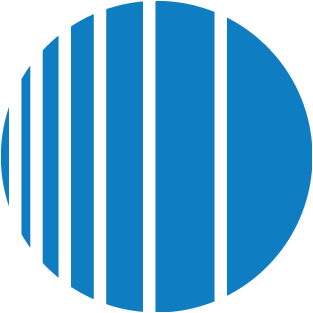
How to Make SIPOCs
The first step to creating a SIPOC is to select the business processes you wish to analyse. This will help your team and you focus on the important areas.
You will then need to identify what inputs you require to make your process run and who is providing them. List the contact information of each supplier along with their raw materials.
You can also list both internal clients and external clients that will be receiving the outputs. This will help you to make sure that your company provides high-quality services and products.
Inputs - This is the top section of a SIPOC Diagram and contains the information or materials specifications that are needed by the process. Material can either be physical goods such as products or information such as reports.
Outputs - This is the next section of the SIPOC diagram. It's usually a listing of the products, completed actions, or services that result from the process. The outputs need to reflect the value the customer expects from the process and meet their needs.
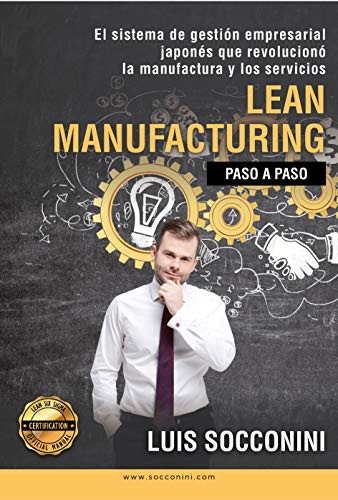
Customers: This section is the last of a SIPOC Diagram and it identifies all the clients who will receive the outputs from the process, internal or external to the organisation. This can include the maintenance team, line operators, and other internal and external clients.
SIPOCs are powerful visual tools that can be used for improving business processes and communication among all stakeholders. Easy to create, it's a great tool to help your team understand the processes you are examining. Use a template which includes the main components of the diagram such as inputs, outputs. You can save both time and energy by using a template.
FAQ
What is the difference between Production Planning, Scheduling and Production Planning?
Production Planning (PP), also known as forecasting and identifying production capacities, is the process that determines what product needs to be produced at any particular time. This is accomplished by forecasting the demand and identifying production resources.
Scheduling refers to the process of allocating specific dates to tasks in order that they can be completed within a specified timeframe.
What are the 7 Rs of logistics management?
The acronym 7Rs of Logistics refers to the seven core principles of logistics management. It was developed and published by the International Association of Business Logisticians in 2004 as part of the "Seven Principles of Logistics Management".
The following letters make up the acronym:
-
Responsible - ensure that actions are in compliance with legal requirements and do not cause harm to others.
-
Reliable - Have confidence in your ability to fulfill all of your commitments.
-
Be responsible - Use resources efficiently and avoid wasting them.
-
Realistic – Consider all aspects, including cost-effectiveness as well as environmental impact.
-
Respectful: Treat others with fairness and equity
-
Be resourceful: Look for opportunities to save money or increase productivity.
-
Recognizable provides value-added products and services to customers
What types of jobs can you find in logistics
There are many kinds of jobs available within logistics. Here are some examples:
-
Warehouse workers: They load and unload trucks, pallets, and other cargo.
-
Transportation drivers – They drive trucks or trailers to transport goods and perform pick-ups.
-
Freight handlers are people who sort and pack freight into warehouses.
-
Inventory managers: They are responsible for the inventory and management of warehouses.
-
Sales reps are people who sell products to customers.
-
Logistics coordinators - They plan and organize logistics operations.
-
Purchasing agents are those who purchase goods and services for the company.
-
Customer service representatives are available to answer customer calls and emails.
-
Shipping clerks – They process shipping orders, and issue bills.
-
Order fillers - They fill orders based on what is ordered and shipped.
-
Quality control inspectors: They inspect outgoing and incoming products for any defects.
-
Others – There are many other types available in logistics. They include transport supervisors, cargo specialists and others.
What do we need to know about Manufacturing Processes in order to learn more about Logistics?
No. No. But, being familiar with manufacturing processes will give you a better understanding about how logistics works.
What are the responsibilities of a production planner
Production planners ensure that all project aspects are completed on time, within budget and within the scope. They ensure that the product or service is of high quality and meets client requirements.
What are the responsibilities of a logistic manager?
Logistics managers ensure that goods arrive on time and are unharmed. This is done through his/her expertise and knowledge about the company's product range. He/she also needs to ensure adequate stock to meet demand.
What are manufacturing and logistics?
Manufacturing is the production of goods using raw materials. Logistics is the management of all aspects of supply chain activities, including procurement, production planning, distribution, warehousing, inventory control, transportation, and customer service. As a broad term, manufacturing and logistics often refer to both the creation and delivery of products.
Statistics
- You can multiply the result by 100 to get the total percent of monthly overhead. (investopedia.com)
- (2:04) MTO is a production technique wherein products are customized according to customer specifications, and production only starts after an order is received. (oracle.com)
- In 2021, an estimated 12.1 million Americans work in the manufacturing sector.6 (investopedia.com)
- [54][55] These are the top 50 countries by the total value of manufacturing output in US dollars for its noted year according to World Bank.[56] (en.wikipedia.org)
- Many factories witnessed a 30% increase in output due to the shift to electric motors. (en.wikipedia.org)
External Links
How To
How to use the Just-In Time Method in Production
Just-in-time (JIT) is a method that is used to reduce costs and maximize efficiency in business processes. It allows you to get the right amount resources at the right time. This means you only pay what you use. Frederick Taylor developed the concept while working as foreman in early 1900s. He saw how overtime was paid to workers for work that was delayed. He concluded that if workers were given enough time before they start work, productivity would increase.
The idea behind JIT is that you should plan ahead and have everything ready so you don't waste money. Look at your entire project, from start to end. Make sure you have enough resources in place to deal with any unexpected problems. If you expect problems to arise, you will be able to provide the necessary equipment and personnel to address them. This way, you won't end up paying extra money for things that weren't really necessary.
There are several types of JIT techniques:
-
Demand-driven: This is a type of JIT where you order the parts/materials needed for your project regularly. This will allow you to track how much material you have left over after using it. You'll also be able to estimate how long it will take to produce more.
-
Inventory-based: This type allows you to stock the materials needed for your projects ahead of time. This allows one to predict how much they will sell.
-
Project-driven: This method allows you to set aside enough funds for your project. If you know the amount you require, you can buy the materials you need.
-
Resource-based JIT: This is the most popular form of JIT. This is where you assign resources based upon demand. You might assign more people to help with orders if there are many. If you don’t have many orders you will assign less people to the work.
-
Cost-based: This is a similar approach to resource-based but you are not only concerned with how many people you have, but also how much each one costs.
-
Price-based: This is a variant of cost-based. However, instead of focusing on the individual workers' costs, this looks at the total price of the company.
-
Material-based: This approach is similar to cost-based. However, instead of looking at the total cost for the company, you look at how much you spend on average on raw materials.
-
Time-based JIT: This is another variant of resource-based JIT. Instead of focusing on the cost of each employee, you will focus on the time it takes to complete a project.
-
Quality-based JIT is another variant of resource-based JIT. Instead of thinking about the cost of each employee or the time it takes to produce something, you focus on how good your product quality.
-
Value-based JIT: One of the most recent forms of JIT. In this case, you're not concerned with how well the products perform or whether they meet customer expectations. Instead, you are focused on adding value to the marketplace.
-
Stock-based: This stock-based method focuses on the actual quantity of products being made at any given time. It's used when you want to maximize production while minimizing inventory.
-
Just-in time (JIT), planning: This is a combination JIT/supply chain management. It's the process of scheduling delivery of components immediately after they are ordered. This is important as it reduces lead time and increases throughput.