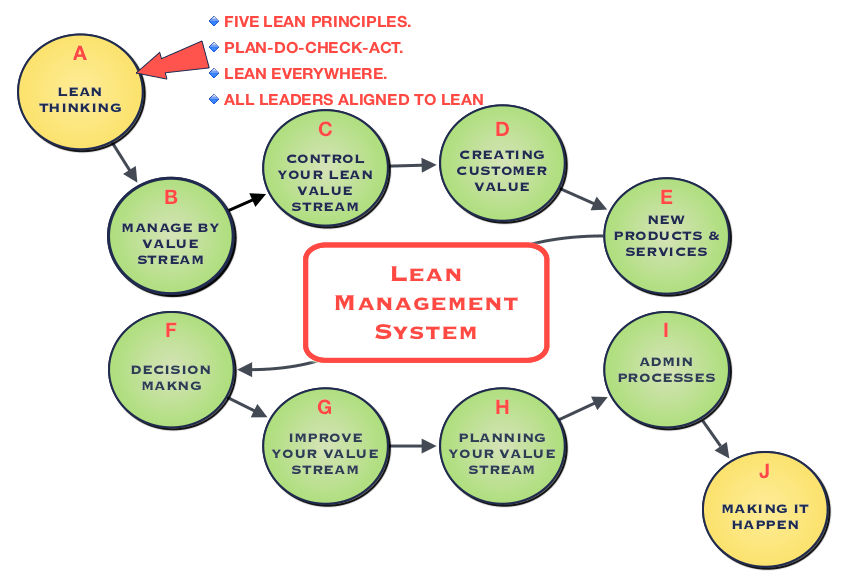
Lean system management is a method of reducing waste in the workplace. It is based on the belief that every activity or process in a company should add value to the product or service it provides for customers. This can be achieved by eliminating any activities that do not add value and working systematically to create more value.
A lean system of management is intended to improve the overall performance and efficiency of a company. It also helps ensure employees understand the purpose and goal of their work.
The first step of lean system-management is to define what value is. It involves identifying the value that a customer is looking for and creating a solution to meet that need. It is possible to achieve this by making everything, from the production process through to customer service efficient and consistent.
The use of lean principles in the production of products can be an effective way to cut costs and increase efficiency. However, it is important to get your employees on board. Without a strong commitment to the program, the results could be disastrous.
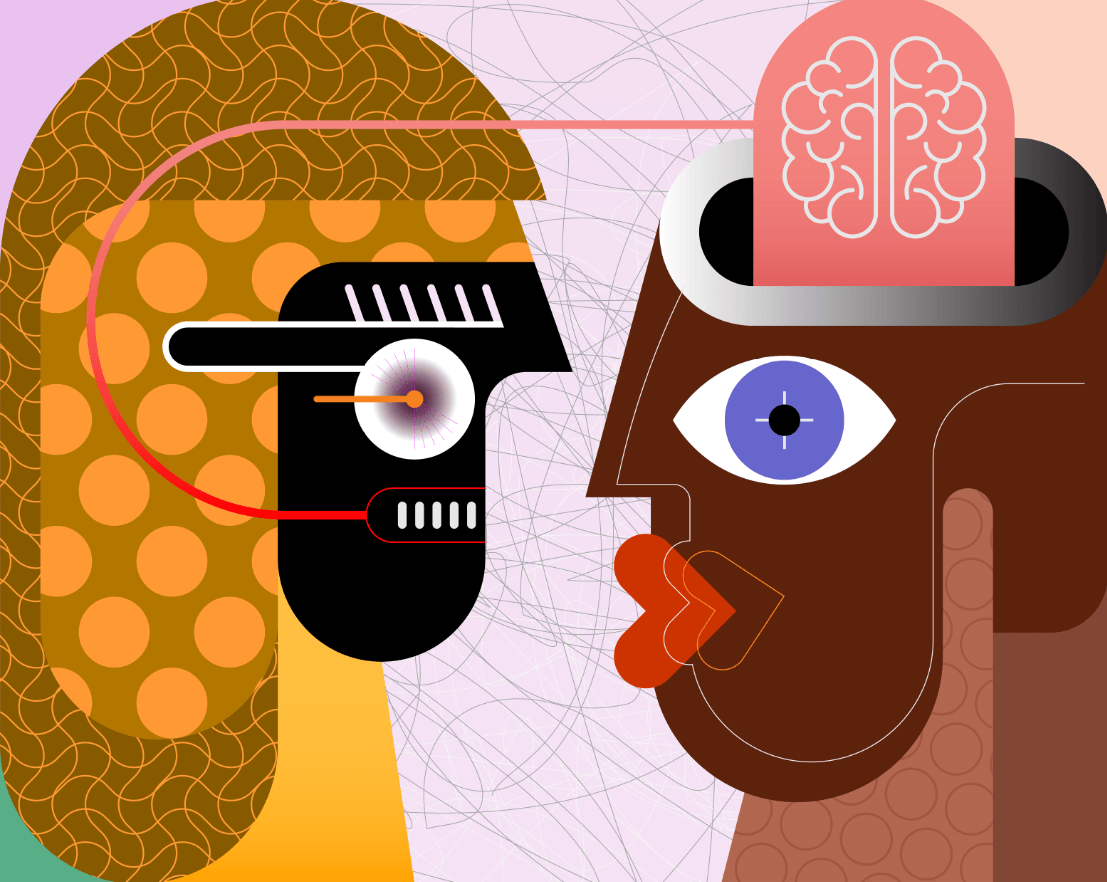
Along with gaining the buy-in of your workforce, it is important to ensure that you have a healthy supply network. It's because many lean initiatives involve retooling the supply-chain to make it function well.
You should ensure your staff are well-trained in lean principles. It is important that your staff understands what waste is, and why it should be removed from the production process.
Another aspect that you need to consider when implementing lean principles is the need for teamwork. It is a difficult goal to reach, but this is a crucial part of the lean production system that will eliminate waste.
Your team will be able to create better products and services, and your bottom line will increase over time. Give your team the opportunity to meet and discuss ways of reducing wastes.
A lean manager can help you achieve this by making sure that your workers have the proper training and know how to use these techniques. They can also keep your production running smoothly and efficiently, by keeping the team updated on any potential issues.
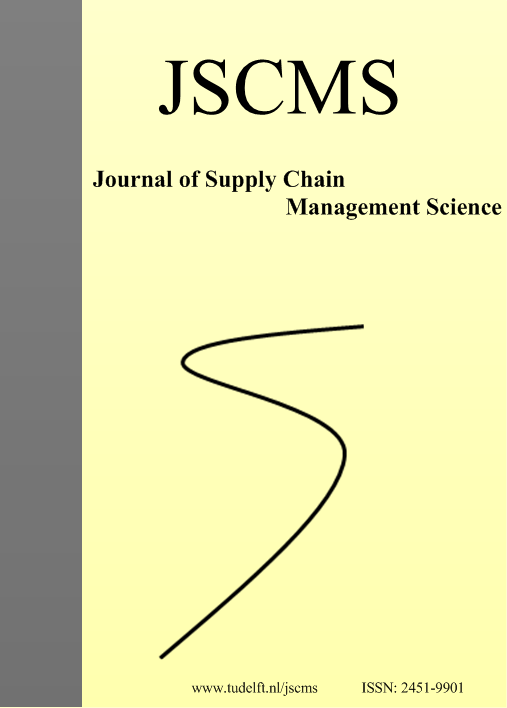
The final step in lean system management is to monitor and improve each of the procedures that are being implemented. You can do this by tracking each project's progress and making sure that all necessary changes are made.
Depending on the level of your organization, you may need to hire someone to manage your lean operations. Searching for lean management positions or job boards can help you find candidates.
FAQ
What type of jobs is there in logistics
There are many kinds of jobs available within logistics. Here are some examples:
-
Warehouse workers - They load trucks and pallets.
-
Transportation drivers – They drive trucks or trailers to transport goods and perform pick-ups.
-
Freight handlers, - They sort out and pack freight in warehouses.
-
Inventory managers – They manage the inventory in warehouses.
-
Sales representatives - They sell products to customers.
-
Logistics coordinators – They plan and coordinate logistics operations.
-
Purchasing agents - They purchase goods and services needed for company operations.
-
Customer service representatives - Answer calls and email from customers.
-
Ship clerks - They issue bills and process shipping orders.
-
Order fillers - These people fill orders based on what has been ordered.
-
Quality control inspectors – They inspect incoming and outgoing products to ensure that there are no defects.
-
Others - There is a variety of other jobs in logistics. These include transportation supervisors and cargo specialists.
What are the products and services of logistics?
Logistics refers to all activities that involve moving goods from A to B.
They cover all aspects of transportation, such as packing, loading, transporting and unloading.
Logisticians ensure that the product is delivered to the correct place, at the right time, and under safe conditions. Logisticians assist companies in managing their supply chains by providing information such as demand forecasts, stock levels and production schedules.
They coordinate with vendors and suppliers, keep track of shipments, monitor quality standards and perform inventory and order replenishment.
What is the difference between manufacturing and logistics
Manufacturing refers to the process of making goods using raw materials and machines. Logistics manages all aspects of the supply chain, including procurement, production planning and distribution, inventory control, transportation, customer service, and transport. Logistics and manufacturing are often referred to as one thing. It encompasses both the creation of products and their delivery to customers.
Is there anything we should know about Manufacturing Processes prior to learning about Logistics.
No. It doesn't matter if you don't know anything about manufacturing before you learn about logistics. However, knowing about manufacturing processes will definitely give you a better understanding of how logistics works.
What is the difference between a production planner and a project manager?
The primary difference between a producer planner and a manager of a project is that the manager usually plans and organizes the whole project, while a production planner is only involved in the planning stage.
What are the 7 Rs of logistics?
The acronym 7R's for Logistics stands to represent the seven basic principles in logistics management. It was developed by the International Association of Business Logisticians (IABL) and published in 2004 as part of its "Seven Principles of Logistics Management" series.
The acronym is made up of the following letters:
-
Responsible - to ensure that all actions are within the legal requirements and are not detrimental to others.
-
Reliable: Have faith in your ability or the ability to honor any promises made.
-
It is reasonable to use resources efficiently and not waste them.
-
Realistic – Consider all aspects, including cost-effectiveness as well as environmental impact.
-
Respectful - show respect and treat others fairly and fairly
-
Reliable - Find ways to save money and increase your productivity.
-
Recognizable: Provide customers with value-added service
What does it take for a logistics enterprise to succeed?
You need to have a lot of knowledge and skills to manage a successful logistic business. You must have good communication skills to interact effectively with your clients and suppliers. You must be able analyze data and draw out conclusions. You need to be able work under pressure and manage stressful situations. To increase efficiency and creativity, you need to be creative. You must be a strong leader to motivate others and direct them to achieve organizational goals.
It is also important to be efficient and well organized in order meet deadlines.
Statistics
- In 2021, an estimated 12.1 million Americans work in the manufacturing sector.6 (investopedia.com)
- According to a Statista study, U.S. businesses spent $1.63 trillion on logistics in 2019, moving goods from origin to end user through various supply chain network segments. (netsuite.com)
- (2:04) MTO is a production technique wherein products are customized according to customer specifications, and production only starts after an order is received. (oracle.com)
- You can multiply the result by 100 to get the total percent of monthly overhead. (investopedia.com)
- According to the United Nations Industrial Development Organization (UNIDO), China is the top manufacturer worldwide by 2019 output, producing 28.7% of the total global manufacturing output, followed by the United States, Japan, Germany, and India.[52][53] (en.wikipedia.org)
External Links
How To
How to use 5S in Manufacturing to Increase Productivity
5S stands as "Sort", Set In Order", Standardize", Separate" and "Store". Toyota Motor Corporation invented the 5S strategy in 1954. It improves the work environment and helps companies to achieve greater efficiency.
This method aims to standardize production processes so that they are repeatable, measurable and predictable. It means tasks like cleaning, sorting or packing, labeling, and storing are done every day. Through these actions, workers can perform their jobs more efficiently because they know what to expect from them.
There are five steps that you need to follow in order to implement 5S. Each step has a different action and leads to higher efficiency. You can make it easy for people to find things later by sorting them. Once you have placed items in an ordered fashion, you will put them together. You then organize your inventory in groups. Make sure everything is correctly labeled when you label your containers.
This requires employees to critically evaluate how they work. Employees must be able to see why they do what they do and find a way to achieve them without having to rely on their old methods. They must learn new skills and techniques in order to implement the 5S system.
The 5S method not only increases efficiency but also boosts morale and teamwork. Once they start to notice improvements, they are motivated to keep working towards their goal of increasing efficiency.