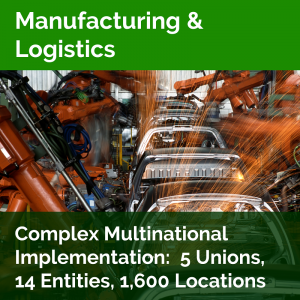
Six-Sigma and lean are complementary approaches to improving processes. Although they both have the same tools for problem solving, each has its strengths and weaknesses. Six-Sigma is a technique for statistical process control. Lean begins with the belief that a product must create value rather than just produce it. Lean means reducing waste and increasing the quality of the product being made.
Problem solving for PDCA
Although there are differences in DMAIC problem solving and PDCA, they both use the DMAIC approach. The PDCA cycle needs more planning and analysis. Unlike DMAIC, PDCA is not effective for solving urgent problems. This approach requires a problem-solver who has technical skills. In the Six Sigma case, a problem-solving lead will be a "green belt" certified Six Sigma practitioner.
Six Sigma's problem-solving cycle was introduced in the 1950s by W. Edwards Deming. It was intended to be used together with continuous improvement techniques to rebuild Japan’s industries. The P (Plan) stage requires real data to be gathered and a clear mission. After the PDCA stage, the team must decide on a recommended solution.
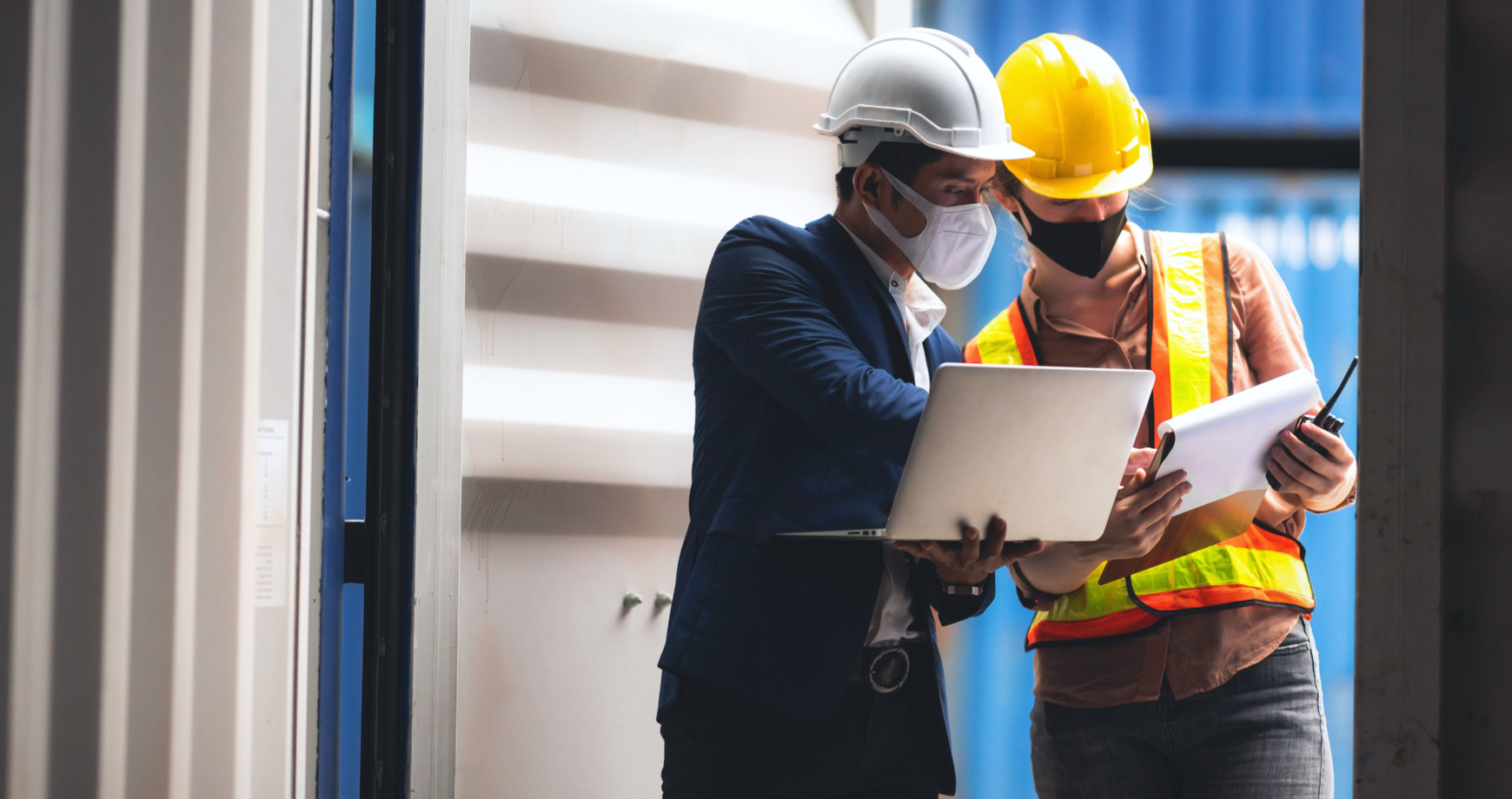
Process maps
A key difference between Lean and Six Sigma processes maps is how each approach describes the processes. Both methods focus on defining the process in detail but each approach focuses more on different aspects. Lean is a method of mapping actual processes, not standard operating protocols. When creating process diagrams, you should consider the major decisions, activities, and sources for approval. You should include areas that you may use multiple methods or factors. Make sure you match the roles and look at the process flow.
To show the flow of a process, a process map should contain steps, symbols and arrows. Each process should be reviewed by several people to ensure that it accurately reflects the actual process. It should also contain information about the date and who to call if you have any questions. Overall, process maps can improve a process. They may also be complex.
Analysis of cause & effect
Six Sigma, lean project management techniques are based on statistical analysis. The Cause and Effect Matrix, also known as the Cause and Effect Matrix (CAE), links each step of a process to its inputs and outputs. The customer requirements are listed by importance and then inputs and outputs are ranked according their effect on the outcome. Key process input variables and their ranking should be determined.
While each technique brings unique benefits, they are all not the same. Lean Six Sigma employs a process improvement method that is based upon Frederick Winslow Taylor’s Principles of Scientific Management. Taylor envisioned business processes as interlocking processes and workflows. He recommended reducing variability as well. Six-Sigma (and lean) are complementary in the effort to reduce waste.
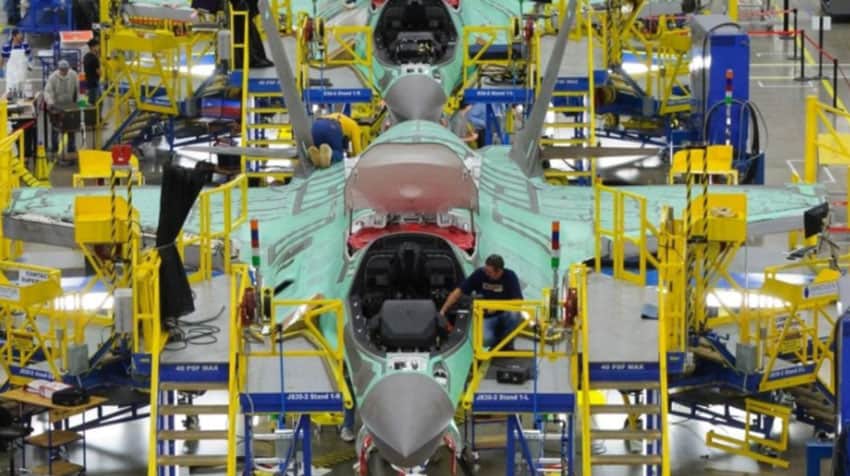
Elimination of variation
Variation is a part of any manufacturing process. Variability in manufacturing processes can cause uncertainty regarding the outcome. Professional results require consistency. Six Sigma and Lean manufacturing methods strive to eliminate variation. Variation is OK. However, too much variation can lead the to repairs, rework, as well as possible out-of-business consequences. The best way to manage variation is to identify the root cause.
You should first look at decision points for variations. Process maps are used to identify decision points. These are represented as diamonds. Six Sigma teams can start by identifying decision points and start eliminating variations there. This information is obtained from either the Six Sigma team owner or process owner. If the owner of a process does not follow a standardized process, the Six Sigma team can't focus on it. A process map might not work if the Six Sigma team lacks the technical capability to make necessary adjustments.
FAQ
How can overproduction in manufacturing be reduced?
In order to reduce excess production, you need to develop better inventory management methods. This would reduce the amount of time spent on unnecessary activities such as purchasing, storing, and maintaining excess stock. This will allow us to free up resources for more productive tasks.
Kanban systems are one way to achieve this. A Kanban board can be used to monitor work progress. Kanban systems are where work items travel through a series of states until reaching their final destination. Each state has a different priority level.
As an example, if work is progressing from one stage of the process to another, then the current task is complete and can be transferred to the next. It is possible to keep a task in the beginning stages until it gets to the end.
This allows you to keep work moving along while making sure that no work gets neglected. Managers can view the Kanban board to see how much work they have done. This information allows them to adjust their workflow based on real-time data.
Lean manufacturing is another way to manage inventory levels. Lean manufacturing works to eliminate waste throughout every stage of the production chain. Waste includes anything that does not add value to the product. Here are some examples of common types.
-
Overproduction
-
Inventory
-
Unnecessary packaging
-
Materials in excess
These ideas can help manufacturers improve efficiency and reduce costs.
What is the role and responsibility of a Production Planner?
Production planners make sure that every aspect of the project is delivered on-time, within budget, and within schedule. They also ensure that the product/service meets the client’s needs.
Are there any Manufacturing Processes that we should know before we can learn about Logistics?
No. No. However, knowing about manufacturing processes will definitely give you a better understanding of how logistics works.
Statistics
- (2:04) MTO is a production technique wherein products are customized according to customer specifications, and production only starts after an order is received. (oracle.com)
- According to a Statista study, U.S. businesses spent $1.63 trillion on logistics in 2019, moving goods from origin to end user through various supply chain network segments. (netsuite.com)
- [54][55] These are the top 50 countries by the total value of manufacturing output in US dollars for its noted year according to World Bank.[56] (en.wikipedia.org)
- It's estimated that 10.8% of the U.S. GDP in 2020 was contributed to manufacturing. (investopedia.com)
- In the United States, for example, manufacturing makes up 15% of the economic output. (twi-global.com)
External Links
How To
How to use 5S to increase Productivity in Manufacturing
5S stands for "Sort", "Set In Order", "Standardize", "Separate" and "Store". Toyota Motor Corporation developed the 5S method in 1954. This methodology helps companies improve their work environment to increase efficiency.
This method has the basic goal of standardizing production processes to make them repeatable. This means that every day tasks such cleaning, sorting/storing, packing, and labeling can be performed. These actions allow workers to perform their job more efficiently, knowing what to expect.
Implementing 5S involves five steps: Sort, Set in Order, Standardize Separate, Store, and Each step involves a different action which leads to increased efficiency. For example, when you sort things, you make them easy to find later. You arrange items by placing them in an order. Once you have separated your inventory into groups and organized them, you will store these groups in easily accessible containers. Finally, label all containers correctly.
Employees need to reflect on how they do their jobs. Employees need to understand the reasons they do certain jobs and determine if there is a better way. They will need to develop new skills and techniques in order for the 5S system to be implemented.
The 5S method not only increases efficiency but also boosts morale and teamwork. As they begin to see improvements, they feel motivated to continue working towards the goal of achieving higher levels of efficiency.