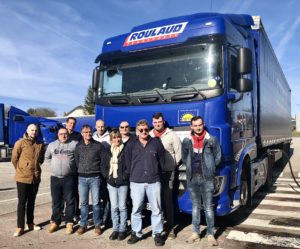
Purchasing Managers, also known as Materials Managers, are responsible for sourcing and coordinating all purchasing activities. They interact with suppliers, vendors, and other purchasing agents. They need to have a good understanding of the company's purchasing process, and how to improve it. They must also know how to negotiate the best deal for the company.
The purchasing manager must keep up-to-date and accurate records. They evaluate the price trends, analyze financial reports, and analyze customer needs. They coordinate purchasing activities with other departments. They may be required to work overtime if the company needs supplies from international markets.
Coordinate and manage inventory, logistics and other activities. They make decisions about the best way to purchase products and ensure they meet company quality standards. They manage budgets and work with their staff to ensure that purchases are made at the best possible price. They also work to find the best vendors and negotiate contracts.

The time schedules of all purchasing staff are also monitored and managed by the Purchasing Managers. They also evaluate the quality of goods purchased, their speed of delivery and how much they cost. They meet with suppliers and buyers and visit their distribution facilities. They ensure that all suppliers adhere to the contract terms. They may also be responsible for disciplinary matters and team building.
Purchasing Managers must have excellent communication skills, analytical abilities, and strategic thinking skills. They should be able analyze the impact of different products on the company. They must have the ability to manage suppliers, and their relationships. They should be able make business decisions, and increase sales. They should also be able handle complex purchases. They must be able assess new vendors, evaluate their capabilities and determine the best vendor for the company.
A bachelor's degree or equivalent in business is required of most purchasing managers. It is also helpful if they have experience in inventory management and supply chain management. They must also have a knowledge of Microsoft Office, as well as other computer software programs.
The best purchasing managers should be able find the best deals and negotiate favorable contracts. They should also have the ability to coordinate all purchasing activities. Manage inventories and track vendor and supplier performance. They must also be able to manage a group of purchasing agents.
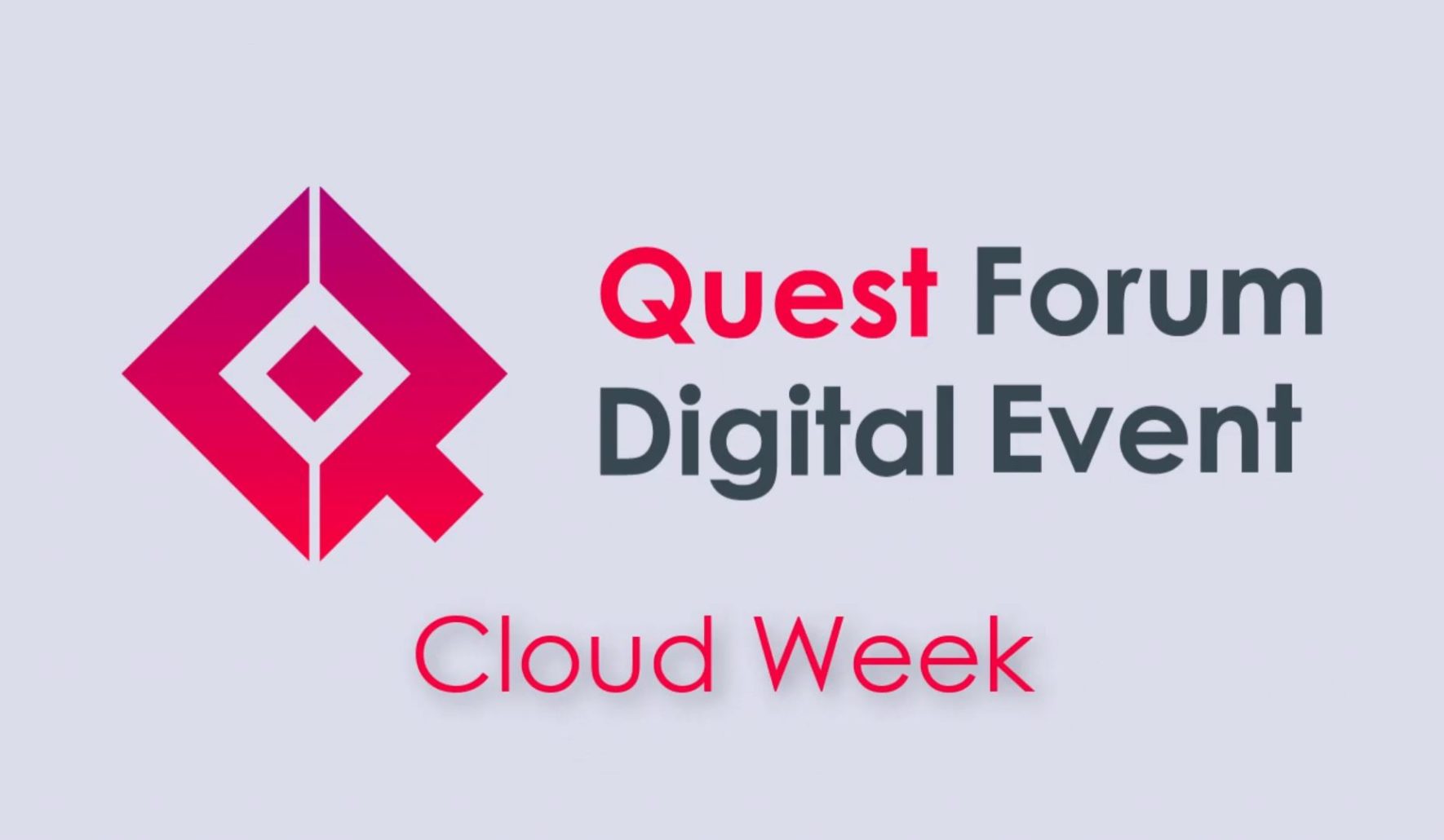
A job description for the purchase manager should include a mention of how important purchasing is to the company. It should also include how vital it is for the company that they stay ahead of their competitors. It should also reflect how much the company values its employees' personal and professional lives. It should include a call for action to encourage applicants.
If the company has to buy materials or equipment for international markets, Purchasing Managers might work overtime. They may have to deal directly with vendors and buyers and attend trade fairs.
FAQ
How can I learn about manufacturing?
Experience is the best way for you to learn about manufacturing. You can read books, or watch instructional videos if you don't have the opportunity to do so.
What skills are required to be a production manager?
Production planners must be flexible, organized, and able handle multiple tasks. It is also important to be able communicate with colleagues and clients.
Why is logistics so important in manufacturing?
Logistics are an integral part any business. They enable you to achieve outstanding results by helping manage product flow from raw materials through to finished goods.
Logistics play an important role in reducing costs as well as increasing efficiency.
What are manufacturing & logistics?
Manufacturing refers to the process of making goods using raw materials and machines. Logistics is the management of all aspects of supply chain activities, including procurement, production planning, distribution, warehousing, inventory control, transportation, and customer service. As a broad term, manufacturing and logistics often refer to both the creation and delivery of products.
Statistics
- According to the United Nations Industrial Development Organization (UNIDO), China is the top manufacturer worldwide by 2019 output, producing 28.7% of the total global manufacturing output, followed by the United States, Japan, Germany, and India.[52][53] (en.wikipedia.org)
- In the United States, for example, manufacturing makes up 15% of the economic output. (twi-global.com)
- Job #1 is delivering the ordered product according to specifications: color, size, brand, and quantity. (netsuite.com)
- It's estimated that 10.8% of the U.S. GDP in 2020 was contributed to manufacturing. (investopedia.com)
- According to a Statista study, U.S. businesses spent $1.63 trillion on logistics in 2019, moving goods from origin to end user through various supply chain network segments. (netsuite.com)
External Links
How To
Six Sigma and Manufacturing
Six Sigma is "the application statistical process control (SPC), techniques for continuous improvement." It was developed by Motorola's Quality Improvement Department at their plant in Tokyo, Japan, in 1986. Six Sigma's basic concept is to improve quality and eliminate defects through standardization. Since there are no perfect products, or services, this approach has been adopted by many companies over the years. Six Sigma seeks to reduce variation between the mean production value. This means that if you take a sample of your product, then measure its performance against the average, you can find out what percentage of the time the process deviates from the norm. If it is too large, it means that there are problems.
Understanding the nature of variability in your business is the first step to Six Sigma. Once you have a good understanding of the basics, you can identify potential sources of variation. Also, you will need to identify the sources of variation. Random variations are caused by human errors. Systematic variations can be caused by outside factors. You could consider random variations if some widgets fall off the assembly lines. You might notice that your widgets always fall apart at the same place every time you put them together.
Once you've identified where the problems lie, you'll want to design solutions to eliminate those problems. That solution might involve changing the way you do things or redesigning the process altogether. After implementing the new changes, you should test them again to see if they worked. If they fail, you can go back to the drawing board to come up with a different plan.