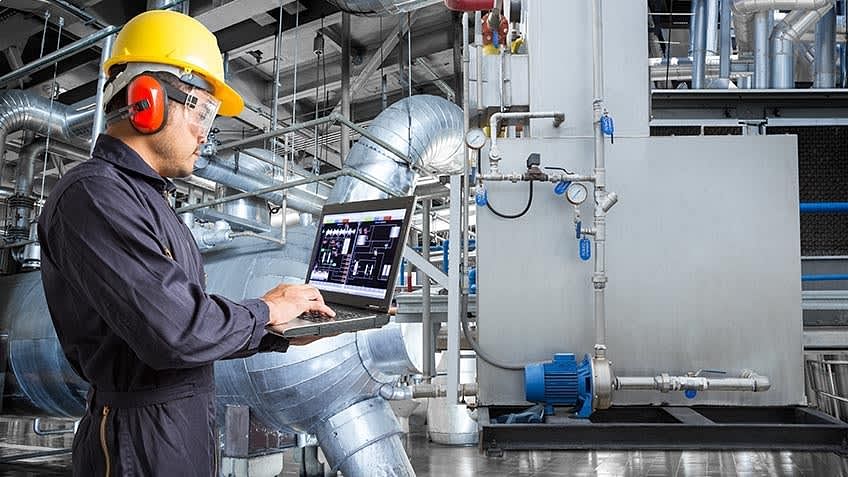
Andon, in the world of lean production, is a visual sign that highlights and draws attention to issues with the intention of solving them permanently. It's an instrument that empowers operators on the production floor and speeds up teamwork.
Andon
The word is of Japanese origin and comes from the paper-covered lanterns of the Edo era, which is the period between the seventeenth and nineteenth centuries. In Japanese, the term can refer to an alert system which uses light or sound signals to signal a process problem.
Toyota uses the term "build-in" quality as a core principle of its Jidoka. It is a component in their TPS system (Toyota Production System). In the US, it is often cited as the root of a commercial concept that allows production line employees to stop the line when a safety or quality problem exists.
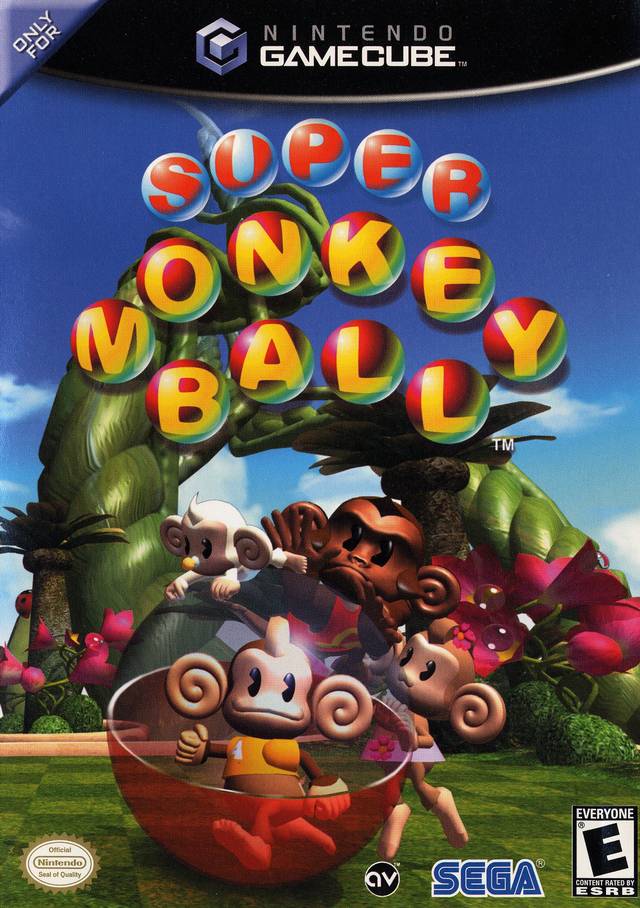
What is anon?
Toyota was the first to introduce Andon, a lean-manufacturing system. The system is simple and consists of an LED board with three colors: green, yellow, and red. Each color indicates a different state of the production. When the green lights are on, the production is going smoothly. When the yellow signal is lit, an issue has been detected and is under investigation. When the red lights are on, production stops. Workers can go on a break, help others, or fill up their bins.
Andon's board is simple to operate and supervisors understand exactly what has occurred. The system was designed to give immediate feedback, ensuring that all problems are solved as quickly as possible.
Many types of adons are available, but the most popular is a bright red light combined with a loud sound or buzzer that alerts production teams. These signal, alert and resolve systems are effective in identifying issues that could result in downtime or repeat issues.
A good andon board helps keep the production going when a problem arises. This simple tool increases productivity, decreases downtime and improves safety and product quality.
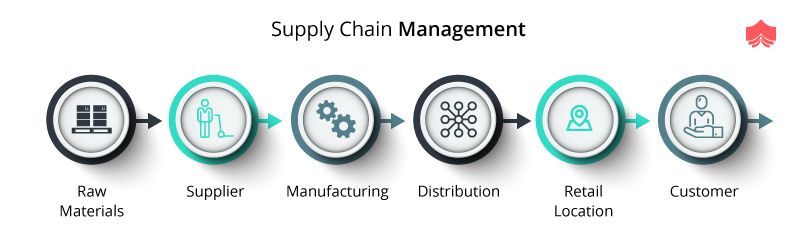
What is andon toyota?
Toyota used a special cord that any employee on the manufacturing floor could pull if they saw a potential issue with one of their cars. Pulling this cord would stop the production immediately if a worker thought the car was faulty.
Modern andon systems also use technology to curate information, which makes it easier to identify emerging problems, send notifications to stakeholders in real-time, and determine the root cause of a problem that requires a long term fix. However, human touch is still essential in interpreting and acting upon this information.
How to make Andon work?
It is important to start by creating a culture in which workers and managers are not afraid to address and identify problems. The more they are hesitant, the more they're likely to conceal problems and miss a chance to fix them. The quickest way to improve this is to tie line stops to problem resolution, so that workers are more likely to hit the button and pull the cord when they see something amiss.
FAQ
Why automate your warehouse?
Automation has become increasingly important in modern warehousing. Increased demand for efficient and faster delivery has resulted in a rise in e-commerce.
Warehouses must adapt quickly to meet changing customer needs. Technology investment is necessary to enable warehouses to respond quickly to changing demands. Automating warehouses has many benefits. Here are some reasons why it's worth investing in automation:
-
Increases throughput/productivity
-
Reduces errors
-
Accuracy is improved
-
Safety is boosted
-
Eliminates bottlenecks
-
This allows companies to scale easily
-
It makes workers more efficient
-
It gives visibility to everything that happens inside the warehouse
-
Enhances customer experience
-
Improves employee satisfaction
-
Reducing downtime and increasing uptime
-
High quality products delivered on-time
-
Removes human error
-
This helps to ensure compliance with regulations
How can efficiency in manufacturing be improved?
First, identify the factors that affect production time. Then we need to find ways to improve these factors. If you don't know where to start, then think about which factor(s) have the biggest impact on production time. Once you have identified the factors, then try to find solutions.
What is the role and responsibility of a Production Planner?
Production planners ensure all aspects of the project are delivered within time and budget. They also ensure the quality of the product and service meets the client's requirements.
What do we need to know about Manufacturing Processes in order to learn more about Logistics?
No. No. It is important to know about the manufacturing processes in order to understand how logistics works.
What are the four types of manufacturing?
Manufacturing is the process by which raw materials are transformed into useful products through machines and processes. Manufacturing involves many activities, including designing, building, testing and packaging, shipping, selling, service, and so on.
Statistics
- In 2021, an estimated 12.1 million Americans work in the manufacturing sector.6 (investopedia.com)
- Many factories witnessed a 30% increase in output due to the shift to electric motors. (en.wikipedia.org)
- [54][55] These are the top 50 countries by the total value of manufacturing output in US dollars for its noted year according to World Bank.[56] (en.wikipedia.org)
- According to the United Nations Industrial Development Organization (UNIDO), China is the top manufacturer worldwide by 2019 output, producing 28.7% of the total global manufacturing output, followed by the United States, Japan, Germany, and India.[52][53] (en.wikipedia.org)
- According to a Statista study, U.S. businesses spent $1.63 trillion on logistics in 2019, moving goods from origin to end user through various supply chain network segments. (netsuite.com)
External Links
How To
Six Sigma and Manufacturing
Six Sigma is defined by "the application SPC (statistical process control) techniques to achieve continuous improvements." It was developed by Motorola's Quality Improvement Department at their plant in Tokyo, Japan, in 1986. Six Sigma is a method to improve quality through standardization and elimination of defects. Many companies have adopted Six Sigma in recent years because they believe that there are no perfect products and services. Six Sigma aims to reduce variation in the production's mean value. This means that you can take a sample from your product and then compare its performance to the average to find out how often the process differs from the norm. If this deviation is too big, you know something needs fixing.
Understanding how variability works in your company is the first step to Six Sigma. Once you understand that, it is time to identify the sources of variation. This will allow you to decide if these variations are random and systematic. Random variations occur when people do mistakes. Symmetrical variations are caused due to factors beyond the process. If you make widgets and some of them end up on the assembly line, then those are considered random variations. However, if you notice that every time you assemble a widget, it always falls apart at exactly the same place, then that would be a systematic problem.
Once you have identified the problem, you can design solutions. The solution could involve changing how you do things, or redesigning your entire process. Test them again once you've implemented the changes. If they fail, you can go back to the drawing board to come up with a different plan.