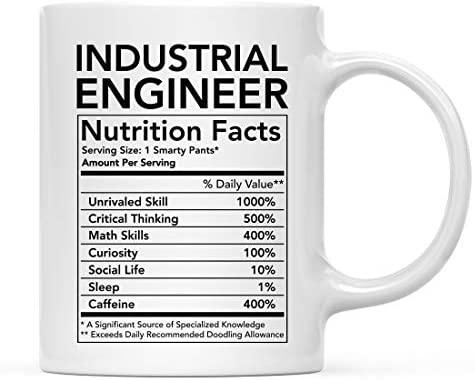
Every five years between 2 and 7 years of age, the Census Bureau collects vital statistics that is essential for understanding the economy. These statistics, called the Economic Census, are the basis of all other business and industrial statistics.
The Economic Census surveys business establishments based on the primary activity of each business. The establishments can be classified according to their primary business activity and geographical location. This classification is derived from the North American Industry Classification System (NAICS).
Owners and firms of businesses
Surveys of entrepreneurs and businesses are conducted using a company/firm basis rather than an establishment. A company or firm is defined as a business that has paid employees and reports receipts of $1,000 per year. This survey includes sole entrepreneurs and nonfarming partnerships that are taxed by the Internal Revenue Service, as well non-employer firms that can be reimbursed.
Characteristics Of Business Owners And Firms
The Census Bureau's Survey of Business Owners is its largest survey of owners of businesses, including women and minorities. It began as a special project for minority-owned businesses in 1969, and was incorporated into the economic census in 1972 along with the Survey of Women-Owned Businesses.
This database is multi-relational and contains information on over 6,000,000 single-unit establishments, as well as 1.8,000,000 multi-unit ones. This information is used in all of the Bureau's programs that collect economic data, such as the Census Bureau Economic Census, County Business Patterns, special summary reports, and non-employer statistics.
Business Register and Census Bureau's Statistical Abstract of Business Enterprises
SBO or the Statistical Abstract of Business Enterprises is the Census Bureau's principal source of non-employer firm information. This is a database with a large number of relationships that includes information on every establishment known to have paid employees within the United States. The data collected are based on firm owners or firms. They are used in the compilation of statistics for programs such as the Economic Census.
SBO contains a number statistical measures that are not included in other census programmes, including establishment births, deaths, firm startups and shutdowns, job creation, and destruction. SBO includes information on demographics of business owners such as their age and educational background, and also provides details about home-based businesses and franchise participation.
SBO Data for Minority- and Women-Owned Businesses
The Survey of Minority- and Women-Owned Business is an annual survey of non-farm businesses that includes those filing income taxes as individual proprietorships, partnerships or corporations, as well as firms with receipts of at least $1,000 per year. It is a primary source of statistics about minority and women-owned businesses, and provides an annual estimate of their total receipts.
This is a valuable resource for researchers who are interested in minority- and women's-owned business. The report also gives an overview of race distributions within various state-industry groups and ZIP Codes. This is helpful for analyzing the economic effects of discrimination.
FAQ
What is production planning?
Production planning is the process of creating a plan that covers all aspects of production. This includes scheduling, budgeting and crew, location, equipment, props, and more. This document will ensure everything is in order and ready to go when you need it. This document should also include information on how to get the best result on set. This information includes locations, crew details and equipment requirements.
First, you need to plan what you want to film. You may already know where you want the film to be shot, or perhaps you have specific locations and sets you wish to use. Once you have identified the scenes and locations, you can start to determine which elements are required for each scene. Perhaps you have decided that you need to buy a car but aren't sure which model. To narrow your options, you can search online for available models.
After you have selected the car you want, you can begin to think about additional features. Do you need people sitting in the front seats? Perhaps you have someone who needs to be able to walk around the back of your car. Maybe you'd like to change the interior from black to a white color. These questions can help you decide the right look for your car. It is also worth considering the types of shots that you wish to take. You will be filming close-ups and wide angles. Maybe you want to show your engine or the steering wheel. This will allow you to determine the type of car you want.
Once you have all the information, you are ready to create a plan. The schedule will show you when to begin shooting and when to stop. Every day will have a time for you to arrive at the location, leave when you are leaving and return home when you are done. Everyone will know what they need and when. Hire extra staff by booking them ahead of time. It's not worth paying someone to show up if you haven't told him.
Your schedule will also have to be adjusted to reflect the number of days required to film. Some projects only take one or two days, while others may last weeks. While creating your schedule, it is important to remember whether you will require more than one shot per day. Multiplying takes in the same area will result both in increased costs and a longer time. If you aren't sure whether you need multiple shots, it is best to take fewer photos than you would like.
Budgeting is another important aspect of production planning. As it will allow you and your team to work within your financial means, setting a realistic budget is crucial. Keep in mind that you can always reduce your budget if you face unexpected difficulties. But, don't underestimate how much money you'll spend. If you underestimate the cost of something, you will have less money left after paying for other items.
Production planning is a detailed process. But, once you understand the workings of everything, it becomes easier for future projects to be planned.
What are the 7 Rs of logistics.
The acronym "7R's" of Logistics stands for seven principles that underpin logistics management. It was developed and published by the International Association of Business Logisticians in 2004 as part of the "Seven Principles of Logistics Management".
The following letters form the acronym:
-
Responsible - ensure that actions are in compliance with legal requirements and do not cause harm to others.
-
Reliable - have confidence in the ability to deliver on commitments made.
-
Be responsible - Use resources efficiently and avoid wasting them.
-
Realistic - Take into consideration all aspects of operations including cost-effectiveness, environmental impact, and other factors.
-
Respectful: Treat others with fairness and equity
-
Be resourceful: Look for opportunities to save money or increase productivity.
-
Recognizable provides value-added products and services to customers
What is the difference in Production Planning and Scheduling, you ask?
Production Planning (PP) is the process of determining what needs to be produced at any given point in time. This is done through forecasting demand and identifying production capacities.
Scheduling is the process of assigning specific dates to tasks so they can be completed within the specified timeframe.
What does manufacturing industry mean?
Manufacturing Industries refers to businesses that manufacture products. Consumers are those who purchase these products. These companies employ many processes to achieve this purpose, such as production and distribution, retailing, management and so on. They produce goods from raw materials by using machines and other machinery. This includes all types if manufactured goods.
What are the goods of logistics?
Logistics refers to the movement of goods from one place to another.
They include all aspects associated with transport including packaging, loading transporting, unloading storage, warehousing inventory management customer service, distribution returns and recycling.
Logisticians ensure that the right product reaches the right place at the right time and under safe conditions. They assist companies with their supply chain efficiency through information on demand forecasts. Stock levels, production times, and availability.
They keep track and monitor the transit of shipments, maintain quality standards, order replenishment and inventories, coordinate with suppliers, vendors, and provide support for sales and marketing.
Statistics
- In 2021, an estimated 12.1 million Americans work in the manufacturing sector.6 (investopedia.com)
- [54][55] These are the top 50 countries by the total value of manufacturing output in US dollars for its noted year according to World Bank.[56] (en.wikipedia.org)
- According to the United Nations Industrial Development Organization (UNIDO), China is the top manufacturer worldwide by 2019 output, producing 28.7% of the total global manufacturing output, followed by the United States, Japan, Germany, and India.[52][53] (en.wikipedia.org)
- It's estimated that 10.8% of the U.S. GDP in 2020 was contributed to manufacturing. (investopedia.com)
- (2:04) MTO is a production technique wherein products are customized according to customer specifications, and production only starts after an order is received. (oracle.com)
External Links
How To
Six Sigma and Manufacturing
Six Sigma refers to "the application and control of statistical processes (SPC) techniques in order to achieve continuous improvement." Motorola's Quality Improvement Department developed it at their Tokyo plant in Japan in 1986. Six Sigma is a method to improve quality through standardization and elimination of defects. Many companies have adopted Six Sigma in recent years because they believe that there are no perfect products and services. Six Sigma's primary goal is to reduce variation from the average value of production. If you take a sample and compare it with the average, you will be able to determine how much of the production process is different from the norm. If this deviation is too big, you know something needs fixing.
Understanding how your business' variability is a key step towards Six Sigma implementation is the first. Once you have this understanding, you will need to identify sources and causes of variation. These variations can also be classified as random or systematic. Random variations are caused by human errors. Systematic variations can be caused by outside factors. For example, if you're making widgets, and some of them fall off the assembly line, those would be considered random variations. But if you notice that every widget you make falls apart at the exact same place each time, this would indicate that there is a problem.
Once you have identified the problem, you can design solutions. This could mean changing your approach or redesigning the entire process. Test them again once you've implemented the changes. If they didn't work, then you'll need to go back to the drawing board and come up with another plan.