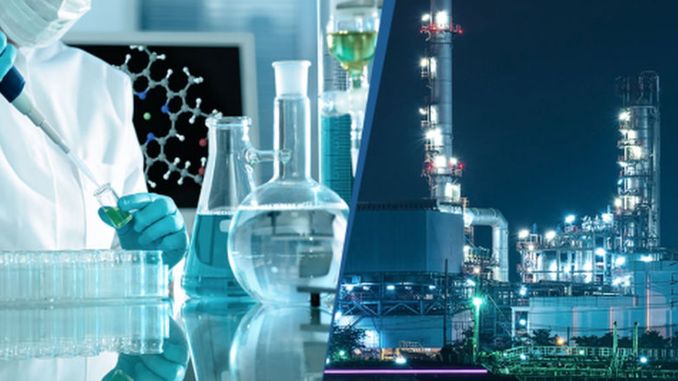
You're here because you are interested in a salary in biochemistry. This article will cover biochemical salary in BOTHELL WA as well as San Mateo CA. You can explore the many biochemical salary options to help you get started with your career. Find out more about the requirements for salary and job descriptions at Worthington Biochemical as well as Youtell Biochemical. Both companies have BOTHELL, WA headquarters and offer competitive benefits.
Youtell Biochemical is paying $29 an hour
Youtell Biochemical pays an average of $99,854. Salary ranges anywhere from $88,159 and $114,509. However, individual salaries can vary wildly depending on the position, department, education, and skills required. Below are some examples of the types of jobs and salaries at Youtell Biochemical. Also, the salary ranges depend on education and previous experience.
Youtell Biochemical has its headquarters in BOTHELL WA
Youtell Biochemical is an enzyme product-focused chemical company with headquarters in BOTHELL. They have a state-of-the-art biotechnology research center in Bothell, and two downstream processing and fermentation factories in China. These companies employ patented technologies to make enzyme products. Youtell Biochemical's main campus is located in BOTHELL WA and produces more than 80,000 tons of enzymes per year.
Worthington Biochemical is located in San Mateo (CA).
Worthington Biochemical was established in 1947. Charles Worthington, the founder of Worthington Biochemical, was an assistant researcher at the Rockefeller Institute who prepared crystal enzymes for biochemical researchers. He soon realized that the growing biochemical researcher community needed reliable, high quality enzymes. This meant that researchers would have a lot to spend time purifying them. Worthington established its own company in Freehold (New Jersey) in 1947 to provide these enzymes.
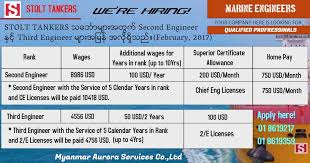
In 1985, Worthington acquired the Clinical Division of Cooper, a biotech firm based in New Jersey. Worthington's acquisition of the Clinical Division of Cooper, a biotech firm based in New Jersey, allowed it to expand its operations and allow it to concentrate more on the lucrative clinic market. However, the company failed to expand into the fields of molecular biology and immunology. Instead, the company developed diagnostic kits for more customers, but devoted less to enzyme production.
FAQ
What is production management?
Production Planning involves developing a plan for all aspects of the production, including scheduling, budgeting, casting, crew, location, equipment, props, etc. This document is designed to make sure everything is ready for when you're ready to shoot. This document should also include information on how to get the best result on set. This includes location information, crew details, equipment specifications, and casting lists.
It is important to first outline the type of film you would like to make. You may have decided where to shoot or even specific locations you want to use. Once you have identified the scenes and locations, you can start to determine which elements are required for each scene. Perhaps you have decided that you need to buy a car but aren't sure which model. If this is the case, you might start searching online for car models and then narrow your options by selecting from different makes.
After you've found the perfect car, it's time to start thinking about adding extras. What about additional seating? Maybe you need someone to move around in the back. You might want to change your interior color from black and white. These questions will help to determine the style and feel of your car. Also, think about what kind of shots you would like to capture. What type of shots will you choose? Maybe the engine or steering wheel is what you are looking to film. This will allow you to determine the type of car you want.
Once you have made all the necessary decisions, you can start to create a schedule. You will know when you should start and when you should finish shooting. The schedule will show you when to get there, what time to leave, and when to return home. Everyone knows exactly what they should do and when. You can also make sure to book extra staff in advance if you have to hire them. You should not hire anyone who doesn't show up because of your inaction.
When creating your schedule, you will also need to consider the number of days you need to film. Some projects may only take a couple of days, while others could last for weeks. When creating your schedule, be aware of whether you need more shots per day. Multiple shots at the same location can increase costs and make it more difficult to complete. It's better to be safe than sorry and shoot less takes if you're not certain whether you need more takes.
Budget setting is another important aspect in production planning. A realistic budget will help you work within your means. Keep in mind that you can always reduce your budget if you face unexpected difficulties. It is important to not overestimate how much you will spend. You'll end up with less money after paying for other things if the cost is underestimated.
Production planning is a complicated process. But once you understand how everything works together, it becomes much easier to plan future project.
What are manufacturing and logistics?
Manufacturing is the production of goods using raw materials. Logistics includes all aspects related to supply chain management, such as procurement, distribution planning, inventory control and transportation. As a broad term, manufacturing and logistics often refer to both the creation and delivery of products.
What kind of jobs are there in logistics?
There are many types of jobs in logistics. Some examples are:
-
Warehouse workers – They load, unload and transport pallets and trucks.
-
Transportation drivers – They drive trucks or trailers to transport goods and perform pick-ups.
-
Freight handlers: They sort and package freight in warehouses.
-
Inventory managers – They manage the inventory in warehouses.
-
Sales representatives - They sell products to customers.
-
Logistics coordinators: They plan and manage logistics operations.
-
Purchasing agents are those who purchase goods and services for the company.
-
Customer service representatives are available to answer customer calls and emails.
-
Shipping clerks: They process shipping requests and issue bills.
-
Order fillers are people who fill orders based only on what was ordered.
-
Quality control inspectors are responsible for inspecting incoming and outgoing products looking for defects.
-
Other - Logistics has many other job opportunities, including transportation supervisors, logistics specialists, and cargo specialists.
Statistics
- It's estimated that 10.8% of the U.S. GDP in 2020 was contributed to manufacturing. (investopedia.com)
- According to the United Nations Industrial Development Organization (UNIDO), China is the top manufacturer worldwide by 2019 output, producing 28.7% of the total global manufacturing output, followed by the United States, Japan, Germany, and India.[52][53] (en.wikipedia.org)
- According to a Statista study, U.S. businesses spent $1.63 trillion on logistics in 2019, moving goods from origin to end user through various supply chain network segments. (netsuite.com)
- Job #1 is delivering the ordered product according to specifications: color, size, brand, and quantity. (netsuite.com)
- [54][55] These are the top 50 countries by the total value of manufacturing output in US dollars for its noted year according to World Bank.[56] (en.wikipedia.org)
External Links
How To
How to Use 5S for Increasing Productivity in Manufacturing
5S stands as "Sort", Set In Order", Standardize", Separate" and "Store". Toyota Motor Corporation was the first to develop the 5S approach in 1954. This methodology helps companies improve their work environment to increase efficiency.
The basic idea behind this method is to standardize production processes, so they become repeatable, measurable, and predictable. This means that daily tasks such as cleaning and sorting, storage, packing, labeling, and packaging are possible. Because workers know what they can expect, this helps them perform their jobs more efficiently.
There are five steps that you need to follow in order to implement 5S. Each step has a different action and leads to higher efficiency. By sorting, for example, you make it easy to find the items later. When you set items in an order, you put items together. Then, after you separate your inventory into groups, you store those groups in containers that are easy to access. Labeling your containers will ensure that everything is correctly labeled.
This process requires employees to think critically about how they do their job. Employees should understand why they do the tasks they do, and then decide if there are better ways to accomplish them. To implement the 5S system, employees must acquire new skills and techniques.
In addition to increasing efficiency, the 5S method also improves morale and teamwork among employees. They feel more motivated to work towards achieving greater efficiency as they see the results.