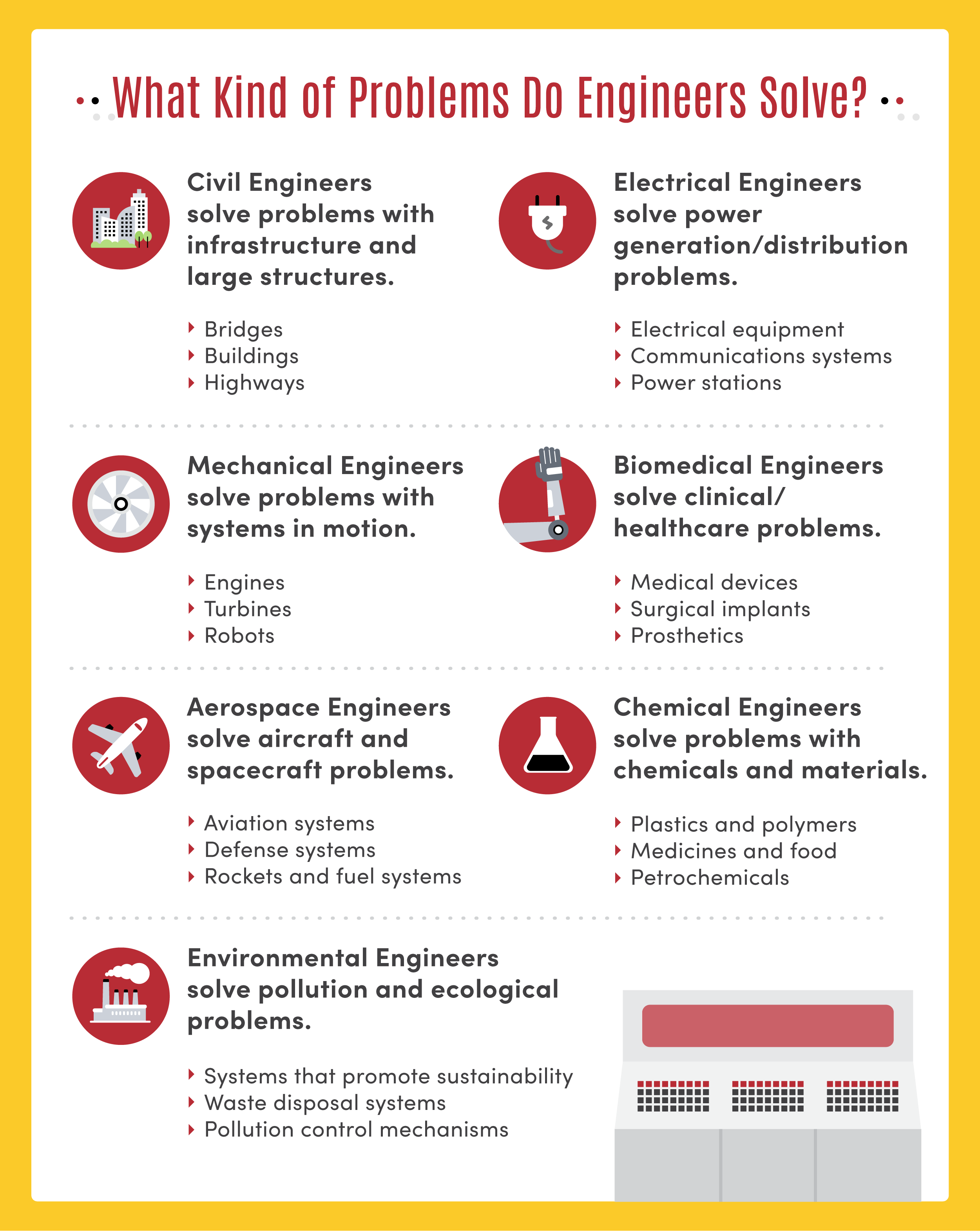
The process of planning demand involves predicting future demand for a product or service. It is an integral part of the supply chain management process, because it helps businesses meet customers' demands while maximizing efficiency and profits.
What is Demand Planning?
In order to plan demand, it is necessary to analyze data, such as sales data and stock information, in order forecast future demand. It's a complex task that may involve multiple departments.
What is a Demand Plan?
A demand planner is a member of a company's supply chain team who uses their understanding of the industry and their business acumen to predict future market trends and customer needs. They then create an ideal demand plan which includes ideal inventory, shipping timelines and all steps that a company must take to meet customer demand.

What Are the Best Tools to Plan Demand?
The most effective demand planning tools are those that provide end-to-end visibility across a company's entire supply chain. This gives planners the opportunity to track and analyse demand in real-time.
What is the best method to predict demand?
A company's sales department will often provide sales data directly to the analyst. These data will help you identify any issues your sales team is having with customers. This could result in changes to your demand plan.
A statistical analysis can be used to establish the relationship between sales and inventories. Using analytics to find these relationships can significantly improve the accuracy of a demand plan.
What Are Some of the Common Pitfalls in Demand Forecasting?
Demand planning can seem like a daunting task. It takes time and energy to do it right. A lack of accuracy in your demand planning can cause a host of problems. Excess inventory, for example, can result in the locking up of working capital or increased inventory carrying cost, both which are costly to companies and can negatively affect customers.
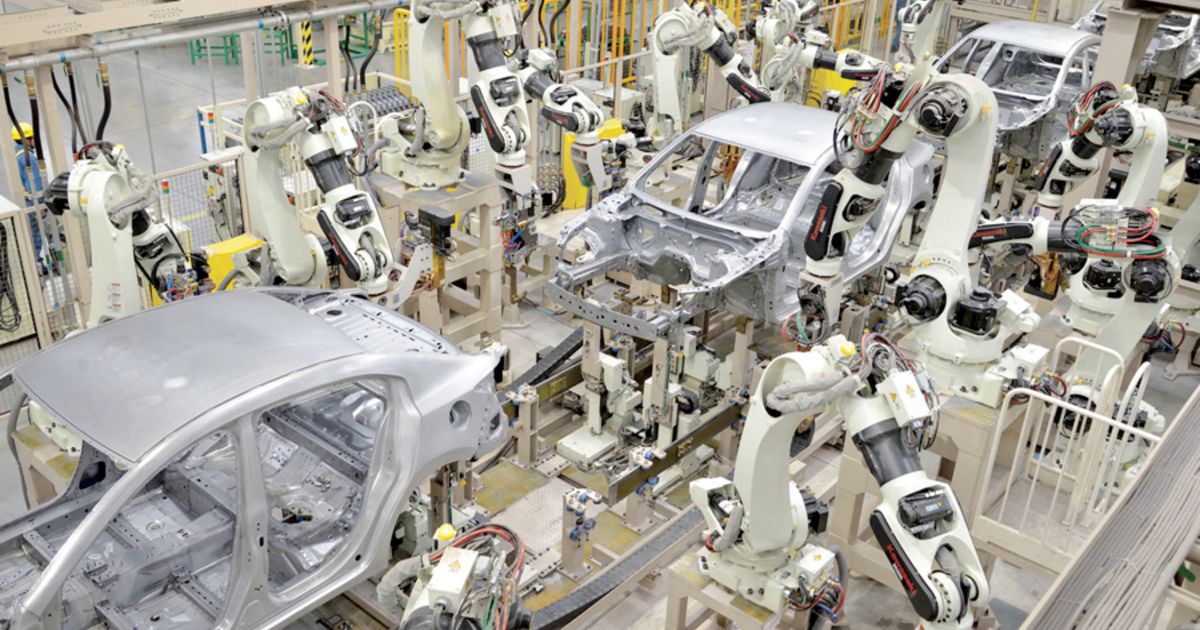
What are the most common skills that a demand planner requires?
A demand planer must have solid analytical and management skills. They should be able analyse complex data sets to make good decisions. They should also have the ability to reach a consensus and work well with others.
What are some of the most valuable skills in demand planning?
A great demand planner should be skilled with both people and technology. This is because they will be working with various teams to develop a forecasting model, and they need to be able to communicate effectively with these teams.
Demand planners should have a good understanding of the Delphi Method, which allows for outside feedback and facilitation from outside experts. This method can come in handy if you only have a small amount of data but need multiple perspectives on an issue.
FAQ
Why is logistics important for manufacturing?
Logistics are an integral part any business. They can help you achieve great success by helping you manage product flow from raw material to finished goods.
Logistics are also important in reducing costs and improving efficiency.
How can I learn about manufacturing?
Hands-on experience is the best way to learn more about manufacturing. If that is not possible, you could always read books or view educational videos.
What skills are required to be a production manager?
Being a production planner is not easy. You need to be organized and flexible. Effective communication with clients and colleagues is essential.
How important is automation in manufacturing?
Not only is automation important for manufacturers, but it's also vital for service providers. It enables them to provide services faster and more efficiently. It helps them to lower costs by reducing human errors, and improving productivity.
Statistics
- It's estimated that 10.8% of the U.S. GDP in 2020 was contributed to manufacturing. (investopedia.com)
- You can multiply the result by 100 to get the total percent of monthly overhead. (investopedia.com)
- According to a Statista study, U.S. businesses spent $1.63 trillion on logistics in 2019, moving goods from origin to end user through various supply chain network segments. (netsuite.com)
- Many factories witnessed a 30% increase in output due to the shift to electric motors. (en.wikipedia.org)
- In 2021, an estimated 12.1 million Americans work in the manufacturing sector.6 (investopedia.com)
External Links
How To
How to Use lean manufacturing in the Production of Goods
Lean manufacturing (or lean manufacturing) is a style of management that aims to increase efficiency, reduce waste and improve performance through continuous improvement. It was first developed in Japan in the 1970s/80s by Taiichi Ahno, who was awarded the Toyota Production System (TPS), award from KanjiToyoda, the founder of TPS. Michael L. Watkins published the "The Machine That Changed the World", the first book about lean manufacturing. It was published in 1990.
Lean manufacturing refers to a set of principles that improve the quality, speed and costs of products and services. It emphasizes eliminating waste and defects throughout the value stream. Lean manufacturing can be described as just-in–time (JIT), total productive maintenance, zero defect (TPM), or even 5S. Lean manufacturing focuses on eliminating non-value-added activities such as rework, inspection, and waiting.
Lean manufacturing not only improves product quality but also reduces costs. Companies can also achieve their goals faster by reducing employee turnover. Lean manufacturing is considered one of the most effective ways to manage the entire value chain, including suppliers, customers, distributors, retailers, and employees. Lean manufacturing is widely practiced in many industries around the world. For example, Toyota's philosophy underpins its success in automobiles, electronics, appliances, healthcare, chemical engineering, aerospace, paper, food, etc.
Five principles are the basis of lean manufacturing:
-
Define Value: Identify the social value of your business and what sets you apart.
-
Reduce waste - Stop any activity that isn't adding value to the supply chains.
-
Create Flow – Ensure that work flows smoothly throughout the process.
-
Standardize and simplify – Make processes as repeatable and consistent as possible.
-
Building Relationships – Establish personal relationships with both external and internal stakeholders.
Although lean manufacturing isn't a new concept in business, it has gained popularity due to renewed interest in the economy after the 2008 global financial crisis. Many businesses have adopted lean manufacturing techniques to help them become more competitive. Economists think that lean manufacturing is a crucial factor in economic recovery.
Lean manufacturing, which has many benefits, is now a standard practice in the automotive industry. These benefits include increased customer satisfaction, reduced inventory levels and lower operating costs.
You can apply Lean Manufacturing to virtually any aspect of your organization. This is because it ensures efficiency and effectiveness in all stages of the value chain.
There are three main types of lean manufacturing:
-
Just-in-Time Manufacturing: Also known as "pull systems", this type of lean manufacturing uses just-in-time manufacturing (JIT). JIT stands for a system where components are assembled on the spot rather than being made in advance. This method reduces lead times, increases availability, and decreases inventory.
-
Zero Defects Manufacturing (ZDM),: ZDM is a system that ensures no defective units are left the manufacturing facility. If a part needs to be fixed during the assembly line, it should be repaired rather than scrapped. This also applies to finished products that need minor repairs before being shipped.
-
Continuous Improvement (CI): CI aims to improve the efficiency of operations by continuously identifying problems and making changes in order to eliminate or minimize waste. Continuous Improvement (CI) involves continuous improvement in processes, people, tools, and infrastructure.