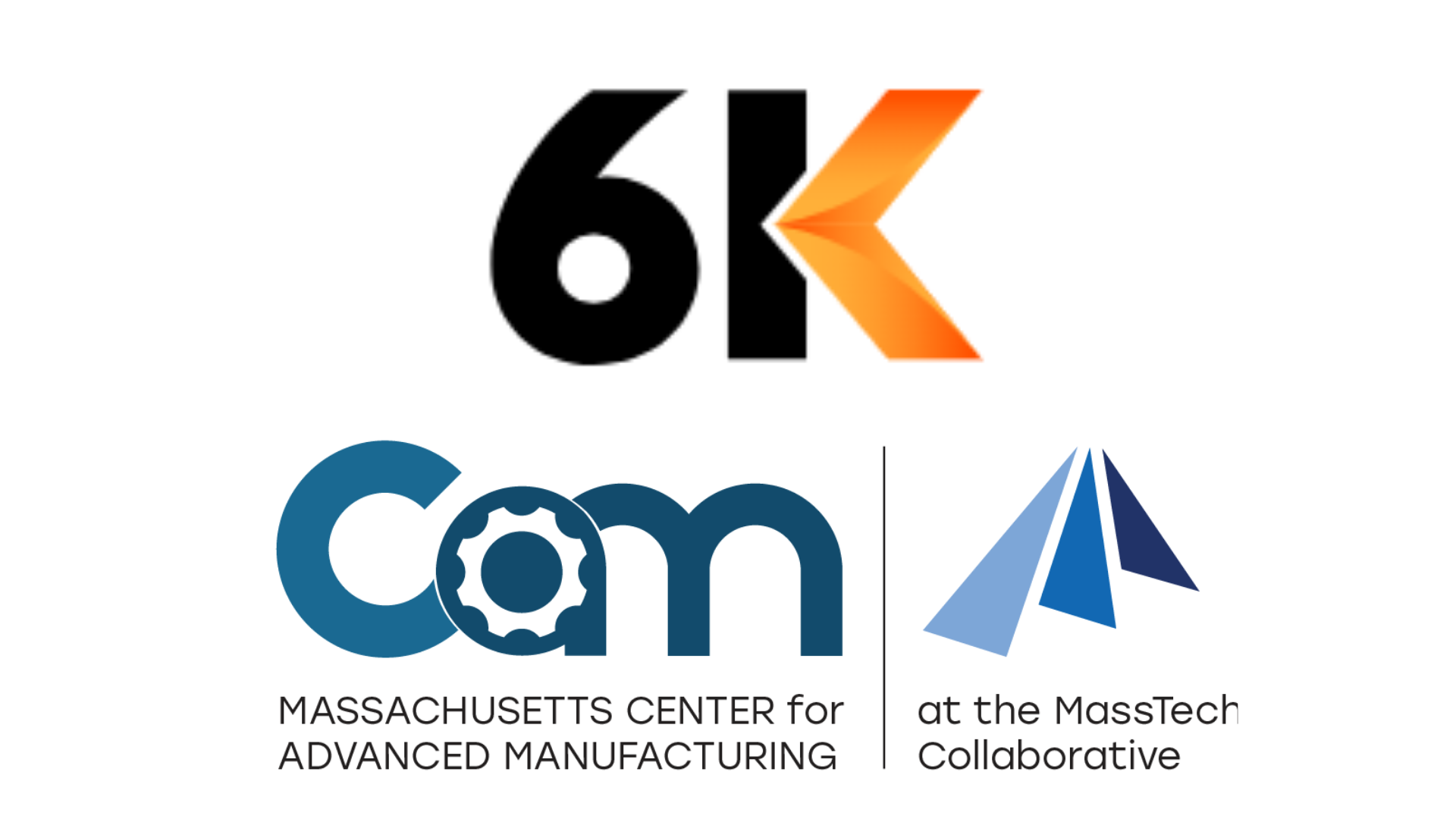
Using math and science, industrial engineers help companies achieve higher levels of efficiency in production processes. They are able identify weaknesses in systems and develop solutions that improve productivity and performance. They can also create processes that require less resources. If you enjoy working with others and are independent, this career is appealing. It allows you to progress in your career and make the transition into management.
There are many industries that industrial engineers can work in. For example, they might work in hazardous materials or at high temperatures. They may have to travel to various locations in order for their work to be completed. They may also be required to communicate via email, telephone and face-to–face to resolve problems. They will also need to be familiar with workplace safety laws and procedures.
Industrial engineers are highly valued because they are able to come up with creative solutions to problems. Many industrial engineers also love solving problems that improve efficiency. In order to improve productivity and reduce costs, industrial engineers may be required to redesign production lines. They may also have to work overtime to meet deadlines. They might also be able to work with other engineers in the design of new production processes.
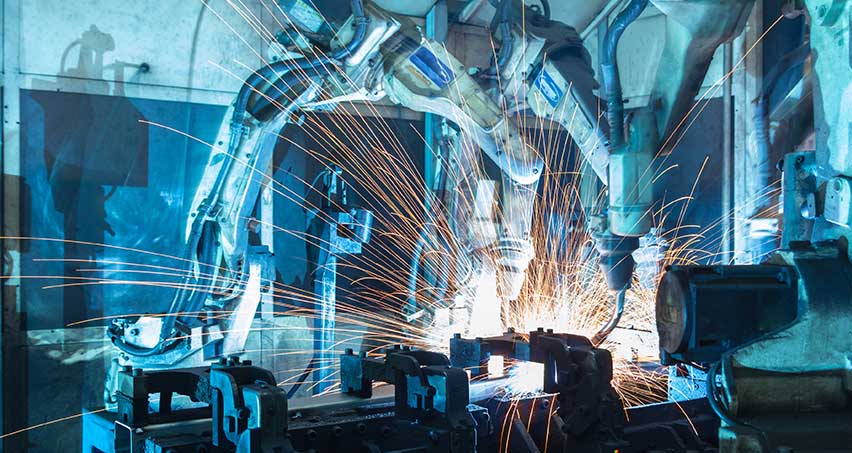
Industrial engineers are expected to have strong interpersonal skills, including the ability to listen and understand what others are saying. They need to be able communicate effectively with colleagues and their supervisors. They must also be able to use their critical thinking skills to identify and assess alternative solutions to a problem. They are also able predict the impact of changes and take steps to increase their chances.
Depending upon their job duties, industrial engineer may have to work in noisy areas, work long hours and travel to different places. Sometimes, they may have trouble balancing work and family life. Although this can be challenging, there are ways to adjust to the demands placed on them by their job.
A bachelor's degree is usually required for industrial engineers. You can then go on to earn a master's, or doctorate. It can take anywhere from two to seven years for this degree program. It is important to select a degree program that is suited for your needs. There are many higher education institutions that offer an online degree program in industrial engineering. These programs are convenient and allow students to complete their studies without incurring high tuition costs. These programs also allow for flexibility in terms of study time.
Industrial engineers might find it useful to join professional organizations such as the Institute of Industrial and Systems Engineers. This organization supports industrial engineers by organizing conferences, publishing white papers, case studies and supporting them. The organization also offers fellowships to recent graduates. They may also be eligible for MOOCs and certifications. They could also apply for fellowships with the American Society for Engineering Education.
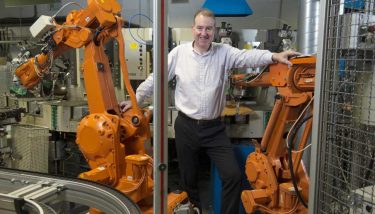
Industrial engineers can also find employment with government agencies. They may be required to obtain licensure. Some large companies may provide formal training. Employers value industrial engineers' experience.
FAQ
What jobs are available in logistics?
There are many types of jobs in logistics. These are some of the jobs available in logistics:
-
Warehouse workers – They load, unload and transport pallets and trucks.
-
Transportation drivers – They drive trucks or trailers to transport goods and perform pick-ups.
-
Freight handlers – They sort and package freight at warehouses.
-
Inventory managers – These people oversee inventory at warehouses.
-
Sales reps are people who sell products to customers.
-
Logistics coordinators - They organize and plan logistics operations.
-
Purchasing agents are those who purchase goods and services for the company.
-
Customer service representatives - Answer calls and email from customers.
-
Shippers clerks - They process shipping order and issue bills.
-
Order fillers are people who fill orders based only on what was ordered.
-
Quality control inspectors - They check incoming and outgoing products for defects.
-
Others - There are many other types of jobs available in logistics, such as transportation supervisors, cargo specialists, etc.
What are the responsibilities of a manufacturing manager
A manufacturing manager must make sure that all manufacturing processes run smoothly and effectively. They must also be alert to any potential problems and take appropriate action.
They should also know how to communicate with other departments such as sales and marketing.
They should also be aware of the latest trends in their industry and be able to use this information to help improve productivity and efficiency.
What are the four types of manufacturing?
Manufacturing is the process of transforming raw materials into useful products using machines and processes. Manufacturing involves many activities, including designing, building, testing and packaging, shipping, selling, service, and so on.
What makes a production planner different from a project manger?
The difference between a product planner and project manager is that a planer is typically the one who organizes and plans the entire project. A production planner, however, is mostly involved in the planning stages.
What is the responsibility of a logistics manager?
Logistics managers ensure that goods arrive on time and are unharmed. This is done using his/her knowledge of the company's products. He/she also needs to ensure adequate stock to meet demand.
How can manufacturing overproduction be reduced?
The key to reducing overproduction lies in developing better ways to manage inventory. This would reduce the time spent on unproductive activities like purchasing, storing and maintaining excess stock. By doing this, we could free up resources for other productive tasks.
Kanban systems are one way to achieve this. A Kanbanboard is a visual tool that allows you to keep track of the work being done. Kanban systems are where work items travel through a series of states until reaching their final destination. Each state represents an individual priority level.
For instance, when work moves from one stage to another, the current task is complete enough to be moved to the next stage. But if a task remains in the beginning stages it will stay that way until it reaches its end.
This allows you to keep work moving along while making sure that no work gets neglected. Managers can see how much work has been done and the status of each task at any time with a Kanban Board. This allows them to adjust their workflows based on real-time information.
Another way to control inventory levels is to implement lean manufacturing. Lean manufacturing emphasizes eliminating waste in all phases of production. Waste includes anything that does not add value to the product. Here are some examples of common types.
-
Overproduction
-
Inventory
-
Packaging that is not necessary
-
Excess materials
By implementing these ideas, manufacturers can improve efficiency and cut costs.
Statistics
- According to a Statista study, U.S. businesses spent $1.63 trillion on logistics in 2019, moving goods from origin to end user through various supply chain network segments. (netsuite.com)
- You can multiply the result by 100 to get the total percent of monthly overhead. (investopedia.com)
- In 2021, an estimated 12.1 million Americans work in the manufacturing sector.6 (investopedia.com)
- Job #1 is delivering the ordered product according to specifications: color, size, brand, and quantity. (netsuite.com)
- In the United States, for example, manufacturing makes up 15% of the economic output. (twi-global.com)
External Links
How To
How to Use Six Sigma in Manufacturing
Six Sigma can be described as "the use of statistical process control (SPC), techniques to achieve continuous improvement." Motorola's Quality Improvement Department in Tokyo, Japan developed Six Sigma in 1986. Six Sigma's basic concept is to improve quality and eliminate defects through standardization. Many companies have adopted this method in recent years. They believe there is no such thing a perfect product or service. Six Sigma's main objective is to reduce variations from the production average. If you take a sample and compare it with the average, you will be able to determine how much of the production process is different from the norm. If this deviation is too big, you know something needs fixing.
Understanding how your business' variability is a key step towards Six Sigma implementation is the first. Once you have this understanding, you will need to identify sources and causes of variation. These variations can also be classified as random or systematic. Random variations are caused when people make mistakes. While systematic variations are caused outside of the process, they can occur. These are, for instance, random variations that occur when widgets are made and some fall off the production line. It would be considered a systematic problem if every widget that you build falls apart at the same location each time.
Once you've identified where the problems lie, you'll want to design solutions to eliminate those problems. This could mean changing your approach or redesigning the entire process. You should then test the changes again after they have been implemented. If they fail, you can go back to the drawing board to come up with a different plan.