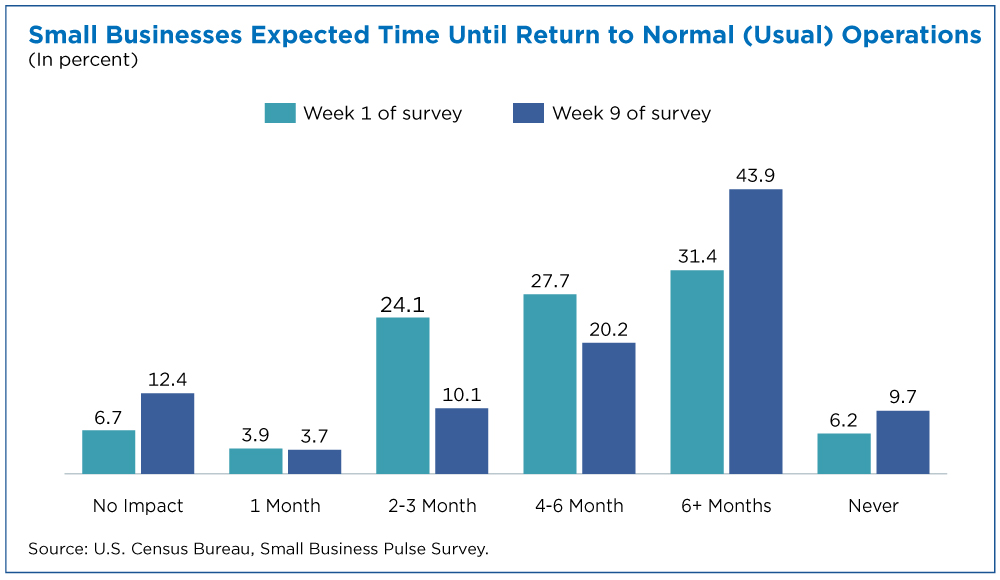
Non-value addition is any activity that does nothing to improve the quality of the product or service that is being made. It may be necessary, useful, or add to the overall value of the finished product. Sharpening the saw is necessary for cutting lumber to the proper size. However, the final product will still be worth more if the saw is sharpened.
Understanding non-value-added activities requires that you first define value. Value is simply the price a customer will pay to get a product/service. This will vary depending on which product or service is being offered. A business' success depends on its ability to add value. It is not possible for a business to succeed if it does not offer value through its products and services. In addition, a business will lose customers.
Ask yourself, "Does this action add value to my product or service?" There are three ways you can answer that question. First, consider the relationship between the action and the final product's value. Another way is to evaluate how the action contributes to customer satisfaction. Last, ask yourself the question "Does it contribute to customer satisfaction?"
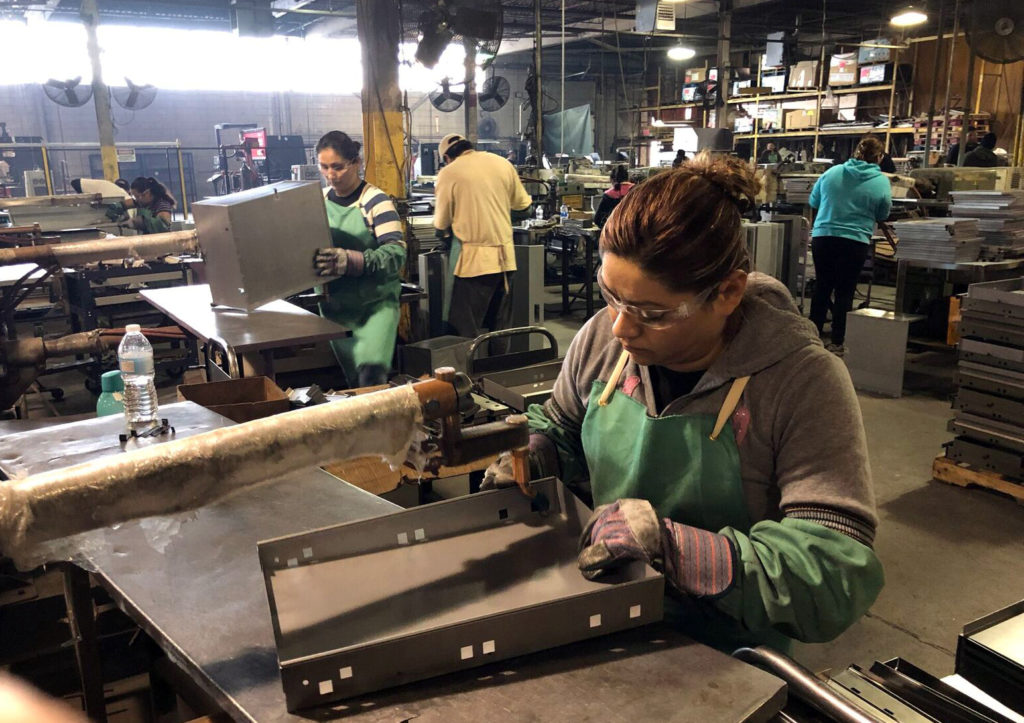
The definition of a value-added activity is one that demonstrates a positive return on investment. Selling merchandise, for instance, is a valuable activity. Selling merchandise is an attractive activity as it can generate a profit for the company. Selling merchandise is an attractive activity because it helps to recover manufacturing costs.
Although it is important that you identify a value-added business activity, this does not guarantee its success. The value-added activity has to be created in a way that meets the customer's expectations. The right process will ensure that the product or service arrives on time and is of high quality. Choosing the wrong process will result in delays or quality issues.
You must first understand the meaning of a non valued activity in order to recognize a value added activity. Non-valued actions are tasks that do nothing to alter the form and function of the product/service. These activities can include inspecting, checking, processing, billing and billing.
Non-valued activity is any activity that does not provide a benefit to the customer or improve their satisfaction. They also consume resources, and can result in expenses. By identifying and eliminating wastes from your process, you can increase speed, quality, as well as service levels. Your cash flow and competitiveness will improve if you take steps to eliminate the waste.
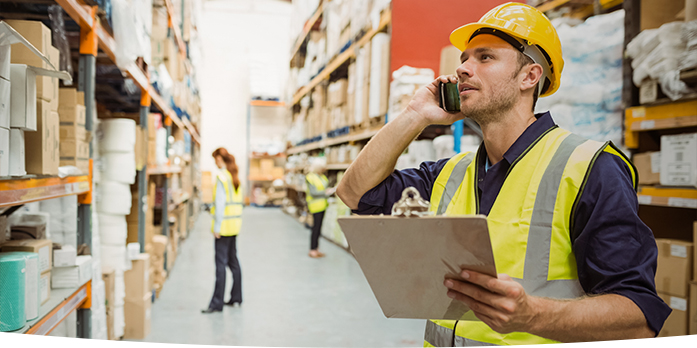
One of the most common mistakes is wasting time on non-value added activities. Waiting, performing inspections, or repairing defective items are all examples of unvalued activities. Moving raw materials, copying documents and filing paperwork are all activities that add no value to the finished product.
A list of processes that add to the product or service can help you determine if your current process has potential to maximize your potential. You can save time, money and resources by breaking down the process.
FAQ
What are the responsibilities for a manufacturing manager
Manufacturing managers must ensure that manufacturing processes are efficient, effective, and cost-effective. They should be aware of any issues within the company and respond accordingly.
They should also be able communicate with other departments, such as sales or marketing.
They should also be aware of the latest trends in their industry and be able to use this information to help improve productivity and efficiency.
How can overproduction in manufacturing be reduced?
Improved inventory management is the key to reducing overproduction. This would reduce the time spent on unproductive activities like purchasing, storing and maintaining excess stock. This could help us free up our time for other productive tasks.
Kanban systems are one way to achieve this. A Kanban Board is a visual display that tracks work progress. A Kanban system allows work items to move through several states before reaching their final destination. Each state has a different priority level.
If work is moving from one stage to the other, then the current task can be completed and moved on to the next. However, if a task is still at the beginning stages, it will remain so until it reaches the end of the process.
This helps to keep work moving forward while ensuring that no work is left behind. Managers can view the Kanban board to see how much work they have done. This information allows managers to adjust their workflow based off real-time data.
Lean manufacturing is another way to manage inventory levels. Lean manufacturing seeks to eliminate waste from every step of the production cycle. Anything that does not contribute to the product's value is considered waste. Here are some examples of common types.
-
Overproduction
-
Inventory
-
Unnecessary packaging
-
Materials in excess
By implementing these ideas, manufacturers can improve efficiency and cut costs.
What are the products and services of logistics?
Logistics is the process of moving goods from one point to another.
They include all aspects associated with transport including packaging, loading transporting, unloading storage, warehousing inventory management customer service, distribution returns and recycling.
Logisticians ensure that products reach the right destination at the right moment and under safe conditions. They assist companies with their supply chain efficiency through information on demand forecasts. Stock levels, production times, and availability.
They keep track and monitor the transit of shipments, maintain quality standards, order replenishment and inventories, coordinate with suppliers, vendors, and provide support for sales and marketing.
What skills do production planners need?
A production planner must be organized, flexible, and able multitask to succeed. It is also important to be able communicate with colleagues and clients.
How important is automation in manufacturing?
Automation is important not only for manufacturers but also for service providers. It allows them to offer services faster and more efficiently. It also helps to reduce costs and improve productivity.
Statistics
- Job #1 is delivering the ordered product according to specifications: color, size, brand, and quantity. (netsuite.com)
- [54][55] These are the top 50 countries by the total value of manufacturing output in US dollars for its noted year according to World Bank.[56] (en.wikipedia.org)
- (2:04) MTO is a production technique wherein products are customized according to customer specifications, and production only starts after an order is received. (oracle.com)
- In 2021, an estimated 12.1 million Americans work in the manufacturing sector.6 (investopedia.com)
- According to a Statista study, U.S. businesses spent $1.63 trillion on logistics in 2019, moving goods from origin to end user through various supply chain network segments. (netsuite.com)
External Links
How To
Six Sigma and Manufacturing
Six Sigma is "the application statistical process control (SPC), techniques for continuous improvement." It was developed by Motorola's Quality Improvement Department at their plant in Tokyo, Japan, in 1986. The basic idea behind Six Sigma is to improve quality by improving processes through standardization and eliminating defects. Since there are no perfect products, or services, this approach has been adopted by many companies over the years. Six Sigma seeks to reduce variation between the mean production value. This means that you can take a sample from your product and then compare its performance to the average to find out how often the process differs from the norm. If there is a significant deviation from the norm, you will know that something needs to change.
Understanding how variability works in your company is the first step to Six Sigma. Once you have this understanding, you will need to identify sources and causes of variation. You'll also want to determine whether these variations are random or systematic. Random variations happen when people make errors; systematic variations are caused externally. These are, for instance, random variations that occur when widgets are made and some fall off the production line. However, if you notice that every time you assemble a widget, it always falls apart at exactly the same place, then that would be a systematic problem.
Once you have identified the problem, you can design solutions. It might mean changing the way you do business or redesigning it entirely. To verify that the changes have worked, you need to test them again. If they don't work, you will need to go back to the drawing boards and create a new plan.