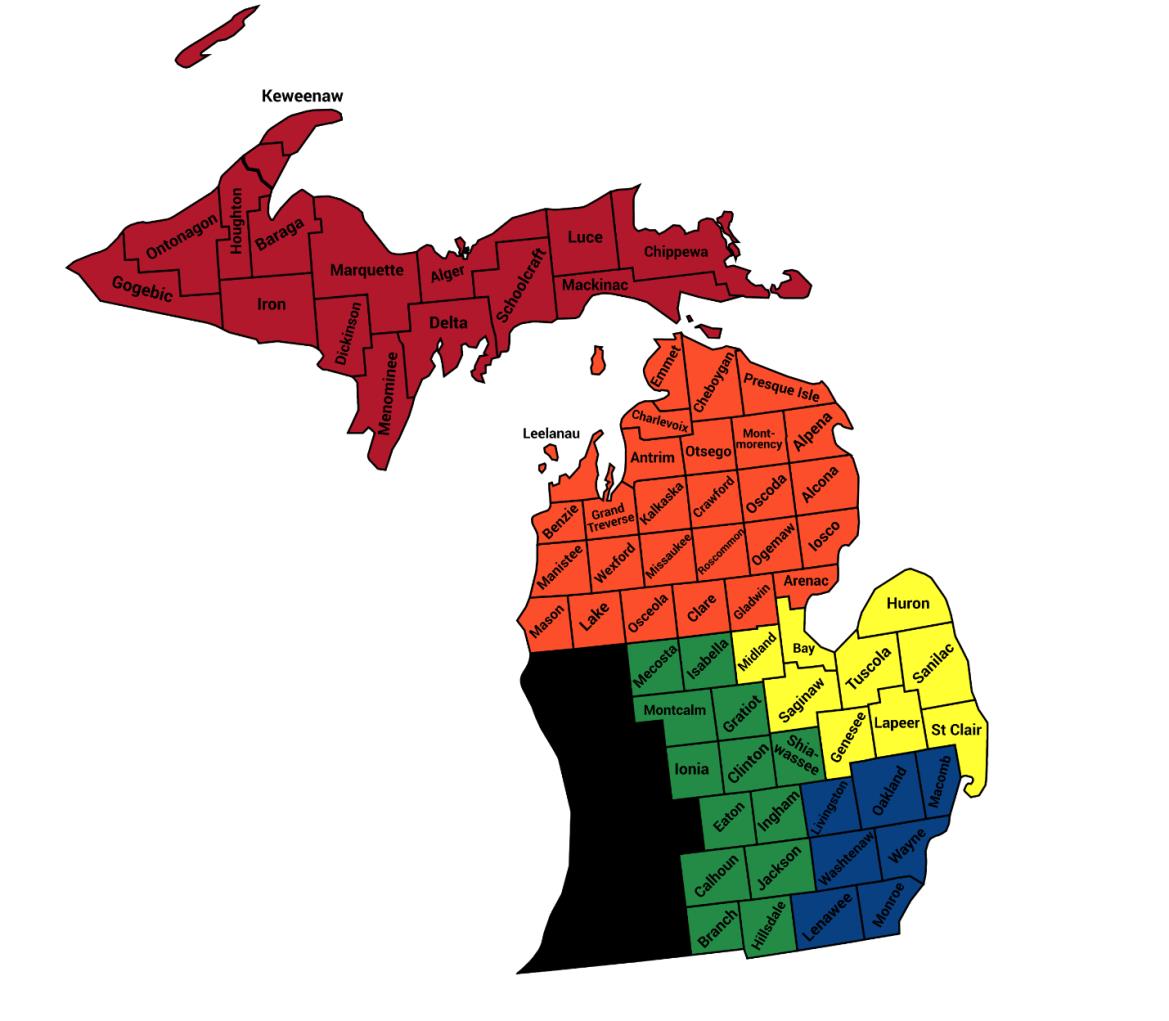
A variety of factors can cause supply chain disruptions. Natural disasters can cause supply chain disruptions. These interruptions can result in price increases and margin reductions. In order to continue production, some companies may have to modify their sourcing strategy. In many cases, companies will need to re-evaluate their supply networks, diversify their production, and audit their current inventories to prepare for the next disruption.
Supply chain disruptions have been experienced in many industries including electronics, pharmaceuticals, and transportation. Sometimes, disruptions occurred due to internal problems at a company. But in other cases, it was caused as a result of a global emergency. One example is a pandemic that caused widespread health disruptions across several countries. It also had an impact on the retail industry. It forced governments to implement policies to stop the spread.
A pandemic could affect the workforce, distribution and manufacturing processes of a company. This could affect production of important products. Companies will need adjust their production lines and supply chains to adapt. The impact of a disruption can vary depending on its severity. Businesses will need a re-evaluation of their inventory in the event of a pandemic. Capital can be reallocated if needed.
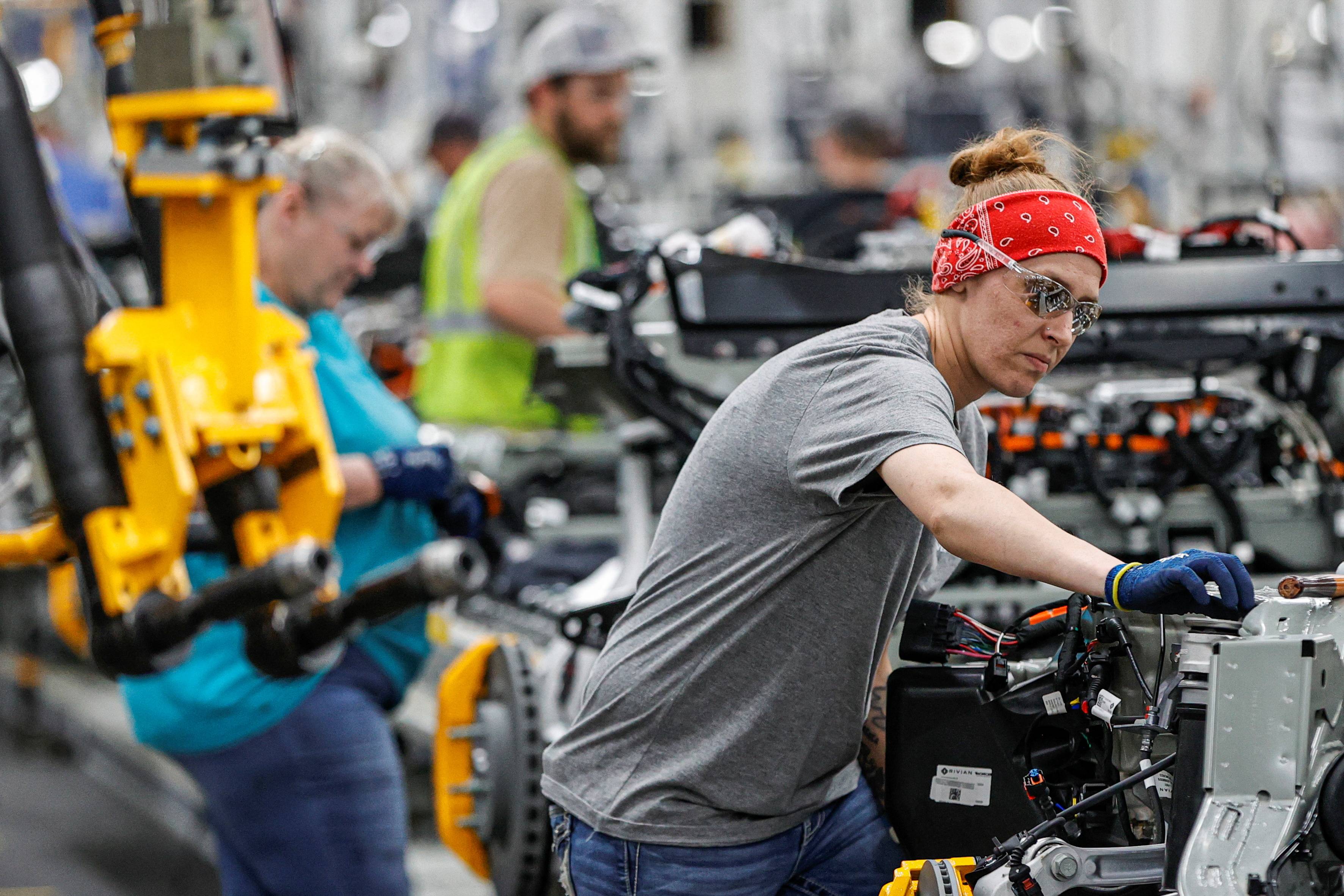
Supply chain disruption can happen at any point in the supply chain. It can happen in both supply and demand. Most often, disruptions will affect the supply side more than the demand side. But if the supply side is affected by a pandemic, it will have a ripple effect on the entire economy.
Supply chain disruptions can have major consequences for a company and are often hard to predict. While it is easy to identify seasonal fluctuations, it is more challenging to predict a rapid shift in consumer behavior. To identify potential problems, predictive analytics tools are a good way to reduce these risks.
A labor shortage is another common source of disruption in the supply chain. If they cannot get equipment or parts from reliable suppliers, companies can lose productivity. The entire operation can be disrupted if a machine breaks down.
Natural disasters as well as market fluctuations and geopolitical instabilities are three of the most frequent causes of disruptions to supply chains. Natural disasters are costly and have the potential to disrupt the global supply network. Another cause of disruption in supply chains is a power outage or telecommunications blackout. Moreover, companies may be forced to store large amounts of stock to protect their business.
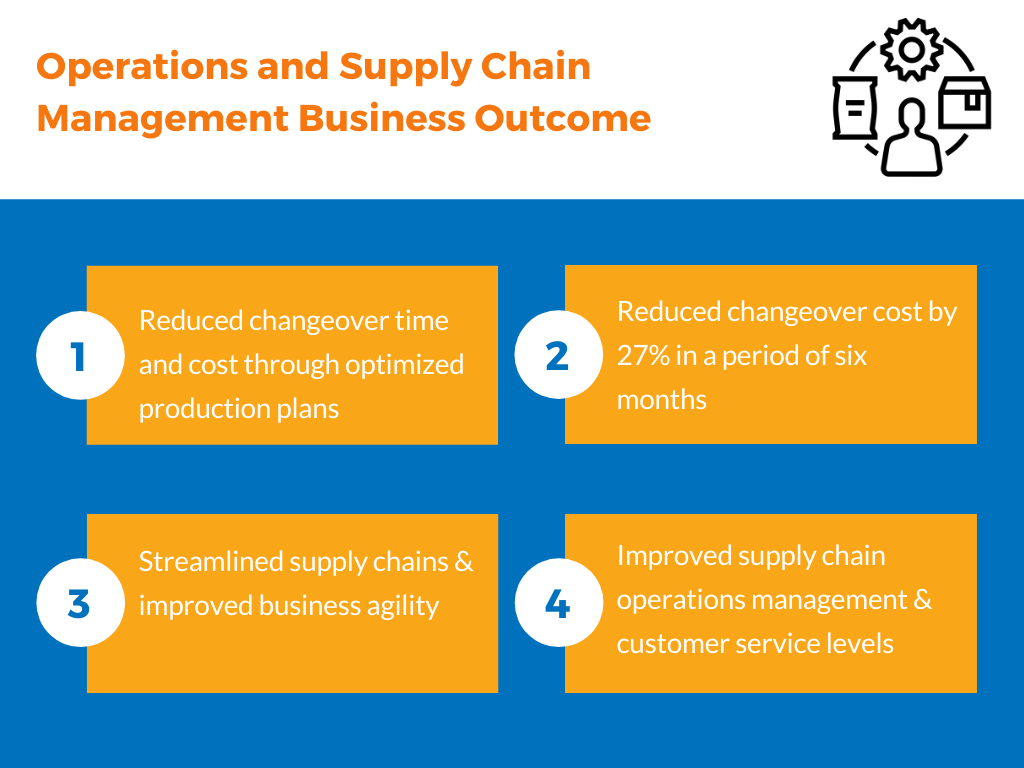
Supply chain disruptions have a relatively low impact, according to general rule. Companies will need action to detect disruptions and most companies will need it at some point. It's important to recognize problems early in order to avoid conflict.
In a recent survey, Ernest & Young LLP found that 72 percent of companies have experienced a disruption at some point, and 57 percent have reported adverse effects. These problems can often be resolved quickly. Others will require a more strategic approach.
FAQ
What is meant by manufacturing industries?
Manufacturing Industries refers to businesses that manufacture products. These products are sold to consumers. This is accomplished by using a variety of processes, including production, distribution and retailing. They make goods from raw materials with machines and other equipment. This includes all types if manufactured goods.
What are the responsibilities of a production planner
A production planner ensures all aspects of the project are delivered on time, within budget, and within scope. They also ensure the quality of the product and service meets the client's requirements.
What is the difference in Production Planning and Scheduling, you ask?
Production Planning (PP) refers to the process of determining how much production is needed at any given moment. Forecasting and identifying production capacity are two key elements to this process.
Scheduling involves the assignment of dates and times to tasks in order to complete them within the timeframe.
What are manufacturing & logistics?
Manufacturing is the process of creating goods from raw materials by using machines and processes. Logistics encompasses the management of all aspects associated with supply chain activities such as procurement, production planning, distribution and inventory control. It also includes customer service. Manufacturing and logistics are often considered together as a broader term that encompasses both the process of creating products and delivering them to customers.
What are the 7 Rs of logistics?
The acronym 7Rs of Logistics refers to the seven core principles of logistics management. It was published in 2004 by the International Association of Business Logisticians as part of their "Seven Principles of Logistics Management" series.
The acronym is made up of the following letters:
-
Responsible - ensure that all actions taken are within legal requirements and are not harmful to others.
-
Reliable – have faith in your ability and capability to keep promises.
-
It is reasonable to use resources efficiently and not waste them.
-
Realistic – consider all aspects of operations, from cost-effectiveness to environmental impact.
-
Respectful - show respect and treat others fairly and fairly
-
Resourceful - look for opportunities to save money and increase productivity.
-
Recognizable - Provide value-added services to customers
Statistics
- According to a Statista study, U.S. businesses spent $1.63 trillion on logistics in 2019, moving goods from origin to end user through various supply chain network segments. (netsuite.com)
- [54][55] These are the top 50 countries by the total value of manufacturing output in US dollars for its noted year according to World Bank.[56] (en.wikipedia.org)
- In 2021, an estimated 12.1 million Americans work in the manufacturing sector.6 (investopedia.com)
- Many factories witnessed a 30% increase in output due to the shift to electric motors. (en.wikipedia.org)
- You can multiply the result by 100 to get the total percent of monthly overhead. (investopedia.com)
External Links
How To
How to Use Lean Manufacturing for the Production of Goods
Lean manufacturing is a management style that aims to increase efficiency and reduce waste through continuous improvement. It was developed by Taiichi Okono in Japan, during the 1970s & 1980s. TPS founder Kanji Takoda awarded him the Toyota Production System Award (TPS). Michael L. Watkins published the "The Machine That Changed the World", the first book about lean manufacturing. It was published in 1990.
Lean manufacturing can be described as a set or principles that are used to improve quality, speed and cost of products or services. It emphasizes eliminating waste and defects throughout the value stream. The five-steps of Lean Manufacturing are just-in time (JIT), zero defect and total productive maintenance (TPM), as well as 5S. Lean manufacturing is about eliminating activities that do not add value, such as inspection, rework, and waiting.
Lean manufacturing can help companies improve their product quality and reduce costs. Additionally, it helps them achieve their goals more quickly and reduces employee turnover. Lean manufacturing has been deemed one of the best ways to manage the entire value-chain, including customers, distributors as well retailers and employees. Many industries worldwide use lean manufacturing. Toyota's philosophy has been a key driver of success in many industries, including automobiles and electronics.
Five basic principles of Lean Manufacturing are included in lean manufacturing
-
Define value - Find out what your business contributes to society, and what makes it different from other competitors.
-
Reduce Waste – Eliminate all activities that don't add value throughout the supply chain.
-
Create Flow – Ensure that work flows smoothly throughout the process.
-
Standardize & Simplify - Make processes as consistent and repeatable as possible.
-
Develop Relationships: Establish personal relationships both with internal and external stakeholders.
Lean manufacturing, although not new, has seen renewed interest in the economic sector since 2008. To increase their competitiveness, many businesses have turned to lean manufacturing. Economists think that lean manufacturing is a crucial factor in economic recovery.
Lean manufacturing has many benefits in the automotive sector. These benefits include increased customer satisfaction, reduced inventory levels and lower operating costs.
Any aspect of an enterprise can benefit from Lean manufacturing. This is because it ensures efficiency and effectiveness in all stages of the value chain.
There are three main types of lean manufacturing:
-
Just-in Time Manufacturing, (JIT): This kind of lean manufacturing is also commonly known as "pull-systems." JIT means that components are assembled at the time of use and not manufactured in advance. This strategy aims to decrease lead times, increase availability of parts and reduce inventory.
-
Zero Defects Manufacturing - ZDM: ZDM focuses its efforts on making sure that no defective units leave a manufacturing facility. If a part needs to be fixed during the assembly line, it should be repaired rather than scrapped. This applies to finished goods that may require minor repairs before shipment.
-
Continuous Improvement (CI): CI aims to improve the efficiency of operations by continuously identifying problems and making changes in order to eliminate or minimize waste. It involves continuous improvement of processes, people, and tools.