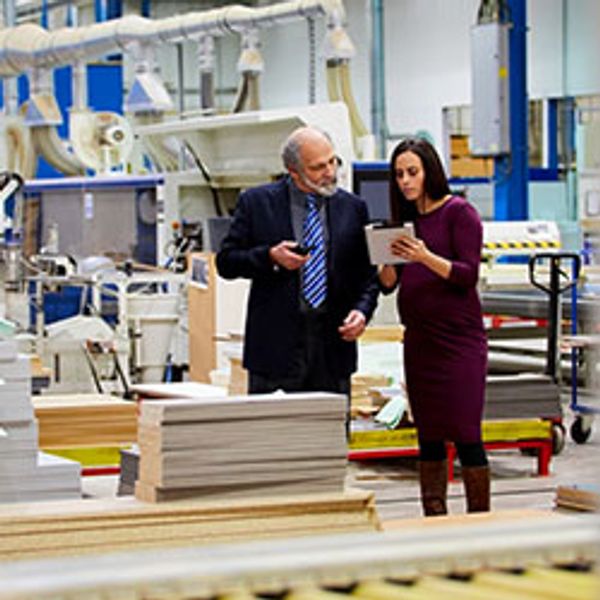
Using a single piece flow production line can increase your output while reducing your inventory and lead times. Before you start using this technology, here are some things to keep in mind. It is important to determine the takt times, which refers to the time it takes for an item to be produced. This allows you calculate the time it takes to make an item so that you can meet customer demand.
One piece flow is best suited to manufacturing operations that are geared towards low-variability products. However, this is not the best option for every business. You need to be sure you're measuring the right metrics so that you can determine if this is the right process for your company.
Choosing to use a single piece flow will also require a more robust and scalable control system. This will help reduce waste and maximize efficiency. You should also ensure that the time needed to produce a single-piece item is sufficient to meet the requirements of your customers. This will ensure that the efficiencies associated with one-piece flow don't lag behind those of a more traditional production process.
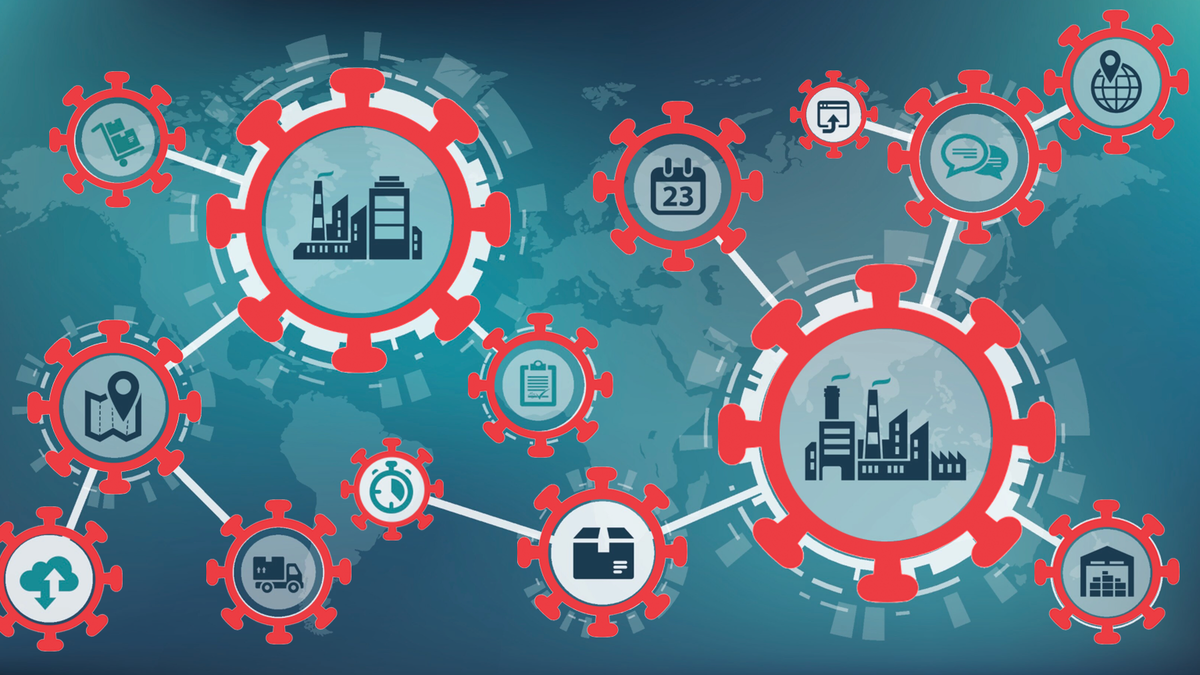
The one piece flow process entails using a production line that looks like a U or S shape. It will allow for less movement from one step to the next. It also increases assembly efficiency.
Poka-yoke is another term associated with lean. This clever method prevents defects from being moved to the next stage. This is an excellent way to save time while improving the quality and value of your products. The poka yoke is also a great way to reduce waste, inefficiency, and cost.
If there is a high demand of individual products, one-piece flow works well. You want to save time and money in this situation by not having to order multiple items at once. The cost of depreciation and delay will be reduced by having one work item flow. This will reduce the time that your products are in storage or in work-in-progress (WIP) mode.
You can also use a single piece flow process to reduce the costs of maintaining your inventory. This is especially important for small businesses. This will help you save money on storage, transport, and re-packaging. This is a great way of reducing the time it takes your customers to receive products.
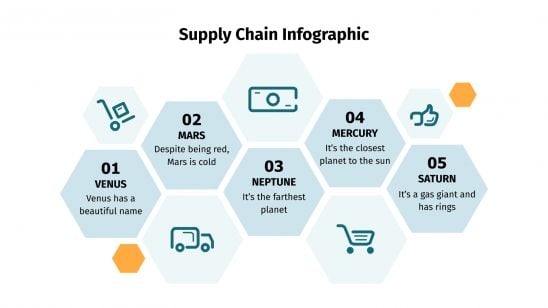
One-piece flow allows employees to work more closely together and helps improve employee morale. It makes it easier to identify any problems with your product. This is crucial because customers could be sent items that are not complete or defective. This is also an excellent way to improve customer service.
One-piece flow production lines can be used inside or outside an assembly line. This type of process is ideal for optimizing your value stream. This type of process also allows for faster production and high quality products. It's also a great way to cut costs and boost morale among employees.
FAQ
What skills are required to be a production manager?
To become a successful production planner, you need to be organized, flexible, and able to multitask. It is also important to be able communicate with colleagues and clients.
What is the difference between manufacturing and logistics
Manufacturing refers to the process of making goods using raw materials and machines. Logistics includes all aspects related to supply chain management, such as procurement, distribution planning, inventory control and transportation. As a broad term, manufacturing and logistics often refer to both the creation and delivery of products.
What type of jobs is there in logistics
There are many kinds of jobs available within logistics. Here are some:
-
Warehouse workers - They load trucks and pallets.
-
Transport drivers - These are people who drive trucks and trailers to transport goods or perform pick-ups.
-
Freight handlers are people who sort and pack freight into warehouses.
-
Inventory managers – They manage the inventory in warehouses.
-
Sales reps are people who sell products to customers.
-
Logistics coordinators – They plan and coordinate logistics operations.
-
Purchasing agents - They purchase goods and services needed for company operations.
-
Customer service representatives are available to answer customer calls and emails.
-
Shipping clerks - They process shipping orders and issue bills.
-
Order fillers - They fill orders based on what is ordered and shipped.
-
Quality control inspectors - They check incoming and outgoing products for defects.
-
Others – There are many other types available in logistics. They include transport supervisors, cargo specialists and others.
How can we reduce manufacturing overproduction?
Better inventory management is key to reducing excess production. This would reduce the amount of time spent on unnecessary activities such as purchasing, storing, and maintaining excess stock. This could help us free up our time for other productive tasks.
This can be done by using a Kanban system. A Kanban board, a visual display to show the progress of work, is called a Kanban board. In a Kanban system, work items move through a sequence of states until they reach their final destination. Each state represents a different priority level.
As an example, if work is progressing from one stage of the process to another, then the current task is complete and can be transferred to the next. But if a task remains in the beginning stages it will stay that way until it reaches its end.
This helps to keep work moving forward while ensuring that no work is left behind. Managers can view the Kanban board to see how much work they have done. This allows them to adjust their workflows based on real-time information.
Lean manufacturing is another option to control inventory levels. Lean manufacturing focuses on eliminating waste throughout the entire production chain. Any product that isn't adding value can be considered waste. The following are examples of common waste types:
-
Overproduction
-
Inventory
-
Packaging that is not necessary
-
Overstock materials
Manufacturers can increase efficiency and decrease costs by implementing these ideas.
Why automate your factory?
Automation has become increasingly important in modern warehousing. The rise of e-commerce has led to increased demand for faster delivery times and more efficient processes.
Warehouses must adapt quickly to meet changing customer needs. To do so, they must invest heavily in technology. Automation warehouses can bring many benefits. These are some of the benefits that automation can bring to warehouses:
-
Increases throughput/productivity
-
Reduces errors
-
Accuracy is improved
-
Safety enhancements
-
Eliminates bottlenecks
-
Companies can scale up more easily
-
Makes workers more efficient
-
The warehouse can be viewed from all angles.
-
Enhances customer experience
-
Improves employee satisfaction
-
This reduces downtime while increasing uptime
-
Ensures quality products are delivered on time
-
Removing human error
-
This helps to ensure compliance with regulations
Is there anything we should know about Manufacturing Processes prior to learning about Logistics.
No. No. It is important to know about the manufacturing processes in order to understand how logistics works.
Statistics
- According to the United Nations Industrial Development Organization (UNIDO), China is the top manufacturer worldwide by 2019 output, producing 28.7% of the total global manufacturing output, followed by the United States, Japan, Germany, and India.[52][53] (en.wikipedia.org)
- According to a Statista study, U.S. businesses spent $1.63 trillion on logistics in 2019, moving goods from origin to end user through various supply chain network segments. (netsuite.com)
- You can multiply the result by 100 to get the total percent of monthly overhead. (investopedia.com)
- In 2021, an estimated 12.1 million Americans work in the manufacturing sector.6 (investopedia.com)
- In the United States, for example, manufacturing makes up 15% of the economic output. (twi-global.com)
External Links
How To
Six Sigma: How to Use it in Manufacturing
Six Sigma is "the application statistical process control (SPC), techniques for continuous improvement." Motorola's Quality Improvement Department in Tokyo, Japan developed Six Sigma in 1986. Six Sigma's main goal is to improve process quality by standardizing processes and eliminating defects. Many companies have adopted Six Sigma in recent years because they believe that there are no perfect products and services. Six Sigma's primary goal is to reduce variation from the average value of production. This means that you can take a sample from your product and then compare its performance to the average to find out how often the process differs from the norm. If the deviation is excessive, it's likely that something needs to be fixed.
Understanding the dynamics of variability within your business is the first step in Six Sigma. Once you've understood that, you'll want to identify sources of variation. You'll also want to determine whether these variations are random or systematic. Random variations are caused when people make mistakes. While systematic variations are caused outside of the process, they can occur. If you make widgets and some of them end up on the assembly line, then those are considered random variations. However, if you notice that every time you assemble a widget, it always falls apart at exactly the same place, then that would be a systematic problem.
Once you've identified the problem areas you need to find solutions. The solution could involve changing how you do things, or redesigning your entire process. You should then test the changes again after they have been implemented. If they didn't work, then you'll need to go back to the drawing board and come up with another plan.