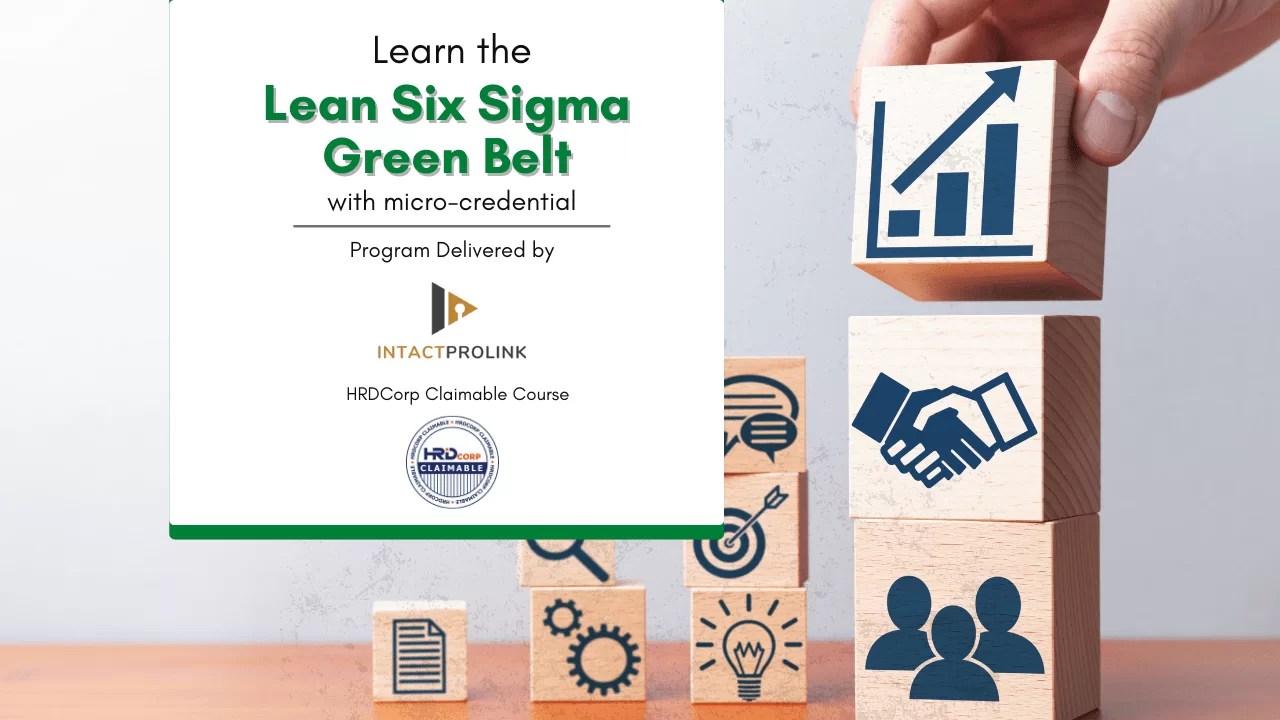
What is supply-chain management? Supply chain management is a cross-functional process that manages relationships across the entire supply chain. By improving operations and financial performance, supply chain management improves overall business performance. This article will discuss the basics of supply chains management and how it can enhance your organization. Let's get started! What is supply management? Why is supply chain management important? Here are some examples of how it could benefit your company.
Management of supply chain relationships is the goal of supply chain management
When selling products, companies need to know how to source raw materials and produce parts. The physical flow or goods is created by suppliers and then goes through different steps to reach a manufacturer, distributor and retailer before reaching the end consumer. Some supply chains skip certain steps. However, the physical items must move from one point to the other, be stored for some time, then be delivered at the end customer. This is a process that requires organization and planning.
Successful supply chain management requires integrating all business functions. For example, suppliers and vendors need clear communication. Information sharing allows both sides to understand each other's expectations, reduce costs, improve quality, and helps them communicate clearly. Collaboration improves communication across the supply chains and helps both parties. The vendor should have a clear understanding of how the vendor will deliver emergency materials. Customers must also be informed about their company's operating procedures. If a company sells perishable products, it is particularly important to know the lead times.
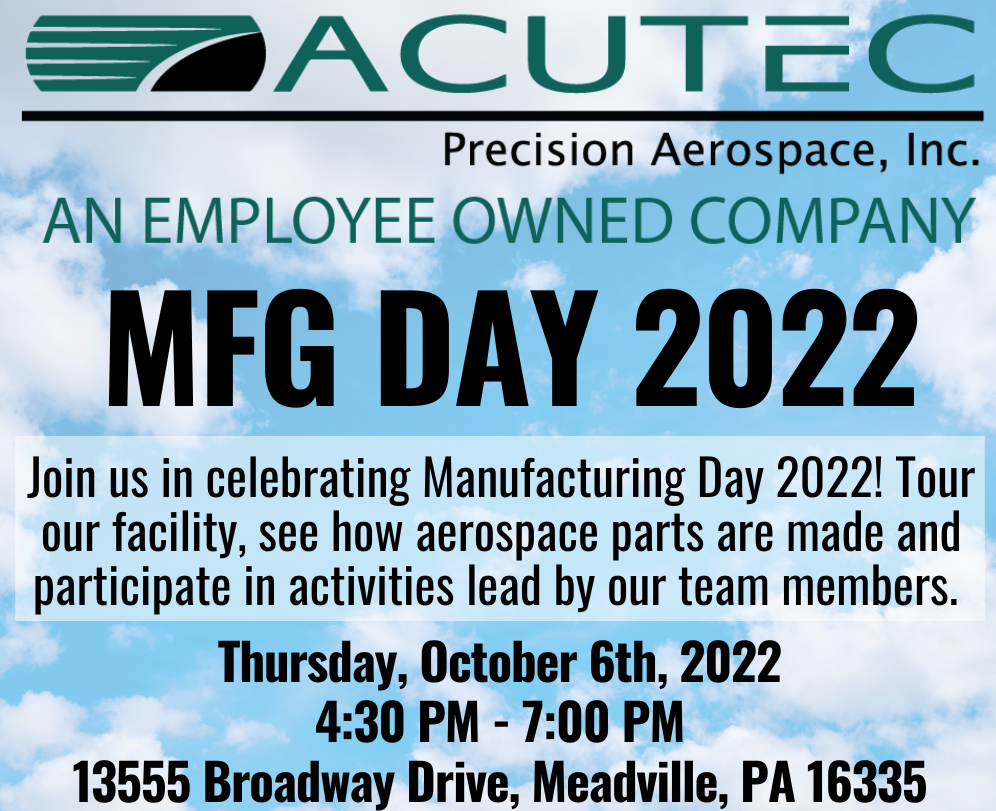
It's a cross-functional business process
Many factors are important to consider when it comes down to a company’s supply chain. For a supply chain to be successful, suppliers need to be able delivery goods on time. That is why it is so important to coordinate. Follow these steps to avoid any problems. This will increase efficiency and help companies save money.
Management must understand the interdependencies within the supply chain and work towards increasing profitability. It is crucial to create guidelines that will allow everyone to reap the benefits from improved processes. Sometimes, the improvement of the process may not be visible to all parties. If the value is not captured, it might be deemed ineffective.
It reduces operating and maintenance costs
One of the most effective ways to reduce operating costs is by streamlining your ordering processes. Your employees will be more likely to use one software system for all requisitions. You can also reduce your operating expenses by setting up an approvals procedure to limit how many goods you order. A streamlined software system can help you avoid confusion and errors, monitor your inventory and order only what you need. It will also allow you to stop shipments being made if you are not required.
Another method to reduce operating costs is by improving communication between warehouse employees. This process should start with examining the current workflow and identify any bottlenecks that are making the process inefficient. Consolidating or using dedicated transport services can help reduce transportation costs. Operating costs will drop dramatically if you can do this. This will help you not only lower your transport costs but also speed up the delivery of your products.
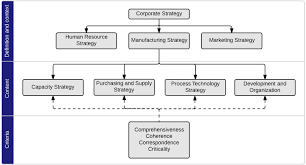
It improves financial position
The financial performance of a company can be improved in several ways by good supply chain management. Effective supply chain managers can reduce the cost of production while maximizing the benefits of variable costs. Increased profit margins are possible when costs can be controlled. Another benefit is the improvement of cash flow. A faster delivery of products to the customer can help it invoice its customers earlier, reducing the need to purchase expensive building space. Additionally, a better supply network reduces the costs of fixed assets.
The Statement of Shareholders' Equity (SSE) is a key financial statement that summarizes the ownership portion of a company. The after-tax cash flow can be increased by about 8.5% by improving a firm's supplier chain. By improving supply chain performance, a company can reduce its costs by as much as 10%, while increasing its customer satisfaction. A company that improves its supply chain management can reduce costs by as much as 10% while increasing customer satisfaction. This will lead to higher operational efficiencies and consequently, greater profits.
FAQ
What do we need to know about Manufacturing Processes in order to learn more about Logistics?
No. No. However, knowing about manufacturing processes will definitely give you a better understanding of how logistics works.
How can I learn about manufacturing?
Hands-on experience is the best way to learn more about manufacturing. You can read books, or watch instructional videos if you don't have the opportunity to do so.
What is the role and responsibility of a Production Planner?
Production planners ensure that all project aspects are completed on time, within budget and within the scope. They ensure that the product or service is of high quality and meets client requirements.
What is production plan?
Production Planning involves developing a plan for all aspects of the production, including scheduling, budgeting, casting, crew, location, equipment, props, etc. It is important to have everything ready and planned before you start shooting. It should also contain information on achieving the best results on set. This includes location information, crew details, equipment specifications, and casting lists.
The first step in filming is to define what you want. You may already know where you want the film to be shot, or perhaps you have specific locations and sets you wish to use. Once you have identified the scenes and locations, you can start to determine which elements are required for each scene. For example, you might decide that you need a car but don't know exactly what model you want. To narrow your options, you can search online for available models.
After you've found the perfect car, it's time to start thinking about adding extras. Do you have people who need to be seated in the front seat? You might also need someone to help you get around the back. Maybe you want to change the interior color from black to white? These questions will help to determine the style and feel of your car. Another thing you can do is think about what type of shots are desired. Are you going to be shooting close-ups? Or wide angles? Maybe the engine or steering wheel is what you are looking to film. These factors will help you determine which car style you want to film.
Once you have established all the details, you can create a schedule. You can create a schedule that will outline when you must start and finish your shoots. The schedule will show you when to get there, what time to leave, and when to return home. Everyone will know what they need and when. Hire extra staff by booking them ahead of time. You should not hire anyone who doesn't show up because of your inaction.
You will need to factor in the days that you have to film when creating your schedule. Some projects take only a few days while others can last several weeks. It is important to consider whether you require more than one photo per day when you create your schedule. Multiplying takes in the same area will result both in increased costs and a longer time. It's better to be safe than sorry and shoot less takes if you're not certain whether you need more takes.
Budget setting is another important aspect in production planning. You will be able to manage your resources if you have a realistic budget. You can always lower the budget if you encounter unexpected problems. But, don't underestimate how much money you'll spend. If you underestimate the cost of something, you will have less money left after paying for other items.
Production planning is a complicated process. But once you understand how everything works together, it becomes much easier to plan future project.
What is the role of a logistics manager
Logistics managers are responsible for ensuring that all goods arrive in perfect condition and on time. This is done by using his/her experience and knowledge of the company's products. He/she should also ensure enough stock is available to meet demand.
Statistics
- You can multiply the result by 100 to get the total percent of monthly overhead. (investopedia.com)
- In 2021, an estimated 12.1 million Americans work in the manufacturing sector.6 (investopedia.com)
- (2:04) MTO is a production technique wherein products are customized according to customer specifications, and production only starts after an order is received. (oracle.com)
- [54][55] These are the top 50 countries by the total value of manufacturing output in US dollars for its noted year according to World Bank.[56] (en.wikipedia.org)
- Job #1 is delivering the ordered product according to specifications: color, size, brand, and quantity. (netsuite.com)
External Links
How To
How to use the Just In-Time Production Method
Just-in-time (JIT) is a method that is used to reduce costs and maximize efficiency in business processes. It allows you to get the right amount resources at the right time. This means that your only pay for the resources you actually use. The term was first coined by Frederick Taylor, who developed his theory while working as a foreman in the early 1900s. Taylor observed that overtime was paid to workers if they were late in working. He realized that workers should have enough time to complete their jobs before they begin work. This would help increase productivity.
JIT is a way to plan ahead and make sure you don't waste any money. Look at your entire project, from start to end. Make sure you have enough resources in place to deal with any unexpected problems. You will have the resources and people to solve any problems you anticipate. This way, you won't end up paying extra money for things that weren't really necessary.
There are different types of JIT methods:
-
Demand-driven JIT: You order the parts and materials you need for your project every other day. This will enable you to keep track of how much material is left after you use it. This will let you know how long it will be to produce more.
-
Inventory-based: This type allows you to stock the materials needed for your projects ahead of time. This allows you to forecast how much you will sell.
-
Project-driven: This method allows you to set aside enough funds for your project. Once you have an idea of how much material you will need, you can purchase the necessary materials.
-
Resource-based JIT : This is probably the most popular type of JIT. You assign certain resources based off demand. For instance, if you have a lot of orders coming in, you'll assign more people to handle them. If you don't receive many orders, then you'll assign fewer employees to handle the load.
-
Cost-based: This is the same as resource-based except that you don't care how many people there are but how much each one of them costs.
-
Price-based: This is similar to cost-based but instead of looking at individual workers' salaries, you look at the total company price.
-
Material-based: This is quite similar to cost-based, but instead of looking at the total cost of the company, you're concerned with how much raw materials you spend on average.
-
Time-based JIT: A variation on resource-based JIT. Instead of focusing on how much each employee costs, you focus on how long it takes to complete the project.
-
Quality-based JIT: Another variation on resource-based JIT. Instead of worrying about the costs of each employee or how long it takes for something to be made, you should think about how quality your product is.
-
Value-based JIT is the newest form of JIT. In this instance, you are not concerned about the product's performance or meeting customer expectations. Instead, you are focused on adding value to the marketplace.
-
Stock-based is an inventory-based system that measures the number of items produced at any given moment. This method is useful when you want to increase production while decreasing inventory.
-
Just-in-time planning (JIT): This is a combination JIT and supply-chain management. It is the process of scheduling components' delivery as soon as they have been ordered. It's important as it reduces leadtimes and increases throughput.