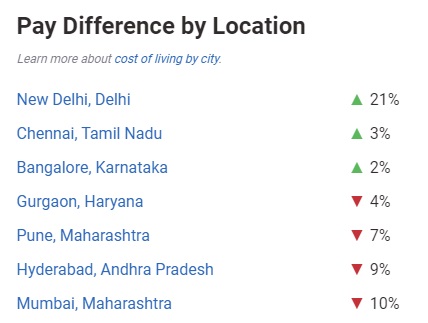
Industrial management is an engineering field where different engineering processes are integrated in order to create a management system. These engineering processes are integrated into an integrated management system by the industrial manager. These are the basics of your job. Below are some benefits and requirements that you must meet to be an industrial manager. This career is for you if your qualifications are up-to-date and you're looking for a rewarding and challenging job. Continue reading to learn about the career.
Job description
An industrial manager supervises the production processes and products. The job can cover every aspect of the production process but will also be responsible for sourcing raw materials and implementing equipment. Computer literacy is essential for industrial production managers, who must be able to use computers to coordinate the work of different departments, suppliers, clients, and other parties. In addition, industrial production managers must be well-versed in the latest production technologies and management practices. Many managers take part in professional organizations, attend tradeshows and conferences in the industry, and enroll in courses to earn certification.
Industrial managers coordinate all activities within a company, in addition to supervising production processes. They ensure that production lines are efficient and meet customer requirements in terms of quality and time. They oversee staffing levels and alter production levels when necessary to reduce inventory. They might also coordinate with other departments and oversee quality control programs. Most of this job involves managing people. This includes training, motivating, and identifying employees.
Education is required
Obtaining a bachelor's degree in business administration, management, or engineering is not typically enough to qualify as an industrial manager. Employers will prefer candidates who have a background in one or more of these fields. Computer literacy is also a requirement for industrial managers. Computers are becoming an increasingly important part of manufacturing, helping to coordinate production across departments and suppliers. This field requires that interested people have the required education and work experience.
Many industrial production managers started their careers as production workers before moving up to the first-line supervisory position. Most professionals need to have a college degree or equivalent in business management to be able to move up to the position of industrial manager. However, entry-level workers may still be able obtain this education through their jobs or by taking classes sponsored in part by their companies. However, managers must have two to five year of relevant experience before becoming a manager.
Earning potential
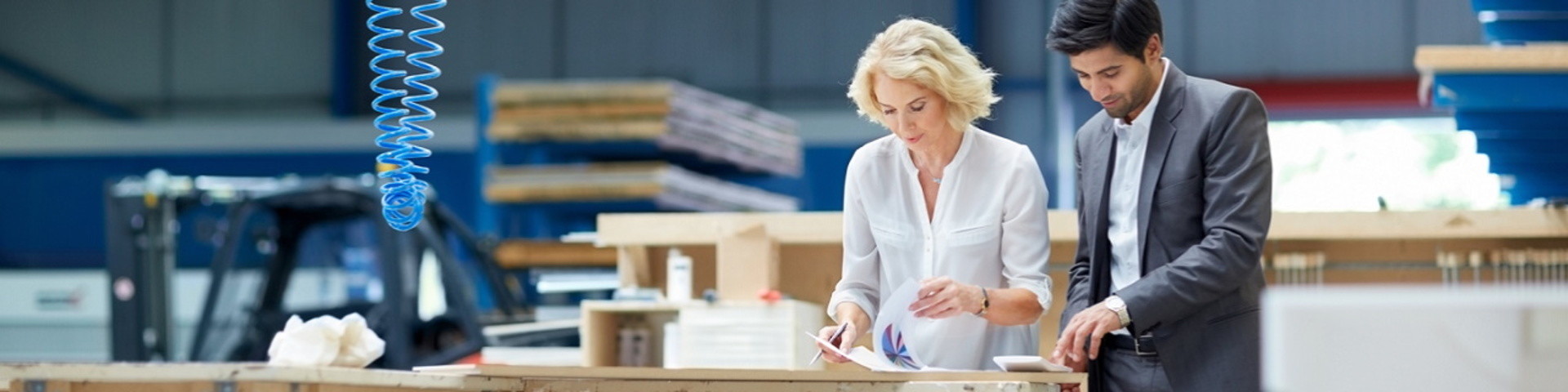
Managers in industrial plants oversee the smooth functioning of the whole process. They help to determine the best use of employees and equipment, establish production standards, and make strategic and tactical decisions. These workers are responsible for the hiring and evaluation of workers, as well as setting production schedules and following safety procedures. They are responsible for overseeing the day-to-day operations of a team and constantly analyzing the production process to ensure it is running efficiently and at peak performance.
The experience and employer of an industrial production manager will determine the potential earnings. It's hard to predict future earnings for industrial managers. The average industrial production manager earned $103,380 annually in May 2016. Also, higher earnings are possible for industrial production managers who have had advanced training and certification. According to U.S. Bureau of Labor Statistics, those who have earned a bachelor’s or higher in industrial production management can earn more.
Work environment
A manager of industrial production divides their time between the production floor or an office. Sometimes, they live in the same building. When working in a manufacturing area, industrial production manager must follow established health and safety protocols and use the proper protective equipment. They also spend significant amounts of time in meetings with subordinates and analyzing production data. These managers may also write reports. A manager of industrial production often works in a dynamic environment.
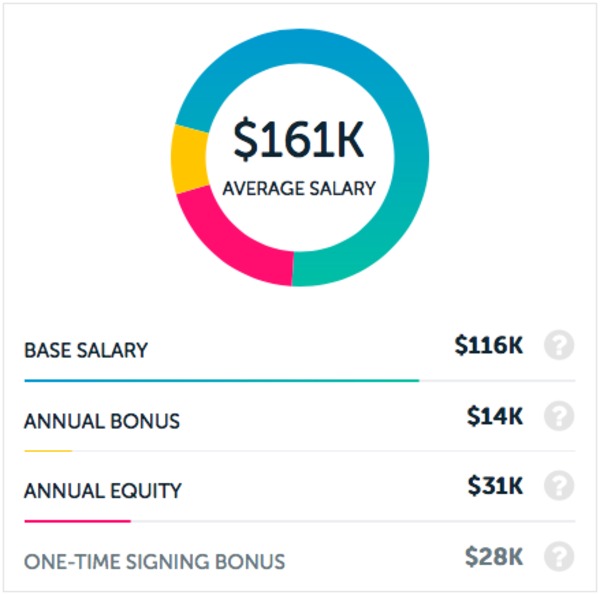
Industrial production managers play a key role in a company's overall management structure. They coordinate the activities and improve productivity of different workers. The primary tasks of an industrial producer manager include increasing productivity and maintaining safety. Due to corporate restructuring, many levels have been eliminated and support staff reduced. Production managers are now able to handle more of the work load. This is a major challenge for any manager and can make the job difficult for a production manger.
FAQ
What are the products and services of logistics?
Logistics are the activities involved in moving goods from point A to point B.
They cover all aspects of transportation, such as packing, loading, transporting and unloading.
Logisticians make sure that the right product arrives at the right place at the correct time and in safe conditions. They assist companies with their supply chain efficiency through information on demand forecasts. Stock levels, production times, and availability.
They can also track shipments in transit and monitor quality standards.
What is the difference in Production Planning and Scheduling, you ask?
Production Planning (PP), or production planning, is the process by which you determine what products are needed at any given time. This is done through forecasting demand and identifying production capacities.
Scheduling refers the process by which tasks are assigned dates so that they can all be completed within the given timeframe.
What can I do to learn more about manufacturing?
Experience is the best way for you to learn about manufacturing. You can also read educational videos or take classes if this isn't possible.
What skills is required for a production planner?
You must be flexible and organized to become a productive production planner. Effective communication with clients and colleagues is essential.
What are the four types in manufacturing?
Manufacturing is the process that transforms raw materials into useful products. Manufacturing can include many activities such as designing and building, testing, packaging shipping, selling, servicing, and other related activities.
Statistics
- (2:04) MTO is a production technique wherein products are customized according to customer specifications, and production only starts after an order is received. (oracle.com)
- According to the United Nations Industrial Development Organization (UNIDO), China is the top manufacturer worldwide by 2019 output, producing 28.7% of the total global manufacturing output, followed by the United States, Japan, Germany, and India.[52][53] (en.wikipedia.org)
- According to a Statista study, U.S. businesses spent $1.63 trillion on logistics in 2019, moving goods from origin to end user through various supply chain network segments. (netsuite.com)
- Many factories witnessed a 30% increase in output due to the shift to electric motors. (en.wikipedia.org)
- In the United States, for example, manufacturing makes up 15% of the economic output. (twi-global.com)
External Links
How To
Six Sigma in Manufacturing
Six Sigma refers to "the application and control of statistical processes (SPC) techniques in order to achieve continuous improvement." Motorola's Quality Improvement Department in Tokyo, Japan developed Six Sigma in 1986. The basic idea behind Six Sigma is to improve quality by improving processes through standardization and eliminating defects. In recent years, many companies have adopted this method because they believe there is no such thing as perfect products or services. Six Sigma's primary goal is to reduce variation from the average value of production. This means that you can take a sample from your product and then compare its performance to the average to find out how often the process differs from the norm. If it is too large, it means that there are problems.
Understanding how your business' variability is a key step towards Six Sigma implementation is the first. Once you understand this, you can then identify the causes of variation. You'll also want to determine whether these variations are random or systematic. Random variations are caused when people make mistakes. While systematic variations are caused outside of the process, they can occur. These are, for instance, random variations that occur when widgets are made and some fall off the production line. If however, you notice that each time you assemble a widget it falls apart in exactly the same spot, that is a problem.
Once you have identified the problem, you can design solutions. That solution might involve changing the way you do things or redesigning the process altogether. You should then test the changes again after they have been implemented. If they don't work you need to rework them and come up a better plan.