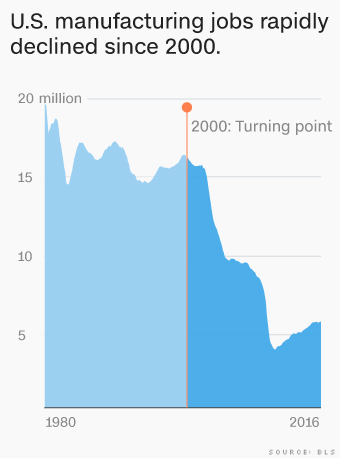
An industrial manager is an engineer who integrates different engineering processes to create an efficient management system. An industrial manager combines these engineering processes to create a single integrated management program. Here are some facts about this job. Listed below are some benefits and requirements for becoming an industrial manager. If you are looking for a challenging but rewarding career, this could be the career for your. Continue reading for more information.
Job description
An industrial manager oversees manufacturing and the production of goods or services. Although this job covers all aspects of the production process it will also cover how to source raw material and implement equipment. As computers play an increasingly important role in the coordination between different departments, suppliers, customers, and employees, industrial production managers need to be computer-literate. Industrial production managers must also be familiar with the latest production technologies as well as management practices. Many managers take part in professional organizations, attend tradeshows and conferences in the industry, and enroll in courses to earn certification.
In addition to overseeing manufacturing processes, industrial managers coordinate the activities of various departments within a company. They make sure that production lines run smoothly and meet customer demands in terms of quality, time and delivery. They oversee staffing levels and alter production levels when necessary to reduce inventory. They may also oversee quality control programs and coordinate communication with suppliers and other departments. The majority of this job involves managing people.
Education is necessary
Obtaining a bachelor's degree in business administration, management, or engineering is not typically enough to qualify as an industrial manager. Employers will prefer candidates who have a background in one or more of these fields. Computer literacy is also a requirement for industrial managers. Computers are becoming an increasingly important part of manufacturing, helping to coordinate production across departments and suppliers. This field requires that interested people have the required education and work experience.
Many industrial production managers begin their careers as workers, and then move up to supervisory positions. All professionals must obtain a college business management degree to reach the industrial manager level. However, entry-level workers may still be able obtain this education through their jobs or by taking classes sponsored in part by their companies. But, managers should have at least two- to five years of relevant experience to be considered for managerial positions.
Earning potential
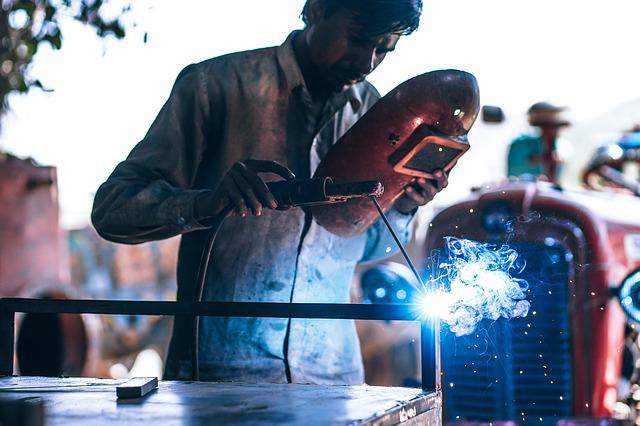
Industrial managers work in manufacturing plants and oversee the smooth operation of the entire process. They make strategic decisions, determine how employees and equipment are best utilized, and meet production standards. These people are responsible for evaluating and hiring workers. They also set production schedules and ensure safety. They are responsible for overseeing the day-to-day operations of a team and constantly analyzing the production process to ensure it is running efficiently and at peak performance.
An industrial production manager's earnings potential is dependent on both the employer and their experience. Although it's impossible to predict the future earnings of industrial producers, the average salary was $103,380 in May 2016, with the highest-paid earning industrial production managers earning $172,000. Higher earnings may also be available for industrial production managers who have completed advanced training or certification. According to the U.S. Bureau of Labor Statistics industrial production managers who have earned a bachelor’s degree or higher could earn more.
Work environment
A manager of industrial production divides their time between the production floor or an office. Sometimes, they live in the same building. Industrial production managers must observe established health and safety practices and wear appropriate protective equipment when working in a production area. They may also spend considerable time in meetings with subordinates or analyzing production data. These managers may also write reports. As a result, an industrial production manager's work environment is often dynamic.
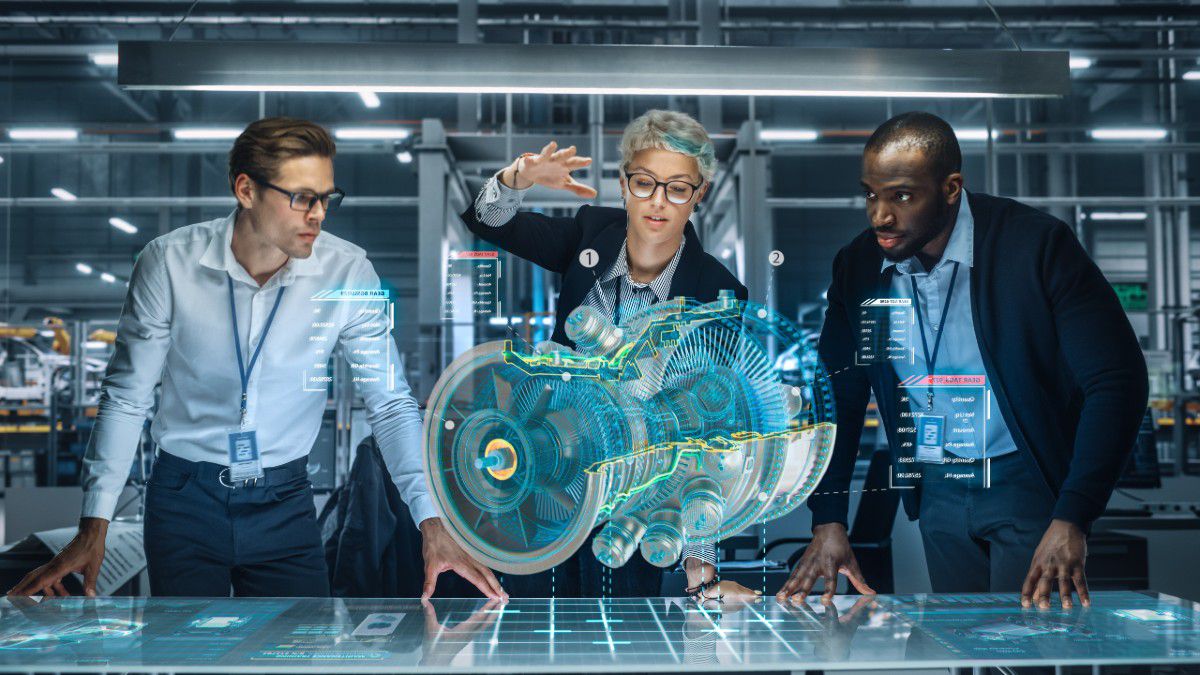
Industrial production managers are an integral part of the business's management structure. They have many responsibilities. They must coordinate the activities of various workers and increase productivity. The primary tasks of an industrial producer manager include increasing productivity and maintaining safety. Corporate restructuring has resulted in many levels of managerial and support staff being eliminated. Production managers now have a greater workload. This is a huge challenge for any manager. It can make the job of production managers difficult.
FAQ
How can I find out more about manufacturing?
Hands-on experience is the best way to learn more about manufacturing. If that is not possible, you could always read books or view educational videos.
What skills do production planners need?
To become a successful production planner, you need to be organized, flexible, and able to multitask. You must also be able to communicate effectively with clients and colleagues.
How can manufacturing efficiency improved?
First, determine which factors have the greatest impact on production time. Next, we must find ways to improve those factors. If you aren't sure where to begin, think about the factors that have the greatest impact on production time. Once you identify them, look for solutions.
Can certain manufacturing steps be automated?
Yes! Yes! Automation has existed since ancient times. The Egyptians discovered the wheel thousands and years ago. To help us build assembly lines, we now have robots.
There are many uses of robotics today in manufacturing. These include:
-
Assembly line robots
-
Robot welding
-
Robot painting
-
Robotics inspection
-
Robots that make products
Automation could also be used to improve manufacturing. For instance, 3D printing allows us make custom products and not have to wait for months or even weeks to get them made.
What are the 7 Rs of logistics?
The acronym 7R's for Logistics stands to represent the seven basic principles in logistics management. It was created by the International Association of Business Logisticians and published in 2004 under its "Seven Principles of Logistics Management".
The following letters form the acronym:
-
Responsible – ensure that all actions are legal and don't cause harm to anyone else.
-
Reliable - Have confidence in your ability to fulfill all of your commitments.
-
Reasonable - use resources efficiently and don't waste them.
-
Realistic - Take into consideration all aspects of operations including cost-effectiveness, environmental impact, and other factors.
-
Respectful - Treat people fairly and equitably
-
Resourceful - look for opportunities to save money and increase productivity.
-
Recognizable provides value-added products and services to customers
What does manufacturing mean?
Manufacturing Industries are those businesses that make products for sale. These products are sold to consumers. This is accomplished by using a variety of processes, including production, distribution and retailing. They produce goods from raw materials by using machines and other machinery. This includes all types manufactured goods such as clothing, building materials, furniture, electronics, tools and machinery.
What do you mean by warehouse?
A warehouse, or storage facility, is where goods are stored prior to being sold. You can have it indoors or outdoors. Sometimes, it can be both an indoor and outdoor space.
Statistics
- (2:04) MTO is a production technique wherein products are customized according to customer specifications, and production only starts after an order is received. (oracle.com)
- Many factories witnessed a 30% increase in output due to the shift to electric motors. (en.wikipedia.org)
- In 2021, an estimated 12.1 million Americans work in the manufacturing sector.6 (investopedia.com)
- It's estimated that 10.8% of the U.S. GDP in 2020 was contributed to manufacturing. (investopedia.com)
- In the United States, for example, manufacturing makes up 15% of the economic output. (twi-global.com)
External Links
How To
How to Use the Just In Time Method in Production
Just-in time (JIT), is a process that reduces costs and increases efficiency in business operations. It is a process where you get the right amount of resources at the right moment when they are needed. This means you only pay what you use. Frederick Taylor, a 1900s foreman, first coined the term. After observing how workers were paid overtime for late work, he realized that overtime was a common practice. He decided to ensure workers have enough time to do their jobs before starting work to improve productivity.
The idea behind JIT is that you should plan ahead and have everything ready so you don't waste money. It is important to look at your entire project from beginning to end and ensure that you have enough resources to handle any issues that may arise. If you expect problems to arise, you will be able to provide the necessary equipment and personnel to address them. This will prevent you from spending extra money on unnecessary things.
There are many JIT methods.
-
Demand-driven: This JIT is where you place regular orders for the parts/materials that are needed for your project. This will allow you to track how much material you have left over after using it. It will also allow you to predict how long it takes to produce more.
-
Inventory-based: This is a type where you stock the materials required for your projects in advance. This allows one to predict how much they will sell.
-
Project-driven: This means that you have enough money to pay for your project. Knowing how much money you have available will help you purchase the correct amount of materials.
-
Resource-based JIT: This type of JIT is most commonly used. You assign certain resources based off demand. You will, for example, assign more staff to deal with large orders. If there aren't many orders, you will assign fewer people.
-
Cost-based: This approach is very similar to resource-based. However, you don't just care about the number of people you have; you also need to consider how much each person will cost.
-
Price-based pricing: This is similar in concept to cost-based but instead you look at how much each worker costs, it looks at the overall company's price.
-
Material-based: This approach is similar to cost-based. However, instead of looking at the total cost for the company, you look at how much you spend on average on raw materials.
-
Time-based JIT: A variation on resource-based JIT. Instead of focusing only on how much each employee is costing, you should focus on how long it takes to complete your project.
-
Quality-based JIT - This is another form of resource-based JIT. Instead of worrying about the costs of each employee or how long it takes for something to be made, you should think about how quality your product is.
-
Value-based JIT is the newest form of JIT. In this instance, you are not concerned about the product's performance or meeting customer expectations. Instead, you're focused on how much value you add to the market.
-
Stock-based: This is an inventory-based method that focuses on the actual number of items being produced at any given time. It's used when you want to maximize production while minimizing inventory.
-
Just-intime (JIT), planning is a combination JIT management and supply chain management. It refers to the process of scheduling the delivery of components as soon as they are ordered. It's important because it reduces lead times and increases throughput.