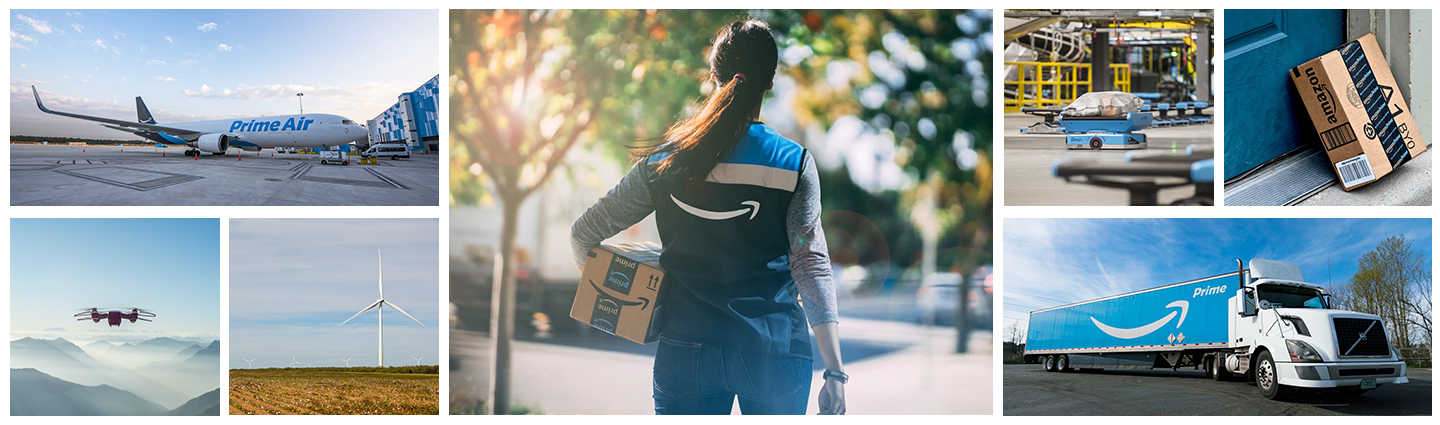
The foundation of continuous improvements is PDCA, or Plan, Do, Check, Act. If done right, this method can lead to significant improvements. Employee involvement is crucial to continuous improvement. A variety of resources are needed to implement the process. The process has many benefits beyond its measurement and costs. The PDCA cycle is not complete without the involvement of employees and customers.
PDCA cycle
Continuous improvement means that you must apply the PDCA process to every aspect your business. This cycle is about improving process and continuing to improve on the previous ones. Sometimes you can see new trends in data while the team is testing a new process. Other times, you might discover a new baseline. Both of these are ways to identify new areas for improvement. The PDCA Cycle is a great tool for identifying improvements opportunities. However, you must use it carefully and in a controlled way.
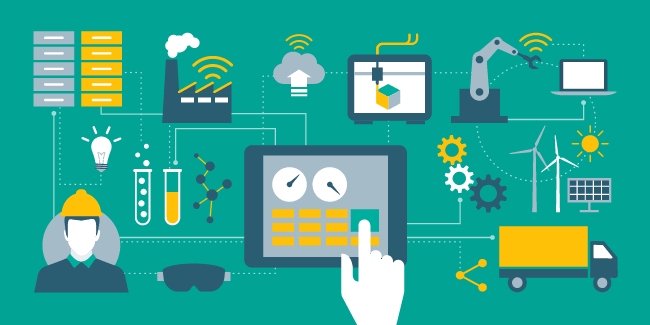
Employee participation
Employee involvement can have many names. However, in all cases effective organizations recognize its importance. Research shows that employee involvement directly correlates with important work outcomes. There are several types of employee involvement: direct communication, representative participation through unions and upward problem solving. These forms of employee involvement are often reinforced through the culture, environment, and leadership of an organization. Here are some examples.
Measuring
Many companies are now incorporating measurement as part of continuous improvement efforts. W. Edwards Deming introduced the Deming process. It has a Check phase to evaluate progress and meet its objectives. If the results are not satisfactory, then changes are made in order to improve the process. The cycle is repeated unless the results are satisfactory. Continuous improvement is a process that includes these processes.
Prices
It is important to conduct an enterprise-wide cost assessment for CI efforts in order to determine if the benefits outweigh any potential costs. The cost-benefit analysis should be based on the business imperative of achieving the highest possible customer satisfaction and employee engagement scores. To ensure success, the cost-benefit analysis must also consider the ROI of CI initiatives as well as the fine-tuning budgets. It should examine the effectiveness of key business processes, and benchmark them against industry standards and other leading competitors.
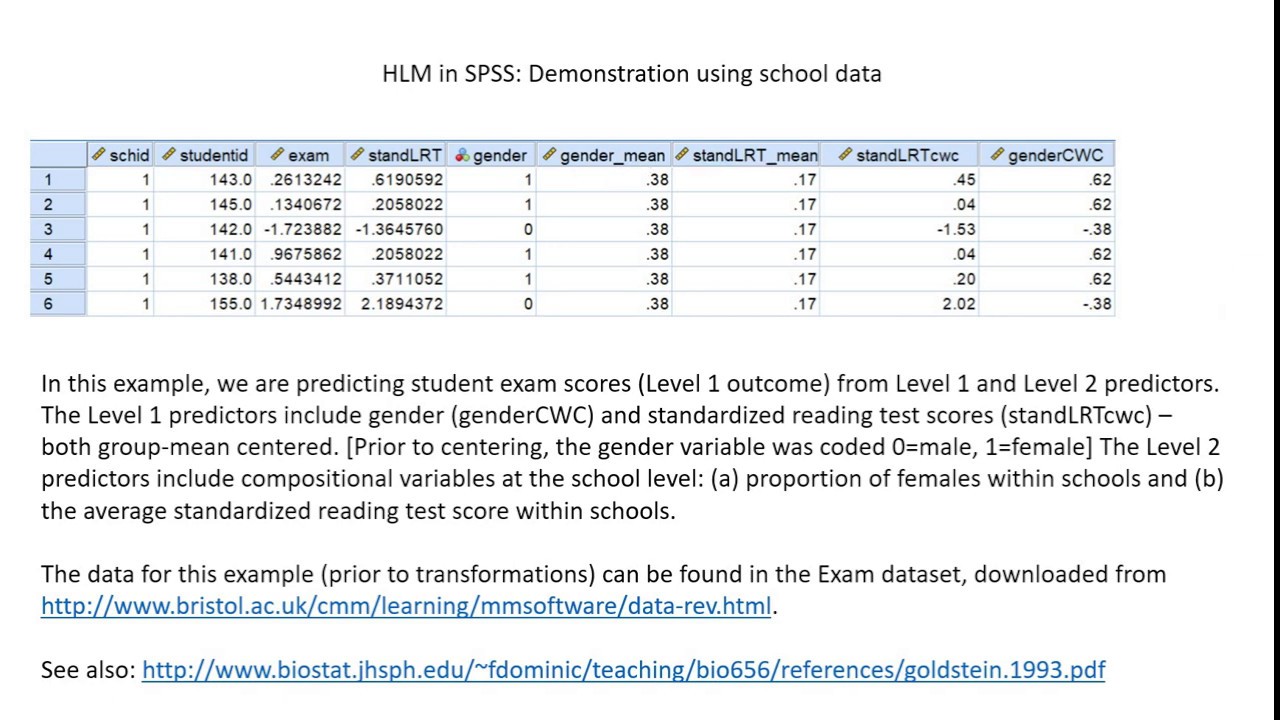
Benefits
The benefits of continuous improvement are clear. It is more likely that major breakthroughs will be achieved if the process is focused on learning and failing. Encourage employees to find ways to improve their work and give them ownership. Also, employees who are more involved in testing new technologies and tools might be empowered. You will also save money by focusing on continuous improvement. Successful changes improve employee satisfaction and make work easier for employees.
FAQ
What are the four types in manufacturing?
Manufacturing is the process that transforms raw materials into useful products. Manufacturing involves many activities, including designing, building, testing and packaging, shipping, selling, service, and so on.
What is it like to manage a logistics company?
To run a successful logistics company, you need a lot knowledge and skills. You must have good communication skills to interact effectively with your clients and suppliers. You need to understand how to analyze data and draw conclusions from it. You must be able and able to handle stress situations and work under pressure. You must be creative and innovative to develop new ideas to improve efficiency. You need to have strong leadership qualities to motivate team members and direct them towards achieving organizational goals.
It is also important to be efficient and well organized in order meet deadlines.
What is the importance of logistics in manufacturing?
Logistics are an essential part of any business. Logistics can help you achieve amazing results by helping to manage product flow from raw materials to finished products.
Logistics are also important in reducing costs and improving efficiency.
What is production planning?
Production Planning includes planning for all aspects related to production. This document aims to ensure that everything is planned and ready when you are ready to shoot. It should also provide information about how best to produce the best results while on set. This includes shooting schedules, locations, cast lists, crew details, and equipment requirements.
The first step in filming is to define what you want. You may have decided where to shoot or even specific locations you want to use. Once you have identified the scenes and locations, you can start to determine which elements are required for each scene. One example is if you are unsure of the exact model you want but decide that you require a car. To narrow your options, you can search online for available models.
Once you have found the right car, you can start thinking about extras. Do you have people who need to be seated in the front seat? Or perhaps you need someone walking around the back of the car? Maybe you'd like to change the interior from black to a white color. These questions will help you determine the exact look and feel of your car. The type of shots that you are looking for is another thing to consider. Do you want to film close-ups, or wider angles? Maybe the engine or steering wheel is what you are looking to film. These things will help you to identify the car that you are looking for.
Once you've determined the above, it is time to start creating a calendar. A schedule will tell you when you need to start shooting and when you need to finish. The schedule will show you when to get there, what time to leave, and when to return home. Everyone will know what they need and when. You can also make sure to book extra staff in advance if you have to hire them. You don't want to hire someone who won't show up because he didn't know.
You will need to factor in the days that you have to film when creating your schedule. Some projects are quick and easy, while others take weeks. It is important to consider whether you require more than one photo per day when you create your schedule. Multiple takes of the same location will lead to higher costs and take more time. It is better to be cautious and take fewer shots than you risk losing money if you are not sure if multiple takes are necessary.
Budgeting is another crucial aspect of production plan. It is important to set a realistic budget so you can work within your budget. If you have to reduce your budget due to unexpected circumstances, you can always lower it later. But, don't underestimate how much money you'll spend. You will end up spending less money if you underestimate the cost of something.
Production planning is a detailed process. But, once you understand the workings of everything, it becomes easier for future projects to be planned.
What is the responsibility of a production planner?
A production planner ensures all aspects of the project are delivered on time, within budget, and within scope. They also ensure the quality of the product and service meets the client's requirements.
Statistics
- It's estimated that 10.8% of the U.S. GDP in 2020 was contributed to manufacturing. (investopedia.com)
- In the United States, for example, manufacturing makes up 15% of the economic output. (twi-global.com)
- According to a Statista study, U.S. businesses spent $1.63 trillion on logistics in 2019, moving goods from origin to end user through various supply chain network segments. (netsuite.com)
- According to the United Nations Industrial Development Organization (UNIDO), China is the top manufacturer worldwide by 2019 output, producing 28.7% of the total global manufacturing output, followed by the United States, Japan, Germany, and India.[52][53] (en.wikipedia.org)
- In 2021, an estimated 12.1 million Americans work in the manufacturing sector.6 (investopedia.com)
External Links
How To
How to Use 5S to Increase Productivity in Manufacturing
5S stands for "Sort", "Set In Order", "Standardize", "Separate" and "Store". Toyota Motor Corporation was the first to develop the 5S approach in 1954. This methodology helps companies improve their work environment to increase efficiency.
This method has the basic goal of standardizing production processes to make them repeatable. Cleaning, sorting and packing are all done daily. This knowledge allows workers to be more efficient in their work because they are aware of what to expect.
Five steps are required to implement 5S: Sort, Set In Order, Standardize. Separate. Each step requires a different action to increase efficiency. You can make it easy for people to find things later by sorting them. When items are ordered, they are put together. You then organize your inventory in groups. You can also label your containers to ensure everything is properly labeled.
Employees need to reflect on how they do their jobs. Employees must be able to see why they do what they do and find a way to achieve them without having to rely on their old methods. They will need to develop new skills and techniques in order for the 5S system to be implemented.
The 5S method increases efficiency and morale among employees. They feel more motivated to work towards achieving greater efficiency as they see the results.