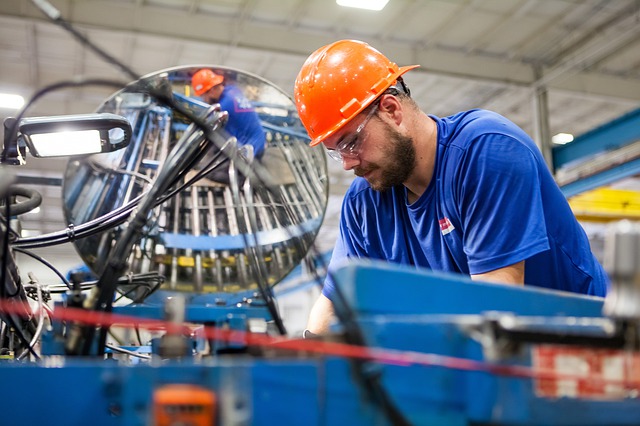
Getting a job as a safety engineer requires a bachelor's degree in an engineering or science related field. In addition to the education, you need to be able to work well with others. You might also need additional certifications.
You will be taught about safety regulations and procedures during your training as a safety engineer. You will also learn how you can investigate accidents and identify potential hazards. You will also learn how to inspect and evaluate machinery, buildings, as well as consumer products. You will also be able to prepare safety protocols and reports. You will learn how you can conduct routine compliance inspections, and prepare safety and occupational health programs.
Safety engineers usually work under the direction of an experienced engineer. You might also be a member of professional safety engineering organizations such as American Society of Safety Professionals. This is a good way to build contacts in your field. You can also use this opportunity to meet experienced safety engineers and learn from them. You should keep your resume up-to-date with your qualifications, if you intend to become a safety engineering professional.
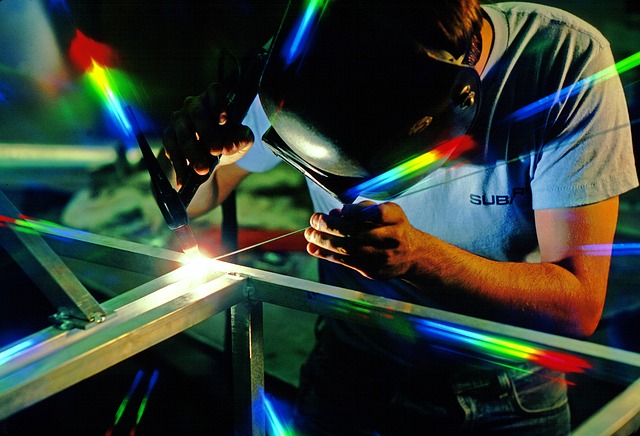
You might consider pursuing a master's program in safety and health after you have completed your bachelors degree. This will make you more competitive in the job market. A master's degree is also an option to get a better job in your field.
Your master's programme will teach you how safety systems can be developed and how to implement organisation-wide procedures. Advanced planning and analytical skills will be taught. This will equip you with the skills to manage more complicated projects and help you move up the ladder. To be eligible for managerial positions within health and safety, you can also use your masters.
Cooperative education is offered by many colleges and universities. These programs allow you both to obtain a bachelor’s and gain practical experience. This allows you apply for positions that would otherwise be more difficult to obtain without a degree. Most of these programs allow you to attend classes part-time, and some even allow you to work full-time while earning your degree.
To work as a safety engineer, you will need to have a bachelor's degree. A license is available in almost all states. You will need to pass a state examination and have four years of work experience that is relevant to your field. You may also be required to complete a course in workplace safety.
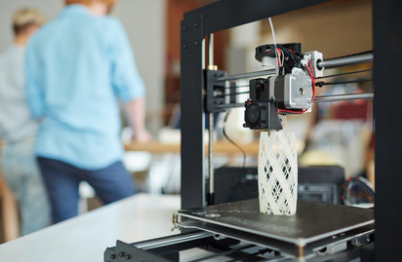
Employers may prefer candidates who have practical experience once you're licensed. Many schools offer cooperative education programs, and some allow students to take classes part-time. You can also search online for employment. You might be interested in joining professional organizations, like the American Society of Safety Engineers. The Institute of Hazardous Materials Management is another option that will help safety professionals develop leadership skills.
Health and safety engineering is an exciting career path. You need to have great communication and science skills. Also, you must be creative and skilled at solving difficult problems.
FAQ
How can manufacturing efficiency be improved?
The first step is to identify the most important factors affecting production time. We then need to figure out how to improve these variables. You can start by identifying the most important factors that impact production time. Once you've identified them all, find solutions to each one.
What are the differences between these four types?
Manufacturing is the process that transforms raw materials into useful products. Manufacturing can include many activities such as designing and building, testing, packaging shipping, selling, servicing, and other related activities.
What is the importance of logistics in manufacturing?
Logistics are an integral part any business. They are essential to any business's success.
Logistics play an important role in reducing costs as well as increasing efficiency.
What skills should a production planner have?
Being a production planner is not easy. You need to be organized and flexible. You must also be able to communicate effectively with clients and colleagues.
Why automate your factory?
Modern warehouses are increasingly dependent on automation. Increased demand for efficient and faster delivery has resulted in a rise in e-commerce.
Warehouses must adapt quickly to meet changing customer needs. Technology investment is necessary to enable warehouses to respond quickly to changing demands. Automation warehouses can bring many benefits. These are just a few reasons to invest in automation.
-
Increases throughput/productivity
-
Reduces errors
-
Improves accuracy
-
Safety Boosts
-
Eliminates bottlenecks
-
Allows companies to scale more easily
-
Makes workers more efficient
-
Gives you visibility into all that is happening in your warehouse
-
Enhances customer experience
-
Improves employee satisfaction
-
Reduces downtime and improves uptime
-
This ensures that quality products are delivered promptly
-
Removing human error
-
It helps ensure compliance with regulations
Statistics
- In 2021, an estimated 12.1 million Americans work in the manufacturing sector.6 (investopedia.com)
- Many factories witnessed a 30% increase in output due to the shift to electric motors. (en.wikipedia.org)
- According to a Statista study, U.S. businesses spent $1.63 trillion on logistics in 2019, moving goods from origin to end user through various supply chain network segments. (netsuite.com)
- It's estimated that 10.8% of the U.S. GDP in 2020 was contributed to manufacturing. (investopedia.com)
- Job #1 is delivering the ordered product according to specifications: color, size, brand, and quantity. (netsuite.com)
External Links
How To
How to use 5S in Manufacturing to Increase Productivity
5S stands for "Sort", 'Set In Order", 'Standardize', & Separate>. Toyota Motor Corporation invented the 5S strategy in 1954. This methodology helps companies improve their work environment to increase efficiency.
This method has the basic goal of standardizing production processes to make them repeatable. It means tasks like cleaning, sorting or packing, labeling, and storing are done every day. These actions allow workers to perform their job more efficiently, knowing what to expect.
There are five steps to implementing 5S, including Sort, Set In Order, Standardize, Separate and Store. Each step has a different action and leads to higher efficiency. By sorting, for example, you make it easy to find the items later. Once you have placed items in an ordered fashion, you will put them together. After you have divided your inventory into groups you can store them in easy-to-reach containers. You can also label your containers to ensure everything is properly labeled.
This requires employees to critically evaluate how they work. Employees need to understand the reasons they do certain jobs and determine if there is a better way. In order to use the 5S system effectively, they must be able to learn new skills.
The 5S method not only increases efficiency but also boosts morale and teamwork. They will feel motivated to strive for higher levels of efficiency once they start to see results.