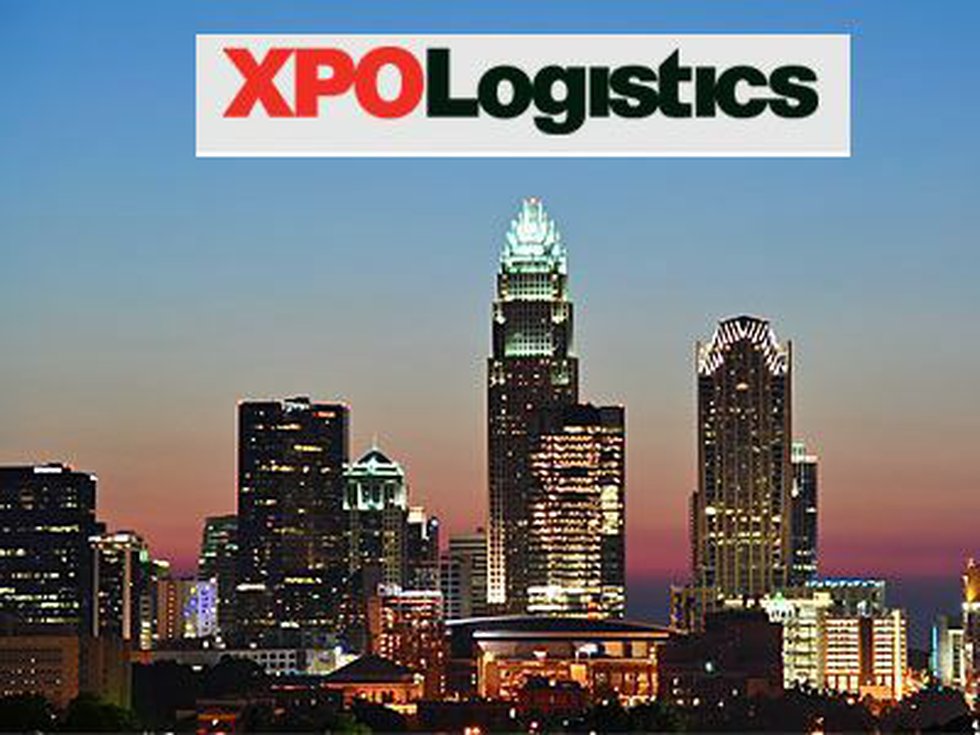
Cellular manufacturing is a method of dividing a production line into sections that produce a particular component of the finished product. This reduces waste and decreases lead times. A cellular manufacturing system can be implemented in many different ways. Some are easier than others, while some require sophisticated computer models. Cellular manufacturing is an example of lean manufacturing.
Cellular manufacturing, an innovative and highly efficient process, can help lower the cost and time it takes to produce parts. The goal is to minimize waste while moving products along the production line as quickly possible. Cellular manufacturing also addresses issues such as group cohesiveness and self management, as well issues involving employee inputs and supervision. Cellular manufacturing gives organizations more flexibility which can be beneficial in meeting customer demand. Cellular manufacturing has also been shown to improve productivity.
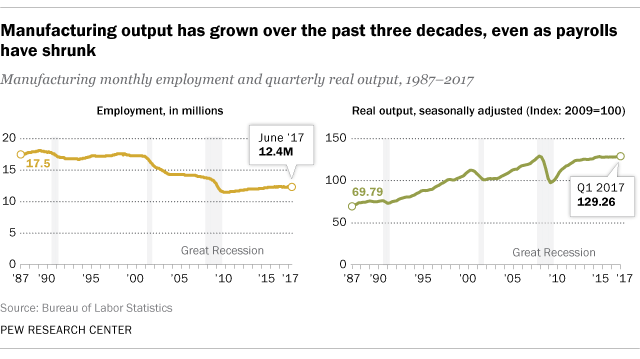
Cellular manufacturing can be used in many different ways. From simple applications like production flow analysis, to more complicated computer models. It is important to produce identical products simultaneously, which reduces wasteful motions and takt time.
The cell layout can impact the overall takt times. The cells' layout can affect the motion, changing it from non-value to value, which reduces cycle time. Some cells are configured in a U-shape, allowing operators to move from machine to machine more quickly. Some cells can be arranged in a U-shape to allow workers to maneuver around heavy machinery. These designs are especially effective for businesses that make a variety of products.
The first step of creating a cell involves identifying the products that will go into it. This can be done using a process diagram, which will help you to determine the production speed. Engineers will need to identify the number of workstations and the steps involved in creating a workcell. Next is to decide what equipment and tools should be used within the cell. Modern work cells are also aware of the different types and steps required to access each holding bin. It also considers how long each machine will take. The physical structure of the cell will determine which layout is most effective.
The design of the cell is crucial to the success in cellular manufacturing. Cell design can affect how much motion is lost and how many waste products are created. It can also impact fatigue. Cellular manufacturing can not only reduce motion but also improve process efficiency, quality and productivity. Cell layout can reduce waste by ensuring that defects are detected quickly.
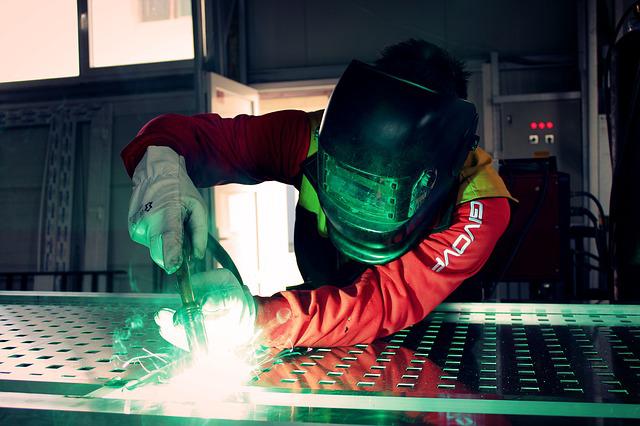
Some of the most common layouts include a U, Z, and S. The Z-shape is most commonly used to work around machines, while the S-shape is used to create cells that process parts one at a time. S-shaped cells may also be used to circumvent obstructions. It is possible to customize the layout of cells, as well as reconfigure different cells to meet different requirements in different parts of a factory.
FAQ
What do you mean by warehouse?
A warehouse, or storage facility, is where goods are stored prior to being sold. It can be an outdoor or indoor area. In some cases it could be both indoors and outdoors.
Why automate your warehouse
Modern warehouses are increasingly dependent on automation. With the rise of ecommerce, there is a greater demand for faster delivery times as well as more efficient processes.
Warehouses need to adapt quickly to meet changing needs. Technology is essential for warehouses to be able to adapt quickly to changing needs. Automating warehouses has many benefits. These are some of the benefits that automation can bring to warehouses:
-
Increases throughput/productivity
-
Reduces errors
-
Improves accuracy
-
Boosts safety
-
Eliminates bottlenecks
-
Allows companies to scale more easily
-
Increases efficiency of workers
-
It gives visibility to everything that happens inside the warehouse
-
Enhances customer experience
-
Improves employee satisfaction
-
It reduces downtime, and increases uptime
-
Quality products delivered on time
-
Removing human error
-
It helps ensure compliance with regulations
What do we need to know about Manufacturing Processes in order to learn more about Logistics?
No. No. Knowing about manufacturing processes will help you understand how logistics works.
How can manufacturing prevent production bottlenecks?
You can avoid bottlenecks in production by making sure that everything runs smoothly throughout the production cycle, from the moment you receive an order to the moment the product is shipped.
This includes planning for both capacity requirements and quality control measures.
This can be done by using continuous improvement techniques, such as Six Sigma.
Six Sigma can be used to improve the quality and decrease waste in all areas of your company.
It's all about eliminating variation and creating consistency in work.
Statistics
- In 2021, an estimated 12.1 million Americans work in the manufacturing sector.6 (investopedia.com)
- According to a Statista study, U.S. businesses spent $1.63 trillion on logistics in 2019, moving goods from origin to end user through various supply chain network segments. (netsuite.com)
- According to the United Nations Industrial Development Organization (UNIDO), China is the top manufacturer worldwide by 2019 output, producing 28.7% of the total global manufacturing output, followed by the United States, Japan, Germany, and India.[52][53] (en.wikipedia.org)
- You can multiply the result by 100 to get the total percent of monthly overhead. (investopedia.com)
- (2:04) MTO is a production technique wherein products are customized according to customer specifications, and production only starts after an order is received. (oracle.com)
External Links
How To
How to Use 5S for Increasing Productivity in Manufacturing
5S stands to stand for "Sort", “Set In Order", “Standardize", and "Store". Toyota Motor Corporation developed the 5S method in 1954. It allows companies to improve their work environment, thereby achieving greater efficiency.
This method aims to standardize production processes so that they are repeatable, measurable and predictable. This means that tasks such as cleaning, sorting, storing, packing, and labeling are performed daily. Workers can be more productive by knowing what to expect.
There are five steps that you need to follow in order to implement 5S. Each step is a different action that leads to greater efficiency. For example, when you sort things, you make them easy to find later. When items are ordered, they are put together. Next, organize your inventory into categories and store them in containers that are easily accessible. Finally, when you label your containers, you ensure everything is labeled correctly.
This requires employees to critically evaluate how they work. Employees need to understand the reasons they do certain jobs and determine if there is a better way. They will need to develop new skills and techniques in order for the 5S system to be implemented.
The 5S method not only increases efficiency but also boosts morale and teamwork. They feel more motivated to work towards achieving greater efficiency as they see the results.