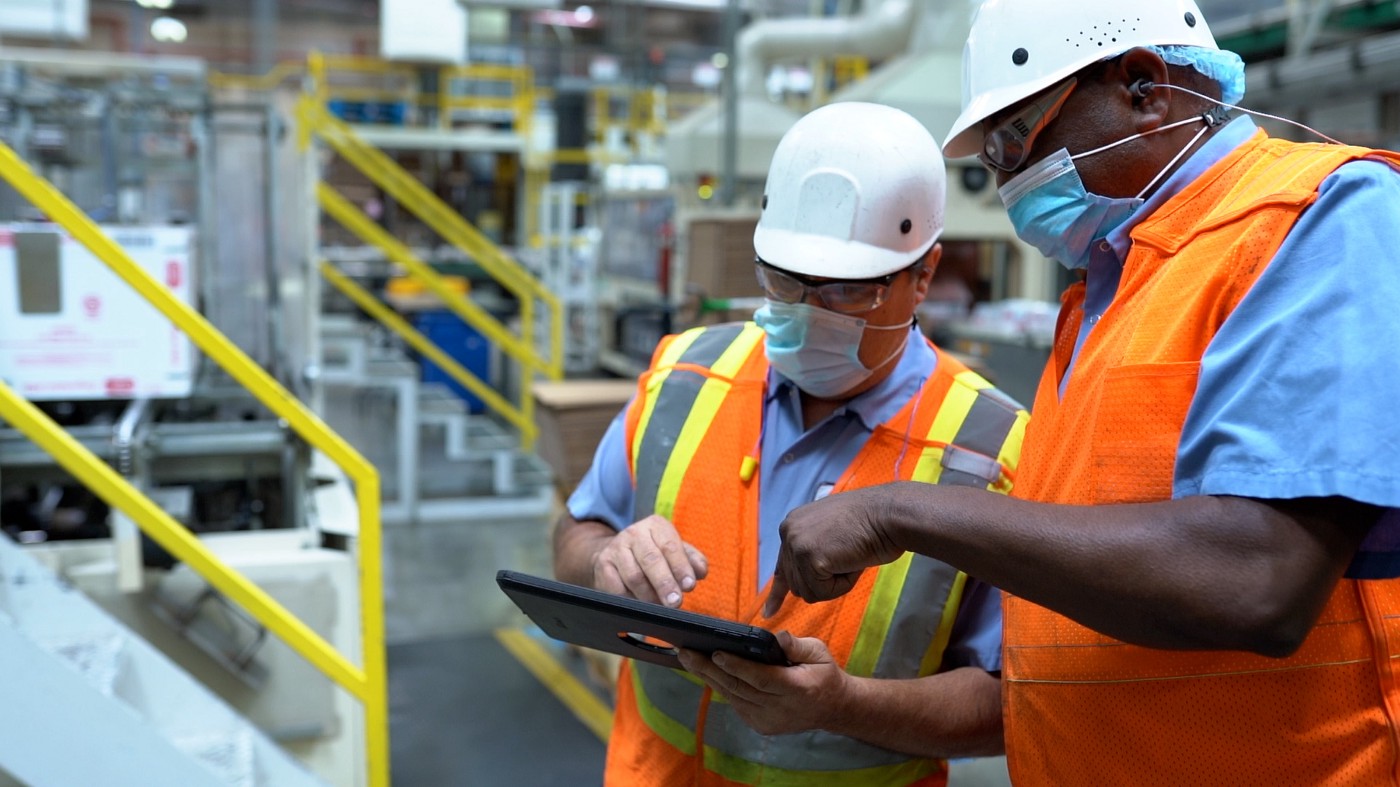
Manufacturing engineers were highly sought after during the industrial revolution. They design manufacturing processes that improve productivity. Manufacturing engineers must be commercially-aware in addition to their technical knowledge. They should also have a solid foundation in science and mathematics. They should also have leadership skills.
Manufacturing engineers' salaries will vary depending on their education, experience, and skills. The average annual salary for a manufacturing engineer in the United States is between $70960 and $126,000. They can get a master’s degree to help them advance their careers. The master's degree will allow them to earn a higher salary. A master's can allow them to learn new technologies, and improve their skills.
You can also apply for a PhD so that you can contribute as a researcher. They can also work for the central and local government. They might also work as consultants. They could work in different areas.
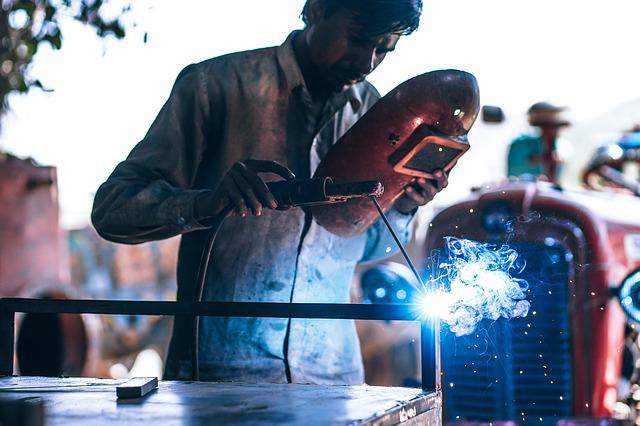
The salary of manufacturing engineers tends to increase with experience. They will become more experienced and can move up to managerial roles. This position allows them to design and implement manufacturing processes. They will also oversee the daily operations of the factory. They may be required to work nights and weekends.
Manufacturing engineers usually start as apprentices or interns. They can work in many areas of manufacturing such as aerospace engineering, food manufacturing and pharmaceutical manufacturing. They may also be able to work in the commercial and industrial design. After a few years of experience, they may be able to work as consultants. In this position, they will be able to take charge of the factory floor and guide engineers. They will be responsible for ensuring the company follows best practices. They will also be expected to identify and resolve any errors in the manufacturing process.
Manufacturing engineers must stay on top of the latest manufacturing trends. They must be able to work in a fast-paced environment and resolve any issues that may occur. They also need to have good leadership and IT skills. They will get a regular salary during their first few year of employment. They can earn a slightly higher salary after they have been in the industry for a few years.
Manufacturing engineers usually earn salaries between $28,500-126,000 each year. This salary range includes bonuses, taxable wages, and other benefits. The salary can also depend on the state in which the job is located. Manufacturing Engineers in some states can make as much as $34 an hour.
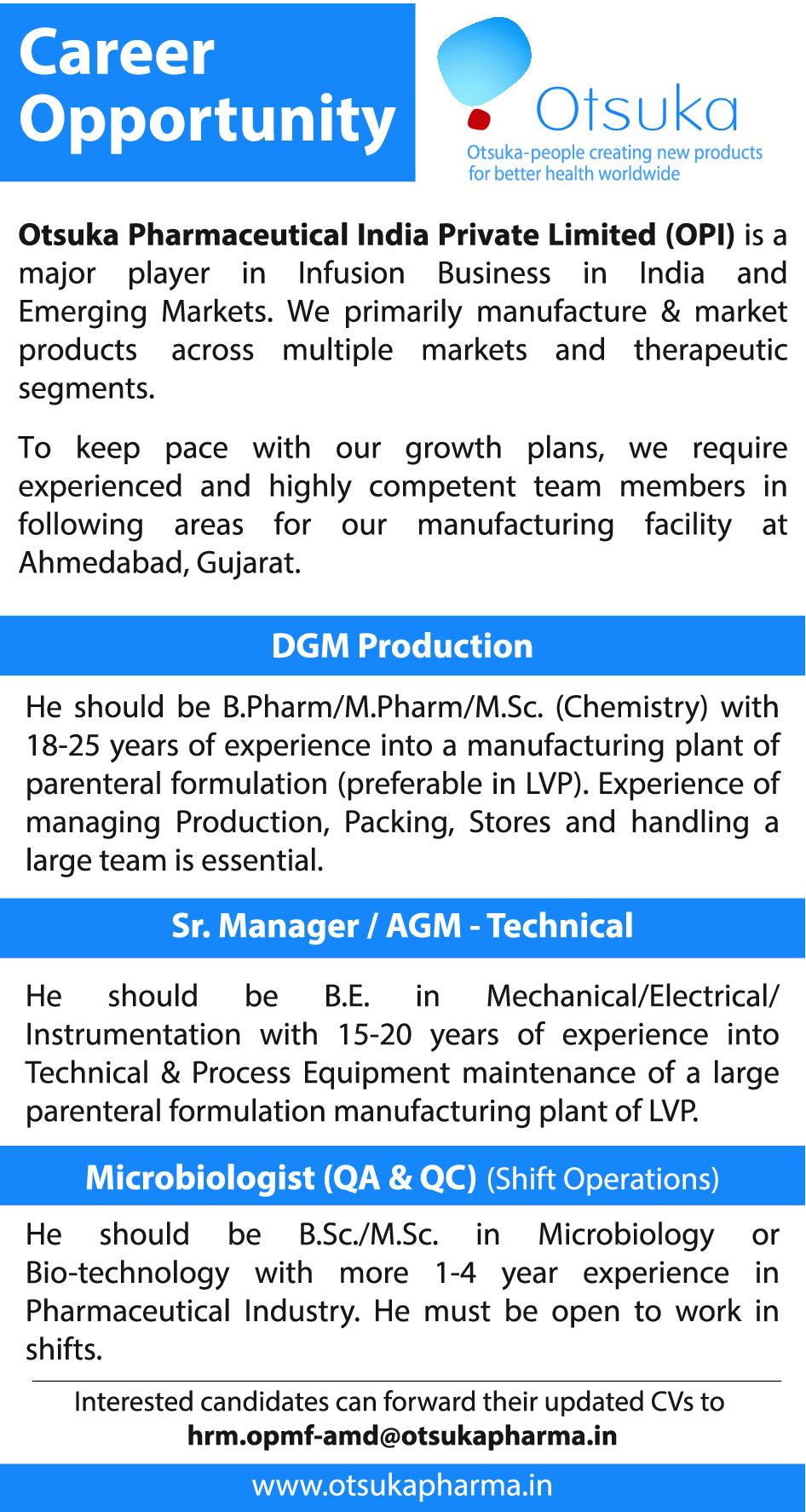
A manufacturing engineer can work in many manufacturing industries, such as aerospace, food manufacturing and pharmaceutical manufacturing. They can work for large multinationals or smaller local companies. They can also work in central or local government.
They can also work for new industrial estates. General Motors and Tesla are some of the most prominent American manufacturing companies. A graduate degree can also help an engineer learn more about new technologies.
FAQ
What are the 7 Rs of logistics.
The acronym 7Rs of Logistics refers to the seven core principles of logistics management. It was created by the International Association of Business Logisticians and published in 2004 under its "Seven Principles of Logistics Management".
The following letters make up the acronym:
-
Responsive - ensure all actions are legal and not harmful to others.
-
Reliable: Have faith in your ability or the ability to honor any promises made.
-
Reasonable - use resources efficiently and don't waste them.
-
Realistic - consider all aspects of operations, including cost-effectiveness and environmental impact.
-
Respectful - show respect and treat others fairly and fairly
-
Responsive - Look for ways to save time and increase productivity.
-
Recognizable - Provide value-added services to customers
What is production planning?
Production planning is the process of creating a plan that covers all aspects of production. This includes scheduling, budgeting and crew, location, equipment, props, and more. This document aims to ensure that everything is planned and ready when you are ready to shoot. You should also have information to ensure the best possible results on set. This includes information on shooting times, locations, cast lists and crew details.
First, you need to plan what you want to film. You may have already chosen the location you want, or there are locations or sets you prefer. Once you have identified the scenes and locations, you can start to determine which elements are required for each scene. Perhaps you have decided that you need to buy a car but aren't sure which model. If this is the case, you might start searching online for car models and then narrow your options by selecting from different makes.
Once you have found the right vehicle, you can think about adding accessories. Do you need people sitting in the front seats? Or maybe you just need someone to push the car around. Maybe you'd like to change the interior from black to a white color. These questions will help guide you in determining the ideal look and feel for your car. It is also worth considering the types of shots that you wish to take. Will you be filming close-ups or wide angles? Maybe you want to show your engine or the steering wheel. These details will help identify the exact car you wish to film.
Once you have made all the necessary decisions, you can start to create a schedule. The schedule will show you when to begin shooting and when to stop. Every day will have a time for you to arrive at the location, leave when you are leaving and return home when you are done. Everyone will know what they need and when. You can also make sure to book extra staff in advance if you have to hire them. You should not hire anyone who doesn't show up because of your inaction.
Your schedule will also have to be adjusted to reflect the number of days required to film. Some projects only take one or two days, while others may last weeks. While creating your schedule, it is important to remember whether you will require more than one shot per day. Multiplying takes in the same area will result both in increased costs and a longer time. It's better to be safe than sorry and shoot less takes if you're not certain whether you need more takes.
Another important aspect of production planning is setting budgets. A realistic budget will help you work within your means. If you have to reduce your budget due to unexpected circumstances, you can always lower it later. However, it is important not to overestimate the amount that you will spend. You'll end up with less money after paying for other things if the cost is underestimated.
Planning production is a tedious process. Once you have a good understanding of how everything works together, planning future projects becomes easy.
What do you mean by warehouse?
A warehouse or storage facility is where goods are stored before they are sold. It can be an outdoor or indoor area. It may also be an indoor space or an outdoor area.
Why automate your factory?
Automation has become increasingly important in modern warehousing. E-commerce has brought increased demand for more efficient and quicker delivery times.
Warehouses must adapt quickly to meet changing customer needs. Technology investment is necessary to enable warehouses to respond quickly to changing demands. Automation of warehouses offers many benefits. Here are some of the reasons automation is worth your investment:
-
Increases throughput/productivity
-
Reduces errors
-
Accuracy is improved
-
Safety Boosts
-
Eliminates bottlenecks
-
Allows companies scale more easily
-
This makes workers more productive
-
Provides visibility into everything that happens in the warehouse
-
Enhances customer experience
-
Improves employee satisfaction
-
Reducing downtime and increasing uptime
-
Ensures quality products are delivered on time
-
Human error can be eliminated
-
It ensures compliance with regulations
Statistics
- (2:04) MTO is a production technique wherein products are customized according to customer specifications, and production only starts after an order is received. (oracle.com)
- In 2021, an estimated 12.1 million Americans work in the manufacturing sector.6 (investopedia.com)
- According to the United Nations Industrial Development Organization (UNIDO), China is the top manufacturer worldwide by 2019 output, producing 28.7% of the total global manufacturing output, followed by the United States, Japan, Germany, and India.[52][53] (en.wikipedia.org)
- Many factories witnessed a 30% increase in output due to the shift to electric motors. (en.wikipedia.org)
- You can multiply the result by 100 to get the total percent of monthly overhead. (investopedia.com)
External Links
How To
How to Use the Just-In-Time Method in Production
Just-intime (JIT), which is a method to minimize costs and maximize efficiency in business process, is one way. It is a process where you get the right amount of resources at the right moment when they are needed. This means that only what you use is charged to your account. Frederick Taylor, a 1900s foreman, first coined the term. He noticed that workers were often paid overtime when they had to work late. He decided to ensure workers have enough time to do their jobs before starting work to improve productivity.
JIT is a way to plan ahead and make sure you don't waste any money. You should also look at the entire project from start to finish and make sure that you have sufficient resources available to deal with any problems that arise during the course of your project. You will have the resources and people to solve any problems you anticipate. This way you won't be spending more on things that aren’t really needed.
There are many JIT methods.
-
Demand-driven: This JIT is where you place regular orders for the parts/materials that are needed for your project. This will let you track the amount of material left over after you've used it. You'll also be able to estimate how long it will take to produce more.
-
Inventory-based: This allows you to store the materials necessary for your projects in advance. This allows you to forecast how much you will sell.
-
Project-driven: This approach involves setting aside sufficient funds to cover your project's costs. When you know how much you need, you'll purchase the appropriate amount of materials.
-
Resource-based JIT: This is the most popular form of JIT. Here you can allocate certain resources based purely on demand. You might assign more people to help with orders if there are many. If you don't have many orders, you'll assign fewer people to handle the workload.
-
Cost-based : This is similar in concept to resource-based. But here, you aren't concerned about how many people your company has but how much each individual costs.
-
Price-based: This approach is very similar to the cost-based method except that you don't look at individual workers costs but the total cost of the company.
-
Material-based: This is very similar to cost-based but instead of looking at total costs of the company you are concerned with how many raw materials you use on an average.
-
Time-based JIT: This is another variant of resource-based JIT. Instead of focusing only on how much each employee is costing, you should focus on how long it takes to complete your project.
-
Quality-based: This is yet another variation of resource-based JIT. Instead of thinking about the cost of each employee or the time it takes to produce something, you focus on how good your product quality.
-
Value-based: This is one of the newest forms of JIT. In this case, you're not concerned with how well the products perform or whether they meet customer expectations. Instead, you focus on the added value that you provide to your market.
-
Stock-based: This is an inventory-based method that focuses on the actual number of items being produced at any given time. This method is useful when you want to increase production while decreasing inventory.
-
Just-in-time planning (JIT): This is a combination JIT and supply-chain management. It is the process that schedules the delivery of components within a short time of their order. This is important as it reduces lead time and increases throughput.