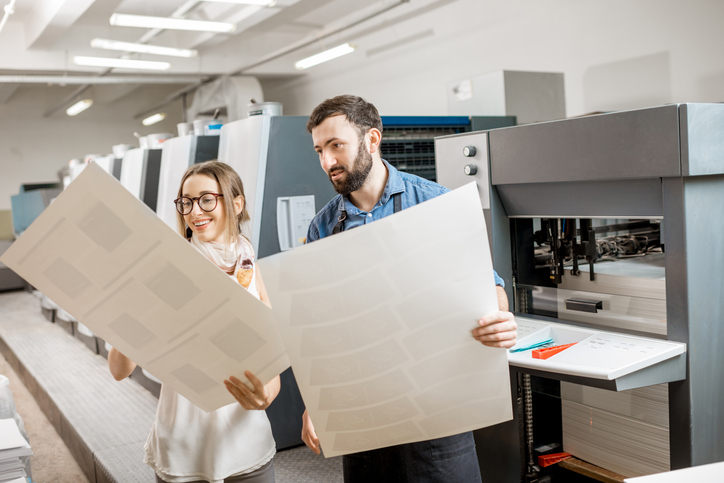
Mechanical Technical Specialists are responsible for analyzing process data and providing technical troubleshooting to maintenance staff. They also assist in short-term outage planning by developing system improvements.
This is an increasingly popular field. A professional mechanic must be able and willing to communicate with customers. You will need to have strong time management skills, technical language knowledge, and the ability work in a group.
These engineers have the technical skills to work in sales and marketing. They can also manage and troubleshoot issues. As the demand for new and more efficient machinery grows, the quality of work expected from these professionals increases.
This field requires a high level of education. Mechanical engineers must understand the science behind design and production. In the field of heat engineering they study heat flow in structures. In heat engineering, equipment is developed for transportation and air conditioning.
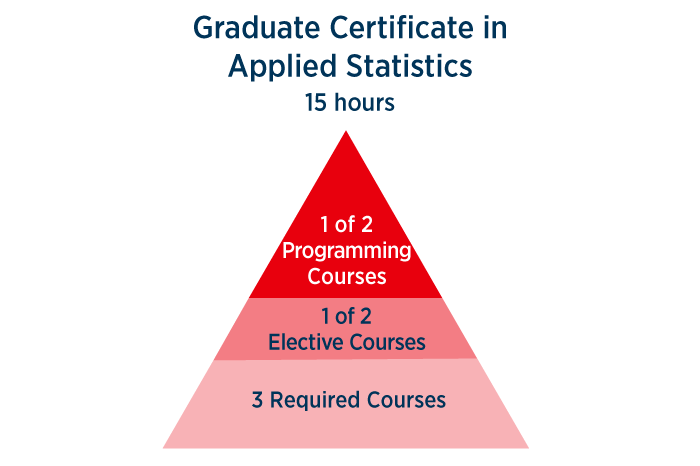
The forefront of technology has always been in the hands of mechanics. Mechanical engineers are now able to design new materials and designs for smaller machines. A further advantage is the ability to use nanotechnology for designing at the smallest scale. Composites are materials that combine multiple materials to create a single product.
These professionals employ rationalized methods of design and manufacturing. Value engineering is an example of this approach. This is a way to get the most out of your resources. Another approach to operations research is also available.
Mechanical engineers are always looking for new jobs and many dream of establishing commercial exchanges with foreigners. For a job abroad, they will need to be able speak and write English fluently.
It is vital to be able to speak a wide range of languages. Attending industry events and reading English-language magazines can help mechanics improve their English. To improve their skills, they can also enroll in an online course.
A mechanic must have these skills and be able time manage well. Two years experience is required for mechanical technicians. They should possess excellent analytical and critical skills, as well the ability to use diagnostic software.
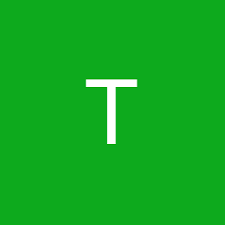
This field requires a solid understanding of computers and computer-aided design. An associate's degree is recommended in mechanical engineering technology.
They assist craftsmen with daily management tasks, analyze process data, provide technical leadership, and support them in crafting their employees. They can also solve recurring problems.
Mechanical Engineers work in collaboration with civil engineers, chemical engineers, and electrical engineers to enhance vehicle and equipment performance. They also assist in research, development, and construction. Many mechanical engineers work full-time, or in addition to their day job.
FAQ
Do we need to know about Manufacturing Processes before learning about Logistics?
No. No. It is important to know about the manufacturing processes in order to understand how logistics works.
What are the jobs in logistics?
There are many jobs available in logistics. Some examples are:
-
Warehouse workers – They load, unload and transport pallets and trucks.
-
Transport drivers - These are people who drive trucks and trailers to transport goods or perform pick-ups.
-
Freight handlers – They sort and package freight at warehouses.
-
Inventory managers - They oversee the inventory of goods in warehouses.
-
Sales representatives: They sell products to customers.
-
Logistics coordinators: They plan and manage logistics operations.
-
Purchasing agents are those who purchase goods and services for the company.
-
Customer service representatives are available to answer customer calls and emails.
-
Ship clerks - They issue bills and process shipping orders.
-
Order fillers - These people fill orders based on what has been ordered.
-
Quality control inspectors - They check incoming and outgoing products for defects.
-
Others - There are many other types of jobs available in logistics, such as transportation supervisors, cargo specialists, etc.
How can we reduce manufacturing overproduction?
It is essential to find better ways to manage inventory to reduce overproduction. This would decrease the time that is spent on inefficient activities like purchasing, storing, or maintaining excess stock. This could help us free up our time for other productive tasks.
You can do this by adopting a Kanban method. A Kanban Board is a visual display that tracks work progress. A Kanban system allows work items to move through several states before reaching their final destination. Each state is assigned a different priority.
As an example, if work is progressing from one stage of the process to another, then the current task is complete and can be transferred to the next. A task that is still in the initial stages of a process will be considered complete until it moves on to the next stage.
This allows for work to continue moving forward, while also ensuring that there is no work left behind. Managers can see how much work has been done and the status of each task at any time with a Kanban Board. This data allows them adjust their workflow based upon real-time data.
Lean manufacturing is another option to control inventory levels. Lean manufacturing emphasizes eliminating waste in all phases of production. Waste includes anything that does not add value to the product. There are several types of waste that you might encounter:
-
Overproduction
-
Inventory
-
Unnecessary packaging
-
Material surplus
Manufacturers can reduce their costs and improve their efficiency by using these ideas.
Can some manufacturing processes be automated?
Yes! Yes. Automation has been around since ancient time. The wheel was invented by the Egyptians thousands of years ago. To help us build assembly lines, we now have robots.
There are many uses of robotics today in manufacturing. These include:
-
Robots for assembly line
-
Robot welding
-
Robot painting
-
Robotics inspection
-
Robots that create products
Manufacturing could also benefit from automation in other ways. 3D printing makes it possible to produce custom products in a matter of days or weeks.
Statistics
- In the United States, for example, manufacturing makes up 15% of the economic output. (twi-global.com)
- According to a Statista study, U.S. businesses spent $1.63 trillion on logistics in 2019, moving goods from origin to end user through various supply chain network segments. (netsuite.com)
- (2:04) MTO is a production technique wherein products are customized according to customer specifications, and production only starts after an order is received. (oracle.com)
- It's estimated that 10.8% of the U.S. GDP in 2020 was contributed to manufacturing. (investopedia.com)
- In 2021, an estimated 12.1 million Americans work in the manufacturing sector.6 (investopedia.com)
External Links
How To
Six Sigma: How to Use it in Manufacturing
Six Sigma can be described as "the use of statistical process control (SPC), techniques to achieve continuous improvement." It was developed by Motorola's Quality Improvement Department at their plant in Tokyo, Japan, in 1986. Six Sigma is a method to improve quality through standardization and elimination of defects. Many companies have adopted this method in recent years. They believe there is no such thing a perfect product or service. The main goal of Six Sigma is to reduce variation from the mean value of production. You can calculate the percentage of deviation from the norm by taking a sample of your product and comparing it to the average. If it is too large, it means that there are problems.
Understanding the nature of variability in your business is the first step to Six Sigma. Once you understand this, you can then identify the causes of variation. It is important to identify whether the variations are random or systemic. Random variations happen when people make errors; systematic variations are caused externally. Random variations would include, for example, the failure of some widgets to fall from the assembly line. However, if you notice that every time you assemble a widget, it always falls apart at exactly the same place, then that would be a systematic problem.
Once you've identified the problem areas you need to find solutions. That solution might involve changing the way you do things or redesigning the process altogether. After implementing the new changes, you should test them again to see if they worked. If they don't work, you will need to go back to the drawing boards and create a new plan.