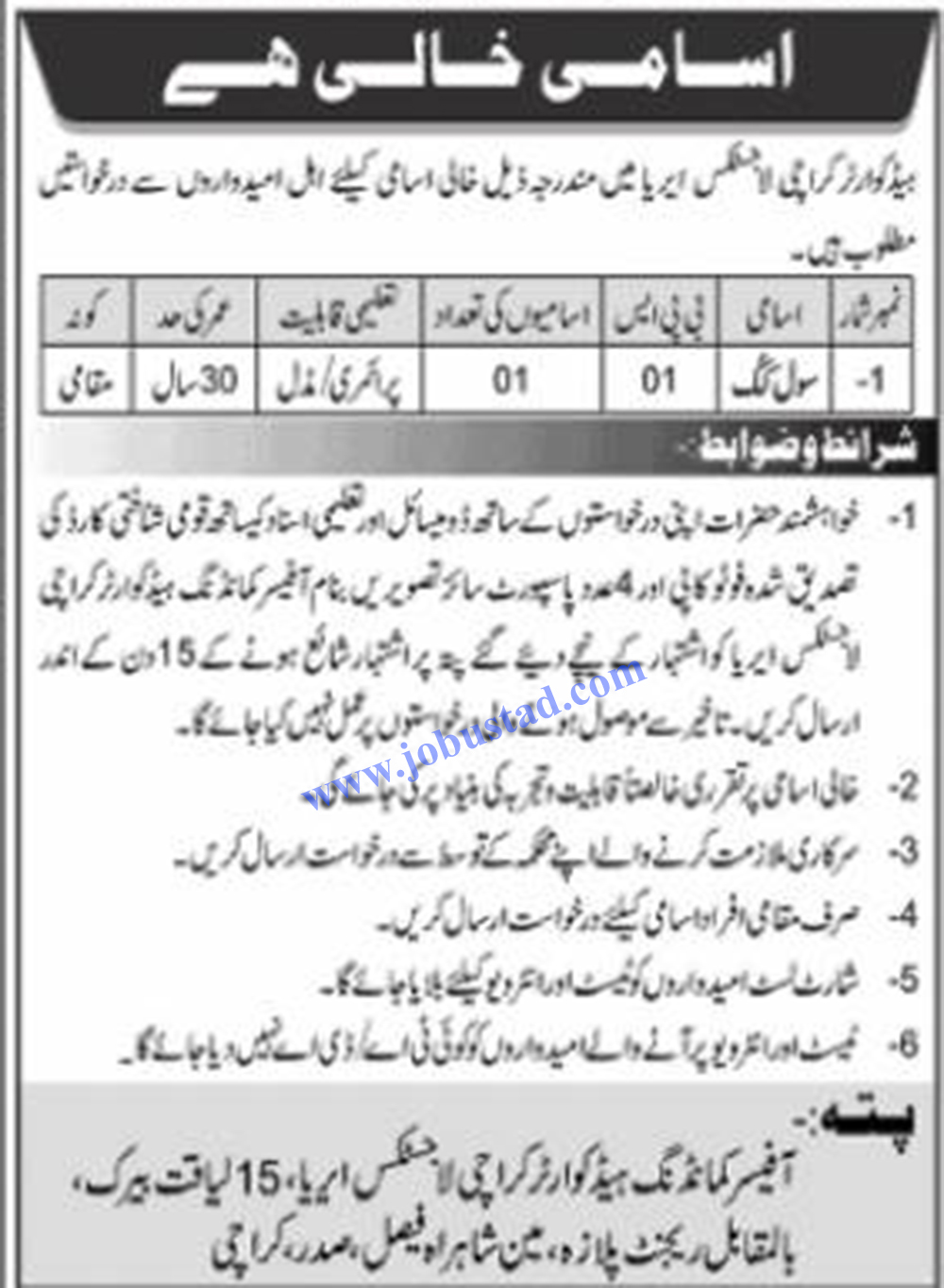
Purchasing Managers, also known as Materials Managers, are responsible for sourcing and coordinating all purchasing activities. They are responsible for coordinating all purchasing activities with suppliers and vendors. They should be knowledgeable about how to improve the company's purchasing processes. They must also be able and willing to negotiate the best deals possible for the company.
Purchaser managers must also keep accurate and current purchasing records. They analyse customer requirements, assess financial reports, evaluate vendor capabilities and evaluate price trends. They also coordinate purchasing activities with other departments. They might be required to work extra hours if supplies are needed from overseas markets.
Coordinate and manage inventory, logistics and other activities. They help determine the best buying method and ensure that all items purchased meet company standards. They work closely with their staff to make sure that they are able to manage their budgets. They also negotiate and search for the best vendors.
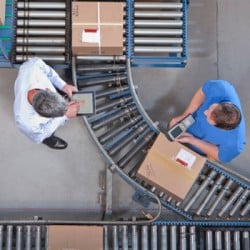
The time schedules and performance of purchasing employees are also managed by purchasing managers. They also assess the quality of purchased goods and the delivery time. They also contact sellers and suppliers and visit their distribution centers. They ensure that all suppliers adhere to the contract terms. They may also have responsibility for team building and disciplinary issues.
The Purchasing Manager must be able to communicate effectively, use analytical skills and think strategically. They should be able analyze the impact of different products on the company. They must be able manage suppliers and their relationships. They must also be able to make business decisions and increase sales. They must also be capable of handling complicated purchases. They must be able to evaluate new vendors, analyze their capabilities, and select the best vendor for the company.
The majority of purchasing managers need to have a bachelor's in business or another related field. A bachelor's degree in business or a related field is helpful. They will also need to be proficient in Microsoft Office as well as other programs.
A good purchasing manager will be able negotiate the best contracts and find the best deals. They must also be able coordinate all purchasing activities, manage inventories and track supplier and vendor performance. They should also be able manage a team.
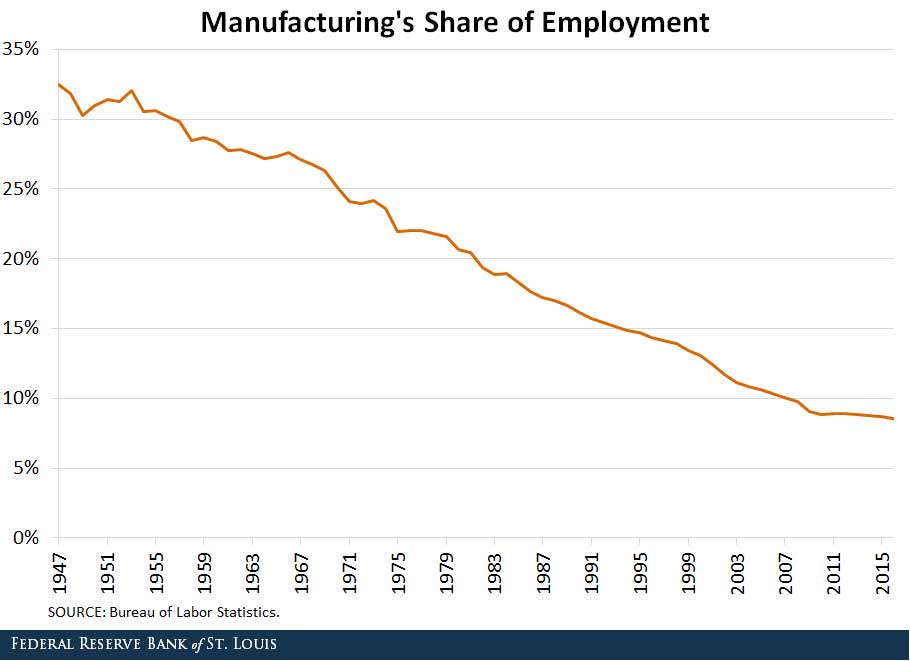
The purchase manager job description should also be able to mention how purchasing is essential to the company's success. It should also highlight how important it for the company's to be ahead of the game. It should also mention how the company values its employees' work-life balance. The call to action should be included to encourage applicants to apply.
Sometimes, the Purchasing Manager may be required to work overtime in order to purchase equipment and materials for an international marketplace. They might also need to meet with sellers and vendors or attend trade shows.
FAQ
Can certain manufacturing steps be automated?
Yes! Yes. Automation has been around since ancient time. The wheel was invented by the Egyptians thousands of years ago. Nowadays, we use robots for assembly lines.
Actually, robotics can be used in manufacturing for many purposes. These include:
-
Assembly line robots
-
Robot welding
-
Robot painting
-
Robotics inspection
-
Robots that make products
Automation can be applied to manufacturing in many other ways. 3D printing is a way to make custom products quickly and without waiting weeks or months for them to be manufactured.
How can manufacturing efficiency improved?
The first step is to determine the key factors that impact production time. We then need to figure out how to improve these variables. If you don’t know how to start, look at which factors have the greatest impact upon production time. Once you've identified them, try to find solutions for each of those factors.
What is manufacturing and logistics?
Manufacturing is the process of creating goods from raw materials by using machines and processes. Logistics is the management of all aspects of supply chain activities, including procurement, production planning, distribution, warehousing, inventory control, transportation, and customer service. As a broad term, manufacturing and logistics often refer to both the creation and delivery of products.
What types of jobs can you find in logistics
Logistics can offer many different jobs. Here are some:
-
Warehouse workers - They load and unload trucks and pallets.
-
Transportation drivers: They drive trucks and trailers and deliver goods and make pick-ups.
-
Freight handlers are people who sort and pack freight into warehouses.
-
Inventory managers – These people oversee inventory at warehouses.
-
Sales representatives: They sell products to customers.
-
Logistics coordinators - They plan and organize logistics operations.
-
Purchasing agents are those who purchase goods and services for the company.
-
Customer service representatives are available to answer customer calls and emails.
-
Shipping clerks: They process shipping requests and issue bills.
-
Order fillers: They fill orders based off what has been ordered and shipped.
-
Quality control inspectors – They inspect incoming and outgoing products to ensure that there are no defects.
-
Others - There are many other types of jobs available in logistics, such as transportation supervisors, cargo specialists, etc.
What skills are required to be a production manager?
Production planners must be flexible, organized, and able handle multiple tasks. You must also be able to communicate effectively with clients and colleagues.
What are the four types of manufacturing?
Manufacturing is the process of transforming raw materials into useful products using machines and processes. Manufacturing involves many activities, including designing, building, testing and packaging, shipping, selling, service, and so on.
What is the responsibility for a logistics manager
Logistics managers ensure that goods arrive on time and are unharmed. This is accomplished by using the experience and knowledge gained from working with company products. He/she must also ensure sufficient stock to meet the demand.
Statistics
- It's estimated that 10.8% of the U.S. GDP in 2020 was contributed to manufacturing. (investopedia.com)
- [54][55] These are the top 50 countries by the total value of manufacturing output in US dollars for its noted year according to World Bank.[56] (en.wikipedia.org)
- Many factories witnessed a 30% increase in output due to the shift to electric motors. (en.wikipedia.org)
- You can multiply the result by 100 to get the total percent of monthly overhead. (investopedia.com)
- Job #1 is delivering the ordered product according to specifications: color, size, brand, and quantity. (netsuite.com)
External Links
How To
How to Use 5S to Increase Productivity in Manufacturing
5S stands for "Sort", "Set In Order", "Standardize", "Separate" and "Store". Toyota Motor Corporation created the 5S methodology in 1954. It improves the work environment and helps companies to achieve greater efficiency.
This method has the basic goal of standardizing production processes to make them repeatable. Cleaning, sorting and packing are all done daily. Through these actions, workers can perform their jobs more efficiently because they know what to expect from them.
Implementing 5S involves five steps: Sort, Set in Order, Standardize Separate, Store, and Each step requires a different action, which increases efficiency. You can make it easy for people to find things later by sorting them. When you set items in an order, you put items together. Once you have separated your inventory into groups and organized them, you will store these groups in easily accessible containers. You can also label your containers to ensure everything is properly labeled.
Employees will need to be more critical about their work. Employees need to be able understand their motivations and discover alternative ways to do them. They must learn new skills and techniques in order to implement the 5S system.
The 5S method not only increases efficiency but also boosts morale and teamwork. They will feel motivated to strive for higher levels of efficiency once they start to see results.