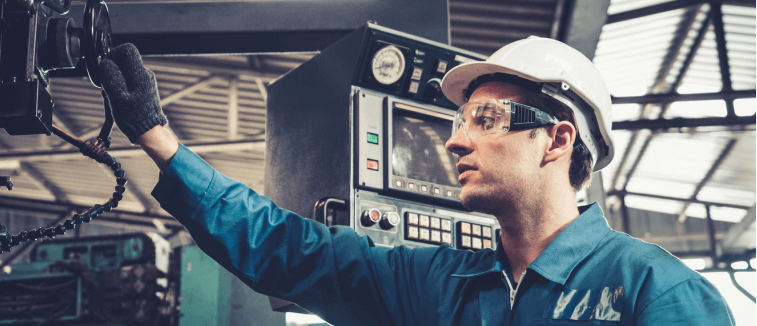
Throughout the years, global supply chains have undergone several changes. They have gone from being an industrial problem into a serious economic problem. It's a good idea keep track of new developments. Global supply chains can be complex and interconnected in many ways.
Global value chains combine capital, flows and intangibles. They are the result of economies, specialization, long-standing relationships, scale, and relationships. Some value chains are capital-intensive while others are more localized.
Global supply chains are becoming more complex, dynamic, and multidimensional. They are vital for the functioning of economies and global trade. They are also vulnerable to disruptions. These disruptions can be short-term or permanent. To counter these disruptions, it is important to create a flexible, resilient, and diversified supply chain. This requires a comprehensive approach including strategic initiatives and risk management. It is important to identify and assess the greatest challenges in order to build a supply chain that can withstand any future storms.
Along with assessing the risk of disruptions in supply chains, companies must also take into account the risks associated to manufacturing, labor and materials. They should also simulate extreme supply-and-demand disruptions in order to determine their impact. They should also review their inventories of critical materials and make sure they have sufficient supply for foreseeable demand. To develop a resilient supply system, it requires a strategic approach. This could include prioritizing production, moving manufacturing to more flexible locations and improving supply chain technology.
The COVID-19 outbreak caused major disruptions to global supply networks. Some countries imposed reciprocal tariffs, while others imposed severe sanctions. These tariffs and sanctions increased trade frictions, making it more difficult for the United States and other countries to sell certain products. These disruptions have led to an increase in price inflation. These disruptions have led to increased price inflation, but they have also made companies aware of the fragility in their supply chains. They have forced them into a rethink on the design and implementation their supply chains.
The COVID-19 epidemic caused severe disruption in global supply chain operations, but the effects of the pandemic are still being felt. For example the Suez Canal blockage caused disruptions in supply chain for up to six weeks. This has also led to a dramatic increase in freight costs. In the UK, annual inflation has reached 9%.
It's hard to ignore the fact that the United States and China are facing a trade war. Supply chain managers need to question why they rely so heavily on outsourced networks. They must consider the risks associated to labor shortages as a result of economic shocks. Leaders in supply chains should also be aware of the potential benefits of cross-border finance as well as regulation that can help expand global integration.
Despite all the chaos, the world continues to be a deeply interconnected place. Firms who are willing to adopt a more holistic view of their supply chains will reap the benefits of global integration.
FAQ
What is the responsibility of a logistics manager?
Logistics managers ensure that goods arrive on time and are unharmed. This is done using his/her knowledge of the company's products. He/she should make sure that enough stock is on hand to meet the demands.
What are the products of logistics?
Logistics are the activities involved in moving goods from point A to point B.
These include all aspects related to transport such as packaging, loading and transporting, storing, transporting, unloading and warehousing inventory management, customer service. Distribution, returns, recycling are some of the options.
Logisticians make sure that the right product arrives at the right place at the correct time and in safe conditions. They assist companies with their supply chain efficiency through information on demand forecasts. Stock levels, production times, and availability.
They also keep track of shipments in transit, monitor quality standards, perform inventories and order replenishment, coordinate with suppliers and vendors, and provide support services for sales and marketing.
Why automate your warehouse?
Modern warehouses have become more dependent on automation. The rise of e-commerce has led to increased demand for faster delivery times and more efficient processes.
Warehouses must be able to quickly adapt to changing demands. Technology investment is necessary to enable warehouses to respond quickly to changing demands. Automating warehouses has many benefits. Here are some of the reasons automation is worth your investment:
-
Increases throughput/productivity
-
Reduces errors
-
Increases accuracy
-
Safety enhancements
-
Eliminates bottlenecks
-
Allows companies to scale more easily
-
Workers are more productive
-
Gives you visibility into all that is happening in your warehouse
-
Enhances customer experience
-
Improves employee satisfaction
-
It reduces downtime, and increases uptime
-
Quality products delivered on time
-
Human error can be eliminated
-
It ensures compliance with regulations
How does a production planner differ from a project manager?
The difference between a product planner and project manager is that a planer is typically the one who organizes and plans the entire project. A production planner, however, is mostly involved in the planning stages.
What type of jobs is there in logistics
There are many kinds of jobs available within logistics. Some of them are:
-
Warehouse workers - They load trucks and pallets.
-
Transportation drivers – These drivers drive trucks and wagons to transport goods and pick up the goods.
-
Freight handlers – They sort and package freight at warehouses.
-
Inventory managers - They oversee the inventory of goods in warehouses.
-
Sales reps are people who sell products to customers.
-
Logistics coordinators: They plan and manage logistics operations.
-
Purchasing agents are those who purchase goods and services for the company.
-
Customer service representatives - Answer calls and email from customers.
-
Shipping clerks: They process shipping requests and issue bills.
-
Order fillers – They fill orders based upon what was ordered and shipped.
-
Quality control inspectors - They check incoming and outgoing products for defects.
-
Other - Logistics has many other job opportunities, including transportation supervisors, logistics specialists, and cargo specialists.
What does the term manufacturing industries mean?
Manufacturing Industries are companies that manufacture products. These products are sold to consumers. These companies use a variety processes such as distribution, retailing and management to accomplish their purpose. They create goods from raw materials, using machines and various other equipment. This covers all types of manufactured goods including clothing, food, building supplies and furniture, as well as electronics, tools, machinery, vehicles and pharmaceuticals.
Statistics
- It's estimated that 10.8% of the U.S. GDP in 2020 was contributed to manufacturing. (investopedia.com)
- According to the United Nations Industrial Development Organization (UNIDO), China is the top manufacturer worldwide by 2019 output, producing 28.7% of the total global manufacturing output, followed by the United States, Japan, Germany, and India.[52][53] (en.wikipedia.org)
- Job #1 is delivering the ordered product according to specifications: color, size, brand, and quantity. (netsuite.com)
- In 2021, an estimated 12.1 million Americans work in the manufacturing sector.6 (investopedia.com)
- In the United States, for example, manufacturing makes up 15% of the economic output. (twi-global.com)
External Links
How To
How to use Lean Manufacturing in the production of goods
Lean manufacturing refers to a method of managing that seeks to improve efficiency and decrease waste. It was created in Japan by Taiichi Ohno during the 1970s and 80s. He received the Toyota Production System award (TPS), from Kanji Toyoda, founder of TPS. Michael L. Watkins published the book "The Machine That Changed the World", which was the first to be published about lean manufacturing.
Lean manufacturing is often defined as a set of principles used to improve the quality, speed, and cost of products and services. It emphasizes eliminating waste and defects throughout the value stream. Lean manufacturing can be described as just-in–time (JIT), total productive maintenance, zero defect (TPM), or even 5S. Lean manufacturing is about eliminating activities that do not add value, such as inspection, rework, and waiting.
In addition to improving product quality and reducing costs, lean manufacturing helps companies achieve their goals faster and reduces employee turnover. Lean manufacturing can be used to manage all aspects of the value chain. Customers, suppliers, distributors, retailers and employees are all included. Lean manufacturing is widely practiced in many industries around the world. For example, Toyota's philosophy underpins its success in automobiles, electronics, appliances, healthcare, chemical engineering, aerospace, paper, food, etc.
Five principles are the basis of lean manufacturing:
-
Define Value- Identify the added value your company brings to society. What makes you stand out from your competitors?
-
Reduce waste - Get rid of any activity that does not add value to the supply chain.
-
Create Flow - Make sure work runs smoothly without interruptions.
-
Standardize and simplify – Make processes as repeatable and consistent as possible.
-
Develop Relationships: Establish personal relationships both with internal and external stakeholders.
Lean manufacturing isn’t new, but it has seen a renewed interest since 2008 due to the global financial crisis. Many businesses have adopted lean manufacturing techniques to help them become more competitive. Some economists even believe that lean manufacturing can be a key factor in economic recovery.
With many benefits, lean manufacturing is becoming more common in the automotive industry. These include higher customer satisfaction, lower inventory levels, lower operating expenses, greater productivity, and improved overall safety.
You can apply Lean Manufacturing to virtually any aspect of your organization. Because it makes sure that all value chains are efficient and effectively managed, Lean Manufacturing is particularly helpful for organizations.
There are three main types of lean manufacturing:
-
Just-in-Time Manufacturing (JIT): This type of lean manufacturing is commonly referred to as "pull systems." JIT refers to a system in which components are assembled at the point of use instead of being produced ahead of time. This approach is designed to reduce lead times and increase the availability of components. It also reduces inventory.
-
Zero Defects Manufacturing (ZDM),: ZDM is a system that ensures no defective units are left the manufacturing facility. Repairing a part that is damaged during assembly should be done, not scrapping. This applies to finished goods that may require minor repairs before shipment.
-
Continuous Improvement (CI),: Continuous improvement aims improve the efficiency and effectiveness of operations by continuously identifying issues and making changes to reduce waste. Continuous Improvement (CI) involves continuous improvement in processes, people, tools, and infrastructure.