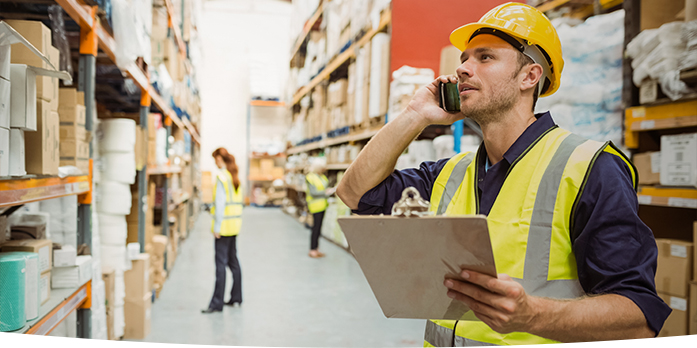
Lean training can be a powerful tool to reduce waste and streamline processes. It helps teams to work more efficiently and produces more product with less effort. It is essential that all employees in an organisation understand the benefits of lean. A training program can help you do this.
Lean training is often delivered in classrooms with a hands-on approach, combining classroom instruction and intensive hands-on experience. A typical course involves 4 to 8 hours per week of involvement by trainees. The goal is to prepare the participants to make suggestions for improvement. Participants can improve the performance within their organizations by using tools like value stream mapping (PDCA) and Plan-Do-Check-Act(PDCA).
Many companies choose to hire professional or in-house services for their lean training requirements. For example, Clemson University offers four different programs for their employees.
Lean training will help you and your company succeed. Companies are actually adopting this methodology more often. It is important to find a program that covers all aspects of lean.
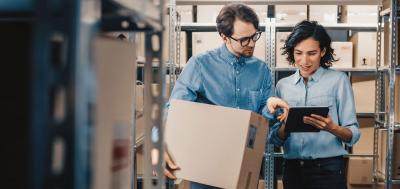
Training should begin with an introduction into lean. This workshop covers both the history and the principles of lean. It lasts approximately two hours. Additionally, you will learn lean tools like value stream maps and kanban. Furthermore, you will learn how to improve the customer experience.
Once you're comfortable with the basics, the Lean Thinking unit can be completed. Here, you'll learn about value stream mapping, error-proofing, and continuous flow. All of these methods are essential to identifying and reducing waste in your business.
Afterwards you'll be able to learn about Plan-Do-Check-Act. PDCA is a Lean improvement technique that most practitioners use. You will also be able to identify the root cause of your problems throughout the course.
You'll also learn how to create a lean plan. This will outline your current situation and the improvements you want to make. Upon completion, you'll receive a certificate for your efforts. To obtain your certification, you must pass a multi-choice exam using the Lean Management Courseware.
You'll be able to put the lessons you have learned into practice once you've completed the program. You'll learn how to lead and manage others, whether you're a technician, manager, or supervisor. You will ultimately be able see positive outcomes.
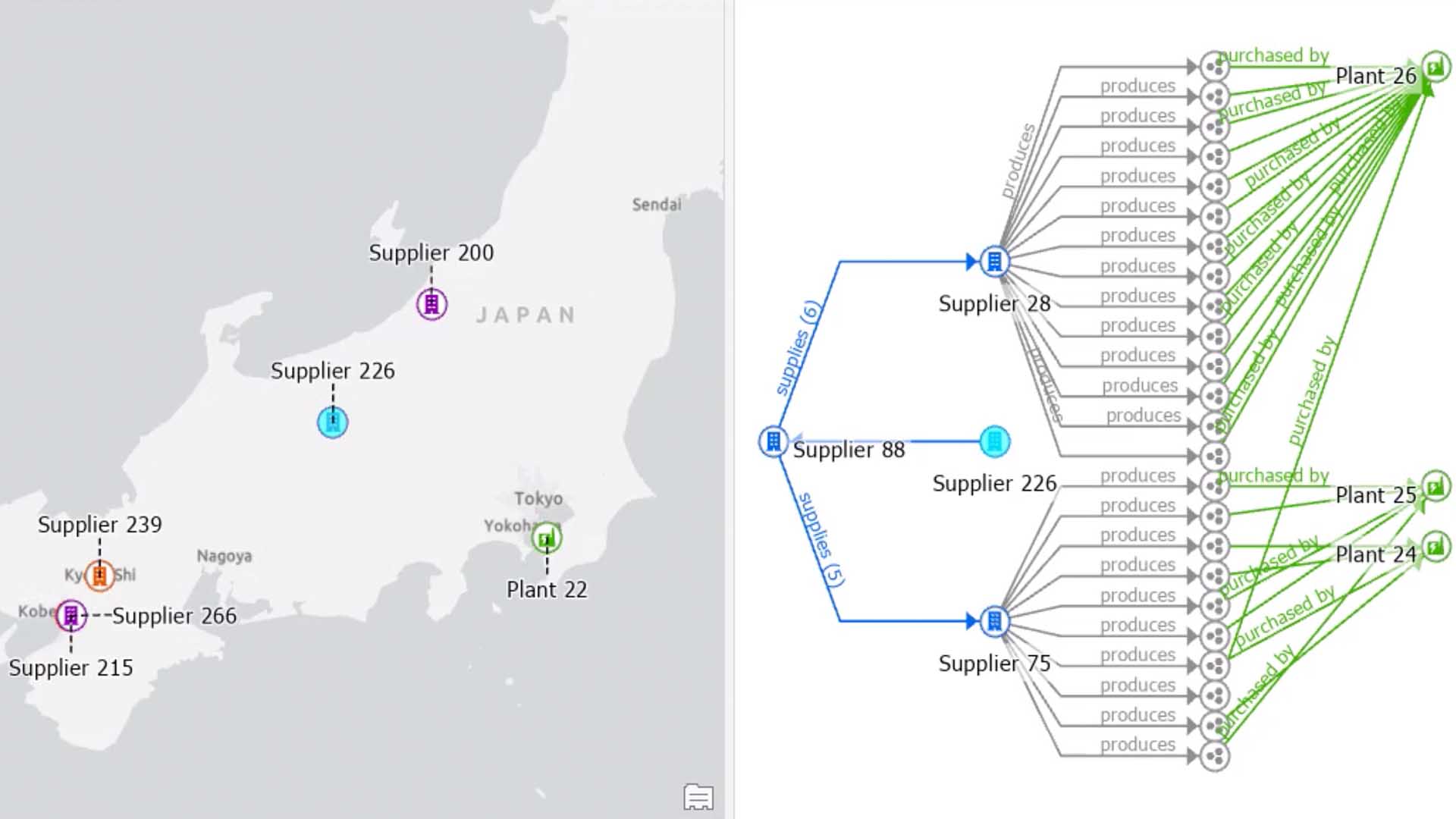
Finally, you will be eligible to earn your Green Belt Certification. April Saunders oversees the Lean training at Virginia University Medical Center. Her 12+ years of experience in the manufacturing industry means that she can teach Lean to her students.
Lean Fundamentals training programs are available in multiple languages. Participants are taught how to quickly implement Lean concepts in their workplaces. You can expect a positive impact on your workplace as a result of this class.
Whether you're interested in implementing lean in your organization, or you simply want to brush up on your skills, this workshop is a great start.
FAQ
What are manufacturing and logistics?
Manufacturing refers to the process of making goods using raw materials and machines. Logistics manages all aspects of the supply chain, including procurement, production planning and distribution, inventory control, transportation, customer service, and transport. Sometimes manufacturing and logistics are combined to refer to a wider term that includes both the process of creating products as well as their delivery to customers.
What is production planning?
Production Planning refers to the development of a plan for every aspect of production. This document will ensure everything is in order and ready to go when you need it. It should also provide information about how best to produce the best results while on set. This includes shooting schedules, locations, cast lists, crew details, and equipment requirements.
First, you need to plan what you want to film. You may have already decided where you would like to shoot, or maybe there are specific locations or sets that you want to use. Once you have determined your scenes and locations, it is time to start figuring out the elements that you will need for each scene. Perhaps you have decided that you need to buy a car but aren't sure which model. In this case, you could start looking up cars online to find out what models are available and then narrow your choices by choosing between different makes and models.
Once you have found the right vehicle, you can think about adding accessories. You might need to have people in the front seats. Maybe you need someone to move around in the back. You may want to change the interior's color from black or white. These questions will help guide you in determining the ideal look and feel for your car. Another thing you can do is think about what type of shots are desired. Do you want to film close-ups, or wider angles? Maybe you want to show your engine or the steering wheel. This will allow you to determine the type of car you want.
Once you have all the information, you are ready to create a plan. You can use a schedule to determine when and where you need it to be shot. A schedule for each day will detail when you should arrive at the location and when you need leave. Everyone will know what they need and when. It is possible to make arrangements in advance for additional staff if you are looking to hire. It's not worth paying someone to show up if you haven't told him.
Your schedule will also have to be adjusted to reflect the number of days required to film. Some projects can be completed in a matter of days or weeks. Others may take several days. When you are creating your schedule, you should always keep in mind whether you need more than one shot per day or not. Multiple takes of the same location will lead to higher costs and take more time. If you are unsure if you need multiple takes, it is better to err on the side of caution and shoot fewer takes rather than risk wasting money.
Budgeting is another crucial aspect of production plan. Setting a realistic budget is essential as it will allow you to work within your means. If you have to reduce your budget due to unexpected circumstances, you can always lower it later. But, don't underestimate how much money you'll spend. You will end up spending less money if you underestimate the cost of something.
Production planning can be a complex process. However, once you know how everything works together it will become easier to plan future projects.
What are the requirements to start a logistics business?
You need to have a lot of knowledge and skills to manage a successful logistic business. You must have good communication skills to interact effectively with your clients and suppliers. It is important to be able to analyse data and draw conclusions. You must be able to work well under pressure and handle stressful situations. You must be creative and innovative to develop new ideas to improve efficiency. You need to have strong leadership qualities to motivate team members and direct them towards achieving organizational goals.
It is important to be organized and efficient in order to meet tight deadlines.
Statistics
- Many factories witnessed a 30% increase in output due to the shift to electric motors. (en.wikipedia.org)
- (2:04) MTO is a production technique wherein products are customized according to customer specifications, and production only starts after an order is received. (oracle.com)
- It's estimated that 10.8% of the U.S. GDP in 2020 was contributed to manufacturing. (investopedia.com)
- In 2021, an estimated 12.1 million Americans work in the manufacturing sector.6 (investopedia.com)
- [54][55] These are the top 50 countries by the total value of manufacturing output in US dollars for its noted year according to World Bank.[56] (en.wikipedia.org)
External Links
How To
Six Sigma in Manufacturing:
Six Sigma is defined as "the application of statistical process control (SPC) techniques to achieve continuous improvement." Motorola's Quality Improvement Department, Tokyo, Japan, developed it in 1986. The basic idea behind Six Sigma is to improve quality by improving processes through standardization and eliminating defects. Many companies have adopted this method in recent years. They believe there is no such thing a perfect product or service. Six Sigma's main objective is to reduce variations from the production average. You can calculate the percentage of deviation from the norm by taking a sample of your product and comparing it to the average. If there is a significant deviation from the norm, you will know that something needs to change.
Understanding the nature of variability in your business is the first step to Six Sigma. Once you understand that, it is time to identify the sources of variation. It is important to identify whether the variations are random or systemic. Random variations are caused when people make mistakes. While systematic variations are caused outside of the process, they can occur. For example, if you're making widgets, and some of them fall off the assembly line, those would be considered random variations. You might notice that your widgets always fall apart at the same place every time you put them together.
After identifying the problem areas, you will need to devise solutions. It might mean changing the way you do business or redesigning it entirely. To verify that the changes have worked, you need to test them again. If they don't work you need to rework them and come up a better plan.