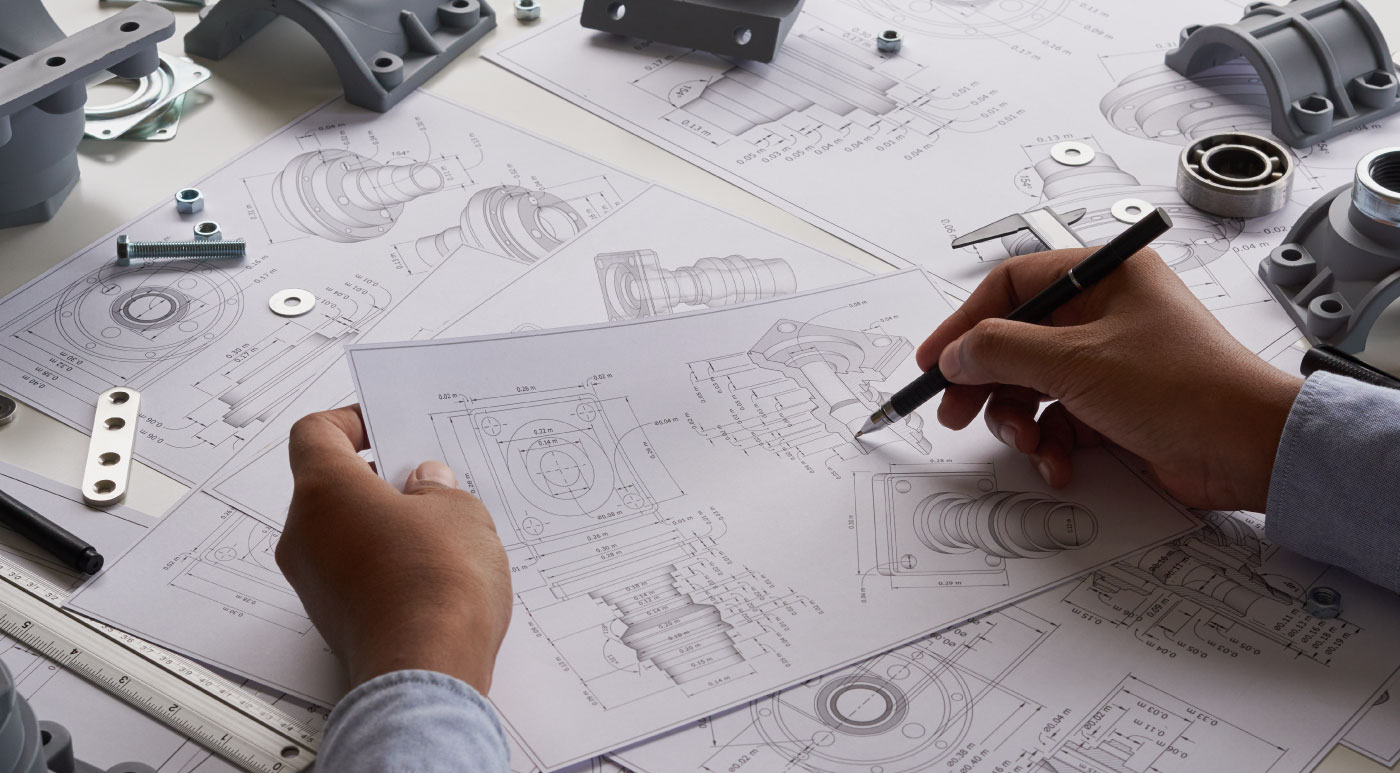
A degree in either architecture or engineering is required to be an engineer or architect manager. Many of these professionals work in offices but some also work on construction sites. Many of these professionals have a bachelor's degree or more in engineering or architecture, and extensive experience in this field. To complement their education, some choose to pursue a graduate degree in business administration. This profession offers many opportunities to grow. Consider a MBA to help you get a job as an architect or engineer manager.
Occupational outlook for architects and engineers managers
The outlook for employment of architectural and engineering managers is favorable. The number of job opportunities is expected to increase by approximately two percent over the next decade. This will be due in part to the growth of several industries. However, there will be fierce competition for jobs. You can find more information on this field at the O*NET site.
Architectural and engineering managers plan and direct activities in an engineering or architectural company. Using their knowledge of architecture, they are responsible for the planning, design, construction, and management of a wide range of activities. These activities may include the design, construction, and maintenance of large buildings, engineering research, or manufacturing sites. They also design new products. They are responsible for identifying the company's technical goals and creating detailed plans to help them achieve them.
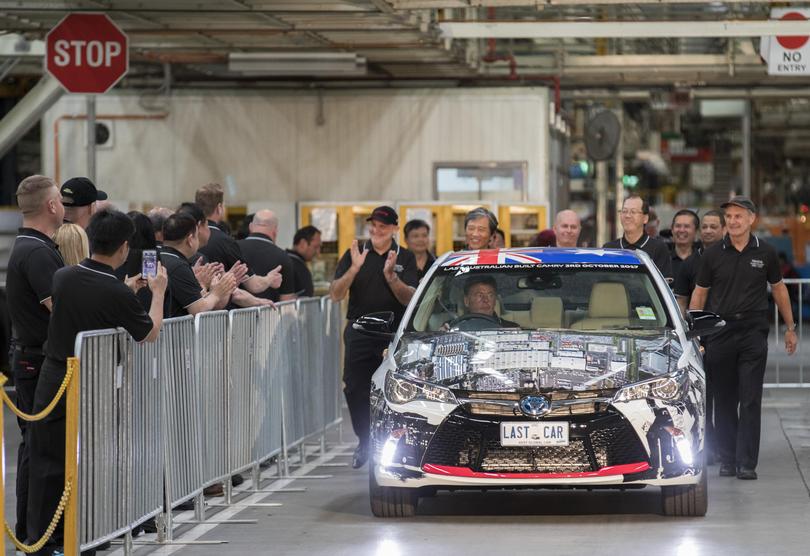
Applicants for this field usually have at least a master's degree in management. The type and level of the management job you are interested in will determine which program is the best. An engineering master's can prepare you for technical managerial positions while a master's of business administration can give you broader management skills. Each type of graduate program requires at least one calendar year.
Education necessary
Management in engineering and architecture requires a high level of education. They are responsible for supervising the day to day operations of engineering teams. They are responsible for providing oversight and training to employees. They may also suggest budgets for certain tasks and serve as mentors to employees. However, if you're considering a career in this field, consider getting a bachelor's degree in this field.
Although most of these managers hold a bachelor’s degree in architecture or engineering, some have earned advanced degrees in business administration and technology management. An MsEM or engineering management graduate degree will give you the managerial skills required for the job. You will need to have strong communication and analytical skills in addition to technical knowledge.
Engineer managers and architects have the responsibility for creating new projects and ensuring the highest quality product. They consider the environmental impact and the user's needs. These professionals prepare detailed plans and budgets based on technical specifications. They supervise teams to help them execute their projects.
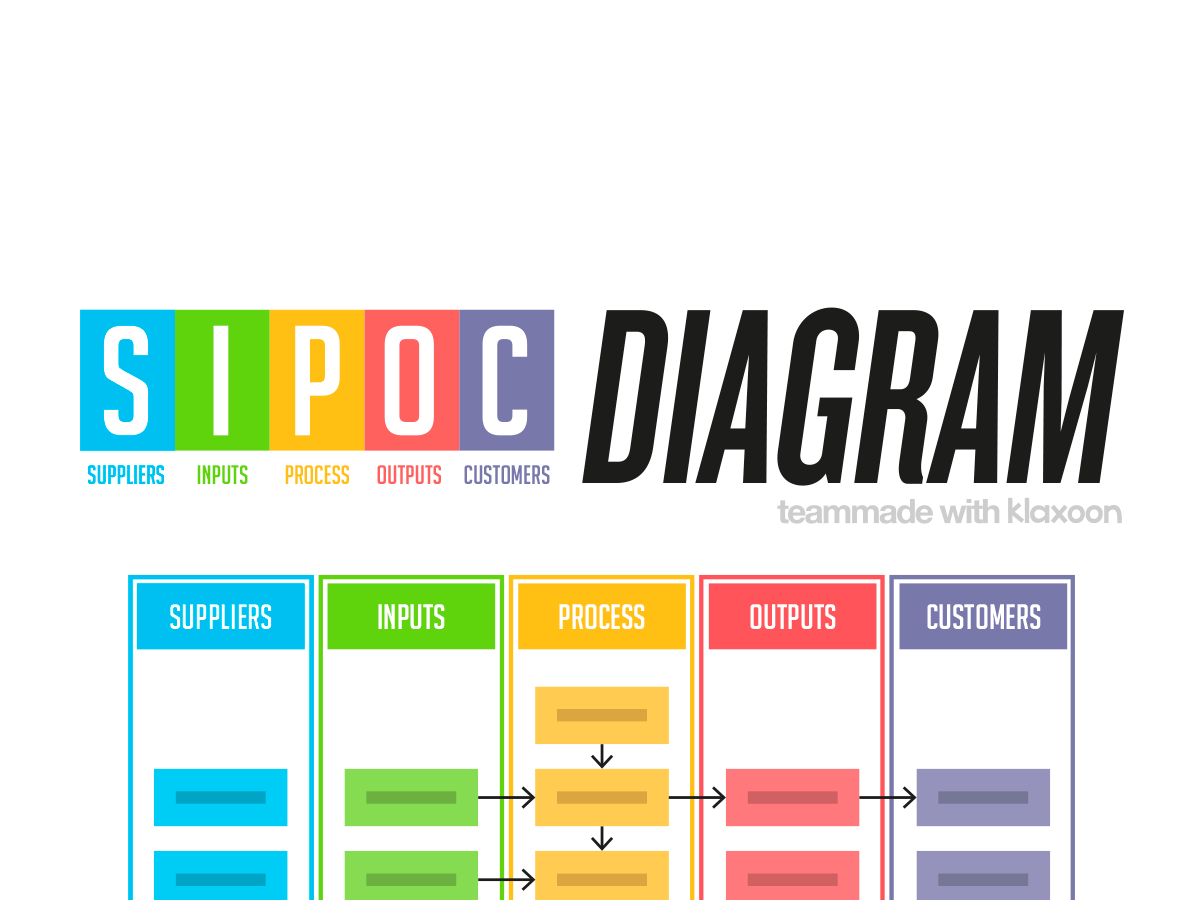
Earning potential
The earning potential for architectural and engineering managers is expected to increase 13 percent over the next decade. The number of jobs in this field is expected to increase in line with the growth of the engineering industry. Despite the fact that the number of jobs in this industry is expected to increase, competition will remain intense. However, the industry's growth rate won't be as fast as that of all other occupations.
The range in salary for this job depends on education and experience. A salary range of $75,190 for an entry-level job in this field is typical. Those with four to five years of experience can expect to make at least $104,800. On the other hand, people with at least ten year's experience can expect to earn around $156,620 per annum.
FAQ
What are the 7 Rs of logistics?
The acronym 7R's of Logistic is an acronym that stands for seven fundamental principles of logistics management. It was published in 2004 by the International Association of Business Logisticians as part of their "Seven Principles of Logistics Management" series.
The following letters form the acronym:
-
Responsible - to ensure that all actions are within the legal requirements and are not detrimental to others.
-
Reliable - You can have confidence that you will fulfill your promises.
-
Reasonable - make sure you use your resources well and don't waste them.
-
Realistic – Consider all aspects, including cost-effectiveness as well as environmental impact.
-
Respectful - Treat people fairly and equitably
-
Resourceful - look for opportunities to save money and increase productivity.
-
Recognizable is a company that provides customers with value-added solutions.
How important is automation in manufacturing?
Automation is important not only for manufacturers but also for service providers. It allows them to offer services faster and more efficiently. It reduces human errors and improves productivity, which in turn helps them lower their costs.
What is the responsibility of a production planner?
Production planners ensure that all project aspects are completed on time, within budget and within the scope. They also ensure the quality of the product and service meets the client's requirements.
Statistics
- (2:04) MTO is a production technique wherein products are customized according to customer specifications, and production only starts after an order is received. (oracle.com)
- In 2021, an estimated 12.1 million Americans work in the manufacturing sector.6 (investopedia.com)
- According to a Statista study, U.S. businesses spent $1.63 trillion on logistics in 2019, moving goods from origin to end user through various supply chain network segments. (netsuite.com)
- In the United States, for example, manufacturing makes up 15% of the economic output. (twi-global.com)
- According to the United Nations Industrial Development Organization (UNIDO), China is the top manufacturer worldwide by 2019 output, producing 28.7% of the total global manufacturing output, followed by the United States, Japan, Germany, and India.[52][53] (en.wikipedia.org)
External Links
How To
How to use lean manufacturing in the production of goods
Lean manufacturing (or lean manufacturing) is a style of management that aims to increase efficiency, reduce waste and improve performance through continuous improvement. It was developed by Taiichi Okono in Japan, during the 1970s & 1980s. TPS founder Kanji Takoda awarded him the Toyota Production System Award (TPS). The first book published on lean manufacturing was titled "The Machine That Changed the World" written by Michael L. Watkins and published in 1990.
Lean manufacturing, often described as a set and practice of principles, is aimed at improving the quality, speed, cost, and efficiency of products, services, and other activities. It emphasizes eliminating waste and defects throughout the value stream. Lean manufacturing is also known as just in time (JIT), zero defect total productive maintenance(TPM), and five-star (S). Lean manufacturing emphasizes reducing non-value-added activities like inspection, rework and waiting.
Lean manufacturing can help companies improve their product quality and reduce costs. Additionally, it helps them achieve their goals more quickly and reduces employee turnover. Lean manufacturing is considered one of the most effective ways to manage the entire value chain, including suppliers, customers, distributors, retailers, and employees. Lean manufacturing is widely used in many industries. Toyota's philosophy is the foundation of its success in automotives, electronics and appliances, healthcare, chemical engineers, aerospace, paper and food, among other industries.
Lean manufacturing includes five basic principles:
-
Define Value- Identify the added value your company brings to society. What makes you stand out from your competitors?
-
Reduce Waste - Eliminate any activity that doesn't add value along the supply chain.
-
Create Flow – Ensure that work flows smoothly throughout the process.
-
Standardize & Simplify - Make processes as consistent and repeatable as possible.
-
Develop Relationships: Establish personal relationships both with internal and external stakeholders.
Lean manufacturing is not a new concept, but it has been gaining popularity over the last few years due to a renewed interest in the economy following the global financial crisis of 2008. Many businesses have adopted lean manufacturing techniques to help them become more competitive. In fact, some economists believe that lean manufacturing will be an important factor in economic recovery.
Lean manufacturing, which has many benefits, is now a standard practice in the automotive industry. These benefits include increased customer satisfaction, reduced inventory levels and lower operating costs.
It can be applied to any aspect of an organisation. However, it is particularly useful when applied to the production side of an organization because it ensures that all steps in the value chain are efficient and effective.
There are three main types of lean manufacturing:
-
Just-in Time Manufacturing (JIT), also known as "pull system": This form of lean manufacturing is often referred to simply as "pull". JIT is a method in which components are assembled right at the moment of use, rather than being manufactured ahead of time. This approach aims to reduce lead times, increase the availability of parts, and reduce inventory.
-
Zero Defects Manufacturing, (ZDM): ZDM is focused on ensuring that no defective products leave the manufacturing facility. If a part needs to be fixed during the assembly line, it should be repaired rather than scrapped. This applies to finished products, which may need minor repairs before they are shipped.
-
Continuous Improvement (CI),: Continuous improvement aims improve the efficiency and effectiveness of operations by continuously identifying issues and making changes to reduce waste. Continuous Improvement (CI) involves continuous improvement in processes, people, tools, and infrastructure.