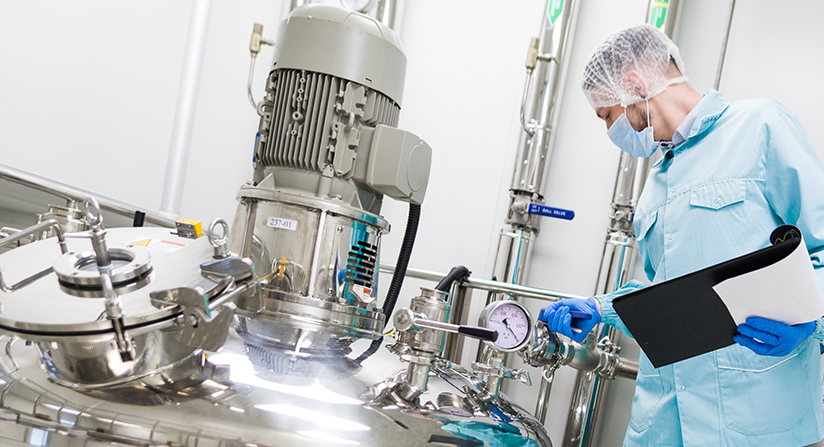
Lean is an abbreviation that is used in the manufacturing industry to describe a set of principles and techniques. It can also be a word of motivation that encourages the improvement of a process.
The Definition of Lean
When a business is aiming to be more efficient, it may have to eliminate certain activities that don't add value to the product or service it creates. This can include idle resources, unused equipment, or other resources that have not been used to the fullest extent.
This is the primary goal of lean production management, which is a method designed to eliminate waste. It is an ongoing process, so it will need to be constantly adjusted and improved.
The lean concept is based upon the idea that companies should put their focus on what their customers want, and give it priority over what they believe they need. This way, companies can avoid wasting money or time creating products that are not wanted by their customers.
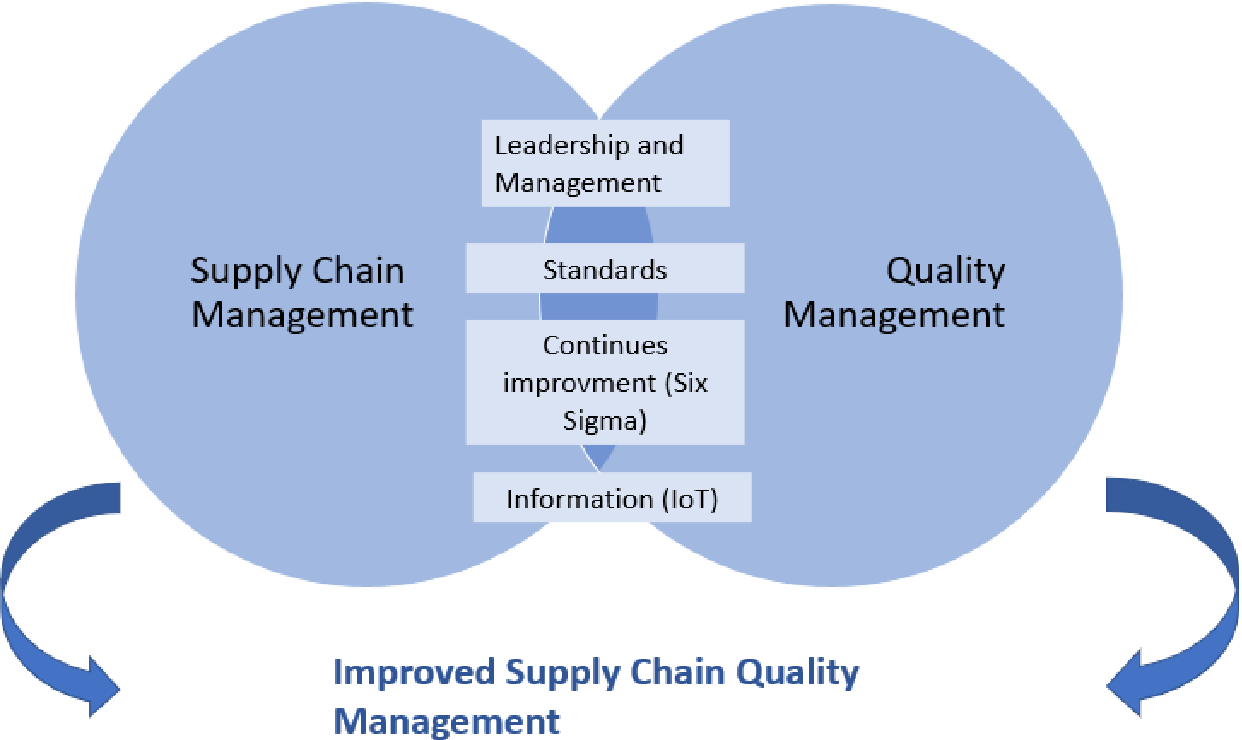
Note that lean principles can be applied to any industry or production method. This is why lean has become so popular across many different industries.
Lean Manufacturing, which is not new, is a method that emphasizes delivering products at the appropriate time in the proper quantity. This is a very effective tool for increasing the efficiency of the manufacturing process.
Defined by Toyota's founder, Toyoda, the concept of lean was based on eliminating waste from production. It includes defects and other waste that would be unacceptable to the customer.
Toyoda used a flow procedure to fix this problem. Workers would stop production to inspect parts and remove them if required. The company was able to optimize each stage of production to reduce defects and increase productivity.
Jidoka stops production automatically when there's an abnormality. Kaizen is a vital part of lean production.
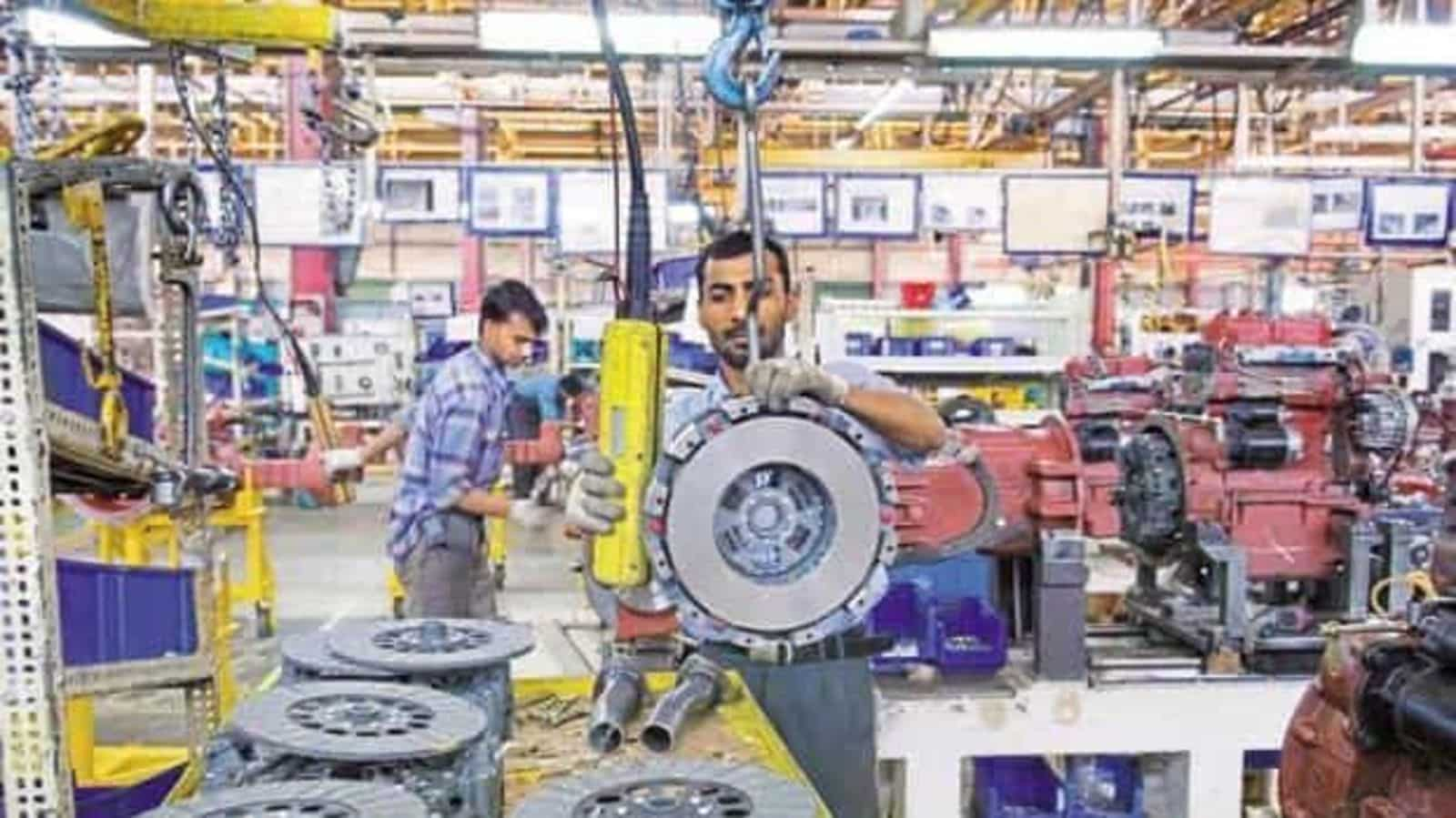
It is a continuous improvement process for any business process. This process can be applied in any area of business, whether it is the production of products.
Most people don't understand what lean really means. However, it is an excellent concept that can improve the way business runs. Lean helps companies save time and resources by improving their business processes. They can also build a good reputation among customers.
Lean isn't an isolated process; it is a system that must be improved on all levels within a company to achieve success. It's important to involve everyone in the process. This way, they can each contribute their own ideas and help ensure that things run smoothly.
FAQ
What are the main products of logistics?
Logistics refers to the movement of goods from one place to another.
They cover all aspects of transportation, such as packing, loading, transporting and unloading.
Logisticians ensure that the right product reaches the right place at the right time and under safe conditions. They help companies manage their supply chain efficiency by providing information on demand forecasts, stock levels, production schedules, and availability of raw materials.
They monitor shipments in transit, ensure quality standards, manage inventories, replenish orders, coordinate with suppliers and other vendors, and offer support services for sales, marketing, and customer service.
What are manufacturing and logistics?
Manufacturing is the act of producing goods from raw materials using machines and processes. Logistics is the management of all aspects of supply chain activities, including procurement, production planning, distribution, warehousing, inventory control, transportation, and customer service. Sometimes manufacturing and logistics are combined to refer to a wider term that includes both the process of creating products as well as their delivery to customers.
What are the 7 R's of logistics?
The acronym "7R's" of Logistics stands for seven principles that underpin logistics management. It was created by the International Association of Business Logisticians and published in 2004 under its "Seven Principles of Logistics Management".
The acronym is composed of the following letters.
-
Responsible – ensure that all actions are legal and don't cause harm to anyone else.
-
Reliable - You can have confidence that you will fulfill your promises.
-
Reasonable - use resources efficiently and don't waste them.
-
Realistic – consider all aspects of operations, from cost-effectiveness to environmental impact.
-
Respectful - treat people fairly and equitably.
-
You are resourceful and look for ways to save money while increasing productivity.
-
Recognizable - provide customers with value-added services.
What skills should a production planner have?
Production planners must be flexible, organized, and able handle multiple tasks. You must also be able to communicate effectively with clients and colleagues.
What does it take to run a logistics business?
You need to have a lot of knowledge and skills to manage a successful logistic business. Good communication skills are essential to effectively communicate with your suppliers and clients. You need to understand how to analyze data and draw conclusions from it. You will need to be able handle pressure well and work in stressful situations. To improve efficiency, you must be innovative and creative. Strong leadership qualities are essential to motivate your team and help them achieve their organizational goals.
It is also important to be efficient and well organized in order meet deadlines.
Statistics
- [54][55] These are the top 50 countries by the total value of manufacturing output in US dollars for its noted year according to World Bank.[56] (en.wikipedia.org)
- Job #1 is delivering the ordered product according to specifications: color, size, brand, and quantity. (netsuite.com)
- You can multiply the result by 100 to get the total percent of monthly overhead. (investopedia.com)
- Many factories witnessed a 30% increase in output due to the shift to electric motors. (en.wikipedia.org)
- (2:04) MTO is a production technique wherein products are customized according to customer specifications, and production only starts after an order is received. (oracle.com)
External Links
How To
How to Use 5S to Increase Productivity in Manufacturing
5S stands as "Sort", Set In Order", Standardize", Separate" and "Store". Toyota Motor Corporation invented the 5S strategy in 1954. It allows companies to improve their work environment, thereby achieving greater efficiency.
This approach aims to standardize production procedures, making them predictable, repeatable, and easily measurable. It means tasks like cleaning, sorting or packing, labeling, and storing are done every day. Workers can be more productive by knowing what to expect.
Implementing 5S requires five steps. These are Sort, Set In Order, Standardize. Separate. And Store. Each step involves a different action which leads to increased efficiency. Sorting things makes it easier to find them later. When you set items in an order, you put items together. Once you have separated your inventory into groups and organized them, you will store these groups in easily accessible containers. You can also label your containers to ensure everything is properly labeled.
Employees will need to be more critical about their work. Employees need to understand the reasons they do certain jobs and determine if there is a better way. They will need to develop new skills and techniques in order for the 5S system to be implemented.
The 5S Method not only improves efficiency, but it also helps employees to be more productive and happier. They feel more motivated to work towards achieving greater efficiency as they see the results.