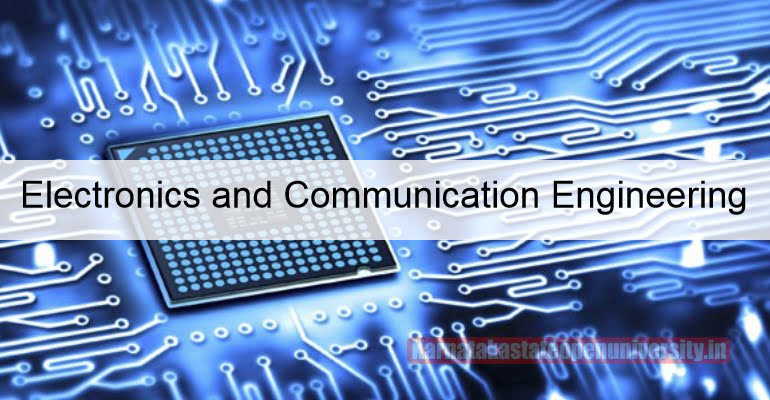
As an industrial design, you are responsible for designing innovative products that can be used in the home, office or industry. You'll find information about your job duties, education and training requirements, as well as the possible salary. This article will also explain how to get into this field and show you the many career options available. You will also learn about the potential benefits of this job and how to advance. Once you've completed your education, you'll be well on your way to a lucrative career in the design field.
Job duties
The Industrial designer is responsible for generating new products and services through the integration of art, business, and engineering skills. They have to balance functionality and aesthetics, and align with brand strategies. You must have experience as an Industrial Designer and a solid portfolio of design concepts. Industrial Designers will need to have strong computer-aided software skills and be creative in incorporating innovative technology into products.
Industrial Designers develop and implement design regulations as part of the job. They must possess excellent problem-solving and analytical skills, and be able to communicate design concepts to cross-functional groups. They should be able interact with engineers, create 3D models, and work with model shops. Industrial Designers should be proficient with Microsoft Office, Solidworks and Keyshot.
Education is necessary
Job seekers who are interested in a career as an industrial designer will benefit from having an educational background. Students can create an electronic portfolio to showcase their design skills through such programs. Industrial designers may also be able to earn a Master of Business Administration degree. This helps them improve their business acumen as well as better understand the limitations of products. Industrial designers use their analytical skills and reasoning to create innovative products and services.
The type of industrial design job desired will dictate the educational requirements. As a general rule, industrial designers need at least a bachelor's degree. Some schools offer an industrial design degree, but others don't. Candidates should take courses in business and design, as well as courses in engineering and mathematics. In addition, it is important to have a portfolio to show prospective employers. There are many career opportunities and advancements available in design jobs.
You have many career options
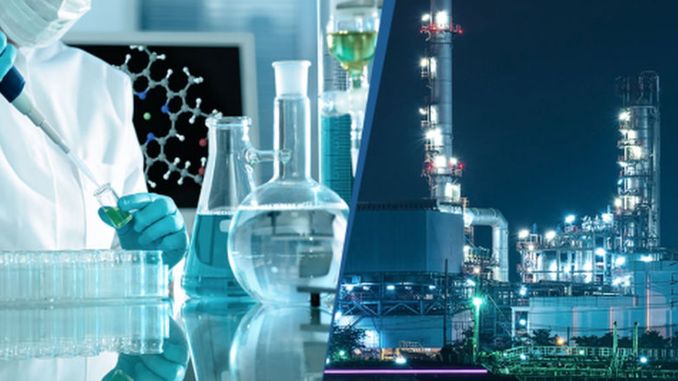
You can apply for entry-level jobs at design firms, manufacturing businesses, or in-house departments if you are interested in becoming an industrial design professional. The next step is to apply for design department heads or chief designers, and you will be able to move up the ladder. No matter what position you choose, it is important to use your design skills wherever possible. Listed below are a few of the most common entry-level positions available to industrial designers.
An industrial designer will usually have a bachelor's degree. Employers are more interested in candidates with a background of drawing and graphics. These skills can be useful for job applications. Employers might prefer candidates with CADD and 3D modeling skills in certain cases. An industrial designer, for example, is required to be proficient at drafting, rendering, and presenting the work to decision-makers, regardless of whether they are an engineer or an architect.
Salary
The salary of an industrial designer depends on their education and experience. An industrial designer who holds a Masters or Doctorate degree is likely to earn more than $75,000. A Bachelor's degree is less. However, many industrial designers progress to managerial positions. Here are some suggestions to help increase your salary. First, read through the job description thoroughly and understand your exact salary expectations.
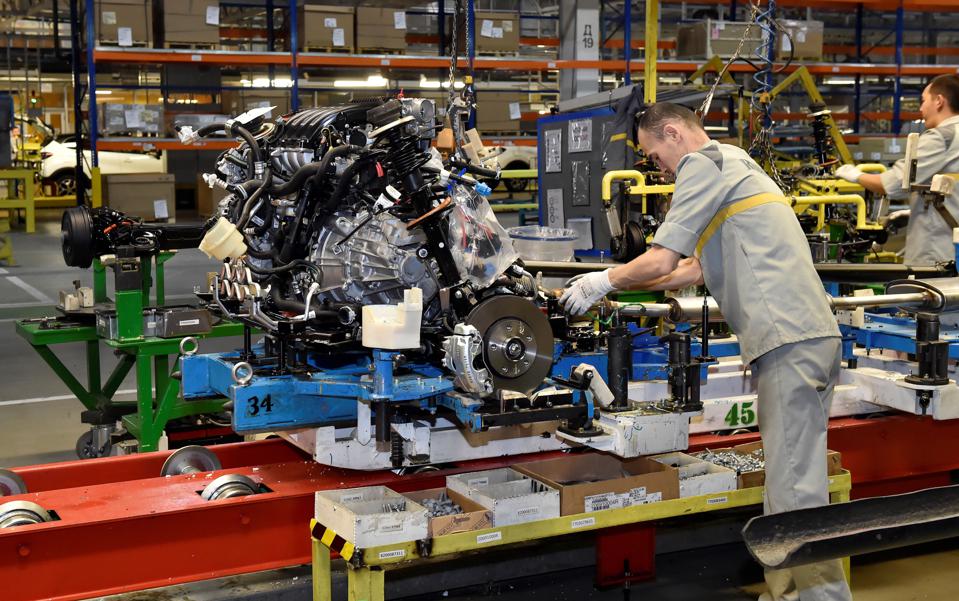
Industrial Designers earn an average annual salary of $62,315, though the actual amount can be much higher. According to the U.S. Bureau of Labor Statistics (USBoLS), the highest earners in this profession make $106,000 a YEAR. But, this is only an estimate. Your experience, job location, and industry will affect your salary. Once you have established your skills and location, you'll want to look at the compensation for your field.
FAQ
How does a Production Planner differ from a Project Manager?
The major difference between a Production Planner and a Project Manager is that a Project Manager is often the person responsible for organizing and planning the entire project. While a Production Planner is involved mainly in the planning stage,
What is the difference in Production Planning and Scheduling, you ask?
Production Planning (PP), is the process of deciding what production needs to take place at any given time. This is done through forecasting demand and identifying production capacities.
Scheduling refers the process by which tasks are assigned dates so that they can all be completed within the given timeframe.
What does it mean to warehouse?
A warehouse or storage facility is where goods are stored before they are sold. It can be an indoor space or an outdoor area. It may also be an indoor space or an outdoor area.
Are there ways to automate parts of manufacturing?
Yes! Yes. The Egyptians discovered the wheel thousands and years ago. To help us build assembly lines, we now have robots.
There are many applications for robotics in manufacturing today. They include:
-
Line robots
-
Robot welding
-
Robot painting
-
Robotics inspection
-
Robots create products
Manufacturing can also be automated in many other ways. For example, 3D printing allows us to make custom products without having to wait for weeks or months to get them manufactured.
Statistics
- (2:04) MTO is a production technique wherein products are customized according to customer specifications, and production only starts after an order is received. (oracle.com)
- Many factories witnessed a 30% increase in output due to the shift to electric motors. (en.wikipedia.org)
- [54][55] These are the top 50 countries by the total value of manufacturing output in US dollars for its noted year according to World Bank.[56] (en.wikipedia.org)
- In the United States, for example, manufacturing makes up 15% of the economic output. (twi-global.com)
- You can multiply the result by 100 to get the total percent of monthly overhead. (investopedia.com)
External Links
How To
How to use lean manufacturing in the production of goods
Lean manufacturing is a management style that aims to increase efficiency and reduce waste through continuous improvement. It was first developed in Japan in the 1970s/80s by Taiichi Ahno, who was awarded the Toyota Production System (TPS), award from KanjiToyoda, the founder of TPS. Michael L. Watkins published the original book on lean manufacturing, "The Machine That Changed the World," in 1990.
Lean manufacturing, often described as a set and practice of principles, is aimed at improving the quality, speed, cost, and efficiency of products, services, and other activities. It emphasizes eliminating waste and defects throughout the value stream. Lean manufacturing is also known as just in time (JIT), zero defect total productive maintenance(TPM), and five-star (S). Lean manufacturing is about eliminating activities that do not add value, such as inspection, rework, and waiting.
Lean manufacturing can help companies improve their product quality and reduce costs. Additionally, it helps them achieve their goals more quickly and reduces employee turnover. Lean manufacturing is considered one of the most effective ways to manage the entire value chain, including suppliers, customers, distributors, retailers, and employees. Lean manufacturing can be found in many industries. Toyota's philosophy is the foundation of its success in automotives, electronics and appliances, healthcare, chemical engineers, aerospace, paper and food, among other industries.
Five basic principles of Lean Manufacturing are included in lean manufacturing
-
Define Value - Determine the value that your business brings to society. Also, identify what sets you apart from your competitors.
-
Reduce waste - Get rid of any activity that does not add value to the supply chain.
-
Create Flow: Ensure that the work process flows without interruptions.
-
Standardize and Simplify – Make processes as consistent, repeatable, and as simple as possible.
-
Build Relationships- Develop personal relationships with both internal as well as external stakeholders.
Lean manufacturing is not a new concept, but it has been gaining popularity over the last few years due to a renewed interest in the economy following the global financial crisis of 2008. Many businesses have adopted lean manufacturing techniques to help them become more competitive. According to some economists, lean manufacturing could be a significant factor in the economic recovery.
Lean manufacturing is becoming a popular practice in automotive. It has many advantages. These include higher customer satisfaction, lower inventory levels, lower operating expenses, greater productivity, and improved overall safety.
You can apply Lean Manufacturing to virtually any aspect of your organization. Lean manufacturing is most useful in the production sector of an organisation because it ensures that each step in the value-chain is efficient and productive.
There are three main types:
-
Just-in Time Manufacturing, (JIT): This kind of lean manufacturing is also commonly known as "pull-systems." JIT refers to a system in which components are assembled at the point of use instead of being produced ahead of time. This strategy aims to decrease lead times, increase availability of parts and reduce inventory.
-
Zero Defects Manufacturing (ZDM),: ZDM is a system that ensures no defective units are left the manufacturing facility. You should repair any part that needs to be repaired during an assembly line. This applies to finished goods that may require minor repairs before shipment.
-
Continuous Improvement: Continuous Improvement aims to improve efficiency by continually identifying problems and making adjustments to eliminate or minimize waste. Continuous Improvement involves continuous improvement of processes.