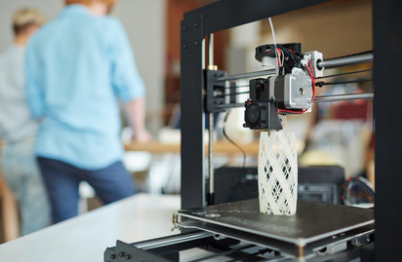
Journal impact factors
These journal impact factors in supply chains management can be used to compare the relative influence on supply chain management journals. These factors were calculated using data from 10 leading academic journals in supply chain management and the ISI Web of Science. The results allow us comparisons and contrasts between the relative influence on journals and their authors within the field.
Journal impact factors play an important role in evaluating a journal’s quality. A high-ranking journal is more likely to have high quality research because it attracts top-quality work. Journal impact factors include the number of citations that a journal receives as well the importance of the journals. Emerald Group Publishing Ltd., an English publishing company, is the Journal's publisher.
Scope of the journal
Journal supply chain management's scope includes a range of topics such as inventory management and transportation. Its mission is to create a dynamic forum for research-based information in these areas. These topics are welcome. This doesn't necessarily mean that every article submitted must be published in the journal.
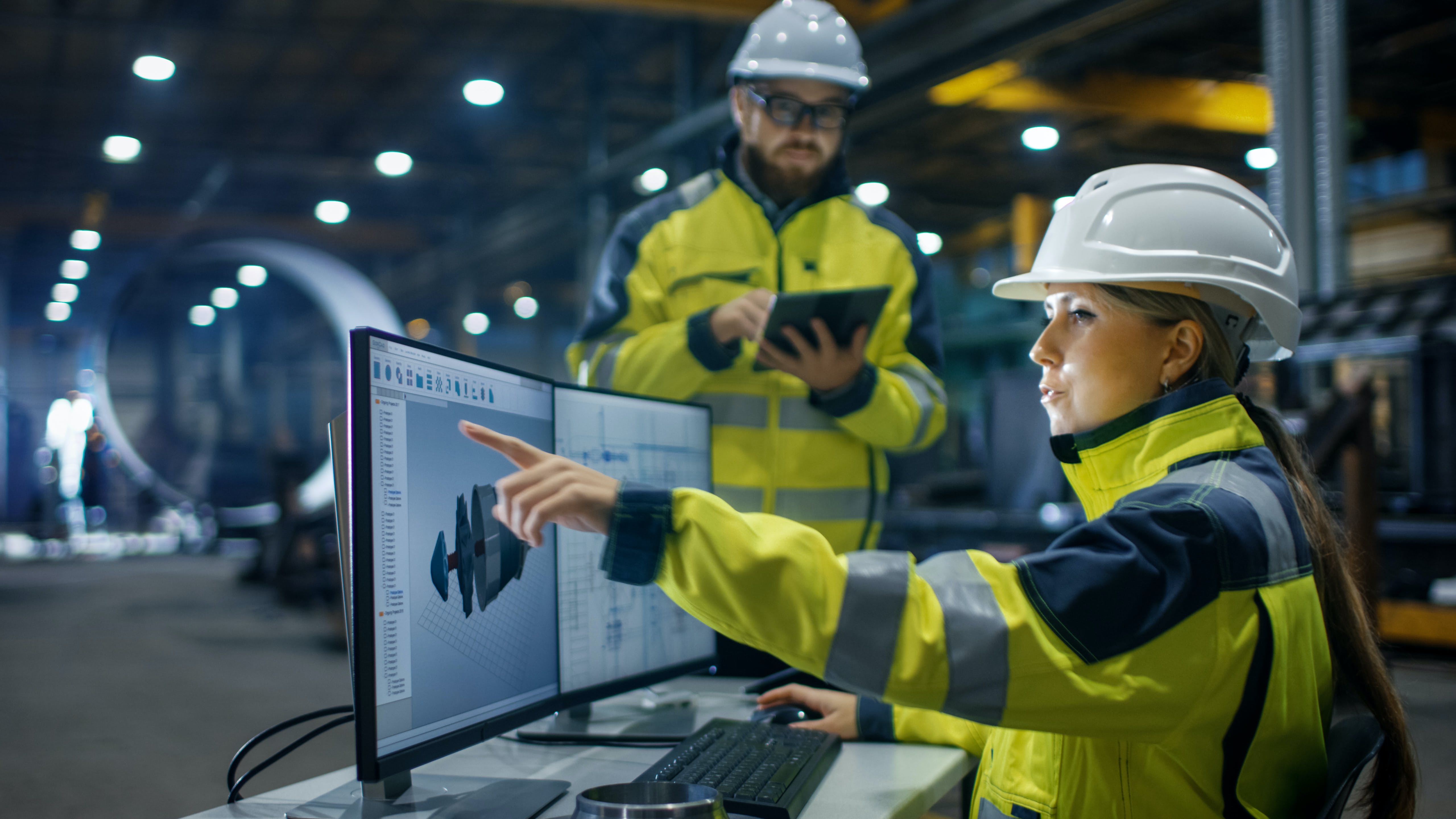
SCMij, an international journal, publishes research that advances supply chain management. It provides a forum for discussion of empirical and theoretical research. It is open for submissions from practitioners and scholars.
Editorial Board
A journal's Editorial Board is an organization that reviews the quality of scientific publications. The Editorial Board is made up of distinguished scientists from various fields. The Board maintains confidentiality of manuscript information, and is bound to the editorial codes of conduct. The journal is registered in many international scientific databases and repositories, and is searchable through major search engines.
The Editorial Board of the Journal of Supply Chain Management is a group of experts who focus on supply chain management, procurement, and logistics. Every article submitted to publication is peer reviewed to ensure it is practical and relevant.
Authors of articles published in the journal
The Journal of Supply Chain Management invites submissions by supply chain management, logistics, or procurement professionals. The journal publishes original research articles and review articles that relate to supply chain management. The articles should not exceed three thousand words and must discuss new techniques or solutions to problems.
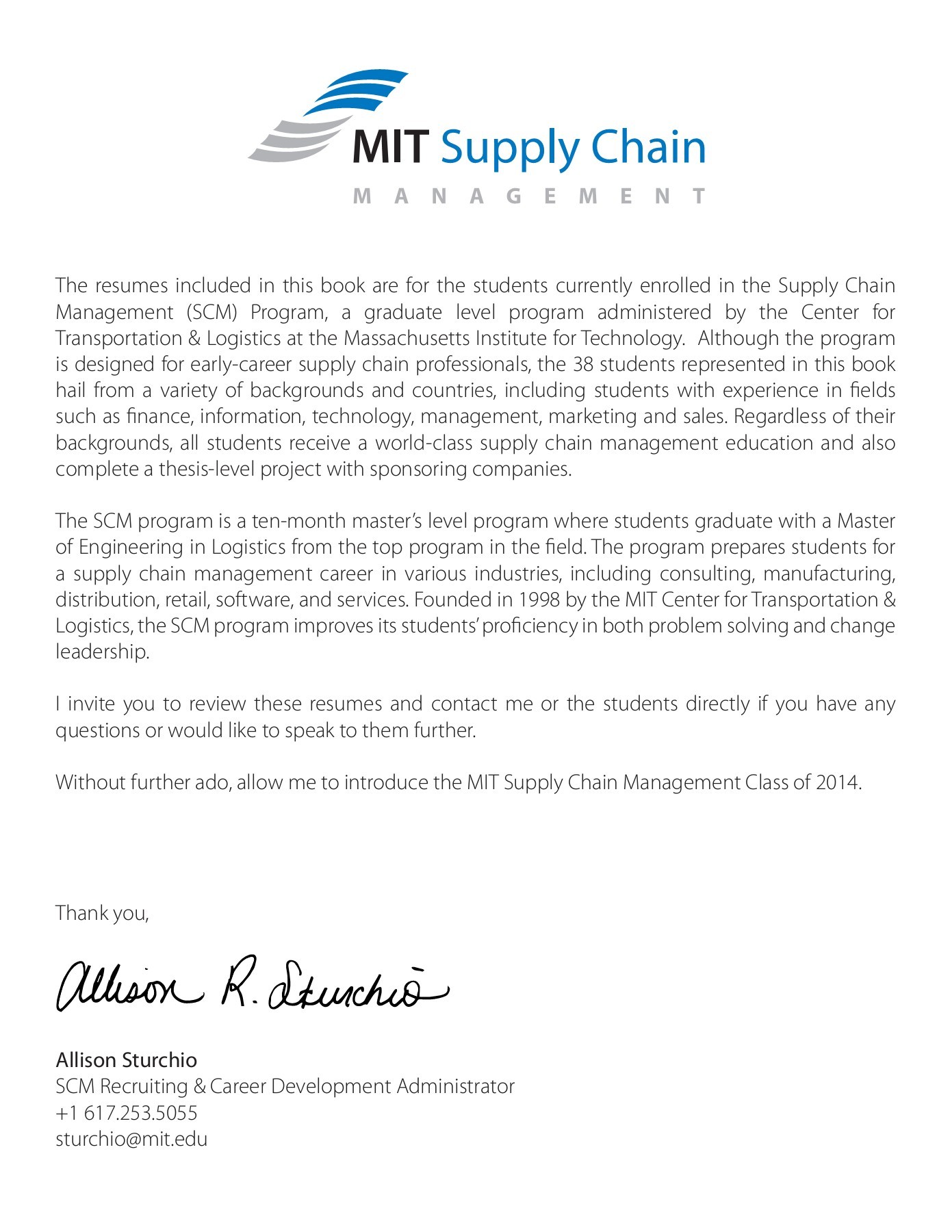
Articles may be submitted online. They can either be submitted in plain text or as separate files that include illustrations. Authors should make sure that their contact details are accurate, and the article should include the most recent address and e-mail. The journal does not charge for publication or submission.
The number of articles that are published each year in the journal
The Journal of Supply Chain Management has articles published in several journals. The journal's h index is high, which means that it is high in productivity and has high citation impacts. The total ISSN for the journal is 15232409, which corresponds to the International Standard Serial Number.
This journal publishes articles written by academics and practitioners in the field. The journal's articles are thought-provoking on supply chain operations. It also publishes features and columns from supply chain practitioners and industry analysts. It also publishes many case studies of companies and their supply chains.
FAQ
What is production planning?
Production Planning involves developing a plan for all aspects of the production, including scheduling, budgeting, casting, crew, location, equipment, props, etc. This document aims to ensure that everything is planned and ready when you are ready to shoot. It should also contain information on achieving the best results on set. This includes shooting schedules, locations, cast lists, crew details, and equipment requirements.
It is important to first outline the type of film you would like to make. You may already know where you want the film to be shot, or perhaps you have specific locations and sets you wish to use. Once you have determined your scenes and locations, it is time to start figuring out the elements that you will need for each scene. Perhaps you have decided that you need to buy a car but aren't sure which model. In this case, you could start looking up cars online to find out what models are available and then narrow your choices by choosing between different makes and models.
After you have selected the car you want, you can begin to think about additional features. You might need to have people in the front seats. Or maybe you just need someone to push the car around. Perhaps you would like to change the interior colour from black to white. These questions will help you determine the exact look and feel of your car. The type of shots that you are looking for is another thing to consider. Are you going to be shooting close-ups? Or wide angles? Maybe you want to show your engine or the steering wheel. This will allow you to determine the type of car you want.
Once you have determined all of the above, you can move on to creating a schedule. You can create a schedule that will outline when you must start and finish your shoots. The schedule will show you when to get there, what time to leave, and when to return home. Everyone will know what they need and when. Hire extra staff by booking them ahead of time. It is not worth hiring someone who won’t show up because you didn’t tell him.
Also, consider how many days you will be filming your schedule. Some projects take only a few days while others can last several weeks. While creating your schedule, it is important to remember whether you will require more than one shot per day. Multiplying takes in the same area will result both in increased costs and a longer time. You can't be certain if you will need multiple takes so it is better not to shoot too many.
Budgeting is another important aspect of production planning. You will be able to manage your resources if you have a realistic budget. Keep in mind that you can always reduce your budget if you face unexpected difficulties. You shouldn't underestimate the amount you'll spend. If you underestimate the cost of something, you will have less money left after paying for other items.
Planning production is a tedious process. Once you have a good understanding of how everything works together, planning future projects becomes easy.
What are the 4 types of manufacturing?
Manufacturing is the process of transforming raw materials into useful products using machines and processes. It can involve many activities like designing, manufacturing, testing packaging, shipping, selling and servicing.
What makes a production planner different from a project manger?
The main difference between a production planner and a project manager is that a project manager is usually the person who plans and organizes the entire project, whereas a production planner is mainly involved in the planning stage of the project.
What is the job of a manufacturer manager?
A manufacturing manager has to ensure that all manufacturing processes work efficiently and effectively. They should be alert for any potential problems in the company and react accordingly.
They must also be able to communicate with sales and marketing departments.
They should also be knowledgeable about the latest trends in the industry so they can use this information for productivity and efficiency improvements.
Is automation important in manufacturing?
Automation is important not only for manufacturers but also for service providers. It enables them to provide services faster and more efficiently. They can also reduce their costs by reducing human error and improving productivity.
How can we reduce manufacturing overproduction?
Improved inventory management is the key to reducing overproduction. This would decrease the time that is spent on inefficient activities like purchasing, storing, or maintaining excess stock. This will allow us to free up resources for more productive tasks.
You can do this by adopting a Kanban method. A Kanbanboard is a visual tool that allows you to keep track of the work being done. Kanban systems allow work items to move through different states until they reach their final destination. Each state represents a different priority level.
As an example, if work is progressing from one stage of the process to another, then the current task is complete and can be transferred to the next. If a task is still in its beginning stages, it will continue to be so until it reaches the end.
This helps to keep work moving forward while ensuring that no work is left behind. Managers can see how much work has been done and the status of each task at any time with a Kanban Board. This allows them to adjust their workflows based on real-time information.
Lean manufacturing can also be used to reduce inventory levels. Lean manufacturing works to eliminate waste throughout every stage of the production chain. Anything that does nothing to add value to a product is waste. Here are some examples of common types.
-
Overproduction
-
Inventory
-
Packaging that is not necessary
-
Materials in excess
These ideas will help manufacturers increase efficiency and lower costs.
Statistics
- (2:04) MTO is a production technique wherein products are customized according to customer specifications, and production only starts after an order is received. (oracle.com)
- According to a Statista study, U.S. businesses spent $1.63 trillion on logistics in 2019, moving goods from origin to end user through various supply chain network segments. (netsuite.com)
- Many factories witnessed a 30% increase in output due to the shift to electric motors. (en.wikipedia.org)
- It's estimated that 10.8% of the U.S. GDP in 2020 was contributed to manufacturing. (investopedia.com)
- In 2021, an estimated 12.1 million Americans work in the manufacturing sector.6 (investopedia.com)
External Links
How To
Six Sigma and Manufacturing
Six Sigma refers to "the application and control of statistical processes (SPC) techniques in order to achieve continuous improvement." It was developed by Motorola's Quality Improvement Department at their plant in Tokyo, Japan, in 1986. Six Sigma's basic concept is to improve quality and eliminate defects through standardization. This method has been adopted by many companies in recent years as they believe there are no perfect products or services. Six Sigma's primary goal is to reduce variation from the average value of production. It is possible to measure the performance of your product against an average and find the percentage of time that it differs from the norm. If it is too large, it means that there are problems.
Understanding how your business' variability is a key step towards Six Sigma implementation is the first. Once you have this understanding, you will need to identify sources and causes of variation. Also, you will need to identify the sources of variation. Random variations occur when people do mistakes. Symmetrical variations are caused due to factors beyond the process. You could consider random variations if some widgets fall off the assembly lines. But if you notice that every widget you make falls apart at the exact same place each time, this would indicate that there is a problem.
After identifying the problem areas, you will need to devise solutions. You might need to change the way you work or completely redesign the process. After implementing the new changes, you should test them again to see if they worked. If they don't work you need to rework them and come up a better plan.