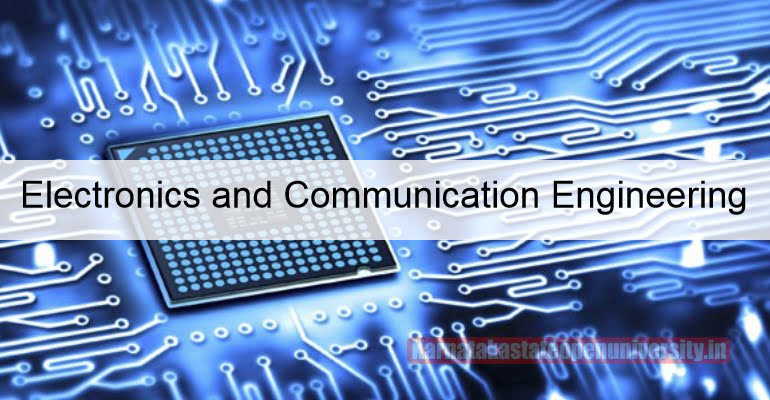
The average engineer salary can vary greatly depending on where you reside. In the United States, the highest paying state is Washington, followed by New York and California. It is also important to take into account the cost of living in a new place. For example, a salary of $96,640 could not cover all of your living expenses. Consider your monthly living costs before you consider applying for a job.
A median salary for an electrician is $96,640
According to U.S. Bureau of Labor Statistics an average salary for an engineer in electrical engineering is $96,640 per the year. This number may differ from one state to another. Salaries can also vary considerably within industry sectors. Electrical engineers make the most in retail trade. Education services makes the least. However, there are some important factors to consider when determining the average salary for an electrical engineer. Below is a breakdown showing the different salary levels of electrical engineers.
The design and development electrical equipment is the responsibility of electrical engineers. These engineers also oversee the installation and manufacturing of these products. This statistic covers all types and levels of electrical engineers. It does not include Computer Hardware Engineers (who make computers). According to the Bureau of Labor Statistics, employment of these professionals will grow by 7 percent by 2026. Although most electricians will be working in an office, they may travel to other types of locations for field work.
Biomedical engineers make a median income of $89 130
Biomedical engineers combine engineering knowledge with a knowledge of the human body in order to design and manufacture medical devices. Their background in biomechanics and mechanics helps them to understand how different medical products work and interact with the body. This knowledge can be used for the creation of artificial organs, medical devices and diagnostic tools.
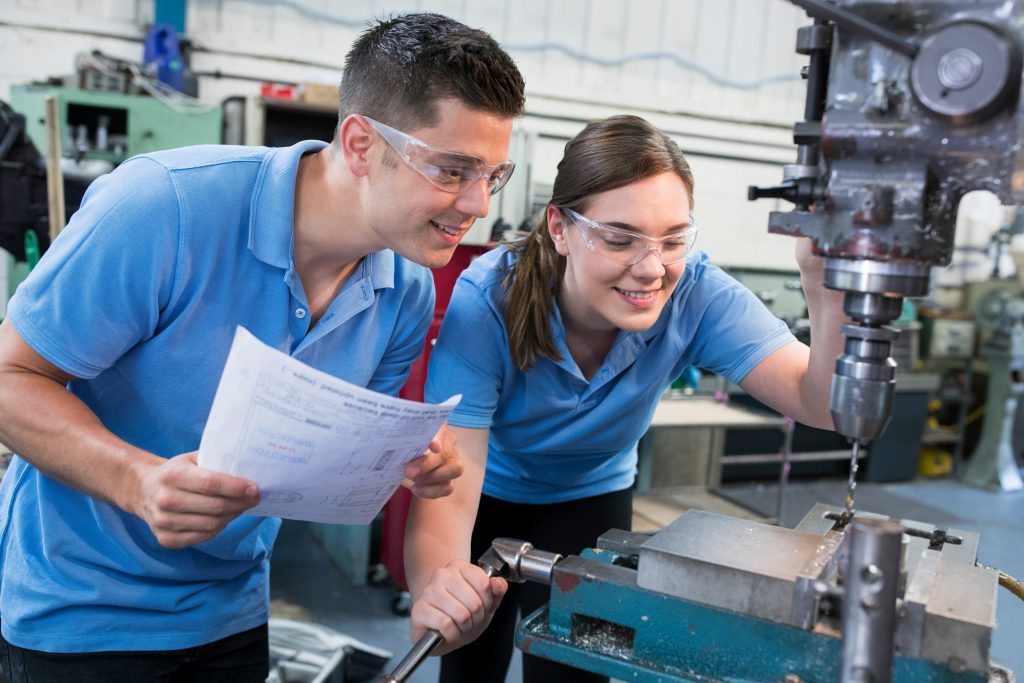
Biomedical engineers must be able to communicate well and not only apply engineering principles to medical procedures. Their work requires them to present research findings, publish scientific papers, and collaborate with other health care professionals. Additionally, they will need to be proficient at advanced mathematics.
Mechanical engineers earn a median salary of $91,352
Multiple factors influence the salary of a mechanical engineer. Salary levels can vary depending on where you live and what industry you work in. According to ASME members' 2017 Salary Survey, those in the Northeast and Southwest have higher salaries than others. The Midwest has the lowest earnings.
The average salary for mechanical engineers ranges from $91,352 - $137,028. The average salary is $91,352, with the top sixth of engineers earning more than the median. The average salary for those with less than two years' experience is $72,400. However, someone with 20 years of experience may earn as high as $150,000
The median salary for agricultural engineers is $89,130
In order to solve problems in relation to power supply and environment, agricultural engineers are employed in agricultural settings. They are also involved in designing and overseeing construction. This job requires advanced engineering abilities and knowledge of science and math. Their salaries are comparable to those of similar occupations in the United States. However, they are typically paid less than naval architects and engineers for locomotives. The job outlook is favorable for agricultural engineers. Between 2016-2026, the employment will grow by 7.4%.
The average salary for agricultural engineers in America is $89 130, with the highest-paid earning individuals making more than $110,000. The median salary for agricultural engineers varies by location. Santa Clara is the best-paying city for agricultural engineers.
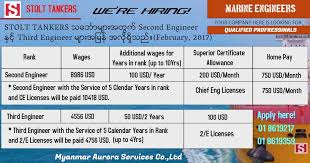
A median salary for an environmental engineer in the United States is $87620
The job of environmental engineers is to prevent the environment from being damaged by developing and implementing solutions that minimize any negative effects. They may work in a variety of fields and collaborate with other engineers, such as construction managers or urban planners. They are trained in biology, chemistry, data analysis, and critical thinking. They also understand environmental law and help organizations comply with regulations.
Environment engineers need to be flexible and adaptable to changes in technology and best practices. They must also have excellent analytical skills and be able to work with others. They must be able problem-solvers and optimistic.
FAQ
How can manufacturing prevent production bottlenecks?
You can avoid bottlenecks in production by making sure that everything runs smoothly throughout the production cycle, from the moment you receive an order to the moment the product is shipped.
This includes both planning for capacity and quality control.
Continuous improvement techniques like Six Sigma are the best way to achieve this.
Six Sigma management is a system that improves quality and reduces waste within your organization.
It emphasizes consistency and eliminating variance in your work.
Can certain manufacturing steps be automated?
Yes! Yes. Automation has been around since ancient time. The Egyptians invented the wheel thousands of years ago. We now use robots to help us with assembly lines.
There are many applications for robotics in manufacturing today. These include:
-
Assembly line robots
-
Robot welding
-
Robot painting
-
Robotics inspection
-
Robots that create products
Automation can be applied to manufacturing in many other ways. 3D printing is a way to make custom products quickly and without waiting weeks or months for them to be manufactured.
Why automate your warehouse
Automation has become increasingly important in modern warehousing. E-commerce has brought increased demand for more efficient and quicker delivery times.
Warehouses must be able to quickly adapt to changing demands. In order to do this, they need to invest in technology. Automating warehouses is a great way to save money. Here are some reasons why it's worth investing in automation:
-
Increases throughput/productivity
-
Reduces errors
-
Improves accuracy
-
Safety is boosted
-
Eliminates bottlenecks
-
Companies can scale more easily
-
Increases efficiency of workers
-
Gives you visibility into all that is happening in your warehouse
-
Enhances customer experience
-
Improves employee satisfaction
-
Minimizes downtime and increases uptime
-
Ensures quality products are delivered on time
-
Eliminates human error
-
It helps ensure compliance with regulations
How can we increase manufacturing efficiency?
The first step is to identify the most important factors affecting production time. We then need to figure out how to improve these variables. If you don't know where to start, then think about which factor(s) have the biggest impact on production time. Once you identify them, look for solutions.
How can I find out more about manufacturing?
The best way to learn about manufacturing is through hands-on experience. But if that is not possible you can always read books and watch educational videos.
Statistics
- It's estimated that 10.8% of the U.S. GDP in 2020 was contributed to manufacturing. (investopedia.com)
- In 2021, an estimated 12.1 million Americans work in the manufacturing sector.6 (investopedia.com)
- [54][55] These are the top 50 countries by the total value of manufacturing output in US dollars for its noted year according to World Bank.[56] (en.wikipedia.org)
- According to the United Nations Industrial Development Organization (UNIDO), China is the top manufacturer worldwide by 2019 output, producing 28.7% of the total global manufacturing output, followed by the United States, Japan, Germany, and India.[52][53] (en.wikipedia.org)
- Many factories witnessed a 30% increase in output due to the shift to electric motors. (en.wikipedia.org)
External Links
How To
How to use Lean Manufacturing in the production of goods
Lean manufacturing (or lean manufacturing) is a style of management that aims to increase efficiency, reduce waste and improve performance through continuous improvement. It was developed in Japan during the 1970s and 1980s by Taiichi Ohno, who received the Toyota Production System (TPS) award from TPS founder Kanji Toyoda. Michael L. Watkins published the "The Machine That Changed the World", the first book about lean manufacturing. It was published in 1990.
Lean manufacturing refers to a set of principles that improve the quality, speed and costs of products and services. It emphasizes the elimination of defects and waste throughout the value stream. The five-steps of Lean Manufacturing are just-in time (JIT), zero defect and total productive maintenance (TPM), as well as 5S. Lean manufacturing emphasizes reducing non-value-added activities like inspection, rework and waiting.
Lean manufacturing improves product quality and costs. It also helps companies reach their goals quicker and decreases employee turnover. Lean manufacturing is considered one of the most effective ways to manage the entire value chain, including suppliers, customers, distributors, retailers, and employees. Lean manufacturing is widely practiced in many industries around the world. Toyota's philosophy, for example, is what has enabled it to be successful in electronics, automobiles, medical devices, healthcare and chemical engineering as well as paper and food.
Five principles are the basis of lean manufacturing:
-
Define value - Find out what your business contributes to society, and what makes it different from other competitors.
-
Reduce waste - Stop any activity that isn't adding value to the supply chains.
-
Create Flow. Ensure that your work is uninterrupted and flows seamlessly.
-
Standardize and simplify – Make processes as repeatable and consistent as possible.
-
Build Relationships- Develop personal relationships with both internal as well as external stakeholders.
Lean manufacturing isn’t new, but it has seen a renewed interest since 2008 due to the global financial crisis. Many businesses have adopted lean manufacturing techniques to help them become more competitive. Many economists believe lean manufacturing will play a major role in economic recovery.
Lean manufacturing is becoming a popular practice in automotive. It has many advantages. These include higher customer satisfaction levels, reduced inventory levels as well as lower operating costs.
Lean manufacturing can be applied to almost every aspect of an organization. It is especially useful for the production aspect of an organization, as it ensures that every step in the value chain is efficient and effective.
There are three main types in lean manufacturing
-
Just-in-Time Manufacturing: Also known as "pull systems", this type of lean manufacturing uses just-in-time manufacturing (JIT). JIT stands for a system where components are assembled on the spot rather than being made in advance. This strategy aims to decrease lead times, increase availability of parts and reduce inventory.
-
Zero Defects Manufacturing, (ZDM): ZDM is focused on ensuring that no defective products leave the manufacturing facility. Repairing a part that is damaged during assembly should be done, not scrapping. This applies to finished goods that may require minor repairs before shipment.
-
Continuous Improvement (CI), also known as Continuous Improvement, aims at improving the efficiency of operations through continuous identification and improvement to minimize or eliminate waste. It involves continuous improvement of processes, people, and tools.