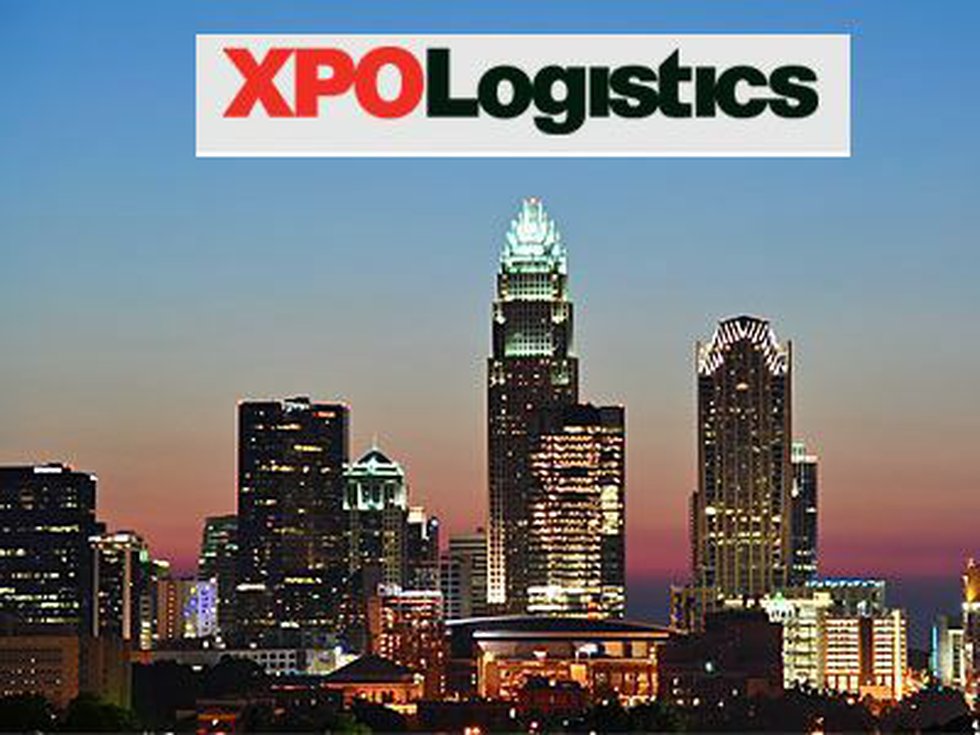
The Defense Industrial Base, or DIB, is a network of nearly 200,000 companies that supplies goods and services to Department of Defense. It includes small businesses, big corporations, and startups. A new report from Government Accountability Office shows the risks that DIB faces as well as the challenges it faces in addressing those threats.
The defense industrial sector has suffered a nearly 40 percent decline over the past decade. As a result, the Department of Defense has struggled to attract new entrants into the sector. To address this issue, the Defense Department has tried a variety of efforts to encourage new businesses to participate. Many smaller businesses are being left behind despite all these efforts. This has made it a greater national security threat.
Diverse DOD offices are working on mitigation of risks in the DIB. However, there is no comprehensive strategy in place to assess and manage these risk. GAO reviewed several reports from the department to find areas for improvement and interviewed DOD officials. Ultimately, GAO identified five elements that could help the department achieve its goals:
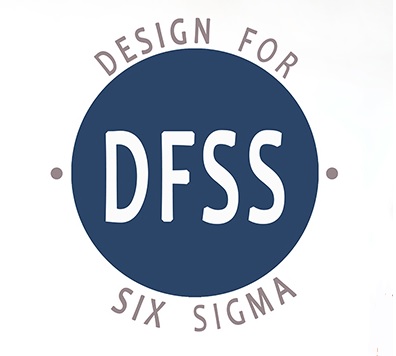
Loss of commercial suppliers is one of the greatest concerns. Many of these suppliers provide parts for military weapon systems. There aren't many metrics available to determine how many new companies enter the market. The industry has seen a decline in small-businesses over the past decade.
Other problems include material shortages as well as reliance on foreign vendors. Additional problems include intellectual property restrictions that slow down the military's acquisitions process and a lack of standardization for what is considered "new entrant" to the defense industry base.
GAO recommended that Defense review its policy regarding mitigating risk in the DIB. The GAO also recommended that the department continue to engage with traditional defense contractors and to implement tools that will make commercial technology providers more easily enter the DoD market. These recommendations should form part of an overall strategy to address industrial base concerns.
As a part of this strategy, the Defense Department should consider how its OTAs and CSOs can be used to expedite acquisition strategy development. By using the right people, processes, and technologies, the supply chain can be restructured to deliver dynamic outcomes.
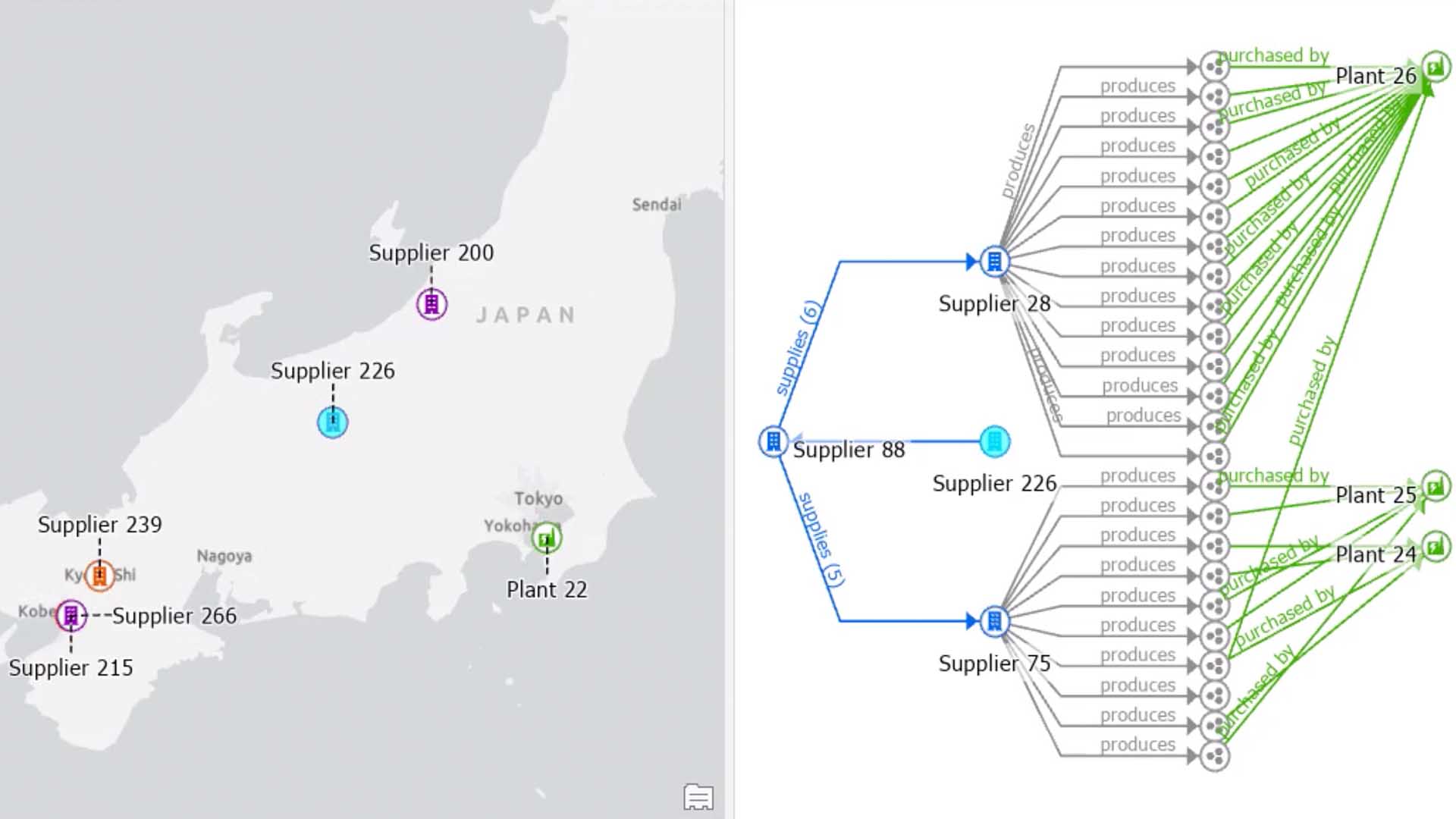
Despite a decrease in new entrants to defense industry base over the last decade the industry is still developing. Many companies do not feel comfortable with the Federal Acquisition Regulation (FAR). Additionally, small businesses might not have as many opportunities to compete with the larger companies in the current market.
Innovation is key for the defense industrial sector. Small businesses and startups play a crucial role. Part of the resilient DIB, companies can support National Security needs while allowing Department of Defense to develop new and better military equipment.
Overall, the defense industry base is a complex business that requires a comprehensive strategy. This strategy must ensure that resources are aligned to the needs of the military. It is vital that the Department of Defense studies best practices in technology integration to ensure more efficient and innovative products.
FAQ
Why automate your warehouse
Modern warehouses are increasingly dependent on automation. E-commerce has brought increased demand for more efficient and quicker delivery times.
Warehouses need to adapt quickly to meet changing needs. They must invest heavily in technology to do this. Automating warehouses is a great way to save money. Here are some of the reasons automation is worth your investment:
-
Increases throughput/productivity
-
Reduces errors
-
Increases accuracy
-
Safety increases
-
Eliminates bottlenecks
-
This allows companies to scale easily
-
This makes workers more productive
-
It gives visibility to everything that happens inside the warehouse
-
Enhances customer experience
-
Improves employee satisfaction
-
Minimizes downtime and increases uptime
-
High quality products delivered on-time
-
Eliminates human error
-
This helps to ensure compliance with regulations
Can some manufacturing processes be automated?
Yes! Yes! Automation has existed since ancient times. The Egyptians invented the wheel thousands of years ago. We now use robots to help us with assembly lines.
Actually, robotics can be used in manufacturing for many purposes. These include:
-
Automated assembly line robots
-
Robot welding
-
Robot painting
-
Robotics inspection
-
Robots that produce products
Automation can be applied to manufacturing in many other ways. For instance, 3D printing allows us make custom products and not have to wait for months or even weeks to get them made.
What skills does a production planner need?
Production planners must be flexible, organized, and able handle multiple tasks. Communication skills are essential to ensure that you can communicate effectively with clients, colleagues, and customers.
What are the 7 Rs of logistics?
The acronym "7R's" of Logistics stands for seven principles that underpin logistics management. It was published in 2004 by the International Association of Business Logisticians as part of their "Seven Principles of Logistics Management" series.
The acronym consists of the following letters:
-
Responsible - to ensure that all actions are within the legal requirements and are not detrimental to others.
-
Reliable - Have confidence in your ability to fulfill all of your commitments.
-
It is reasonable to use resources efficiently and not waste them.
-
Realistic – consider all aspects of operations, from cost-effectiveness to environmental impact.
-
Respectful - Treat people fairly and equitably
-
Resourceful - look for opportunities to save money and increase productivity.
-
Recognizable - provide customers with value-added services.
Is automation important for manufacturing?
Automation is important not only for manufacturers but also for service providers. Automation allows them to deliver services quicker and more efficiently. It reduces human errors and improves productivity, which in turn helps them lower their costs.
Statistics
- According to the United Nations Industrial Development Organization (UNIDO), China is the top manufacturer worldwide by 2019 output, producing 28.7% of the total global manufacturing output, followed by the United States, Japan, Germany, and India.[52][53] (en.wikipedia.org)
- Many factories witnessed a 30% increase in output due to the shift to electric motors. (en.wikipedia.org)
- According to a Statista study, U.S. businesses spent $1.63 trillion on logistics in 2019, moving goods from origin to end user through various supply chain network segments. (netsuite.com)
- (2:04) MTO is a production technique wherein products are customized according to customer specifications, and production only starts after an order is received. (oracle.com)
- Job #1 is delivering the ordered product according to specifications: color, size, brand, and quantity. (netsuite.com)
External Links
How To
How to use 5S to increase Productivity in Manufacturing
5S stands for "Sort", "Set In Order", "Standardize", "Separate" and "Store". The 5S methodology was developed at Toyota Motor Corporation in 1954. This methodology helps companies improve their work environment to increase efficiency.
This method aims to standardize production processes so that they are repeatable, measurable and predictable. This means that tasks such as cleaning, sorting, storing, packing, and labeling are performed daily. Workers can be more productive by knowing what to expect.
Five steps are required to implement 5S: Sort, Set In Order, Standardize. Separate. Each step requires a different action to increase efficiency. By sorting, for example, you make it easy to find the items later. You arrange items by placing them in an order. You then organize your inventory in groups. Finally, label all containers correctly.
Employees will need to be more critical about their work. Employees need to be able understand their motivations and discover alternative ways to do them. To be successful in the 5S system, employees will need to acquire new skills and techniques.
The 5S Method not only improves efficiency, but it also helps employees to be more productive and happier. They will feel motivated to strive for higher levels of efficiency once they start to see results.