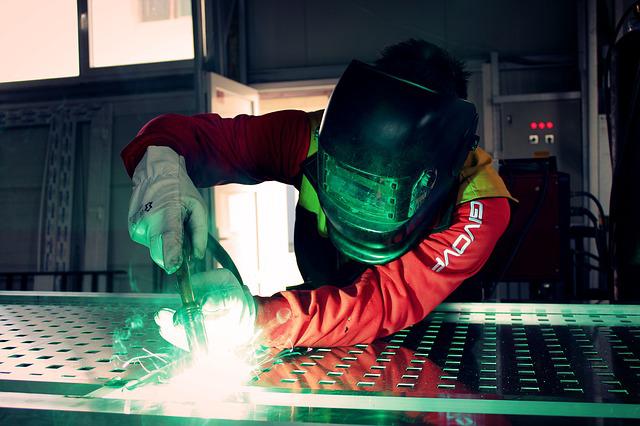
Supply chain disruptions can lead to economic and productivity losses across all industries. It is clear that companies have not been proactive in managing risk, which has led to disruptions.
In the face of growing internationalization, the defence industry has been affected by this trend. There may be a shortage of certain technologies, such high-quality carbon-fiber and advanced semiconductors. This can lead to increased reliance on foreign capital and oligopolistic behavior. There is also an increased risk of dual products. These products can cause safety and reliability problems.
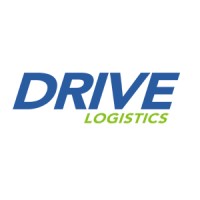
The security of vital minerals is crucial to modern industrial systems development in the age of globalization. Some minerals are distributed in economically underdeveloped countries and can be vulnerable to political instability. Different circumstances can lead to different global allocations of critical minerals. China is a vital node of the global critical minerals value chains, but the industry depends heavily on other nations. Instead of concentrating resources in one country, it is vital that governments create a global critical minerals allocation network that includes multiple countries.
The European Union (EU), has been involved in discussions about its defense technology (DTIB) and industrial base. The European Commission established the European Defence Agency in order to provide a framework to develop a new European defense industry. This new approach will bring about a number of changes in the EU's defence industry. Certain technologies cannot be supplied by all non-EU companies. The EU's defense industry will have both oligopoly and monopoly structures. Furthermore, it will be much easier to purchase raw materials from non EU firms. This will open the door to a new type, called bundled volume.
An increased emphasis is placed on the creation of a secure supply chain. To reduce the risk of supply chain disruptions, there are many strategies. One strategy is to implement a formal risk management plan. A formal risk management approach is a way to allow the supply chain not only to survive but thrive. It should involve both internal and external key stakeholders, including suppliers, investors and governments. Management of the supply chain should be in line with global supply-chain dynamics.
The security of the 99m/99m Tc supply chains is another important policy issue. The policy approach developed by the High-Level Group on Medical Radioisotopes (HLG-MR) ensures the long-term security of the supply of these radioisotopes. The approach consisted of several elements. It included a review and analysis of the 99 Mo/99mtc supply chain, as well as an economic impact analysis, and a policy approach.
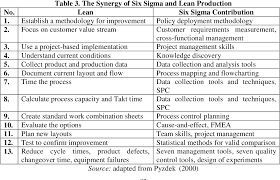
HLG-MR identified two areas of vulnerability that must be addressed to increase the security of the 99 M/99m supply chain. These areas include monopolistic behaviour, foreign capital, and political conflicts. These factors can lead to price rises and significant risk. HLG-MR's policy approach also identified key steps to address these vulnerabilities.
FAQ
What is the difference between a production planner and a project manager?
The main difference between a production planner and a project manager is that a project manager is usually the person who plans and organizes the entire project, whereas a production planner is mainly involved in the planning stage of the project.
What are the 4 types of manufacturing?
Manufacturing is the process by which raw materials are transformed into useful products through machines and processes. It can involve many activities like designing, manufacturing, testing packaging, shipping, selling and servicing.
Can we automate some parts of manufacturing?
Yes! Since ancient times, automation has been in existence. The Egyptians discovered the wheel thousands and years ago. Today, robots assist in the assembly of lines.
Actually, robotics can be used in manufacturing for many purposes. These include:
-
Automated assembly line robots
-
Robot welding
-
Robot painting
-
Robotics inspection
-
Robots that make products
There are many other examples of how manufacturing could benefit from automation. 3D printing is a way to make custom products quickly and without waiting weeks or months for them to be manufactured.
Statistics
- In the United States, for example, manufacturing makes up 15% of the economic output. (twi-global.com)
- Job #1 is delivering the ordered product according to specifications: color, size, brand, and quantity. (netsuite.com)
- In 2021, an estimated 12.1 million Americans work in the manufacturing sector.6 (investopedia.com)
- It's estimated that 10.8% of the U.S. GDP in 2020 was contributed to manufacturing. (investopedia.com)
- Many factories witnessed a 30% increase in output due to the shift to electric motors. (en.wikipedia.org)
External Links
How To
How to Use Lean Manufacturing in the Production of Goods
Lean manufacturing is a management style that aims to increase efficiency and reduce waste through continuous improvement. It was first developed in Japan in the 1970s/80s by Taiichi Ahno, who was awarded the Toyota Production System (TPS), award from KanjiToyoda, the founder of TPS. Michael L. Watkins published the original book on lean manufacturing, "The Machine That Changed the World," in 1990.
Lean manufacturing is often described as a set if principles that help improve the quality and speed of products and services. It emphasizes the elimination and minimization of waste in the value stream. Just-in-time (JIT), zero defect (TPM), and 5S are all examples of lean manufacturing. Lean manufacturing is about eliminating activities that do not add value, such as inspection, rework, and waiting.
In addition to improving product quality and reducing costs, lean manufacturing helps companies achieve their goals faster and reduces employee turnover. Lean manufacturing is a great way to manage the entire value chain including customers, suppliers, distributors and retailers as well as employees. Lean manufacturing practices are widespread in many industries. Toyota's philosophy is the foundation of its success in automotives, electronics and appliances, healthcare, chemical engineers, aerospace, paper and food, among other industries.
Five basic principles of Lean Manufacturing are included in lean manufacturing
-
Define value - Find out what your business contributes to society, and what makes it different from other competitors.
-
Reduce waste - Get rid of any activity that does not add value to the supply chain.
-
Create Flow. Ensure that your work is uninterrupted and flows seamlessly.
-
Standardize and Simplify – Make processes as consistent, repeatable, and as simple as possible.
-
Develop Relationships: Establish personal relationships both with internal and external stakeholders.
Lean manufacturing, although not new, has seen renewed interest in the economic sector since 2008. Many businesses are now using lean manufacturing to improve their competitiveness. In fact, some economists believe that lean manufacturing will be an important factor in economic recovery.
Lean manufacturing, which has many benefits, is now a standard practice in the automotive industry. These include improved customer satisfaction, reduced inventory levels, lower operating costs, increased productivity, and better overall safety.
The principles of lean manufacturing can be applied in almost any area of an organization. Because it makes sure that all value chains are efficient and effectively managed, Lean Manufacturing is particularly helpful for organizations.
There are three types of lean manufacturing.
-
Just-in Time Manufacturing, (JIT): This kind of lean manufacturing is also commonly known as "pull-systems." JIT stands for a system where components are assembled on the spot rather than being made in advance. This approach is designed to reduce lead times and increase the availability of components. It also reduces inventory.
-
Zero Defects Manufacturing, (ZDM): ZDM is focused on ensuring that no defective products leave the manufacturing facility. If a part needs to be fixed during the assembly line, it should be repaired rather than scrapped. This is true even for finished products that only require minor repairs prior to shipping.
-
Continuous Improvement (CI),: Continuous improvement aims improve the efficiency and effectiveness of operations by continuously identifying issues and making changes to reduce waste. Continuous improvement refers to continuous improvement of processes as well people and tools.